《超大型耐熱鋼焦炭塔製造組焊工法》是中國石化集團寧波工程有限公司和中國石化集團第五建設公司完成的工程建設類施工工法;完成人分別是俞松柏、瞿繼虎和胡明。該工法適用於材料為Cr-Mo珠光體、貝氏體耐熱鋼大直徑壓力容器的整體製造、現場分片組焊;還適用於大直徑壓力容器的整體製造。
《超大型耐熱鋼焦炭塔製造組焊工法》主要的工法特點是:採用1.25Cr-0.5Mo-Si+410S/1.25Cr-0.5Mo-Si材料增強韌性,提高設備的疲勞壽命,同時採用複合板提高了設備的耐腐蝕性能;使用立式組裝、分段組對焊接和剛性外加固圈,在預製場內形成流水作業,提高了機具的周轉率、人員勞動效率,降低施工成本和機械使用成本;減少了由於焦炭塔組焊對其他部位施工帶來的工期、安全等不利影響。
2011年9月30日,《超大型耐熱鋼焦炭塔製造組焊工法》被中華人民共和國住房和城鄉建設部評定為國家二級工法。
基本介紹
- 中文名:超大型耐熱鋼焦炭塔製造組焊工法
- 工法編號:YJGF77-2002
- 類別:工程建設類
- 主要完成人:俞松柏、瞿繼虎、胡明
- 審批單位:中華人民共和國住房和城鄉建設部
- 完成單位:中國石化集團寧波工程有限公司、中國石化集團第五建設公司
- 主要榮譽:國家二級工法(2009-2010年度)
形成原因,工法特點,操作原理,適用範圍,工藝原理,工藝流程,操作要點,材料設備,質量控制,安全措施,環保措施,效益分析,套用實例,榮譽表彰,
形成原因
焦炭塔是延遲焦化裝置的關鍵設備,長期的(除焦和充焦)在常溫至430/500℃的工況下交替運作,使塔體不斷經受冷熱疲勞,二相溫差引起局部的塑性變形,長期使用造成塔體鼓脹,尤其裙座與錐體封頭的搭接接頭處產生大量的不規則裂紋。採用鍛焊連體錐形封頭作過渡段,從而使裙座與錐封頭搭接處的疲勞壽命從不到600次提高到10000多次,設備材料也從15CrMoR提升到了1.25Cr-0.5Mo-Si/1.25Cr-O.5Mo,且氣液二相及以上部分採用了25Cr-0.5M。-Si+410S複合板材料,使得設備的耐蝕性也大為提高,但給設備製造組焊過程中的焊接、熱處理等工藝提出了新的要求。
在總結高橋石化、鎮海煉化焦炭塔製造經驗的基礎上,2006-2010年度在青島大煉油、中海油惠州大煉油和出口印度愛莎石油公司焦炭塔、新疆塔河延遲焦化焦炭塔的製造組焊過程中,針對新材料的焊接特點、技術質量要求和設備的不斷大型化,中國石化集團寧波工程有限公司和中國石化集團第五建設公司改進和開發了新的組裝、焊接和熱處理工藝,如開發新材料的焊接工藝、開發使用橫向埋弧自動焊的專有(技術)工藝、保證圓度的加固方法等。在技術開發和創新的同時,在原有的組裝、焊接和熱處理工藝工法的基礎上,增加了因運輸條件的制約無法整體或分段製作、運輸的大型焦炭塔在現場進行分片組焊等內容,中國石化集團寧波工程有限公司和中國石化集團第五建設公司在工程實踐基礎上總結完成了《超大型耐熱鋼焦炭塔製造組焊工法》。
工法特點
《超大型耐熱鋼焦炭塔製造組焊工法》有如下特點:
1、中國石化集團寧波工程有限公司和中國石化集團第五建設公司使用該工法製造的青島大煉油焦炭塔(Dg9400x39440)、中海油惠州大煉油焦炭塔(Dg9800x36600)、新疆塔河焦炭塔(Dg9000x38626),屬於巨大直徑的焦炭塔,而1.25Cr-0.5Mo-Si+410S/1.25Cr-0.5Mo-Si材料又在中國國內首次套用於焦炭塔。1.25Cr-0.5Mo-Si相比15CrMoR強度降低而韌性提高,從而提高設備的疲勞壽命,同時採用複合板提高了設備的耐腐蝕性能,但焊接時更容易產生延遲裂紋,同時如果坡口加工和焊接不當容易形成馬氏體組織而產生裂紋。
2、該工法在工廠組焊時採用將塔體採用立式組裝成大段(10米左右)、臥式組裝成整體的組裝工藝;環縫焊接釆用自行新開發的立式橫向埋弧焊工藝和臥式埋弧自動焊工藝相結合;熱處理採用了分段整體爐內熱處理及環縫局部電加熱熱處理工藝。
3、該工法鍛焊過渡段分4段(與原工法相比,直徑增大分段減少)進行爐外精煉、鍛壓、熱處理及壓彎(冷彎),坡口加工後進行組對焊接和熱處理,再進行機械加工和無損檢測。
4、該工法對於大直徑筒體進行臥式埋弧自動焊並進行良好的預後熱困難,加之1.25Cr-0.5Mo-Si+410S/1.25Cr-0.5Mo-Si焊接時若工藝操作不當易產生冷裂紋或延遲裂紋和馬氏體組織。該工法在原工法的基礎上,採用剛性外加固圈取代原來的內圈工字鋼加米字形加固,減少了對設備本身的損傷。並對加熱器進行改造,適合殼體轉動時的預熱,解決了殼體剛度不足、避免了轉動時的冷作硬化及埋孤焊接時的預後熱難題。
5、該工法在現場分片組焊時,為防止筒節變形採用立式組對,組對在水平剛性平台上進行,並採取合理加固措施,控制了筒節和筒體的橢圓度、端面不平度、稜角等,保證了組焊質量。
6、該工法分段立式組焊在預製場內形成流水作業,充分提高了機具的周轉率、人員的勞動效率,大幅降低施工成本;而且分段吊裝可使用吊裝能力較低的起重設備,降低機械使用成本。
7、該工法捨棄了以往在裝置焦池內進行組對吊裝的組焊方法,改在裝置外單獨設定立式分段組對的預製場地,並在焦炭塔框架與焦化爐中間站位吊車進行分段吊裝,減少了由於焦炭塔組焊對其他部位施工帶來的工期、安全等不利影響。
操作原理
適用範圍
