性能特點
金剛石刀具具有硬度高、
抗壓強度高、
導熱性及耐磨性好等特性,可在高速切削中獲得很高的加工精度和加工效率。金剛石刀具的上述特性是由金剛石晶體狀態決定的。在金剛石晶體中,
碳原子的四個
價電子按
四面體結構成鍵,每個碳原子與四個相鄰原子形成共價鍵,進而組成
金剛石結構,該結構的
結合力和
方向性很強,從而使金剛石具有極高硬度。由於聚晶金剛石(PCD)的結構是取向不一的細晶粒金剛石燒結體,雖然加入了結合劑,其硬度及耐磨性仍低於
單晶金剛石。但由於PCD燒結體表現為
各向同性,因此不易沿單一
解理面裂開。
主要指標
①PCD的硬度可達8000HV,為硬質合金的8~12倍;
③PCD的
摩擦係數一般僅為0.1~0.3(硬質合金的摩擦係數為0.4~1),因此PCD刀具可顯著減小切削力;
④PCD的
熱膨脹係數僅為0.9×10^-6~1.18×10^-6,僅相當於硬質合金的1/5,因此PCD刀具
熱變形小,
加工精度高;
⑤PCD刀具與有色金屬和
非金屬材料間的親和力很小,在加工過程中切屑不易粘結在刀尖上形成
積屑瘤。
套用
製造技術
製造過程
PCD刀具的製造過程主要包括
兩個階段:①PCD
複合片的製造:PCD複合片是由天然或人工合成的金剛石粉末與
結合劑(其中含鈷、鎳等金屬)按一定比例在高溫(1000~2000℃)、高壓(5~10萬個大
氣壓)下燒結而成。在燒結過程中,由於結合劑的加入,使
金剛石晶體間形成以TiC、SiC、Fe、Co、Ni等為主要成分的結合橋,金剛石晶體以
共價鍵形式鑲嵌於結合橋的骨架中。通常將複合片製成固定直徑和厚度的圓盤,還需對燒結成的複合片進行
研磨拋光及其它相應的物理、
化學處理。②PCD刀片的加工:PCD刀片的加工主要包括複合片的切割、刀片的焊接、刀片刃磨等步驟。
切割工藝
表1 PCD複合片切割工藝的比較
工藝方法-工藝特點
雷射加工-非接觸加工,效率高、加工變形小、工藝性差
在上述加工方法中,電火花加工效果較佳。PCD中結合橋的存在使電火花加工複合片成為可能。在有工作液的條件下,利用
脈衝電壓使靠近電極金屬處的工作液形成放電通道,並在局部產生放電火花,瞬間高溫可使
聚晶金剛石熔化、脫落,從而
形成所要求的
三角形、長方形或
正方形的刀頭毛坯。電火花加工PCD複合片的效率及
表面質量受到
切削速度、PCD粒度、層厚和電極質量等因素的影響,其中切削速度的合理選擇十分關鍵,實驗表明,增大切削速度會降低加工表面質量,而切削速度過低則會產生“拱絲”現象,並降低切割效率。增加PCD刀片厚度也會降低
切割速度。
PCD複合片與
刀體的結合方式除採用機械夾固和粘接方法外,大多是通過釺焊方式將PCD複合片壓制在硬質合金基體上。焊接方法主要有
雷射焊接、真空
擴散焊接、
真空釺焊、
高頻感應釺焊等。投資少、成本低的高頻感應加熱釺焊在PCD刀片焊接中得到廣泛套用。在刀片焊接過程中,焊接溫度、
焊劑和焊接合金的選擇將直接影響焊後刀具的性能。在焊接過程中,焊接溫度的控制十分重要,如焊接溫度過低,則焊接強度不夠;如焊接溫度過高,PCD容易石墨化,並可能導致“過燒”,影響PCD複合片與硬質合金基體的結合。在實際加工過程中,可根據
保溫時間和PCD變紅的深淺程度來控制焊接溫度(一般應低於700℃)。國外的
高頻焊接多採用自動焊接工藝,焊接效率高、質量好,可實現
連續生產;國內則多採用
手工焊接,
生產效率較低,質量也不夠理想。
刃磨工藝
PCD的高硬度使其材料去除率極低(甚至只有硬質合金去除率的萬分之一)。PCD刀具刃磨工藝主要採用
陶瓷結合劑金剛石砂輪進行
磨削。由於砂輪磨料與PCD之間的磨削是兩種硬度相近的材料間的相互作用,因此其磨削規律比較複雜。對於高粒度、低轉速砂輪,採用
水溶性冷卻液可提高PCD的磨削效率和磨削精度。砂輪結合劑的選擇應視磨床類型和加工條件而定。由於
電火花磨削(EDG)技術幾乎不受被磨削工件硬度的影響,因此採用EDG技術磨削PCD具有較大優勢。某些複雜形狀PCD刀具(如
木工刀具)的磨削也對這種靈活的磨削工藝具有巨大需求。隨著電火花磨削技術的不斷發展,EDG技術將成為PCD磨削的一個主要發展方向。
設計原則
PCD粒度
PCD粒度的選擇與刀具加工條件有關,如設計用於精加工或超精加工的刀具時,應選用強度高、韌性好、抗衝擊性能好、細晶粒的PCD。粗晶粒PCD刀具則可用於一般的
粗加工。PCD材料的粒度對於刀具的磨損和破損性能影響顯著。研究表明:PCD粒度號越大,刀具的
