錯誤類型
刷錫後貼片前:橋接-移位-無錫-錫不足
貼片後
回流焊前:移位,漏料、極性、歪斜、
腳彎、錯件
回流焊或
波峰焊後:少錫/多錫、無錫短接
錫球 漏料-極性-移位腳彎錯件
PCB行業裸板檢測
主要特點
2)快速便捷的編程系統
運用帖裝數據自動進行數據檢測
運用元件資料庫進行檢測數據的快速編輯
4)根據被
檢測元件位置的瞬間變化進行檢測視窗的自動化校正,達到高精度檢測
5)通過用墨水直接標記於PCB板上或在操作顯示器上用圖形錯誤表示來進行檢測電的核對
相關比較
人工檢查 AOI檢查
人 重要 輔助檢查
時間 正常 正常
持續性 因人而異 (差) 好
可靠性 因人而異 (差) 較好
時間 長 短
實施目標
實施AOI有以下兩類主要的目標:
最終品質
對產品走下生產線時的最終狀態進行監控。當生產問題非常清楚、產品
混合度高、數量和速度為關鍵因素的時候,優先採用這個目標。AOI通常放置在生產線最末端。在這個位置,設備可以產生範圍廣泛的過程控制信息。
過程跟蹤
使用檢查設備來監視
生產過程。典型地包括詳細的缺陷分類和元件貼放偏移信息。當
產品可靠性很重要、低混合度的大批量製造、和元件供應穩定時,製造商優先採用這個目標。這經常要求把檢查設備放置到生產線上的幾個位置,線上地監控具體
生產狀況,並為
生產工藝的調整提供必要的依據。
放置位置
雖然AOI可用於生產線上的多個位置,各個位置可檢測特殊缺陷,但AOI檢查設備應放到一個可以儘早識別和改正最多缺陷的位置。有三個檢查位置是主要的:
錫膏印刷之後
如果
錫膏印刷過程滿足要求,那么ICT發現的缺陷數量可大幅度的減少。典型的印刷缺陷包括以下幾點:
C.焊錫對焊盤的重合不良。
在ICT上,相對這些情況的缺陷機率直接與情況的
嚴重性成比例。輕微的少錫很少導致缺陷,而嚴重的情況,如根本無錫,幾乎總是在ICT造成缺陷。焊錫不足可能是元件丟失或
焊點開路的一個原因。儘管如此,決定哪裡放置AOI需要認識到元件丟失可能是其它原因下發生的,這些原因必須放在檢查計畫內。這個位置的檢查最直接地
支持過程跟蹤和特徵化。這個階段的定量過程控制數據包括,印刷偏移和焊錫量信息,而有關印刷焊錫的
定性信息也會產生。
回流焊前
檢查是在元件貼放在板上
錫膏內之後和
PCB送入
回流爐之前完成的。這是一個典型地放置檢查機器的位置,因為這裡可發現來自
錫膏印刷以及機器貼放的大多數缺陷。在這個位置產生的定量的過程控制信息,提供高速片機和密間距元件貼裝
設備校準的信息。這個信息可用來修改元件貼放或表明
貼片機需要校準。這個位置的檢查滿足過程跟蹤的目標。
回流焊後
在
SMT工藝過程的最後步驟進行檢查,這是AOI最流行的選擇,因為這個位置可發現全部的裝配錯誤。
回流焊後檢查提供高度的安全性,因為它識別由
錫膏印刷、元件貼裝和回流過程引起的錯誤。
最佳化設計
基本最佳化
每塊PCB可以採用光學或者X-ray技術並運用適當 的
運算法則來進行檢查。基於圖像檢查的基本 原理是:每個具有明顯
