基本介紹
- 中文名:壓模製模法
- 套用領域:工藝,機械製造
壓模的製作方法,鋁型材料壓模製模技術,壓模層壓板成型工藝,浸料壓模製模成型工藝,壓制前的準備,壓制工藝,
壓模的製作方法
壓模由一上部組件1和一下部組件2組成,上部組件1包括一衝頭3和一個用於支承沖頭3的沖頭支承體4,下部組件2包括一個模5和一個用於支承模5的模夾具6。模的中心部5被加工成所需的彎曲形狀,而其邊緣則經受衝壓以便形成邊裙部分(部分標號如下圖所示)。
如果將一個要加工的材料W放在這樣一個壓模中,則上、下部組件1和2中的任何一個被移動以便使被放在沖頭3和模5間的材料W可被加工成形為所需形狀。為了將完全成形的產品W從模上脫下來,一般在沖頭3的周圍安裝多個脫模桿,脫模桿7以這樣一種形式即它們可以向下延伸的形式被安裝在上部組件1的沖頭支承體4上。
然而,這些脫模桿並不只是將完成的成品W從沖頭3上脫下,而且在壓製成形過程中特別是衝壓過程中起著支承加工中的工件的作用,即作為坯料夾具。因此,這些脫模桿通常帶有螺旋彈簧8作為提供彈力的手段,然而,在將片金屬及類似物質壓製成形的場合下,要將一個軟合成橡膠材料如一個橡皮墊9安在其前端以防止損壞產品。
然而,這樣的彈簧8在彈力上與標準彈簧有嚴重偏差,墊9隨著彈性的逐漸損失除了性能上的降低外,變得具有更嚴重的偏差。因此,為了用作坯料夾具而使用彈簧8或墊9的這些脫模桿在其彈性支持刀上是互不相同的,由此使得它們不能以一致的力量支承加工中的工件。特別是在壓製成形薄片金屬的場合,在產品上產生捲曲,成品形狀與其尺寸配合公差不能相符,因而增加了次產品率。此外,當使成品從沖頭上脫下時,各個脫模桿的脫模力不一致,結果是產品在脫模過程中可能變形。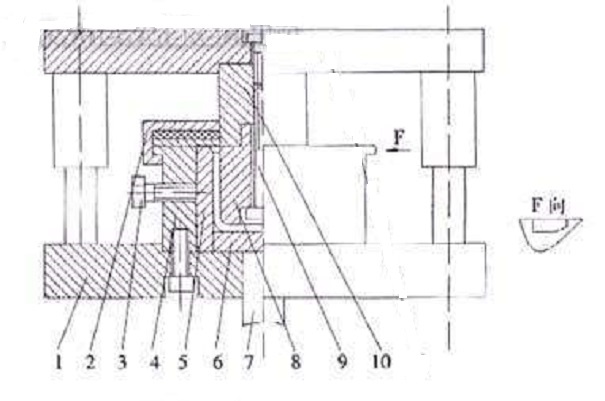
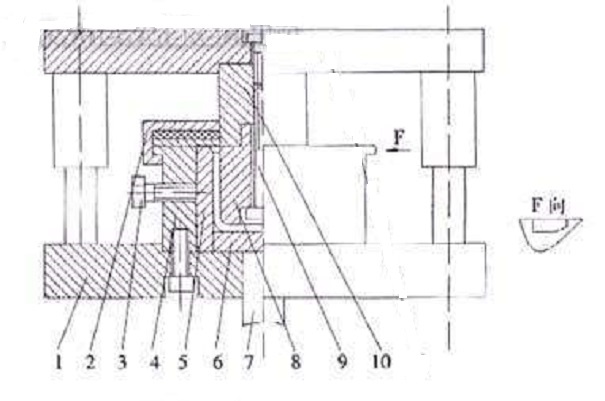
鋁型材料壓模製模技術
鋁型材擠壓工模具的製造也是決定其品質和使用壽命的關鍵因素之一。由於鋁擠壓工模具具有一系列特點,因此對鋁型材模具制模技術提出了一些特殊要求:
1、由於鋁合金擠壓工模具的工作條件十分惡劣,在擠壓過程中需要經受高溫、高壓、高摩擦的作用,因此要求使用高強耐熱合金鋼,而這些鋼材的熔煉、鑄造、鍛造、熱處理、電加工、機械加工和表面處理等工藝過程都非常複雜,這給模具加工帶來了一系列的困難。
2、為了提高工模具的使用壽命和保證產品的表面品質,要求模腔工作帶的粗糙度達到0.8-0.4μm,模子平面的粗糙度達到1.6μm以下,因此,在制模時需要採取特殊的拋光工藝和拋光設備。