工藝原理
《超大型耐熱鋼焦炭塔製造組焊工法》是根據焦炭塔的交貨狀態、結構及材料特點、工期及技術質量要求、可利用資源,結合在大型設備製造方面的經驗和優勢,最佳化組合而成的新工藝方法,其工藝原理為:
1、錐形連體過渡段的加工是通過進行爐外精煉、鍛壓、熱處理及精確的冷成型(通過改進鍛壓和成型工藝,鍛件的厚度比原來減少15毫米左右,節省材料,減少加工量),坡口加工後進行組對、焊接和熱處理,再進行機械加工和無損檢測,解決了大型錐體過渡段鍛件的製作難題。
2、該工法是中國國內首次使用1.25Cr-0.5Mo-Si+410S/1.25Cr-0.5Mo-Si材料。設計對材料和焊縫金屬的要求高:其中材料σb在415~585兆帕間(焊縫金屬不大於材料的1.1倍),σ0.2≥241兆帕;-20℃時衝擊值254焦耳;X係數W15PPm等。通過對板材、鍛件、特別是焊接材料的化學成分調整和熱處理的控制,經過大量的試驗和復驗,制定了合理先進的工藝措施,滿足了設計要求,且低溫衝擊值一般均在100焦耳以上。
3、通過對埋弧焊機的專門設計和改造,將焊機倚掛在設備壁板上,筒體上圈筒節頂部作為焊機行走路徑,並設計合理的坡口,使用了橫向埋弧自動焊焊接工藝。
4、焊接時採用電加熱方式保證了焊前預熱溫度、焊接層間溫度和焊後消氫溫度;同時,通過改造加熱器的結構形式(為滿足水平埋弧焊,在預熱用的加熱器上安裝滾珠軸承),並對塔體進行了剛性外加固,提高塔體剛度,保證塔體表面質量,解決了預熱、消氫處理難題,使用了埋弧自動焊焊接工藝。
5、採用現場組焊,在裝置外預製、分段組焊的方法能克服現場作業環境狹窄的制約因素;採用分段吊裝可選用合理的吊裝能力相對較小的吊車,滿足了因場地狹窄大型吊車無法站位的組焊要求,並對周邊單元施工影響也降到最低,提高吊車利用率,有效降低吊裝成本。
6、在預製平台組對時,通過投影檢測的方法,保證了下椎體上口與下口的同心度。設定多個預製平台進行筒節組對和分段組裝,可以形成流水作業,提高人員勞動效率和機具使用率。
7、在熱處理方面,利用大型熱處理爐(現場拼裝式的和正式的)在爐內進行立式分段整體熱處理和段間環縫局部熱處理相結合的方法,以及組焊完畢在基礎上進行整體內燃式、外保溫的熱處理方法,解決了大設備整體熱處理的技術難題,保證了熱處理質量。
工藝流程
一、加工廠加工工藝
工廠加工工藝流程見下圖: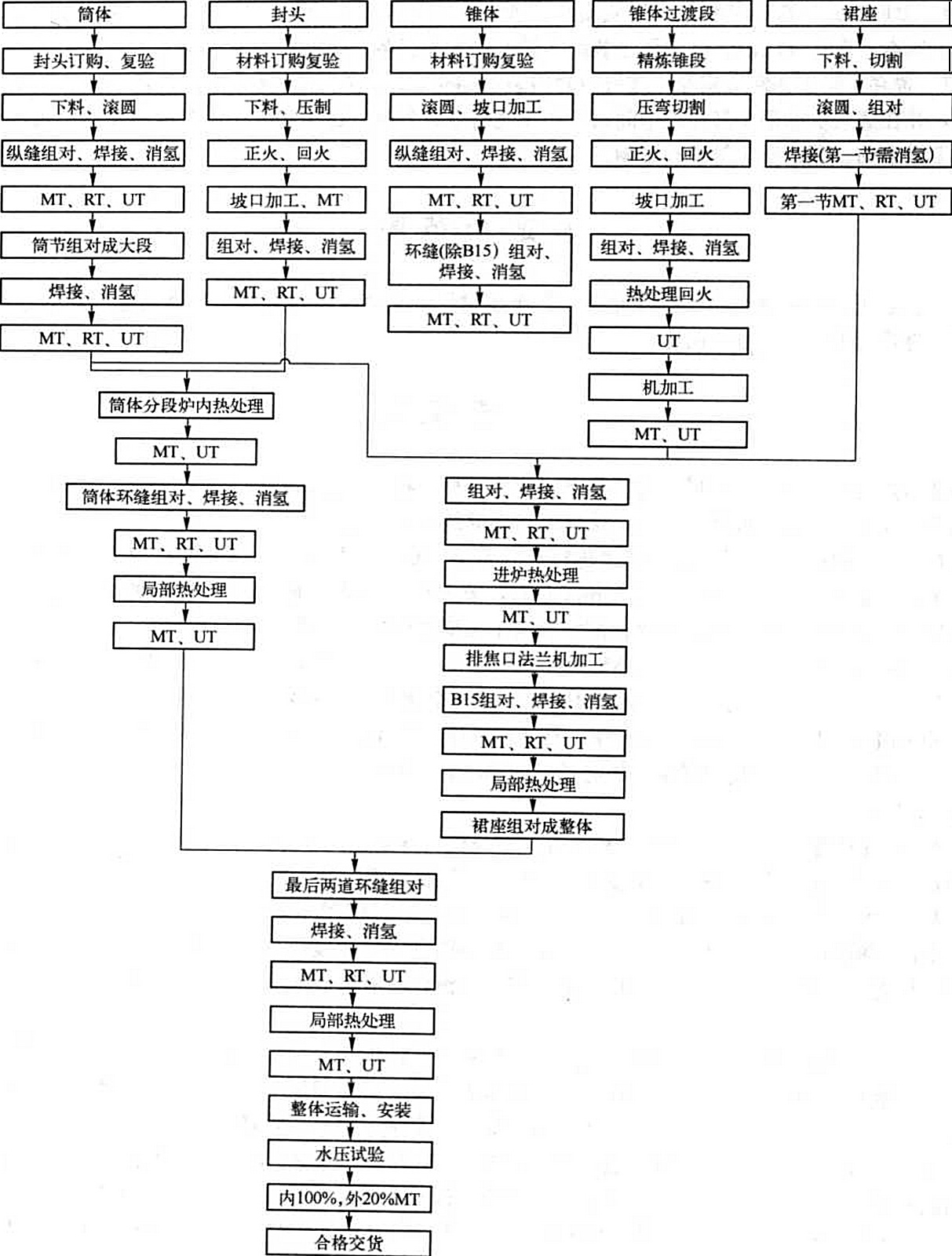
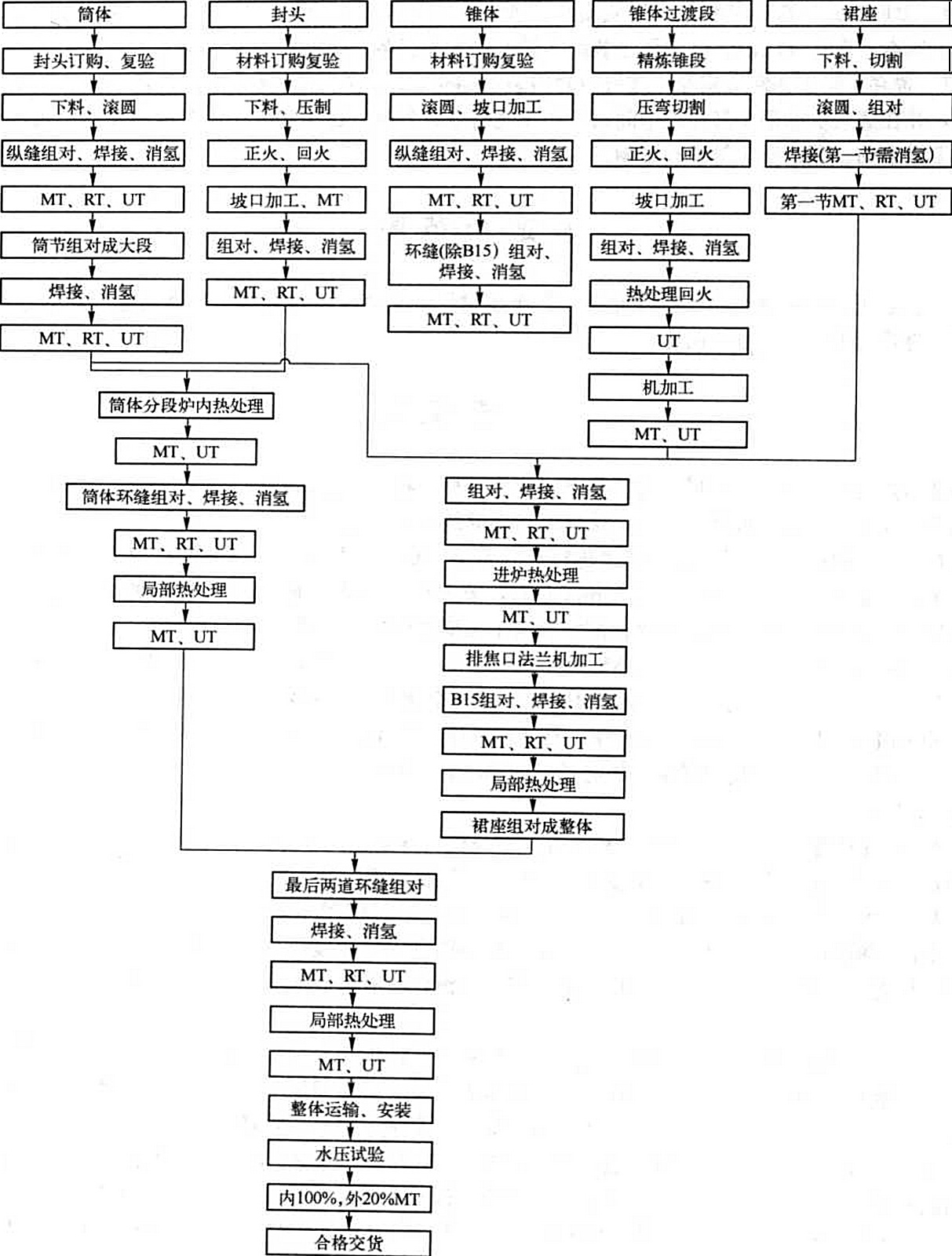
工廠加工工藝流程圖
二、現場組焊工藝
現場組焊分段立式組裝施工工藝流程見下圖: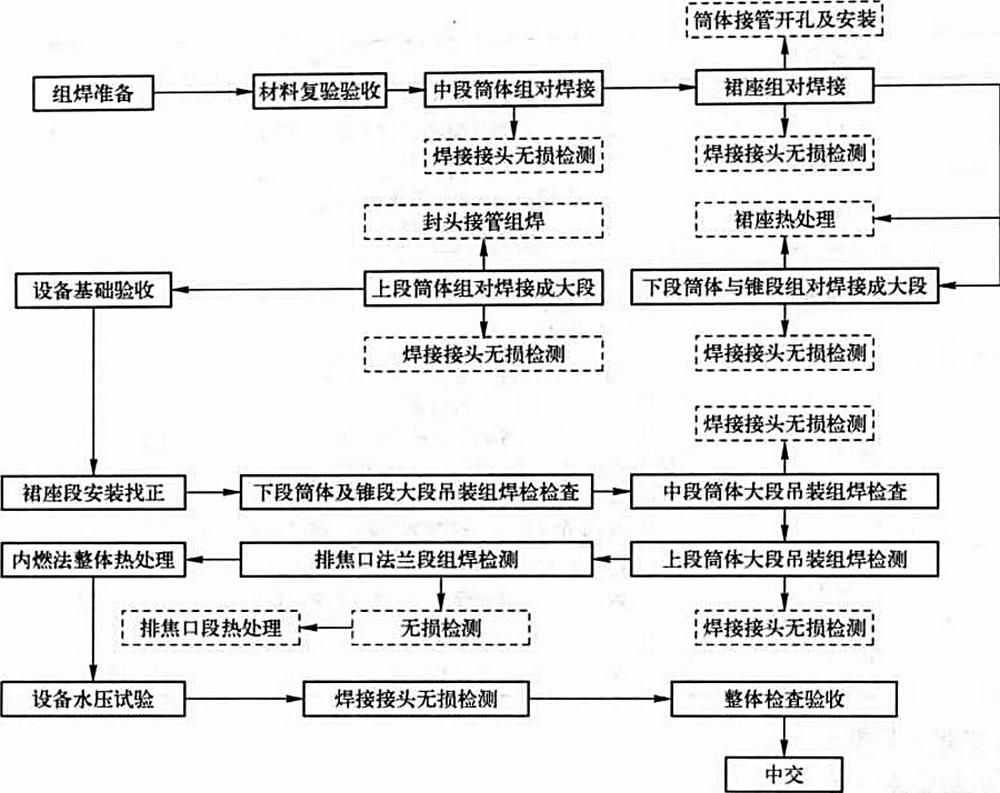
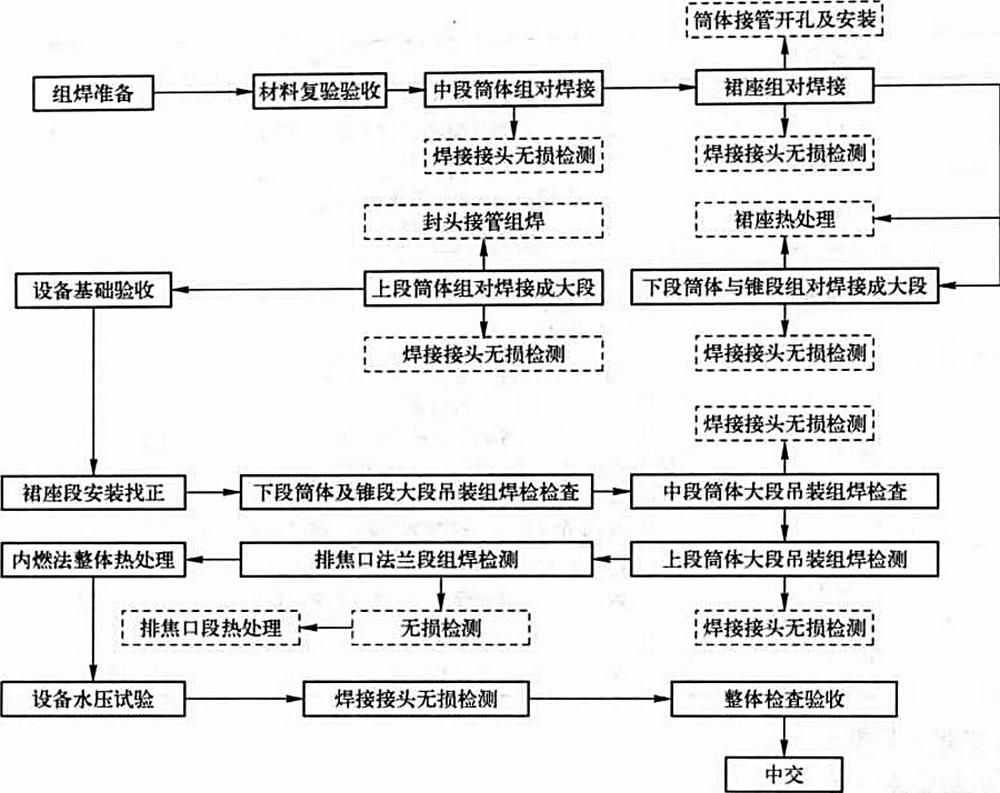
現場分段立式組裝工藝流程圖
三、具體工藝順序
根據吊裝、熱處理、焊接等工裝能力,按排版圖筒體組焊成7~12米段進行爐內熱處理,然後進行外加固;封頭單獨成體;錐體段除最下段外,其餘組焊成一體後與鍛焊過渡段組焊(B12),然後進行爐內熱處理;最下面段與排焦口法蘭(B16)焊接後進行爐內熱處理,然後進行法蘭密封面的加工。環縫先組焊B1縫、接著組對B5、B9縫、最後組焊B11縫,B15縫在立式狀態下組對焊接。
四、現場組焊分段
現場組焊分段原則:焦炭塔以分片形式運至現場,根據吊車吊裝能力,在指定區域組對焊接成三段,即裙座+大錐段+1節筒體構成下段、5節中間筒體為中段和球封頭+3節筒體構成上段,經過二次倒運至吊裝位置進行吊裝,用400噸吊車進行吊裝。
操作要點
一、鍛件製造工藝要點
錐形過渡段鍛件整體由4份組對拼焊組成,每份長約8米,均厚為245~255毫米,具體如下圖所示:
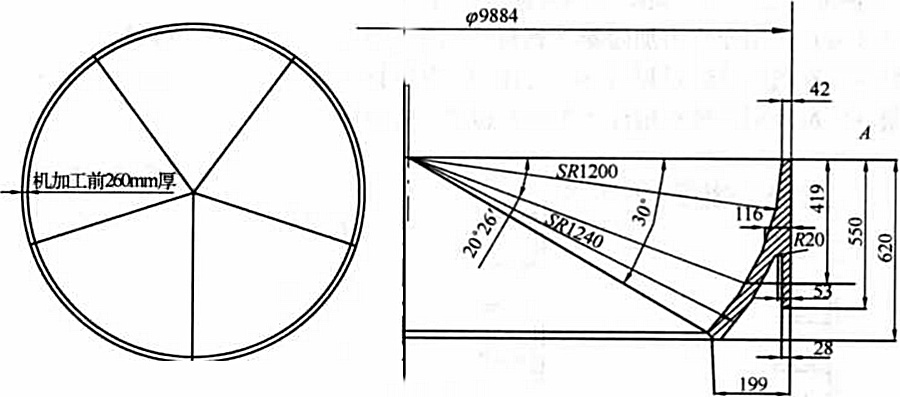
錐形鍛焊過渡段結構圖
(改進鍛壓和成型工藝後,有所減薄)各工序工藝要點見下表:
序號 | 工序名稱 | 工藝要求及控制措施 |
---|---|---|
1 | 制錠(爐外精煉) | 1、選用低S、P的優質生鐵; 2、控制Sn、Sb、As等元素,合理選擇Si、C,Mn含量,澆鑄系統乾燥清潔 |
2 | 鍛壓 | 1、厚度單側餘量220毫米左右,長度單側餘量50毫米餘; 2、鍛造比N6,加熱溫度1220℃、終鍛溫度>800℃,鍛造後熱處理:930℃±10℃x5小時(空冷)660℃±10℃x6小時(爐冷) |
3 | 壓彎 | 1、採用專用模具壓彎,採用冷彎成型; 2、公差為W±8毫米,表面凹坑≤5毫米,撓曲≤15毫米 |
4 | 單片熱處理 | 1、930℃±10℃x6小時空冷(風冷),660℃±10℃x6小時(爐冷); 2、爐冷至150℃時取樣。 3、試板檢驗 |
5 | 拼焊 | 1、坡口加工,按雙U形對稱坡口進行加工,並進行MT; 2、周長留10~15毫米餘量: 3、採用手工電孤焊,焊前預熱180~250℃、層間溫度均為200~250℃;焊接時採用交替焊以防焊接變形,減少焊接應力; 4、焊後進行690~700°Cx5小時消應力熱處理; 5、焊道清根打磨,控制線能量,內外交替分段退步焊 |
6 | 機械加工 | 1、用10米以上數控立車加工,並設胎模; 2、內外圓出白後進行UT,儘可能減少翻轉,避免切削量過大 |
