原理套用
滲入鋼中的氮一方面由表及里與鐵形成不同含氮量的氮化鐵,一方面與鋼中的
合金元素結合形成各種合金氮化物,特別是氮化鋁、氮化鉻。這些氮化物具有很高的硬度、熱穩定性和很高的彌散度,因而可使滲氮後的鋼件得到高的表面硬度、
耐磨性、疲勞強度、抗咬合性、抗大氣和過熱蒸汽腐蝕能力、抗
回火軟化能力,並降低缺口敏感性。與
滲碳工藝相比,滲氮溫度比較低,因而畸變小,但由於心部硬度較低,滲層也較淺,一般只能滿足承受輕、中等載荷的耐磨、耐疲勞要求,或有一定耐熱、耐腐蝕要求的機器零件,以及各種切削刀具、冷作和熱作模具等。滲氮有多種方法,常用的是氣體滲氮和
離子滲氮。
鋼鐵滲氮的研究始於20世紀初,20年代以後獲得工業套用。最初的氣體滲氮,僅限於含鉻、鋁的鋼,後來才擴大到其他
鋼種。從70年代開始,滲氮從理論到工藝都得到迅速發展並日趨完善,適用的材料和
工件也日益擴大,成為重要的
化學熱處理工藝之一。
氣體滲入
一般以提高金屬的耐磨性為主要目的,因此需要獲得高的表面硬度。它適用於38CrMoAl等
滲氮鋼。滲氮後
工件表面硬度可達HV850~1200。滲氮溫度低,工件畸變小,可用於精度要求高、又有耐磨要求的零件,如鏜床鏜桿和主軸、磨床主軸、氣缸套筒等。但由於滲氮層較薄,不適於承受重載的耐磨零件。
氣體滲氮可採用一般滲氮法(即等溫滲氮)或多段(二段、三段)滲氮法。前者是在整個滲氮過程中滲氮溫度和氨氣分解率保持不變。溫度一般在480~520℃之間,氨氣分解率為15~30%,保溫時間近80小時。這種工藝適用於滲層淺、畸變要求嚴、硬度要求高的零件,但處理時間過長。
多段滲氮是在整個滲氮過程中按不同階段分別採用不同溫度、不同氨分解率、不同時間進行滲氮和擴散。整個滲氮時間可以縮短到近50小時,能獲得較深的滲層,但這樣滲氮溫度較高,畸變較大。
還有以抗蝕為目的的氣體滲氮,滲氮溫度在 550~700℃之間,保溫0.5~3小時,氨分解率為35~70%,工件表層可獲得化學穩定性高的化合物層,防止工件受濕空氣、過熱蒸汽、氣體燃燒產物等的腐蝕。
正常的氣體滲氮工件,表面呈銀灰色。有時,由於氧化也可能呈藍色或黃色,但一般不影響使用。
滲氮工藝 常用的氣體滲氮工藝有等溫滲氮、二段式滲氮和三段式滲氮三種方法。
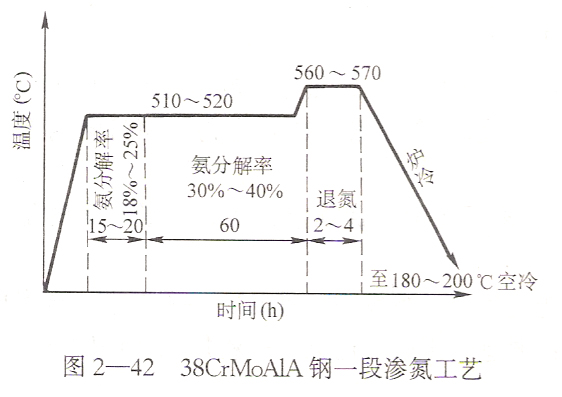
a.等溫滲氮 也稱一段式滲氮法。它是在恆溫下進行長時間保溫的滲氮工藝,滲氮溫度510~530℃,其滲氮工藝曲線如圖2-42所示。
第一階段保溫15~20h,為吸氮階段。這一階段採用較低的氨分解率(18%25%)。零件表面因洗後大量氮原子而與零件心部形成氮濃度差。第二階段為擴散階段。在這個階段為家少活性氮原子的數量而將氨分解率提高到30%~40%,保溫時間在60h左右。