3、由於擠壓產品向高、精、尖方向發展,有的型材和管材的壁厚要求降到0.5mm左右,其擠壓製品公差要求達到±0.05mm,為了擠壓這種超高精度的產品,要求模具的製造精度達到0.01mm,采崩傳統的工藝足根本無法製造出來的,因此,要求更新工藝和採用新型專用設備。
4、鋁型材斷面十分複雜,特別是超商精度的薄壁空心鋁型材和多孔空心壁板鋁型材,要求採用特殊的擠壓模具結構,往往在一塊模子上同時開設有多個異形孔腔,各截面的厚度變化急劇,相關尺寸複雜,圓弧拐角很多,這給模具的加工和熱處理帶來了很多麻煩。
7、擠壓工模具的種類繁多,結構複雜,裝配精度要求很高,除了要求採取特殊的加工方法和採用特殊的設備以外,尚需採用特殊的工裝卡具和刀具以及特殊的熱處理方法。
8、為了提高工模具的品質和使用壽命,除了選擇合理的材料和進行最佳化設計以外,尚需採用最佳的熱處理工藝和表面強化處理工藝,以獲得適中的模具硬度和高的表面品質,這對於形狀特別複雜的難擠壓製品和特殊結構的模具來說顯得特別重要。
由此可見,擠壓模具的加工工藝小同於一般的機械製造工藝,而是一門難度很大涉及面很廣的特殊技術。為了製造出高質量和高壽命的模具,除了要選擇和製備優質的模具材料外,尚需要制定合理的冷加工工藝、電加工工藝、熱處理工藝和表面處理工藝。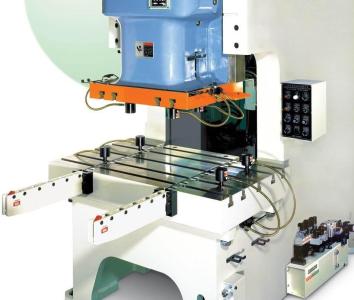
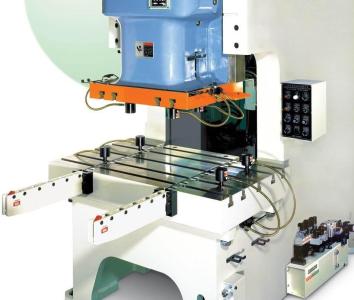
壓模層壓板成型工藝
複合材料的層壓工藝的熱壓過程,一般分為預熱預壓和熱壓兩個階段。
1、第一階段---預熱預壓階段
此階段的主要目的是使樹脂熔化,去除揮發物、浸漬纖維,並且使樹脂逐步固化至凝膠狀態。此階段的成型壓力為全壓的1/3-1/2。
2、第二階段---中間保溫階段
3、第三階段---升溫階段
目的在於提高反應溫度,加快固化速度。此時,升溫速度不能過快,否則會引起暴聚,使固化反應放熱過於集中,導致材料層間分層。
4、第四階段---熱壓保溫階段
目的在於使樹脂能夠充分固化。從加全壓到整個熱壓結束,稱為熱壓階段。而從達到指定的熱壓溫度到熱壓結束的時間,稱為恆溫時間。熱壓階段的溫度、壓力和恆溫時間,也是由配方決定。
5、第五階段---冷卻階段
浸料壓模製模成型工藝
預浸料模壓成型工藝基本過程是:將一定量經一定預處理的模壓料放入預熱的模具內,施加較高的壓力使模壓料填充模腔。在一定的壓力和溫度下使模壓料逐漸固化,然後將製品從模具內取出,再進行必要的輔助加工即得產品。
壓制前的準備
1、裝料量的計算
在模壓成型工藝中,對於不同尺寸的模壓製品要進行裝料量的估算,以保證製品幾何尺寸的精確,防止物料不足造成廢品,或者物料損失過多而浪費材料。常用的估算方法有:
①形狀、尺寸簡單估算法,將複雜形狀的製品簡化成一系列簡單的標準形狀,進行裝料量的估算;
②密度比較法,對比模壓製品及相應製品的密度,已知相應製品的重量,即可估算出模壓製品的裝料量;
③注型比較法,在模壓製品模具中,用樹脂、石蠟等注型材料注成產品,再按注型材料的密度、重量及製品的密度求出製品的裝料量。
2、脫模劑的塗刷
3、預壓
將鬆散的粉狀或纖維狀的模壓料預先用冷壓法壓成重量一定、形狀規整的密實體。採用預壓作業可提高生產效率、改善勞動條件,有利於產品質量的提高。
4、預熱
5、表壓值的計算
在模壓工藝中,首先要根據製品所要求的成型壓力,計算出壓機的表壓值。成型壓力是指製品水平投影面上單位面積所承受的壓力。它和表壓值之間存在的函式關係。在模壓成型工藝中,成型壓力的大小決定於模壓料的品種和製品結構的複雜程度,成型壓力是選擇壓機噸位的依據。
壓制工藝
1、裝料和裝模
2、模壓溫度制度
模壓溫度制度主要包括裝模溫度、升溫速率、成型溫度和保溫時間的選擇。
①裝模溫度
裝模溫度是指將物料放入模腔時模具的溫度,它主要取決於物料的品種和模壓料的質量指標。一般地,模壓料揮發份含量高,不溶性樹脂含量低時,裝模溫度較低。反之,要適當提高裝模溫度。製品結構複雜及大型製品裝模溫度一般宜在室溫-90℃範圍內。
②升溫速率
指由裝模溫度到最高壓制溫度地升溫速率。對快速模壓工藝,裝模溫度即為壓制溫度,不存在升溫速率問題。而慢速模壓工藝,應依據模壓料樹脂的類型、製品的厚度選擇適當的升溫速率。
③成型溫度
樹脂在固化過程中會放出或吸收一定的熱量,根據放熱量可判斷樹脂縮聚反應的程度,從而為確定成型溫度提供依據。一般情況下,先確定一個比較大的溫度範圍,再通過工藝-性能試驗選擇合理的成型溫度。成型溫度與模壓料的品種有很大關係。成型溫度過高,樹脂反應速度過快,物料流動性降低過快,常出現早期局部固化,無法充滿模腔。溫度過低,製品保溫時間不足,則會出現固化不完全等缺陷。
④保溫時間
指在成型壓力和成型溫度下保溫的時間,其作用是使製品固化完全和消除內應力保溫時間的長短取決於模壓料的品種、成型溫度的高低和製品的結構尺寸和性能。
⑤降溫
在慢速成型中,保溫結束後要在一定壓力下逐漸降溫,模具溫度降至60℃以下時,方可進行脫模操作。降溫方式有自然冷卻和強制降溫兩種。快速壓制工藝可不採用降溫操作,待保溫結束後即可在成型溫度下脫模,取出製品。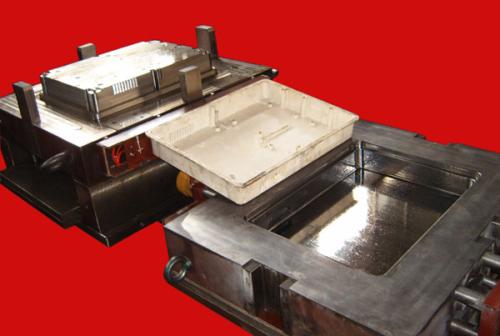
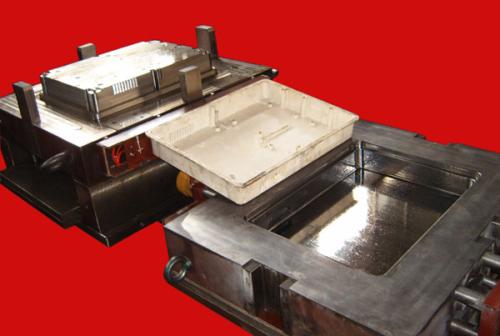