7 | 檢測 | 1、試板力學性能試驗; 2、用直、斜探頭進行UT檢測、MT、PT檢測和幾何尺寸檢查 |
二、組裝工藝要點
1、工廠預製總體方案
(1)鍛件組對在平整的胎膜上按事先號制的線進行,無需進行加固。
(2)設計合理的坡口。縱縫坡口外大內小,以防止稜角的產生,環縫坡口應適用於橫向埋弧焊工藝;複合板的坡口復層開設5~6毫米的台階,以防止碳鋼焊材焊至復層上而產生裂紋;筒節的組對和筒體的組對應在剛性平台上進行,以防止產生連線埠不平。
(3)每3~4個筒節立式組焊成一大段(一般高約8~12米,也可以組對成5~8米段),環縫採用橫向埋弧焊進行焊接。環縫立式組對吊裝採用“十”字平衡梁進行,以防橢圓變形。熱處理前對筒體進行外加固,熱處理後將筒體放倒,利用300噸滾輪架將幾個大段臥式逐一組對焊接環縫而成整體,並製作埋弧自動焊專用操作平台架。具體程式根據焦炭塔製造排版圖。
(4)為保證圓度,外加固圈應整體製作並立式將其設定在筒體上。程式如下:
以加固圈外圈尺寸加焊接收縮量為直徑製作作為加固圈外翼板的筒節(內翼板可分瓣單獨滾制)→自動切割作為加固圈的腹板→腹板與外翼板筒節組對焊接f用自動切割機切割成單獨加固圈→放置在水平胎具上組焊內翼板成整體加固圈→將加固圈套置在塔筒體的指定位置,如下圖所示:
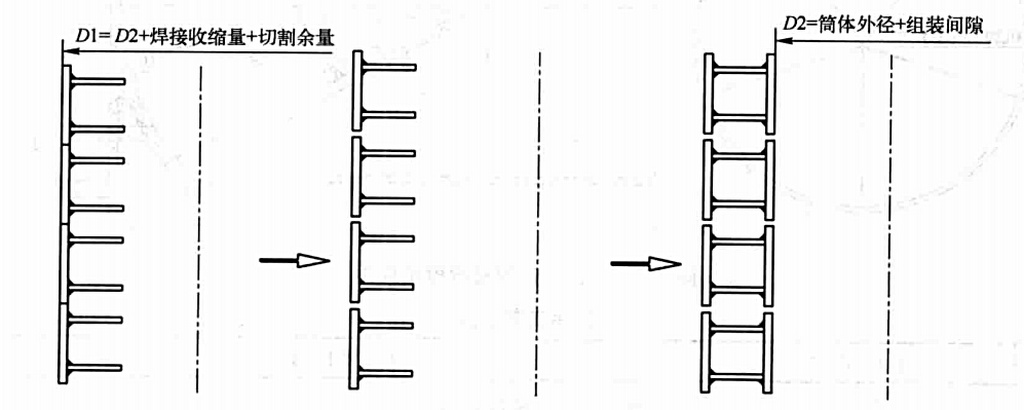
加固圈製作程式示意圖
注:分段筒體在熱處理爐內立式進行,爐子可以是電加熱也可以是油氣加熱。
(5)焦炭塔組焊分段情況如下圖所示。
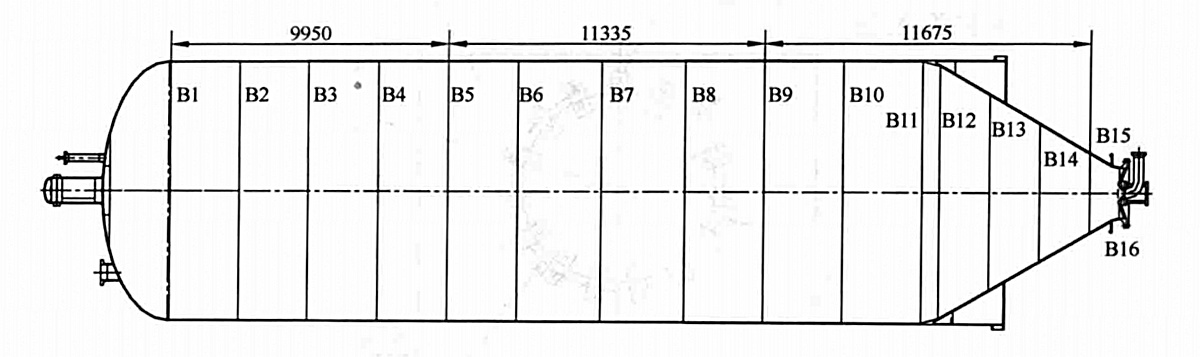
焦炭塔組焊分段示意圖
2、操作要點
(1)坡口設計要合理,要防止稜角產生,滿足埋弧焊的需要,而且複合板坡口須設定台階。外加固圈應整體製作、整體設定在筒體上,並用加減絲拉緊後焊接牢固,內側翼板局部(隔一定距離)採用與殼體相同的材料,以便與殼體進行部分的焊接。
(2)筒體、錐形封頭、橢圓封頭的立縱向焊縫組對焊接應在找平後的剛性平台上進行;環向焊縫組對、焊接以及整體組對,應在找水平後的滾輪架上進行,以保證圓度及端面不平度。環縫組對時應事先測量周長,使錯邊均勻。
(3)塔體整體組對在大型托滾上進行,托滾下面設定軌道,對托滾應找水平和對中,以免塔體轉動時產生偏重和偏心。
(4)為防止殼體失穩並避免殼體損傷,與滾輪架滾輪接觸應是外加固圈。
(5)工卡具、吊耳、引弧板等須統一設定,嚴禁強制組對。
(6)成型弧板、筒節、成段筒體的吊運應採用專用平衡梁,以防變形。
3、現場分片組裝方案和要求
3.1、筒節和筒體組對(見下圖)

筒節和筒體組對示意圖1
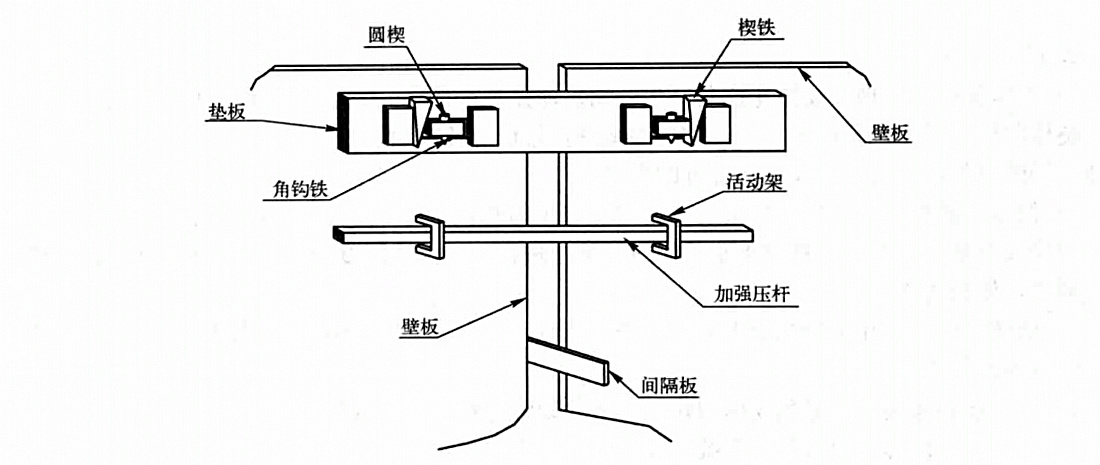
筒節筒體組對示意圖2
(1)筒節組對在剛性平台胎具上進行,組裝胎具的基準面必須找平,其水平度允許偏差為1毫米;
(2)在距離組對焊縫兩側約100毫米範圍處各設定一塊定位板,在組裝基準圓內,設定組裝胎具,以定位板和組裝胎距為基準,用工卡具使瓣片緊靠定位板和胎具,進行對口間隙和錯邊量的調整;
(3)組對完成後,在筒圈外測進行必要的防變形加固措施,可採用工廠組焊的外加固方法;
(4)筒體環縫組焊也應在剛性水平平台上進行,在底圈筒體的上口內側或外側每隔500毫米設定一塊定位板,以定位板為基準,相鄰筒節四條方位母線要求必須對正,在對口處每隔500毫米放置間隙片一塊,用調節絲槓調整組對間隙,用卡子、銷子調整錯邊量,使其沿圓周均勻分布,防止局部超標。
3.2、下段筒體組對,組對流程見下圖: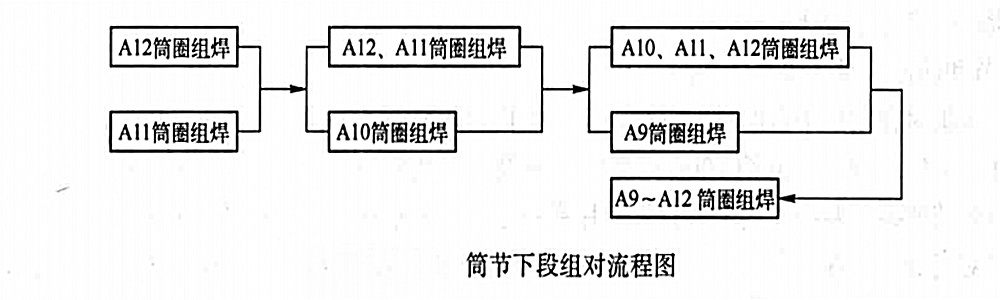
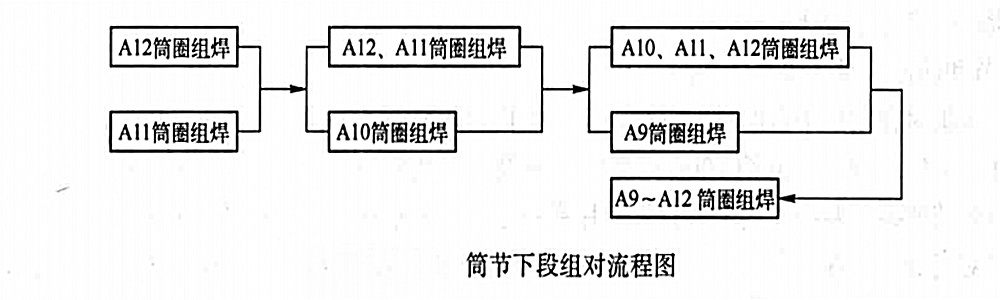
筒節下段組對流程圖
3.3、錐體組對
(1)錐體組對在鋼平台上劃出錐體大口組裝基準圓,組裝胎具的基準面必須找平,其水平度允許偏差為1毫米。
(2)以定位板和組裝胎距為基準,用工卡具使瓣片緊靠定位板和胎具,進行對口間隙和錯邊量的調整,胎具示意圖見下圖: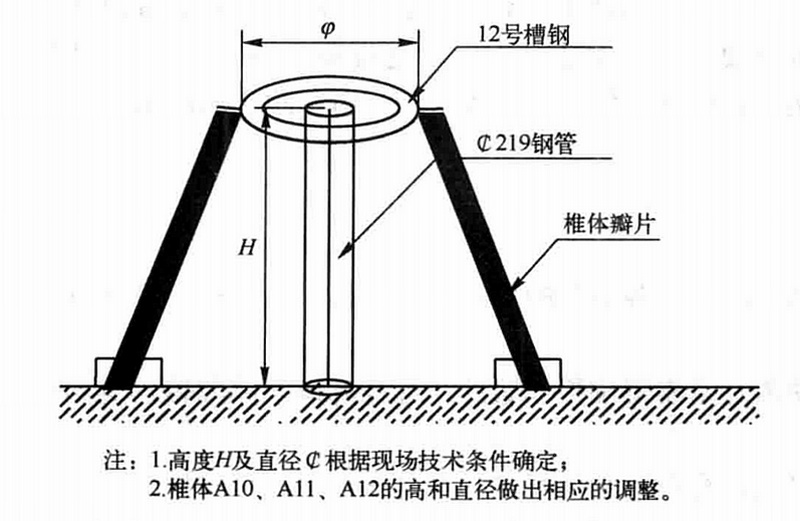
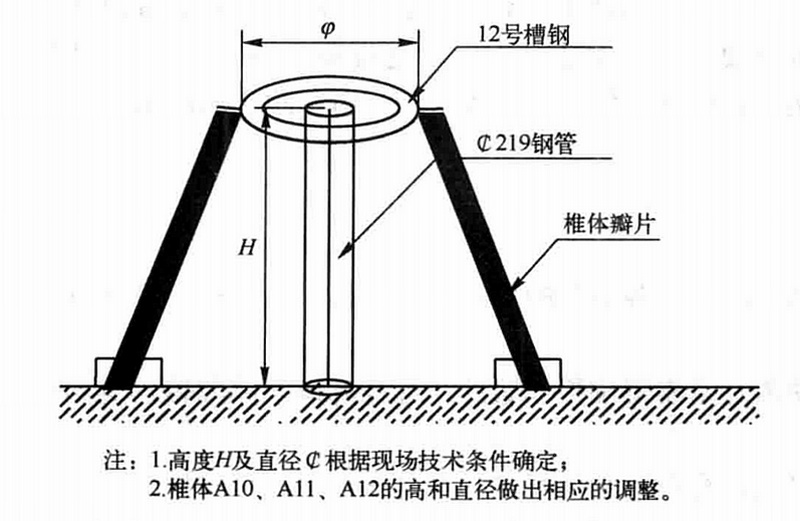
胎具示意圖
(3)錐段組對間隙、錯變數等具體允許偏差必須符合設計檔案要求,並要求上下口保持同心,同心圓的檢測方式如下圖: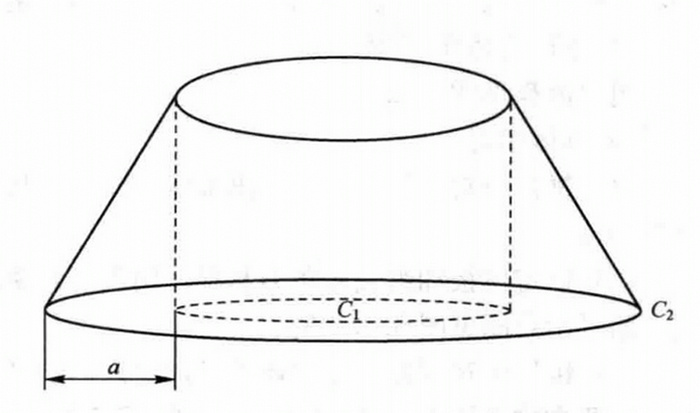
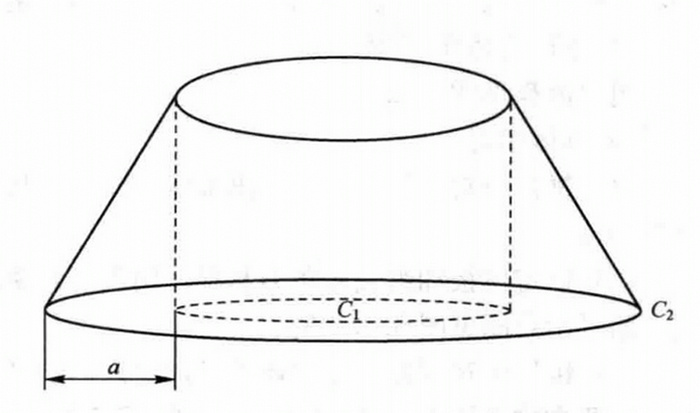
同心圓檢測方式
上圓投影到底板上的圓C1與底板定位圓C2間距相等,所有測量的a的數據相等。
(4)錐體環縫組對時,在底圈筒體的上口外側每隔500毫米設定一塊定位板,以定位板為基準,相鄰筒節四條方位母線應對正,在對口處每隔500毫米放置間隙片一塊,用調節絲槓調整組對間隙,用卡子、銷子調整錯邊量,使其沿圓周均勻分布,防止局部超標。
(5)錐體與圓筒筒圈組對要求同上。
3.4、上段組對(上段組對流程圖見下圖:)
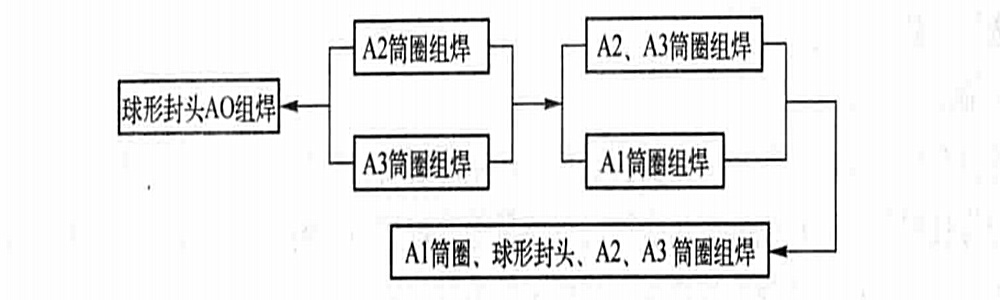
上段組對流程圖
(1)球形封頭的組對必須搭設臨時胎具,其水平度允許偏差為1毫米,球形封頭組對胎具示意如下圖:
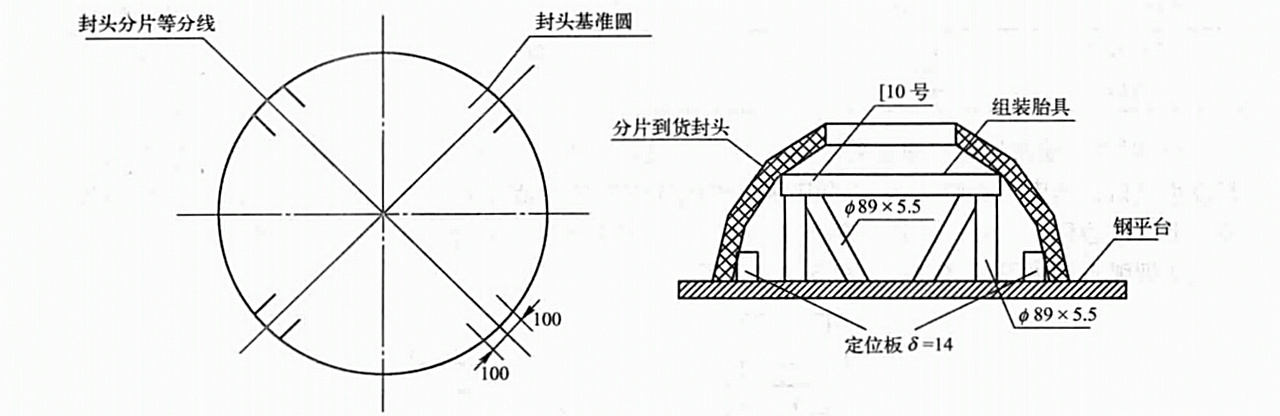
球形封頭組對胎具示意圖
(2)以定位板和組裝胎距為基準,用工卡具使瓣片緊靠定位板和胎具,進行對口間隙和錯邊量的調整。
(3)找正球形封頭整體的錯邊量、對口間隙、下口的周長、圓度等。
(4)球形封頭與圓筒筒圈組對時,根據球形封頭最大切面的幾何尺寸與相鄰的筒圈A1的幾何尺寸應進行相應的調整,具體以球形封頭的尺寸為準。
三、焊接工藝要點
1、工廠製作總體方案
(1)筒體、錐形封頭、橢圓封頭的縱向焊縫焊接採用立式手工電弧焊,筒節間的段內環縫採用橫向埋弧自動焊;筒體間、筒體與錐形封頭、橢圓封頭之間的環向焊縫,組對成大段採用臥式埋弧自動焊(見下圖:)。
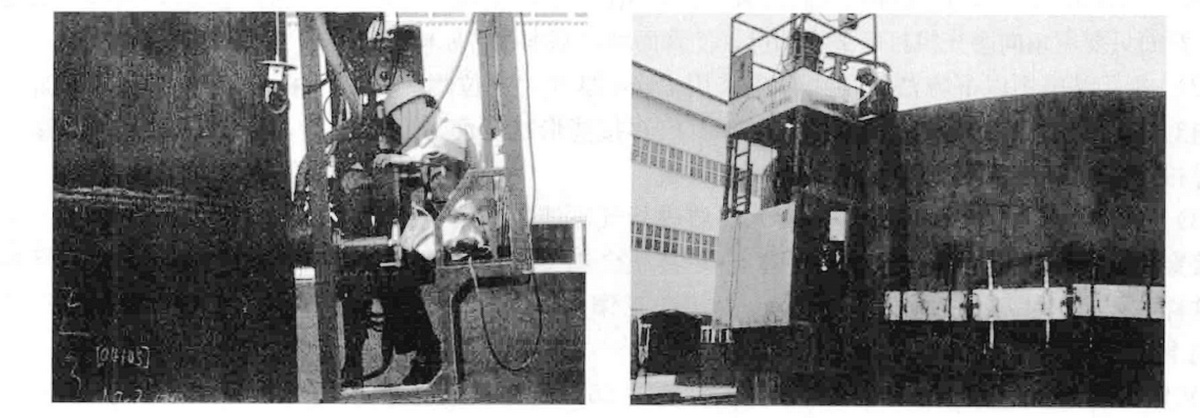
埋弧自動橫焊焊接狀態圖
2、現場分片組焊總體方案
(1)現場所有縱、環縫的焊接全部採用手工電弧焊。
(2)複合板段的復層和過渡層採用NiCrFe-3的Ni基焊材,避免使用其他奧氏體焊材而產生與鐵素體膨脹係數不一致的問題。
3、工廠製作操作要點
該工法採用低合金耐熱鋼,其焊接的主要特點是易產生冷裂紋、延遲裂紋,因此降低組裝應力、改善焊縫成型、進行焊接預後熱、控制並採用合理的線能量等是焊接的關鍵。同時坡口設計要合理,縱縫要防止稜角的產生,環縫要適合於橫向埋弧焊。焊接工藝參數如下表所示(橫向埋弧焊比水平埋弧焊要略小):
焊接方法 | 焊材 | 電流(安) | 電壓(伏) | 焊速(厘米/分鐘) | 線能量(焦耳/厘米) |
---|---|---|---|---|---|
手工電弧焊 | R307CRH | 110~160 | 23~26 | 6.5~12.5 | 17500~38000 |
埋弧焊 | H08CrMo | 580~650 | 34~36 | 32~48 | 24650~40800 |
(1)埋弧自動橫焊坡口通常採用不對稱X形坡口,上面角度稍大,根據壁板厚度一般取35°,下面開設小坡口,角度一般取15°,以利於提高焊縫性能並使清渣方便(渣容易自動脫落)、背面清根容易。坡口上口鈍邊留1~2毫米,下口鈍邊留5~6毫米,可有效地防止組對過程中出現錯邊而影響焊接質量。典型的埋弧自動橫焊焊接坡口如下圖所示:
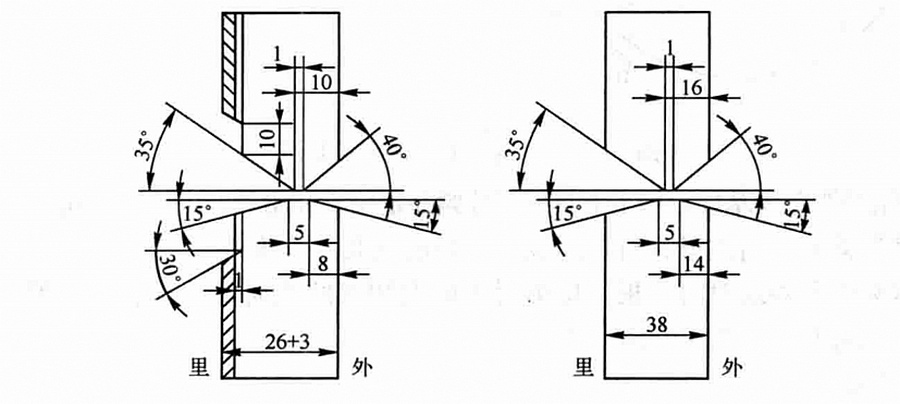
典型的埋弧自動橫焊焊接坡口(左側為複合板)
埋弧自動橫焊的一個關鍵工序在於根部打底焊接,為減少焊縫背面清根工作量,一般要求採取以下措施:
①組對時先在下部筒節上每隔3米左右點焊一塊與壁板同材質厚度為2毫米的小板條,以保證組對間隙均勻保持在1.5毫米左右,定位焊完成後用氧一乙快焰將小板條清除。這樣,根部打底焊接時焊縫背面穿透會較好,背面只要用角向磨光機打磨清根即可,使背面坡口基本保持原樣,以利於另一側的焊接工作。
②也可以採用以下方法,但小板條採用3毫米厚度,定位焊完成、小板條清除後,在背面焊縫貼上橫向對接接頭專用陶瓷襯墊,這樣,根部打底焊接能形成單面焊雙面成型,背面只需要局部修正即可進行焊接,省時省序,並能更好地提高焊接質量。
③若不採取上述措施,則焊縫背面需要進行氣刨清根,再進行打磨,直至露出新鮮金屬。由於橫向焊接穿透性較差,氣刨清根工作量大,有時甚至會刨得很深,焊接之前需要用手工電弧焊進行補焊找齊。這樣,雖然焊前工作量少了,但背面焊接前工作量增加,而且焊接質量還不容易保證。因此,宜採用上述兩種措施。
(2)定位焊前採用火焰預熱,預熱溫度為200~250℃,要求定位焊焊縫每段長度不小於150毫米,厚度12~16毫米,間距440~500毫米。
(3)每條縱向焊縫內外第一、二遍採用自上而下分段退步焊,其餘各遍自下而上一次焊完。
(4)焊前及焊接過程中,焊縫表面溫度應預熱溫度及層間溫度嚴格控制在150~250℃之間。
(5)定位焊及臨時工卡具、吊耳的焊接應採用和主體相同的焊接工藝及焊材,去除打磨後應進行表面檢查。
(6)雨、雪天、相對濕度大於85%、風速大於10米/秒等焊接環境下,未採取保護措施不得焊接。X寸接焊縫及角焊縫表面不得有咬邊。RT、UT、MT檢驗須在焊接完24小時後進行。
4、現場分片組焊操作要點
(1)焦炭塔所用的焊接工藝評定,須經特檢中心、業主等相關單位審批。焊接方法按照設計檔案要求選用採用焊條電弧焊和氣弧焊。
(2)焊縫坡口及組對形式
①焦炭塔環焊縫焊接形式見下圖:
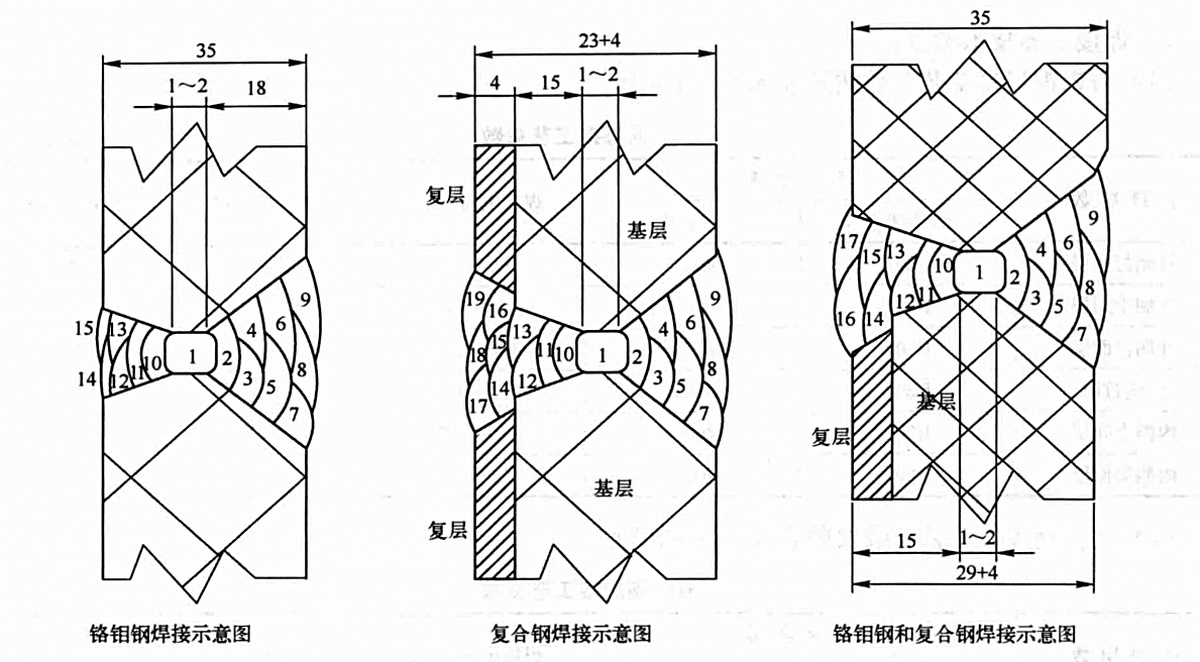
焦炭塔環焊縫焊接形式圖
②焦炭塔縱焊縫焊接形式見下圖:
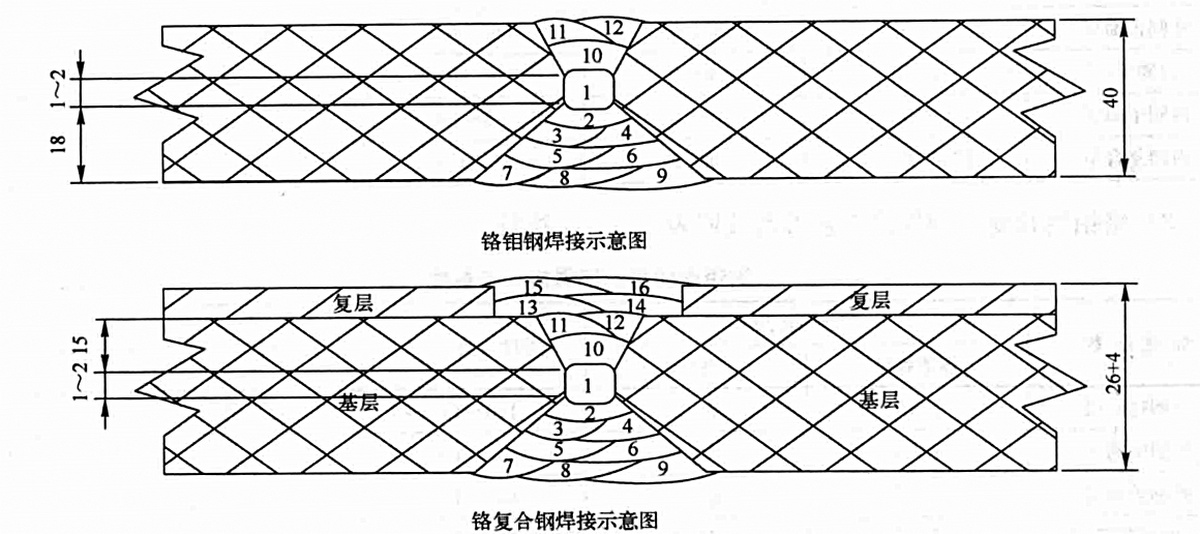
焦炭塔縱焊縫焊接形式圖
③焦炭塔裙座與下椎體焊縫形式見下圖:
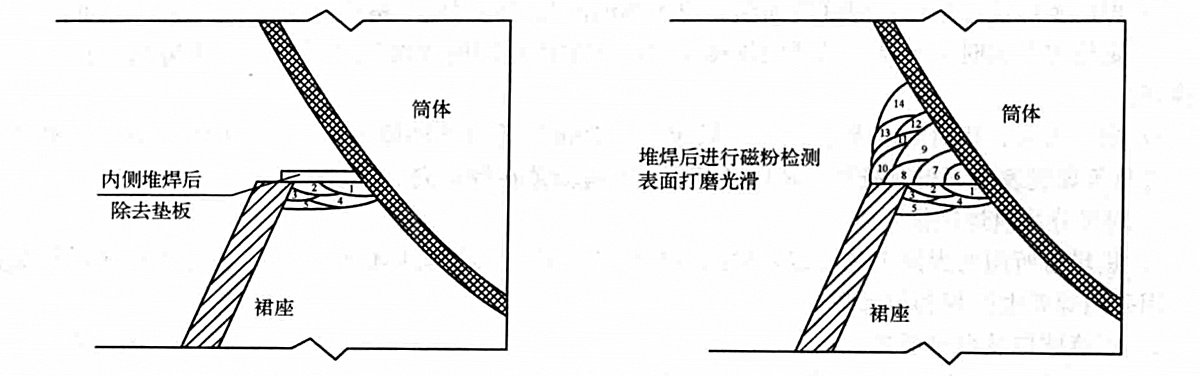
焦炭塔裙座與下椎體焊縫形式圖
(3)焊接主要技術參數:
①鉻鉬鋼焊接工藝參數按照下表執行:
焊縫層 | 焊條牌號 | 直徑Φ | 焊接電流(安) | 焊接電壓(伏) | 焊接速度(厘米/分鐘) |
---|---|---|---|---|---|
外側打底層 | R307 | Φ3.2 | 100~130 | 20~24 | 7~10 |