對比度的圖像都是可以 被檢查的。在AOI中存在的主要問題是,當一些檢查對象是 不可見的,或是在PCB上存在一些干擾使得圖像變得模糊 或隱藏起來了。然而,實際經驗和系統化測試都表明,這 些影響是可以通過PCB的設計來預防甚至減少的。為了推 動這種
最佳化設計,可以運用一些看上去很古老的附加手段(這些方法仍在很多領域被推崇),它的優點包括:
減少編程時間
最大限度地減少誤報? 改善失效檢查。
制定設計方針,可以有效地簡化檢查和顯著地降低生 產成本。Viscom AG 和 KIRRON GmbH &Co KG
合作開發 出一項特殊測試方案,目的是為了從根本上研究和證明這 些設計在檢查中產生的效果。基於IPC-7350標準的PCB布 局被推薦為針對這些測試的基準。首先,為了探究每一種 布局的檢查效果,建議在大量PCB布局上採用這種基準; 之後,再有意地利用PCB錯誤布局,使得它產生一些工藝 中的缺陷,如立碑和引腳懸空等。
布局建議
針對AOI檢查的PCB整體布局
器件到PCB的邊緣應該至少留有3mm(0.12”)的工 藝邊。片式器件必須優先於圓柱形器件。布局上建議考慮
感測器技術,因為有時檢查只能通過垂直(正交)角度,而其他時候又需要一個輔助的角度來進行。
元器件
對一個穩定的工藝過程來說,一個重要的因素是元器 件,這不僅與PCB上直接的器件布局有關,而且或多或少 也與“
工藝流程設計”有關。元器件的採購趨勢是盡 可能地便宜,而不管它在顏色、尺寸等參數上的不同。不 幸的是,這些選擇在日後對AOI或
AXI檢查過程中造成的影 響往往被忽略了。始終採用同樣的材料和產品能夠顯著地 減少檢查時間和誤報,而這些問題主要是通過元器件以及 PCB的突然變化而出現的。
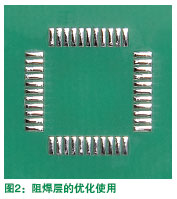
圖2
元器件尺寸
IPC-7350標準描述了器件的尺寸,並對某些焊盤的尺 寸提出了建議。根據IPC標準,器件的長度和引腳的寬度可 以有一個較大變化範圍,相反,焊盤的尺寸卻是相對固定 的。此外,PCB製造公差的影響相對於這些器件的變化來說 也是是很小的。
PCB的顏色和阻焊
通常,設備能夠檢查 出所有不同單板的顏色, 儘管檢查中的某些細節處 理是不倚賴於顏色的。例 如, 一塊白色和一塊綠 色的PCB有著不同的對比 度,因此設備需要一些特 定的補償。在一種極端情 況下,橋接在亮背景下呈 現黑色,而在另一種極端情況下,橋接在黑背景下卻是呈現出亮色。這裡我們建議 使用無光澤的
阻焊層。在我們的實踐中,焊盤間(甚至是
細間距引腳)的區域也應該覆蓋著阻焊層,這個建議也已 經被
焊料供應商所回響。
印刷圖案
所有印有圖案的PCB也是能夠被檢查的,例如,當元 器件的框線或元器件本體上的字母單獨出現在組件的某個 區域從而干擾對其他部分的檢查時,可以手工調整檢查程 序。儘管如此,在生產允許的範圍內,圖案的印刷範圍仍 然有一個較大的選擇,因此,減少非反射性標識印刷(黑 或暗黃)值得加以考慮。另外一個可能出現的情況是需要 有選擇地印刷標識:例如,當某些特定的器件(如霍爾傳 感器)正面向下時就必須印刷成白色;而另一種情況是印 有極性標誌的有
傾斜角的
鉭電容器件;這樣能使標識和背 景形成鮮明的對比,使得檢查的圖像更加清晰。
