超高速加工技術是指採用超硬材料刀具和磨具,利用能可靠地實現高速運動的高精度、高自動化和高柔性的製造設備,以提高切削速度來達到提高材料切除率、加工精度和加工質量的先進加工技術。
特徵
經濟效益指標
分類
發展
套用
特點
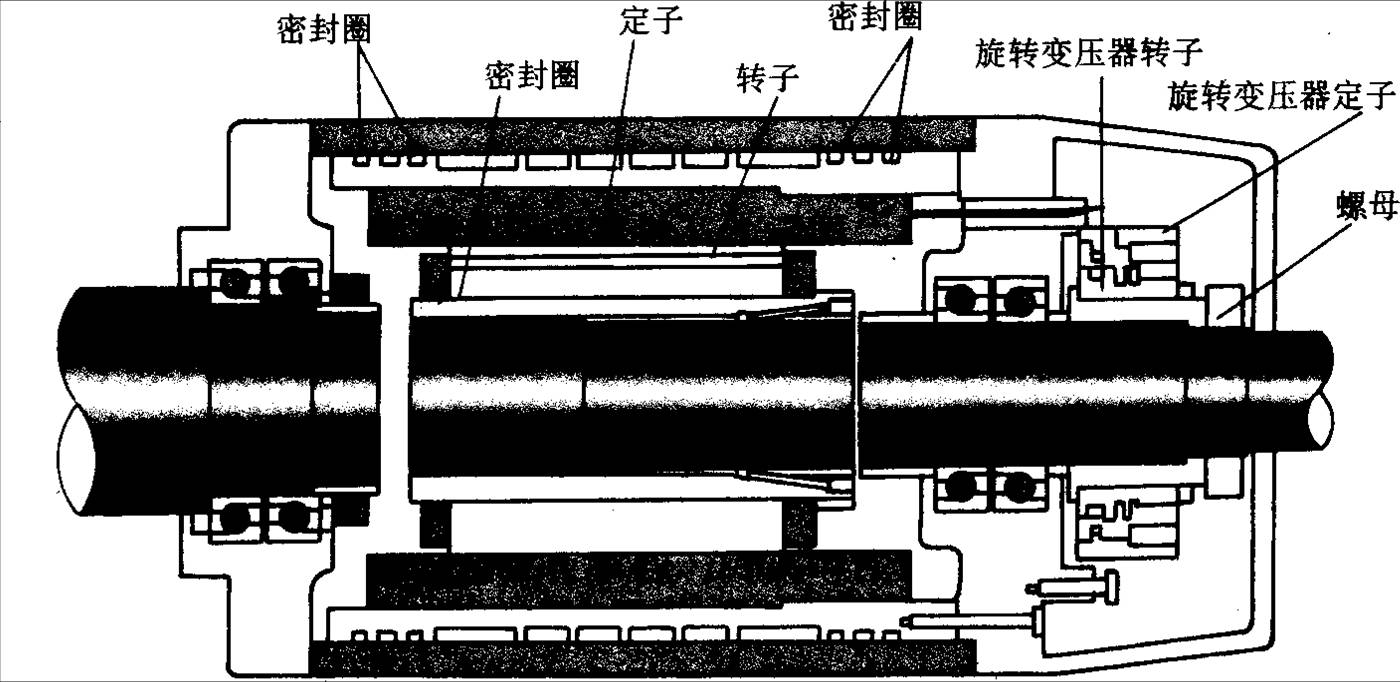
超高速加工技術是指採用超硬材料刀具和磨具,利用能可靠地實現高速運動的高精度、高自動化和高柔性的製造設備,以提高切削速度來達到提高材料切除率、加工精度和加工質量的先進加工技術。
超高速加工技術是指採用超硬材料刀具和磨具,利用能可靠地實現高速運動的高精度、高自動化和高柔性的製造設備,以提高切削速度來達到提高材料切除率、加工精度和加工...
超高速加工技術是指採用超硬材料的刃具,通過極大地提高切削速度和進給速度來提高材料切除率、加工精度和加工質量的現代加工技術。超高速加工技術主要包括:超高速切削...
超高速切削通常指切削速度超過傳統切削速度5-10倍的切削加工方法。...... 化高速切削工具機大量湧現,21世紀初,高速切削技術在工業已開發國家得到普遍套用,正成為切削加工...
高速切削加工作為模具製造中最為重要的一項先進制造技術,是集高效、優質、低耗於一身的先進制造技術。在常規切削加工中備受困擾的一系列問題,通過高速切削加工的套用...
《數控高速加工與工藝》是2013年機械工業出版社出版的圖書,作者是高永祥。...... 《數控高速加工與工藝》主要內容包括:高速加工技術的特點與套用;高速加工工具機的結構...
3.1 先進制造工藝技術概述3.1.1 機械製造工藝的定義和內涵3.1.2 先進制造工藝的發展趨勢3.1.3 先進制造工藝的特點3.2 超高速加工技術...
高速切削關鍵技術是一項先進的、正在發展的綜合技術,必須將高性能的高速切削工具機、與工件材料相適應的刀具和對於具體加工對象最佳的加工工藝技術相結合,充分發揮高速...
高速加工中心,不斷提高的工作性能是模具製造業得以高效和高精度加工模具的重要前提。在驅動技術的推動下,湧現出結構創新、性能優良的眾多不同類型的高速加工中心。90...
《高速加工數控編程技術》是2009年機械工業出版社出版的圖書,作者是王衛兵。本書全面介紹了高速加工的工具機、工具等相關知識,並重點講解了高速加工中的編程要點。...
《高速切削與五軸聯動加工技術》是2011年機械工業出版社出版的圖書,作者是陸啟建。...... 《高速切削與五軸聯動加工技術》是2011年機械工業出版社出版的圖書,作者是...
第3 章 先進制造技術的原理及套用 503. 1 精密與超精密加工技術 503. 2 高速與超高速加工技術 603. 3 特種加工技術 713. 4 微細加工技術 105...
《高速加工理論與套用》是由科學出版社出版,平裝,定價70元。...... 在高速加工理論基礎部分,給出了高速加工的定義,介紹了高速加工技術的發展和套用現狀,重點論述了...
高速加工技術的主要特點,論述用於模具工業的高速工具機、高速刀具和高速CAD/CAM系統等關鍵技術。 模具是製造業中使用量大、影響面廣的工具產品。沒有型腔模、壓鑄模...
《高速加工與數控編程》是電子工業出版社出版的圖書,作者是何慶。...... 本書闡述了高速加工機理及國內外在此方面的研究,詳細介紹了高速加工的關鍵技術,進行了高速...
《PowerMILL 10.0數控高速加工實例詳解》是機械工業出版社出版的圖書,作者是劉江 高長銀 黎勝容...
《先進數控加工技術》是教育部和財政部“中等職業學校教師素質提高計畫”中“數控技術套用專業師資培訓包開發項目(LBZD017)”的成果之一。為了適合骨幹教師的專業技術...
《難加工材料高效加工技術》主要介紹難加工材料的高效加工技術,其內容包括難加工材料的套用及其高效加工技術的發展現狀與趨勢,難加工材料的分類及其加工特點,難加工材料...
高速主軸部件是高速工具機最為關鍵部件之一,同時高速主軸單元的沒計是實現高速加工的關鍵技術之一。高速主軸單元的類型主要有電主軸、氣動主軸、水動主軸等。不同類型...
高速研磨機變速控制方法,屬於機械加工技術中的超精密加工技術,在研磨加工開始及結束兩個階段控制磨具轉速的變化,使之有一個緩慢、迅速、緩慢的提速和降速過程。其...