外側中間層 | R307 | Φ4.0 | 140~175 | 24~28 | 12~14 |
外側蓋面層 | R307 | Φ4.0 | 150~170 | 25~27 | 11~13 |
內側首層 | R307 | Φ3.2 | 100~130 | 21~24 | 8~10 |
內側中間層 | R307 | Φ4.0 | 140~175 | 24~28 | 12~14 |
內側蓋面層 | R307 | Φ4.0 | 150~170 | 25~27 | 12~13 |
②複合鋼焊接工藝參數按照下表執行:
焊縫層 | 焊條牌號 | 直徑Φ | 焊接電流(安) | 焊接電壓(伏) | 焊接速度(厘米/分鐘) |
---|---|---|---|---|---|
外側打底層 | R307 | Φ3.2 | 110~130 | 21~24 | 6~9 |
外側中間層 | R307 | Φ4.0 | 140~160 | 24~27 | 10~14 |
外側蓋面層 | R307 | Φ4.0 | 140~155 | 24~27 | 10~14 |
內側首層 | R307 | Φ3.2 | 110~130 | 21~24 | 7~9 |
內側中間層 | R307 | Φ4.0 | 150~180 | 25~28 | 10~14 |
內側複合層 | ENiCrFe-3 | Φ3.2 | 85~150 | 18~25 | 9~14 |
③鉻鉬鋼和複合鋼焊接工藝參數按照下表執行:
焊縫層 | 焊條牌號 | 直徑Φ | 焊接電流(安) | 焊接電壓(伏) | 焊接速度(厘米/分鐘) |
---|---|---|---|---|---|
外側打底層 | R307 | Φ3.2 | 110~130 | 21~24 | 7~9 |
外側中間層 | R307 | Φ4.0 | 150~180 | 25~28 | 10~14 |
外側蓋面層 | R307 | Φ4.0 | 150~170 | 25~27 | 10~14 |
內側首層 | R307 | Φ3.2 | 110~130 | 21~24 | 7~9 |
內側中間層 | R307 | Φ4.0 | 150~180 | 25~28 | 10~14 |
內側複合層 | EniCrFe-3 | Φ3.2 | 90~140 | 19~24 | 12~15 |
四、防變形操作要點
1、大直徑筒節無法進行校圓,因此縱縫的稜角應從坡口設計、滾弧及焊接程式和方法上加以控制。坡口採用不對稱X形坡口,滾弧時板端形成4~5毫米的負稜角如圖5.2.4-1所示(複合板的縱縫要達到6~7毫米)。焊接時,進行分段退步焊,焊接過程中根據變形情況及時調整焊接順序,過渡層及復層焊接要實施多道焊,不得擺動焊,以減少內應力控制變形。
2、由於殼體直徑大,壁厚相對較薄(Φ9800x28+3~42),放置在滾輪上會發生癟殼失穩,因此在殼體熱處理後安放上滾輪上之前,在殼體與滾輪接觸部位置的殼體外側設定有足夠剛度的“口”形支撐,(同時軌道和托滾要求找正)如下圖所示: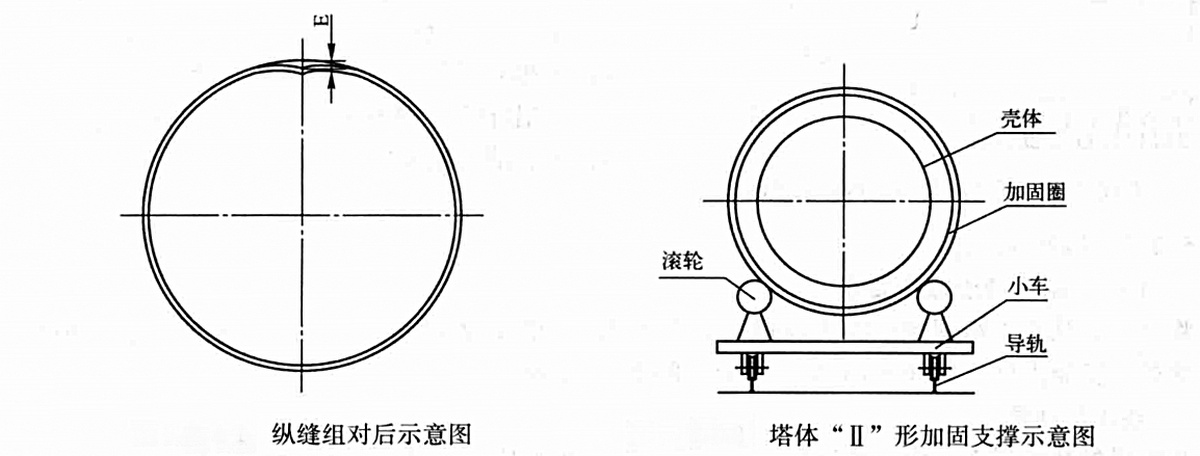
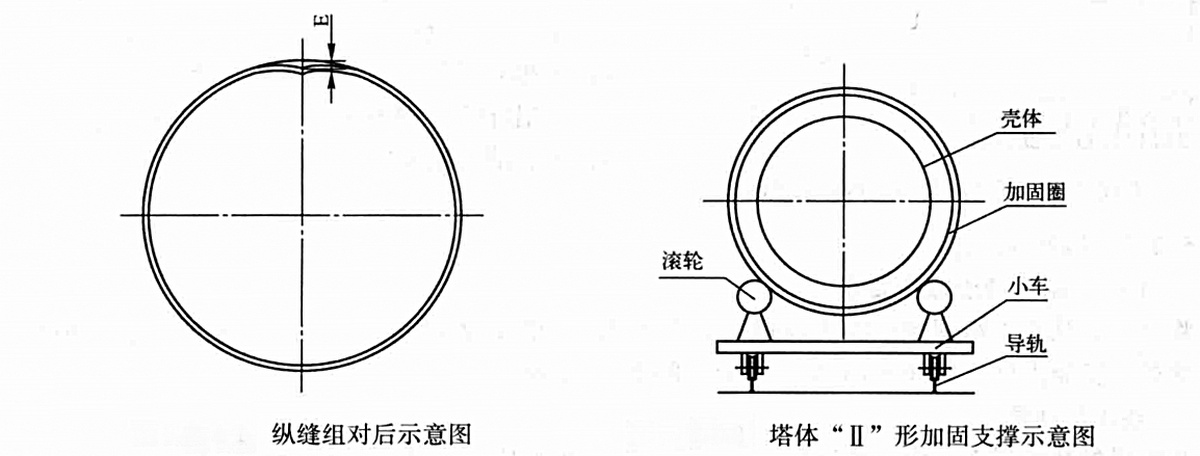
(左)滾弧時板端形成4〜5mm(右)軌道和托滾要求找正示意圖
3、環縫焊接接頭局部熱處理時,支撐點應設定均勻合理,儘量使被處理接頭不處於受力狀態;同時加熱器每串聯組應設定一熱電偶,以防過燒而變形。
4、熱處理爐內設定8個水平的活動支撐座,並設定好加固。
5、為保證排焦口的密封效果,所有錐段的連線埠圓度應合適。法蘭應先與錐體的一段焊接,單獨整體熱處理後進行法蘭密封面加工,然後與錐體進行無應力組對。焊接採用氯弧焊打底,4個焊工同時同向對稱進行焊接,如下圖:
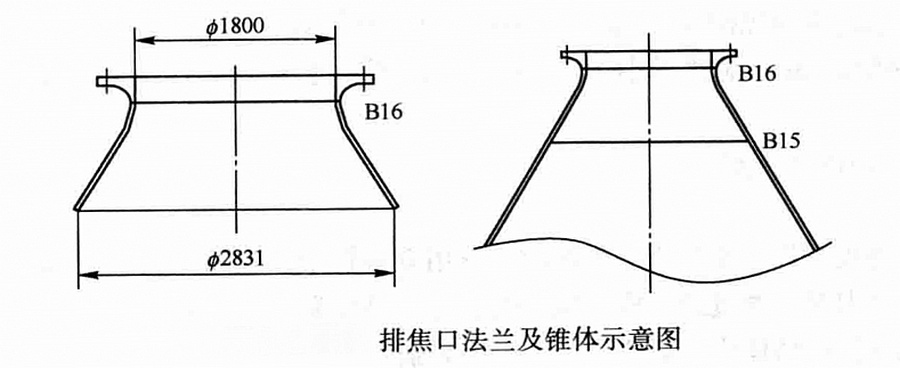
排焦口法蘭及椎體示意圖
五、防止裂紋操作要點
1、控制下料尺寸誤差,保證滾弧質量,組對時減少錯口,吊裝時使用“十”字平衡梁,避免強力組對,減少組裝應力。
2、焊前預熱及消氫
組對及工卡具的焊接應採用氧-乙炔焰按規定溫度進行預、後熱,以避免表面硬而產生表面裂紋;
焊前進行150~200℃的預熱,層間溫度控制在150~250℃之間,以降低殘餘應力、提高焊接接頭的強度,避免延遲裂紋的產生;焊後立即進行2小時350~400℃的消氫處理,利於氫的溢出、提高改善焊縫金屬的抗裂性能,避免延遲裂紋的產生。
3、復層刨邊時不得將復層材料殘留基層上,基層焊接時不得將復層材料融入焊池或焊到復層上,以免產生馬氏體組織而產生裂紋,焊後應仔細檢查,尤其是橫向埋弧焊,有懷疑時套用CuSO4溶液檢驗並徹底打磨清除。
4、焊接時選用合理的線能量,既要降低焊接拘束應力和焊接接頭的硬度,又要防止熱影響區晶粒粗大、焊接接頭衝擊韌性降低,避免產生延遲裂紋。
六、預熱和焊後消氫操作要點