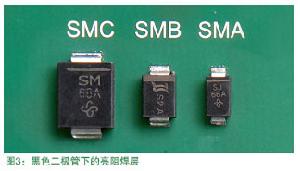
圖3
設備可以檢查所有 類型的基準點,而且任 何構件都可以被定義成 一個基準點。雖然三個基 準點可以補償一塊單板的 變形,但通常情況下只需 要確定兩個基準點就可以 了。每個基準點至少離單 板邊緣5mm(0.2”)。
十字形、菱形、星形等比較適用,並建議使用統一的黑背 景。此外,十字形的基準點特別有優勢,他們在檢測光下的圖像十分穩定且可以被快速和容易地判定。。
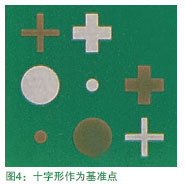
圖4
確認壞板
設備有能力檢查所有已知類型的壞板標識。板上的任 何構件都可以被定義為壞板標識。這裡建議採用與上述基 準點的判定相類似的方法,即在可能的情況下,首先通過 檢查整板或已完成組裝的單板上的單個壞板標識來進行確 認。板上每個單獨的壞板標識只有在整板的壞板標識檢查失敗後才會被逐一檢查;整板的壞板標識應該定位於PCB的邊上。
避免焊點反射
焊點的形狀和
接觸角是焊點反射的根源。焊點的形成 依賴於焊盤的尺寸、器件的高度、
焊錫的數量和回流工藝 參數。為了防止焊接反射,應當避免器件對稱排列。
波峰焊
經過波峰焊後,焊點所有的參數會有很大的變化,這 主要是由於焊爐內錫的老化導致焊盤
反射特性從光亮到灰 暗,因此,在檢查時算法上必須要包含這些變化。在波峰焊 中,典型的缺陷是短路和
焊珠。當檢測到短路時,假如印刷 的圖案或者無反射印刷這兩種情況的減少以及套用阻焊層, 就可以消除這些誤報。如果基準點沒有被
阻焊膜蓋住而過波 峰焊,可能會導致一個圓形基準點上錫成了一個半球,其內 在的反射特性將會發生改變;套用
十字型作為基準點或者用 阻焊層覆蓋基準點,可以防止這種情況的發生。
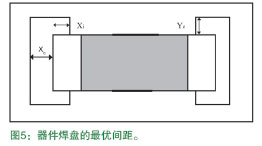
圖5
在片式元件和MELF器件上,彎月狀的焊點必須被正 確地識別出來;而在器件本體兩側下方的焊點由於焊錫無 爬升,很難檢查。另外,焊盤邊緣到
焊端的間距Xc也需要 注意。Xc (焊盤的外側間距)對Xi(焊盤的內側間 距)的比率應選擇>1。同樣的規則也適用於C-leads器件的 彎月型和器件本體兩側的焊盤設計。這裡,我們建議Xc對 Xi的比率稍微大於1.5。值得注意的是:任何元器件的長度 變化也必須計算在內。
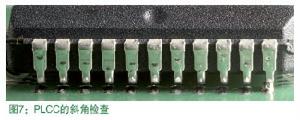
圖7
“鷗翼”型引腳器件
通常,這類器件的判定標準可以通過對毛細效應在垂 直方向的作用的分析中找到。由於
毛細力,焊錫從焊盤末端 爬到引腳上形成焊點。由於工藝波動和器件邊緣的阻擋作 用,導致不能完全形成一個完整的上半月型焊點。儘管沒有 形成一個上半月型的焊點,但也可以被認為焊接得很好。 “鷗翼”型引腳焊錫的側面爬升情況由於器件變化或 焊盤設計的原因,並不是經常能夠被檢查出來,這是由於 焊錫的爬升方向必須用同引腳方向垂直的角度去檢查。假 如爬升很小,必須從其他角度來檢查,而只有通過這樣的
輔助檢查,才能提供豐富的圖像信息去評估焊點的好壞。?