抗磨損性能越強。採用DeBeers 公司SYNDITE 002和SYNDITE025兩種PCD材料的刀具加工SiC基複合材料時的刀具
磨損試驗結果表明,粒度為2μm的SYNDITE002PCD材料較易磨損。

PCD粒度

圖1
PCD粒度有
亞微米、2μm、5μm、10μm、25μm及2~30μm,其中10μm粒度的CDW010材質為通用型,抗崩刃型和耐磨性均良好,一般情況,粒度越大,刀片材質更耐磨損,而
混合粒度2~30μm的CDW302材質的耐磨性更好。如圖1所示,為不同PCD粒度的抗崩刃性和耐磨性對比,還有
放電特性和
可磨性對比。
刀片厚度
通常情況下,PCD複合片的層厚約為0.3~1.0mm,加上硬質合金層後的總厚度約為2~8mm。較薄的PCD層厚有利於刀片的
電火花加工。DeBeers公司推出的0.3mm厚PCD複合片可降低磨削力,提高電火花的切割速度。PCD複合片與刀體材料焊接時,硬質合金層的厚度不能太小,以避免因兩種材料
結合面間的應力差而引起分層。
PCD刀具的幾何參數取決於工件狀況、刀具材料與結構等具體加工條件。由於PCD刀具常用於工件的精加工,切削厚度較小(有時甚至等於刀具的刃口半徑),屬於微量切削,因此其
后角及
後刀面對加工質量有明顯影響,較小的后角、較高的後刀面質量對於提高PCD刀具的加工質量可起到重要作用。
PCD複合片與刀桿的
連線方式包括機械夾固、焊接、可轉位等多種方式,其特點與套用範圍見表2。
表2 PCD複合片與刀桿連線方式的特點與套用
連線方式-特點-套用範圍
機械夾固-由標準刀體及可做成各種集合角度的可換刀片組成,具有快換和便於重磨的優點-中小型工具機
整體焊接-結構緊湊、製作方便,可製成小尺寸刀具-專用刀具或難於機夾的刀具,用於小型工具機
切削參數
PCD刀具切削參數對切削性能的影響
切削速度
PCD刀具可在極高的
主軸轉速下進行切削加工,但切削速度的變化對加工質量的影響
不容忽視。雖然
高速切削可提高加工效率,但在高速切削狀態下,
切削溫度和
切削力的增加可使刀尖發生破損,並使工具機產生振動。加工不同工件材料時,PCD刀具的合理切削速度也有所不同,如銑削
Al2O3強化地板的合理切削速度為110~120m/min;車削SiC顆粒增強鋁基複合材料及
氧化矽基工程陶瓷的合理切削速度為30~40m/min。
如PCD刀具的進給量過大,將使工件上殘餘幾何面積增加,導致
表面粗糙度增大;如進給量過小,則會使切削溫度上升,切削壽命降低。
增加PCD刀具的切削深度會使切削力增大、切削熱升高,從而加劇
刀具磨損,影響刀具壽命。此外,切削深度的增加容易引起PCD刀具崩刃。
不同粒度等級的PCD刀具在不同的加工條件下加工不同工件材料時,表現出的切削性能也不盡相同,因此應根據具體加工條件確定PCD刀具的實際切削參數。
失效機理
刀具的磨損形式主要有
磨料磨損、
粘結磨損(
冷焊磨損)、
擴散磨損、
氧化磨損、
熱電磨損等。PCD刀具的失效形式與傳統刀具有所不同,主要表現為聚晶層破損、粘結磨損和擴散磨損。研究表明,採用PCD刀具加工金屬基複合材料時,其失效形式主要為粘結磨損和由
金剛石晶粒缺陷引起的微觀晶間裂紋。在加工高硬度、高
脆性材料時,PCD刀具的粘結磨損並不明顯;相反,在加工低脆性材料(如碳
纖維增強材料)時,刀具的磨損增大,此時
粘接磨損起主導作用
套用領域
複合材料相比於其它材料具有質量輕、強度高、耐高溫、耐腐蝕等特性,成為航空航天領域的理想材料。隨著航空
航天複合材料的廣泛套用,如何正確選擇、
合理使用刀具進行高效高質量
切削加工是一個非常重要的問題。
航空航天製造業廣泛套用的刀具材料主要有
硬質合金和PCD刀具材料,其中,PCD刀具材料所占比重越來越大,在當今的航空製造中兩者成為航空航天業刀具發展中的主導刀具,套用範圍相當廣泛。
(2)汽車行業領域
PCD刀具於1973年在美國開始套用。自
汽車工業套用PCD刀具以來,PCD刀具在
北美汽車工業中的使用量高速增長。美國汽車公司使用PCD刀具加工的主要對象是發動機的鋁合金
汽缸體。
PCD刀具的套用涵蓋汽車幾乎所有
鋁合金零部件加工領域,包括專用階梯複合刀具,鑄鋁及鋁合金加工
絲錐,各種高精度孔複合
絞刀,複合鑽頭,大
倍徑鑽頭,高難度材料加工鑽頭等等。國內汽車企業如
一汽大眾,已廣泛使用PCD刀具加工汽車鋁合金零部件(如汽車鋁合金活塞、
鋁合金輪轂)。
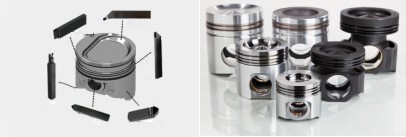
圖冊