為減少滲氮層的脆性,在滲氮結束前2~4h進行退氮處理,氨分解率提高到70%以上,退氮溫度提高到560~570℃。等溫滲氮工藝過程簡單,滲氮溫度較低、滲層淺、零件變形小、表面硬度高,但滲氮速度慢,產生周期長,適用於滲氮深度淺,尺寸精度和硬度要求高的零件。

b.兩段式滲氮 兩段式滲氮工藝曲線如圖2-43所示。第一階段的
工藝參數(除保溫時間外)與等溫滲氮相同。第二階段把滲氮溫度提高到550~560℃,以加速氮原子的擴散,縮短滲氮周期,氨分解率提高到40%~60%。根據對滲氮層的脆性要求,急速前也應提前2h提高氨分解率和溫度進行退氮處理。
兩段式滲氮的時間比等溫滲氮短,表面硬度稍微低,變形略有增大,適用於滲氮層較深批量較大的零件。
c.三段式滲氮 三段式滲氮工藝曲線如圖2-44所示。
它是在二段式滲氮基礎上發展起來的。這種工藝是將第二階段的溫度適當提高,以加快滲氮過程,同時增加較低溫度的第三階段,以彌補因第二階段氮的擴散快而使表面氮濃度過低,保證表面含氮量以提高表面硬度。
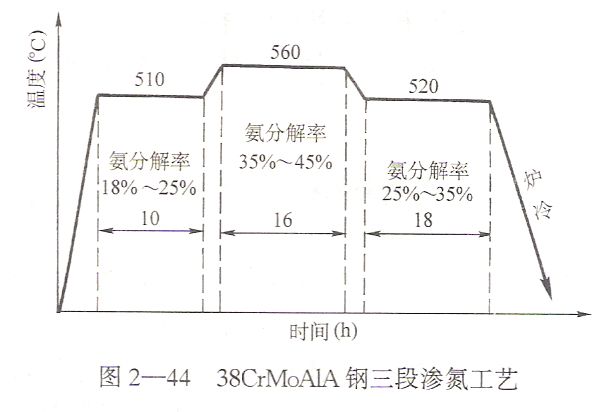
三段式滲氮能進一步提高滲氮速度,但硬度比一般滲氮工藝低,脆性、變形等比一般滲氮工藝略大。
離子滲入
又稱輝光滲氮,是利用輝光放電原理進行的。把金屬工件作為陰極放入通有含氮介質的負壓容器中,通電後介質中的氮氫原子被電離,在陰陽極之間形成等離子區。在等離子區強電場作用下,氮和氫的正離子以高速向工件表面轟擊。離子的高動能轉變為熱能,加熱工件表面至所需溫度。由於離子的轟擊,工件表面產生原子濺射,因而得到淨化,同時由於吸附和擴散作用,氮遂滲入工件表面。
與一般的氣體滲氮相比,離子滲氮的特點是:①可適當縮短滲氮周期;②滲氮層脆性小;③可節約能源和氨的消耗量;④對不需要滲氮的部分可禁止起來,實現局部滲氮;⑤離子轟擊有淨化表面作用,能去除工件表面鈍化膜,可使不鏽鋼、耐熱鋼工件直接滲氮;⑥滲層厚度和組織可以控制。
離子滲氮發展迅速,已用於工具機絲桿、
齒輪、模具等工件。
一、優點:滲氮時間短,質量容易控制,氮化層耐疲勞、有高強度,由於氮化溫度在520-540,所以工件變形小,表面抗磁性高。
二、缺點:設備控制複雜,爐溫均勻性不好。
氮碳共滲
低溫氮碳共滲又稱軟氮化,即在鐵-氮共析轉變溫度以下,使工件表面在主要滲入氮的同時也滲入碳。碳滲入後形成的微細碳化物能促進氮的擴散,加快高氮化合物的形成。這些高氮化合物反過來又能提高碳的溶解度。碳氮原子相互促進便加快了滲入速度。此外,碳在氮化物中還能降低脆性。氮碳共滲後得到的化合物層韌性好,硬度高,耐磨,耐蝕,抗咬合。
常用的氮碳共滲方法有液體法和氣體法。處理溫度530~570℃,保溫時間1~3小時。早期的液體鹽浴用氰鹽,以後又出現多種鹽浴配方。常用的有兩種:中性鹽通氨氣和以尿素加碳酸鹽為主的鹽,但這些反應產物仍有毒。氣體介質主要有:吸熱式或放熱式氣體(見