斜角檢測:PLCCs型器件
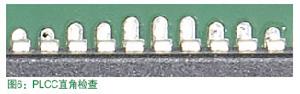
圖6
PLCCs器件的引腳的焊盤有著不同設計。如果是一個 長焊盤設計,在PLCC引腳上焊錫的爬升效果是可以檢查 的。如果焊盤保持明亮,那么焊錫已經爬升到了引腳端, 所以認為器件是焊上了。假如遵循這個
設計原則,可以通過垂直檢測來檢查出缺陷。
對於PLCC焊點,有時會出現少錫的情況。由於引腳少 錫的爬升情況和沒有焊錫時是一樣的,所以對PLCC焊點不 能通過垂直檢測,而要通過斜角檢測的方式來檢查少錫缺陷。
PCB的整體布局 對於普通的AXI測試PCB布局,所有的焊盤都必須進行 阻焊處理。這是因為阻焊層和實際的焊盤並沒有真正
地接 觸到,在阻焊層和焊盤之間存在著一定的間隙。這樣做的 好處是:焊錫受熱後就可以聚集在焊盤內,這也使得在XRAY影像中很容易再現焊料的爬升情況。
2D x-ray
當套用2D x-ray技術時,所有的器件都需要被布置在 PCB的正面。而用2D
x-ray去檢測這些器件時,還必須再定 義出一塊沒有器件的地方為“禁區”。對於有些BGAs,會 推薦使用一種淚滴型的不對稱焊盤設計,這使得焊錫的成 型性質被系統錯誤的判斷為一種幾何的連線形態;此外, 一些特殊的
QFN向內或向外的彎月型焊盤設計也同樣有這種情況。
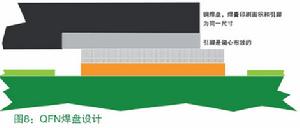
圖8
QFN 焊盤設計
QFN器件的焊盤尺寸、
焊膏印 刷面積與它的引腳尺寸是同樣大小 的,而且器件的引腳是
交錯排列在 封裝體底部的(
圖8)。
因此,QFN的 焊盤設計建議為:焊盤伸出於器件引腳的外端, 而縮進於器件的內 端,這樣使得在器件引腳的內外形成彎月型焊盤。在這裡 很重要的一點是,在進行設計計算時必須考慮器件的公差範圍。(圖9)
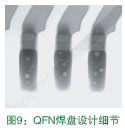
圖9
在BGA設計時,焊點的形狀(如淚滴型)可以通過特 別的布局使其成為可見的;就是說,淚滴型的焊點除了具 有奇怪的形狀外,它的方向也是很隨意的。總而言之,在 器件面的焊盤和在PCB上的焊盤正好和BGA焊球的大小是 一樣的(圖10 )。在德國Erlangen 大學,學者做了大量的 研究去評價單個焊盤形狀的模型;他們發現,無論焊盤是 圓形還是非圓形的,焊膏印刷圖形要保持為圓形不變。
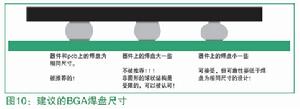
圖10
結論
作為慣例,在生產中,測試系統應當根據
生產批量的要 求建立並最佳化。實際運作中無數次地證明,僅這樣做是遠 遠不夠的。如果在兩周的
生產時間內要測試一個新批次的 PCB,有可能會發生這樣的情況:ELKO的顏色突然由黑色 變為了黃色,或者
電晶體的引腳變短了、是彎的;或是電阻的顏色由黃色變成了藍色的,等等。
AOI檢查程式必須而且能夠處理這些不同的變化所帶來 的問題。但是,其中的一些變化需要花費時間進行處理, 因為我們不能預先知道是否有一種新的元器件被使用,或 是存在一個錯誤的元器件布局。同時,面對質量方面的困 難,大量允許的可能出現的情況也需要一個一致的,確實 可行的說明。
始終採用同樣的材料和產品,再加上最佳化的
PCB設計, 正如上面所描述的那樣,可以減小由於產品的變更對AOI/ AXI測試所造成的影響。在這裡必須指出,比照所有用於 AOI和AXI 檢查的標準,PCB布局的建議可使檢查工藝適當 簡化並更有效率。
DFT可以提高缺陷的檢查率,減少誤報, 縮短編程時間和降低編程的難度,從而最終達到有效降低
產品製造成本的目的。
實際套用
對
無缺陷生產來講,
自動光學檢查(AOI)是必不可少的。在轉到使用無鉛工藝時,製造商將面臨新的挑戰,在生產中會出現其他的問題,引起了人們的關注。本文分析轉到無鉛工藝的整個過程,特別是在
大規模生產中引進了0402無鉛元件。
由於缺乏無鉛元件,轉到使用無鉛元件是分階段進行的。在2004年,由於要求電子產品的體積越來越小,迫使製造商廣泛地用0402元件來取代0603元件和0805元件。