預熱和焊後消氫至關重要且是一大技術難題,稍有不慎即產生延遲裂紋。焊前將磁鐵加熱器緊緊地固定在焊接工作面的背面,焊接完成後在加熱器的另一側設一層矽酸鋁纖維(用磁鐵的扁鋼固定)或也設定加熱器,將溫度升到350~400℃進行消氫。手工電弧焊及橫向埋弧自動焊焊接時,加熱器設定在焊縫的另一側;水平埋弧自動焊內側焊接時,在原熱器結構的基礎上將兩根4~6毫米厚的端頭(原磁鐵部位)各固定一隻滾珠軸承。各加熱器用2毫米扁鐵緊密串接緊貼殼體,分成上下兩半分別固定在自動焊框架上,並要求滾珠軸承與殼體接觸。當殼體轉動時通過軸承傳遞,使加熱器處於相對位置而不轉動,從而達到預熱的目的。焊接完成後在加熱器的另一側設一層矽酸鋁纖維,將溫度升到350~400℃進行消氫。預熱、焊後消氫用加熱器如圖所示。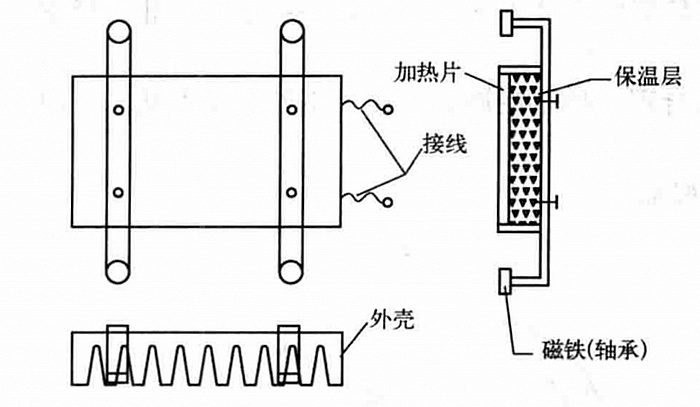
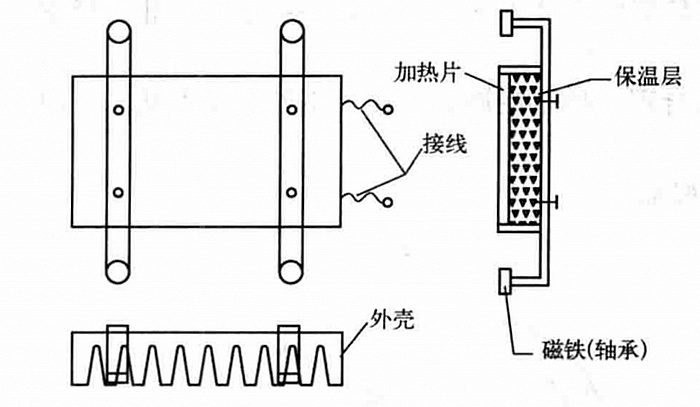
預熱消氫用加熱器示意圖
七、熱處理操作要點
1、工廠預製熱處理操作要點
將在立式狀態下組焊完畢的大段進行爐內整體熱處理,大段與大段組對而成的環縫採用局部熱處理。熱處理恆溫溫度:(690±15)℃。恆溫時間90~120分鐘。
(1)整體熱處理
每大段的熱處理在爐內立式進行。爐內設8個平衡滑塊式支座,使熱處理件的下連線埠處於水平位置並防止變形,在大段兩側連線埠附近外側進行周向加固,以保證熱處理後的整體圓度。測溫熱電偶應固定在工件上,每次處理的熱電偶數量不少於8個,以保證工件均勻受熱。
(2)局部熱處理
將履帶式紅外線加熱器緊密串聯(每3片為一組),每組設一熱電偶,並用8號鐵絲綑紮在被處理的外側,內外進行保溫,保溫寬度不小於1.8米、厚度不小於0.06米,用DWK-36電腦溫控儀進行控溫。
2、現場組焊熱處理操作要點
(1)熱處理方法
採用燃油法進行熱處理以焦炭塔內部為爐膛,選用0號輕柴油(隨氣溫選用標號)為燃料,焦炭塔外部用保溫材料進行絕熱保溫,通過鼓風機送風和噴嘴將燃料油噴入並霧化,由電子點火器點燃,隨著燃油不斷燃燒產生的高溫氣流在塔體內壁對流傳導和火焰熱輻射作用,使塔體升溫到熱處理所需的溫度。
(2)熱處理工藝流程,見下圖: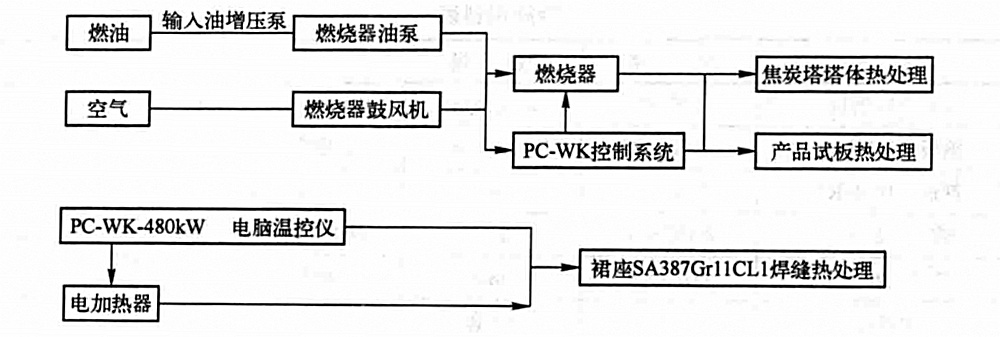
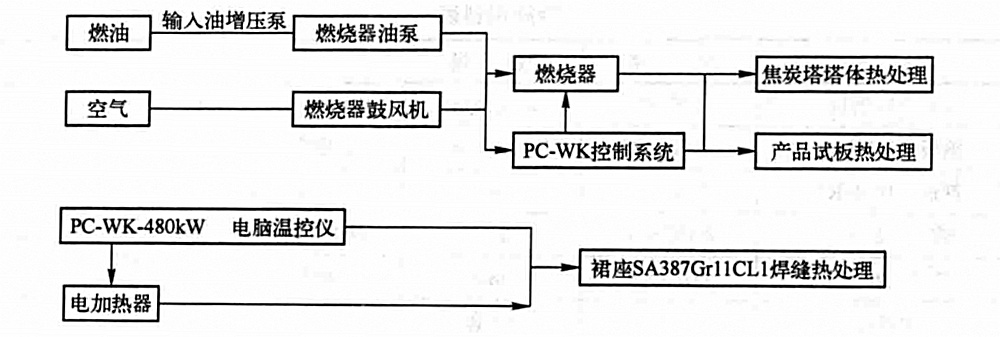
熱處理工藝流程
(3)熱處理工藝參數
恆溫溫度:690°C±14°C;恆溫時間:2小時;升溫速度:50~80°C/小時(≤400°C時可不予控制);降溫速度:50~80°C/小時(≤400°C時可不予控制);恆溫時的最大溫差:≤28°C:升溫時的最大溫差:≤100°C;降溫時的最大溫差:≤120°C。
(4)熱處理工藝系統控制
熱處理系統由燃油、供油、溫度測量、形態測量和排煙系統組成。
①燃油系統
採用燃燒器與焦炭塔底部的管口法蘭,通過過渡法蘭相對接,用一套微機系統對熱處理過程進行智慧型化控制,以滿足工藝要求,燃料採用0號柴油(按氣溫選標號)通過油泵送油,由電磁閥控制經噴嘴後噴出,霧化的燃燒油,由電子點火器自動點燃柴油進行燃燒。燃燒器上的鼓風機風量按預先設定的風油比助燃。
②供油系統
根據熱工計算,本次焦炭塔熱處理最大耗油量為1164升/小時,單台熱處理耗油量W8噸,儲油罐一次裝油量應保證塔體熱處理全周期所需油量的1.5倍。
③溫度測量控制系統
溫度測量監控系統由熱電偶,補償導線和一套PC-WK型集散控制系統對溫度進行智慧型化測量和控制。
④測溫點布置
按照《鋼製壓力容器焊接工藝評定》JB/T4708-2000、美國ASME的有關技術標準的要求,本次熱處理在塔體上共設測溫點63個,每塊焊接試板各設定一個熱電偶。其中封頭上布置15個、筒體上布置36個、錐體布置12個。
⑤熱電偶安裝
採用儲能式熱電偶點焊機將熱電偶牢固地點焊在塔體壁板,煙道氣和試板應單獨另設熱電偶。試板和接管按規範都布置熱電偶,在熱處理過程中往往因外力和操作不慎碰斷電偶,又因高溫期間無法補焊和修復,因此對試板、接管等關鍵部分採用雙熱電偶以備發生故障及時替代更換,在每段多布置1至2點作為備份。補償導線應妥善固定,以防燒毀。各熱電偶型號均為K型操銘一鐐矽,補償導線採用K型雙芯線。
⑥溫度監測
溫度監測配置兩套系統,一套是EH100-24長圖自動平衡記錄儀2台,共可記錄48個測溫點,另一套是微機集散型溫度監控系統,3秒掃描一個測溫點巡迴檢測各測溫點的溫度,並與設定的熱處理工藝曲線進行比較對照,從而向燃燒器給出具體燃油控制量,同時按工藝每30分鐘列印1份各點溫度的報表。
3、硬度檢測
硬度測試在整體熱處理後,對所有焊縫進行硬度測試(包括母材、焊縫金屬和熱影響區)。硬度值≤225HB。
材料設備
一、材料用料
中國石化集團寧波工程有限公司和中國石化集團第五建設公司在青島大煉油延遲焦化裝置4台焦炭塔的製造組焊中,採用該工法需用主要措施材料用料見下表:
序號 | 名稱 | 規格 | 數量 | 用途 | 備註 |
---|---|---|---|---|---|
1 | Cr-Mo鋼板 | 336/42 | 12平方米/8平方米 | 吊耳、刀把、孤板 | - |
2 | 鋼板(16MnR) | 828-36 | 180平方米/95平方米 | 工裝胎具、加固圈 | 分可重複利用 |
3 | 鋼板(16MnR) | 810-16 | 16平方米 | 組對胎具 | - |
4 | 管子(20號) | Φ325x10 | 30米 | 封頭、筒體組對胎具 | (重複利用) |
5 | 管子(20號) | Φ159x6 | 48米 | 封頭組對胎具 | - |
