基本介紹
- 中文名:TnPM
- 外文名:Total Normalized Productive Maintenance
- 1:全員參與的,步步深入的
- 2:以全系統的預防維修為載體
八個要素
四個全
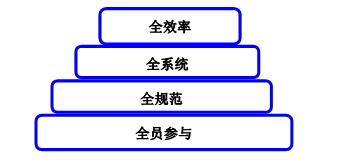
五個六
6S
6I
6Z
6T
6H
SOON模式
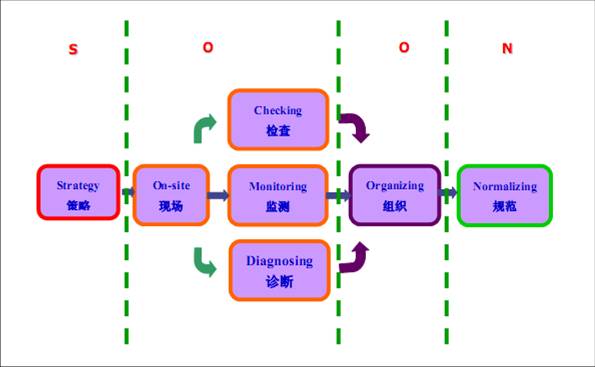
FROG體系
工作能力
成長約束
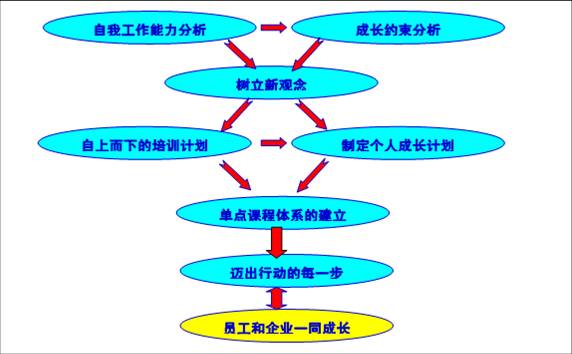
推進
一到六步
七到十三
規範
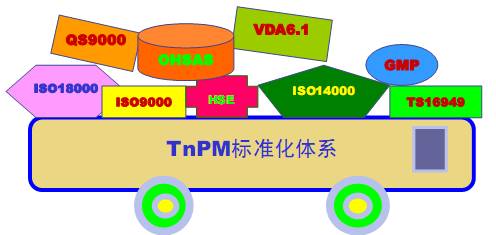
全面規範化生產維護(Total Normalized Productive Maintenance,簡稱:TnPM),是規範化的TPM,是全員參與的,步步深入的,通過制定規範,執行規範,評估效果,不斷改善來推進...
TnPM管理模式 全面規範化生產維護(簡稱TnPM),是以設備綜合效率和完全有效生產率為目標,以全系統的預防維修為載體,以員工的行為規範為過程,全體人員參與為基礎的生產...
全國TnPM大會是由全國TnPM大會組委會及中國機械工程學會設備與維修工程分會TnPM推進中心主辦,學府諮詢(國際)集團有限公司和現代設備管理研究院承辦的一場全國性學術會議...
《TnPM推進實務和案例分析》是2007年機械工業出版社出版的圖書,作者是徐保強,李葆文。本書中介紹了從TPM到TnPM發展變化的過程,主要內容包括TnPM基本理論、企業如何導...
TnPM理論框架的搭建是以清除6源、使用6項管理工具及不斷向6個零的極限目標靠近為基礎。...
《TnPM企業推進實務1001問》作者是徐保強,由機械工業在2007年出版。...... 生產現場管理人員和人事設備維護的工程技術人員作為參考書,尤其適合企業推進TnPM/TPM的設備...
《點檢屋TNPM設備點檢管理新視角》是2010年機械工業出版社出版的圖書,作者是李葆文。...
李葆文教授是TnPM管理體系創始人,國際知名設備管理專家,專注於TnPM設備人機系統精細化管理、維修策略設計、設備管理評價體系和評價指標設計、維修組織和資源配置、設備...
【摘要】TnPM是“全面規範化生產維護”的管理體系。以設備綜合效率和完全有效生產率,以全系統的預防維修系統為載體,以員工的行為規範為過程,全員參與為基礎的生產和...
五個“六”——TnPM體系的推進利器,五個“六”——TnPM體系的攀登階梯!全面規範化生產維護(Total Normalized Productive Maintenance,簡稱TnPM),是以設備綜合效率和...
廣州學府設備管理工程顧問有限公司成立於2005年,目前擁有一大批設備管理與維修領域的頂尖專家,為眾多企業提供設備管理規劃、TPM(全面生產維護)/TnPM(全面規範化生產...
全面規範化生產維護(Total Normalized Productive Maintenance,簡稱TnPM),是以設備綜合效率和完全有效生產率為目標,以全系統的預防維修為載體,以員工的行為規範為過程,...
徐保強,學府諮詢(國際)集團有限公司資深專家,總經理。現代設備管理研究院副院長兼秘書長,TnPM五階六維評價委員會 副主任委員兼秘書長 全國TnPM大會組委會 秘書長 ,...
首創“一目了然”工程的理論及方法,編著並由中國標準出版社出版的《“一目了然”工程標準管理手冊》成為製造等相關行業安全管理有效工具並獲第八屆全國TnPM大會功勳...
廣西中煙工業有限責任公司南寧捲菸廠[2] 、大慶油田礦區服務事業部物業管理二公司銀浪供熱分公司、江西中煙工業有限責任公司井岡山捲菸廠等多家企業推行TnPM設備管理...
《規範化的設備備件管理》是2008年4月在機械工業出版社出版的書籍,作者是徐保強。本書按照全面規範化生產維護體系(TnPM)中對備件進行規範化管理的總要求編寫。...
本書介紹如何將TnPM的全員規範化體系建設與員工的培訓和成長同步進行,主要內容包括如何進行員工能力分析、如何進行員工成長約束分析、如何制定個人成長計畫、如何建立自...
設備管理大視野是設備管理行業領先的綜合性入口網站,涵蓋了國內外最新設備管理新聞資訊、TnPM行業動態、TnPM/TPM學術板塊、設備管理百科、各種設備管理培訓資訊、還有每年...
本書介紹了考核設備管理水平的TnPM五階六維評價體系,同時介紹了團隊評價之後的員工激勵。書後附錄了國內外的設備管理評價,能夠起到拋磚引玉的作用,為中國目前十分...
企業現場TnPM推進指導 指導車間推進活動的現場開展 指導企業樣板機台打造 TnPM階段驗收診斷評價 員工的溝通和組織小組團隊活動 指導企業現場定置管理 指導企業現場可視化...
本鋼工學院機械系主任,副教授;中國機械工程學會設備與維修工程分會TnPM推進中心副主任。專注於點檢定修制、企業設備管理、液壓技術、企業ERP系統的研究與實施,具備...
名詞解釋TnPM的全員規範化是與員工的培訓和成長同步進行的。因而,員工能力成長決定企業的發展,也決定著 TnPM 的穩定持續發展。 我們把“員工未來能力持續成長”的...
名詞解釋 在TnPM體系里,除了生產現場操作員工參與的規範化活動之外,精心設計的檢維修系統解決方案具有重要的實踐意義。這個體系我們稱為SOON體系,即"Strategy--On-...