工藝條件
除了普遍使用的0402元件,印刷
電路板的第一次合格率(
FPY)必須達到95%,而且必須根據
印刷電路協會(IPC)的2級標準來檢測缺陷。例如,在有608個焊點的168元件的情況下,相當於要求
誤報率是百萬分之65。為了達到FPY的要求,在檢測缺陷時必須考慮以下條件:元件長度的公差、元件供應商、貼片公差、在25 個AOI系統上的全球檢測資料庫、有80個獨特產品的全球檢測資料庫、無鉛焊料、不同的電路板供應商以及
檢測質量要達到IPC的2級標準。
可以從三個方面看到無鉛的影響:
灰度值提高、流程的改變和有效的助焊劑。無鉛焊點的亮度
平均值高了2.5%。這相當於亮度提高了五級。焊點看上去粗糙,而且表面呈粗大的
顆粒狀。這可以利用特性
萃取方法來消除或者過濾掉。流動性稍微差一些,特別是對於那些較輕的元件,會妨礙元件在熔化焊膏中浸沒或者浮起。這表示元件自動對正的程度較差。由於效果差,意味著輕輕的0402元件沿著縱向翹起的傾向會增強,結果是不能完全看到元件的頂部。
在
回熔溫度較高以及使用侵蝕性更強的助焊劑時,也會導致與助焊劑
直接接觸的較薄的元件受到侵蝕,元件頂部不能夠
反射光線。流動性的改變和侵蝕性助焊劑,對R0402型元件的影響比C0402型元件大,因為R0402型元件更輕也更薄。在使用R0603元件時,這也不常見。
檢查庫
圍繞工藝的環境產生消極影響,必須通過幾個途徑降低到最小,以滿足頭工作的要求。
● AOI全球檢查庫──對部分AOI製造商的標定工具進行調整是極為重要的,所以,這些變化能夠傳遞到照相機和照明模組上。
● 對於不同產品的AOI全球檢查庫,有可能在當地進行調整──這是AOI軟體必備的特性。
● 確定檢查質量:IPC標準2級——必須允許使用朝下的
電阻器。組件趐起和
共面性的檢測必須可靠。
關於元件長度公差,不同的組件供應商、電路板和無鉛焊料的供應商都不可能沒有任何直接的影響。優良的AOI程式應該能夠應付這些這影響。如果這些個別點的變化可以保持不變,那么就能夠相當大地簡化AOI編程。經研究得到的結論是,由於無鉛產生的影響,圖形對照系統無法得到適合的檢查結果,這是因為合格的樣品變化太大。更加可行的方法是,取出確定每道工藝和元件變化的特性。這些變化可以分成不同的等級。如果在使用的工藝中,出現了一個新的變化,就要增加一個級別,來保證檢查的
精確性。所有認識到的和已知的缺陷都儲存起來,他們的類型和圖片可以用於AOI系統和全球資料庫里的檢查程式。我們沒有必要把一塊不同缺陷的電路板保存起來用於詳細的檢查。
用AOI軟體核實真正的缺陷
AOI軟體中有一個綜合性的驗證功能,它能減少檢查的誤報,保證檢測程式無缺陷。它可以檢查儲存起來的有缺陷的樣品,例如,修理站存放的樣品,以及印刷了焊膏的空白印刷電路板。在最佳化階段,在這方面花時間的原因是為了不讓任何缺陷溜過去。所有已知的缺陷都必須檢查,同時要把允許出現的誤報數量做到最小。在針對減少誤報而對任何程式進行調整時,要檢查一下,看看以前檢查出來的真正缺陷,是否得到維修站的證實。通過綜合的核實,保證檢查程式的質量,用於專門的製造和核查,同時對誤報進行追蹤。
適應性程式沒有發現轉到無鉛會對焊
點質量的檢查帶來什麼影響。缺陷看上去還是一樣的。毫無疑問,只需要稍微修改一下資料庫,就足以排除其他誤報可能會帶來的影響。在元件頂上的內容改變時,就需要大量的工作,確定
門限值。這些可以納入到標準資料庫中。在元件的一端立起來時,激活其他環節的檢測,便可以進行可靠的分析。對於橋接的形成或者元件一端立起來的普遍看法,證明常常不是那樣。經驗表明,橋接的形成沒有改變,元件一端立起來的現像就會有所減少。轉到使用
無鉛焊膏並不需要投資新的系統或者設備,只要使用的AOI系統配備了靈活的感測器模組、照明和軟體,就足以適應這些變化了。
生產廠家
國內
明銳理想 Magic Ray
鐳晨 Maker-ray
振華興VCTA
視界焦點VIFO
勁拓 JT
矩子智慧型 JUTZE
神州視覺ALEDER
北京星河康帝思 SRC
吉洋GEEYOO