6 | 加減絲 | - | 60套 | - | - |
7 | 道木 | - | 60根 | 擺放筒體 | - |
8 | 防火石棉布 | - | 約100平方米 | 防火 | - |
9 | 安全網 | - | 約240平方米 | - | 符合安全要求 |
10 | 竹跳板 | - | 250片 | 操作平台 | - |
11 | 竹拍子 | - | 100片 | 操作平台 | - |
二、機具設備
中國石化集團寧波工程有限公司和中國石化集團第五建設公司在青島大煉油延遲焦化裝置4台焦炭塔的製造組焊中,採用該工法需用的主要機具設備見下表:
序號 | 名稱 | 規格 | 數量 | 用途 | 備註 |
---|---|---|---|---|---|
1 | 吊車 | 100噸 | 2台 | 縱縫組對、翻轉、環縫組對,大段進出 | - |
2 | 吊車 | 50噸 | 2台 | 熱處理爐。 | - |
3 | 汽車吊 | 75/50噸 | 各1台 | 大段運輸、翻轉 | - |
4 | 烘烤房 | - | 2個 | - | - |
5 | 烘烤箱 | YGCH-G-60 | 2台 | 焊材焊劑烘烤 | - |
6 | 恆溫箱 | YGCH-X-200 | 1台 | - | - |
7 | 電焊機 | ZXG7-300 | 6台 | - | - |
8 | 橫向埋弧焊機 | - | 3台 | 橫向自動焊 | 改造 |
9 | 電焊機 | DC-1000 | 2台 | 埋弧焊用電源 | - |
10 | 氣刨機 | QBT-1000 | 3台 | - | - |
11 | 電腦溫控儀 | 360kW | 3台 | - | - |
12 | 加熱器 | 860x260 | 350片 | 預熱、局部熱處理 | - |
13 | 千斤頂 | 10噸/5噸 | 6個 | 組對用 | - |
質量控制
一、質量規範標準
施工企業採用《超大型耐熱鋼焦炭塔製造組焊工法》時應執行的主要規範、標準:
- 《鋼製壓力容器》GB150-1998
- 《鋼製化工容器製造技術要求》HG20584-1998
- 《鋼製塔式容器》JB/T4710-2005
- 《承壓設備無損檢測》JB/T4730-2005
- 《承壓設備用碳素鋼和合金鋼鍛件》NB/T47008-2010
- 《壓力容器用鋼焊條訂貨技術條件》JB/T4747-2002
- 《鋼製壓力容器焊接工藝評定》JB4708-2000
- 《鋼製壓力容器焊接規程》JB/T4709-2000
- 《鋼製壓力容器產品焊接試板的力學性能檢驗》JB/T4744-2007
- 《固定式壓力容器安全技術監察規程》TSGR0004-2009(原《壓力容器安全技術監察規程》99版)
- 《焦炭塔製造技術條件》11060-C-101A~D
二、質量保證措施
1、認真執行國家有關法規、標準和質量體系檔案要求,做好過程質量控制。
2、編制詳細的質量檢驗及控制計畫並編制工藝、焊接、熱處理、運輸、試壓、油漆等作業指導書。並設立如下質量控制重點:
(1)制訂訂貨技術協定、工藝檔案編審,主材及焊接材料的訂貨。
(2)焊接工藝及熱處理工藝試驗、焊工培訓、工藝評定、焊工考試。
(3)材料、半成品(尤其是封頭)的復驗、驗收。下料允差、錯口、稜角、橢圓度的控制。
(4)預後熱溫度控制,熱處理過程、尤其是局部熱處理溫度均勻性的控制。
(5)焊材發放、回收,焊接過程工藝紀律檢查。
(6)廣品焊接、驗證試板的製作與檢驗。
3、嚴格工藝紀律,控制錯邊量和裝配間隙,徹底進行焊前坡口表面及層間的清理;加強材料表面的保護;對焊前預熱、焊後消氫處理及最終熱處理都設專人測溫;對咬邊、裂紋、氣孔、夾渣做專職檢查;合理設定工裝胎具及吊耳,減少對母材表面的損壞,嚴禁強力組裝。
4、嚴格按規範標準進行原材料、焊縫(焊接接頭)、試板、鍛件、焊材的機械性能、化學成分、硬度等的檢驗和測試,質檢員和責任工程師對檢測、檢驗過程和結果進行跟蹤檢查。
三、質保體系
施工企業採用《超大型耐熱鋼焦炭塔製造組焊工法》時加工廠質保體系和現場施工質保體系見下圖:
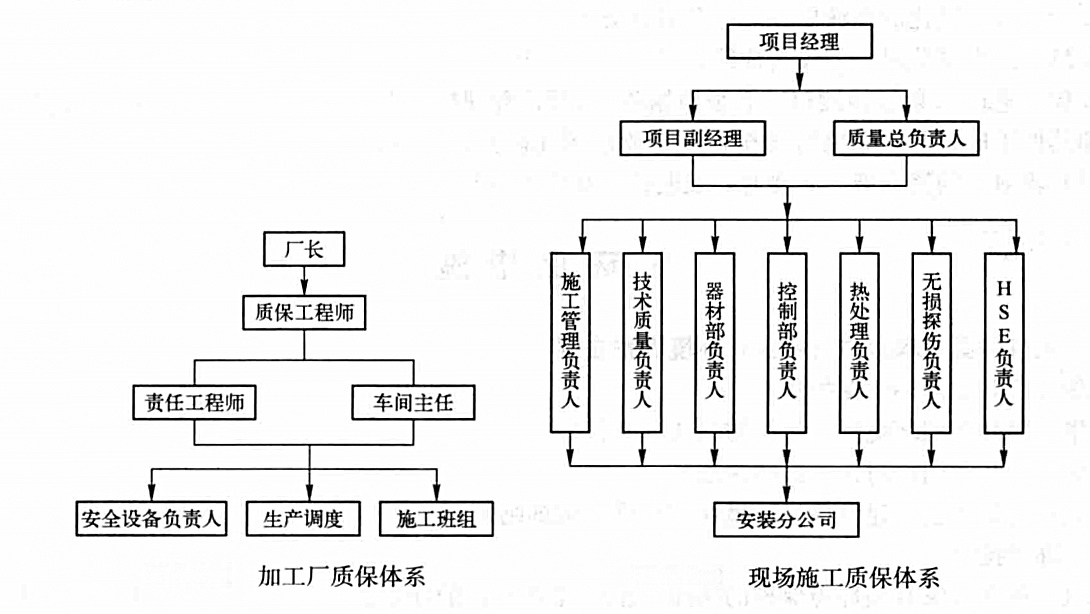
加工廠質保體系(左圖)、現場施工質保體系(右圖)
安全措施
施工企業採用《超大型耐熱鋼焦炭塔製造組焊工法》時應執行的安全法規和措施:
一、安全法規
中國國家、行業和地方的法律法規及規定:
1、中華人民共和國國務院令《建設工程安全生產管理條例》。
2、中國石化集團公司健康、安全、環境管理體系。
3、中國石化集團公司安全生產監督管理制度、安全檢查規定、安全教育管理規定。
4、中國石化集團公司臨時用電安全管理規定。
二、安全措施
1、嚴格執行國家、地方的法律法規和行業的有關規定,搞好安全教育,充分做好風險和環境識別以及應急預案措施。
2、做好安全技術交底,對施工方法、工藝程式、工藝要求、現場作業特點、關鍵控制點等做詳盡交底。
3、施工用電必須做到規範,並做隨時、定時檢查。用電設備應由專業人員進行維修及定期維護,並做好防雨措施。導線、把線、電纜線應避免損壞漏電,電動設備、工具須配備相應的漏電保護器。熱處理前應詳細檢查導線、接頭是否配合良好,確保無誤後方可通電。
4、筒節(體)擺放、運輸應平穩,吊裝運輸前作技術交底,按要求詳細檢查吊裝機索具、吊耳,確認無誤後方可起吊,吊裝時由專人統一指揮,吊裝過程中應平穩,嚴禁衝撞腳手架。
5、整體組對區地面應埋設軌道,軌道應水平;放置設備的托滾應對中,以防止設備轉動時串動。轉動時應嚴密監視設備的橫向串動情況。
6、腳手架的搭設應編制《腳手架搭設技術措施》,並按措施執行。腳手架材料一律果用鋼管架,嚴格按《石油化工施工安全技術規程》SH3505-1999第二節有關規定。所有腳手架、梯孚、安全網必須經聯檢合格確認,掛牌後方可使用,並做定時檢查。
7、每個動火的操作平台,四周圍設合格的三防帆布(高約1.2米),竹拍子上鋪設二層石棉布,每個動火點設4~6個滅火器材。
8、無損檢測應設專門警示牌及警戒線。現場作業時須按規定要求進行,並執行《石油化工施工安全技術規程》SH3505-1999規定。
9、夜間作業應有足夠照明,冬季、雨季做好防凍防滑工作。殼體內施工應使用12V安全行燈。
10、酸洗鈍化的廢液要經過中和處理方可排放。
11、壓力試驗時,應設警戒線,無關人員嚴禁進入試壓區。
12、進行X射線檢測時,必須根據項目HSE管理規定辦理射線作業票,與業主取得聯繫、同意,應和其他工序錯開,避免射線傷害,作業現場無防護時,則以X射源為中心的20米內不得有人,並設“當心輻射”的警告牌。必要時,設監護人和臨時圍欄。
環保措施
施工企業採用《超大型耐熱鋼焦炭塔製造組焊工法》時應執行的環保法規和措施:
一、環保法規
中國國家和地方(行業)環境保護法規:
- 《中國石化集團公司建設項目環境保護管理實施細則》
二、環保措施
1、遵守國家有關環境保護的法律法規,建立有效的環境監測系統,加強對施工現場粉塵、噪聲、廢氣、廢水的檢測和監控工作。與文明施工現場管理一起定期檢查、考核、獎罰各項環保工作,及時採取措施消除粉塵、廢氣、廢水噪聲的污染。要對易飛揚物的細顆粒、散體材料和廢棄物的運輸、堆放應具備可靠的防揚塵措施。禁止在施工現場焚燒垃圾。
2、及時回收余料、廢料、嚴禁亂堆亂放,施工材料做到工完料淨場地清,保證施工場地清潔、道路暢通,排水系統處於良好的使用狀態。在車輛、行人通行的地方施工時,應設定施工標誌。
效益分析
一、經濟效益
中國石化集團寧波工程有限公司和中國石化集團第五建設公司採用《超大型耐熱鋼焦炭塔製造組焊工法》施工的青島大煉油和惠州大煉油延遲焦化8台焦炭塔的製造組焊經濟效益分析見下表:
工程定額直接費 | 實際發生費用 | 節約費用(萬元) |
---|---|---|
人工費:878.52 | 725.36 | 153.16 |
機械費:989.97 | 878.67 | 111.30 |
消耗材料費:1062.78 | 816.23 | 246.55 |
鍛件製作費:2557.6 | 2232.8 | 324.8 |
熱處理費:516.5 | 369.39 | 147.11 |
合計:6005.37 | 5022.45 | 982.92 |
工程定額直接費是參照《全國統一安裝工程預算定額浙江省單位估價表》而得出的。 |
二、社會效益
《超大型耐熱鋼焦炭塔製造組焊工法》的套用,有效保證了設備的製造質量、降低了勞動強度、提高了勞動效率、減少了現場的交叉作業,為現場施工的有效組織創造了良好的條件,同時為大型設備製造組焊開拓了一條新的路子。
註:施工費用以2009-2010年施工材料價格計算
套用實例
中國石化集團寧波工程有限公司和中國石化集團第五建設公司採用《超大型耐熱鋼焦炭塔製造組焊工法》,在青島大煉油工程、惠州大煉油工程、印度愛莎焦炭塔項目、新疆塔河延遲焦化裝置、廣州石化140萬噸/年延遲焦化等焦炭塔的製造組焊中,首次採用鍛焊的連體錐形封頭過渡段結構,鍛焊過渡段最厚處達120毫米,證明了該工法的合理性和先進性。
青島大煉油/惠州大煉油延遲焦化裝置8台焦炭塔的性能參數見下表:
參數表1 | |||
設計溫度(℃) | 上:40°C,下:50°C | 無損檢測 | 100%RT、100%UT、100%MT及PT |
設計壓力(兆帕) | 0.35 | 耐壓試驗(兆帕) | 0.60(立式) |
主體材質 | 1.25Cr-0.5Mo-Si+410S/ 1.25Cr-0.5Mo-S | 保溫厚度(毫米) | 140 |
規格(毫米) | Φ9400x39440x24+(3~42) | 熱處理 | 焊接預後熱、焊後消氫、 整體應力解除熱處理 |
金屬總重(噸) | 322 | 容積(立方米) | 2196 |
參數表2 | |||
設計溫度(℃) | 490"C | 無損檢測 | 100%RT、100%UT、100%MT及PT |
設計壓力(兆帕) | 0.414 | 耐壓試驗(兆帕) | 0.897(立式) |
主體材質 | 1.25Cr-0.5Mo-F410S/ 1.25Q-0.5Mo | 保溫厚度(毫米) | 140 |
規格(毫米) | Φ9800x36600x28+(3~44) | 熱處理 | 焊接預後熱、焊後消氫、 整體應力解除熱處理 |
金屬總重(噸) | 340.5 | 容積(立方米) | 2152 |
榮譽表彰
2011年9月30日,中華人民共和國住房和城鄉建設部發布《關於公布2009-2010年度國家級工法的通知》,以文號建質[2011]154號公布《超大型耐熱鋼焦炭塔製造組焊工法》為國家二級工法。