可控氣氛)加氨氣;尿素熱分解氣;滴注含碳、氮的有機溶劑,如甲醯胺、三乙醇胺等。
氰化cyaniding,指高溫
碳氮共滲(早期的碳氮共滲是在有毒的氰
鹽浴中進行)。由於溫度比較高,碳原子擴散能力很強,所以以
滲碳為主, 形成含氮的高碳奧氏體,淬火後得到含氮高碳馬氏體。由於氮的滲入促進碳的滲入, 使共滲速度較快,保溫4~6h可得到0.5~0.8mm的滲層,同時由於氮的滲入,提高了過冷奧氏體的穩定性,加上共滲溫度比較低,奧氏體晶粒不會粗大,所以鋼件碳氮共滲後可直接淬油,滲層組織為細針狀的含氮馬氏體加碳氮化合物和少量殘餘奧氏體。碳氮共滲層比
滲碳層有更高的硬度、耐磨性、抗蝕性、彎曲強度和接觸疲勞強度。但一般碳氮共滲層比滲碳層淺,所以一般用於承受載荷較輕,要求高耐磨性的零件。
氮碳共滲不僅能提高工件的疲勞壽命、耐磨性、抗腐蝕和抗咬合能力,而且使用設備簡單,投資少,易操作,時間短和工件畸變小,有時還能給工件以美觀的外表。
處理工藝
在滲氮零件的整個製造過程中,滲氮往往是最後一道工序,至多再進行精磨或研磨。滲氮零件的工藝流程一般為:鍛造→
正火(退火)→粗加工→
調質→精加工→去應力→粗磨→滲氮→精磨→裝配。
氮化前的預熱處理包括正火(退火)、調質處理、去應力。
a.正火(退火),其目的是細化晶粒、降低硬度、消除鍛造應力。
b.調質處理,可以改善鋼的加工性能,獲得均勻的
回火索氏體組織,以保證零件心部有足夠的強度和韌性,同時又能使滲氮層和基本結合牢固。
c.去應力處理,對於形狀複雜的精密零件,在滲氮前應進行1~2次去應力,以減少滲氮過程中的變形。
生產準備
a.去污處理。零件裝爐前要用汽油或酒精進行脫脂、去污處理,零件表面不允許有鏽蝕及髒污。
b.防滲處理。對零件非滲氮部分,可用電鍍或塗料法進行防滲氮處理。
c.滲氮件的表面質量應良好,不允許有脫碳層存在,因此,零件在預先熱處理前應留有足夠的加工餘量,以便在滲氮前的機加工能將脫碳層全部去除,以保證滲氮層的質量。
d.裝爐前檢查設備和滲氮夾具、電系統、管道、氨分解測定儀等應保證正常使用;滲氮夾具不允許有髒物或氧化皮,如有應清除。
e.隨爐試樣。隨爐的試樣應與滲氮零件通材料並經過同樣的預先處理。
脆性檢驗
a、
級別 | 滲氮層脆性級別說明 |
1 | 壓痕邊角完整無缺 |
2 | 壓痕一邊或一角碎裂 |
3 | 壓痕二邊或二角碎裂 |
4 | 壓痕三邊或三角碎裂 |
5 | 壓痕四邊或四角碎裂 |
b、滲氮層脆性檢驗一般採用
維氏硬度計,試驗力10公斤,試驗力的載入必須緩慢(在5-9S內完成),試驗力載入完成後必須停留5-10S,然後卸載試驗力,特殊情況也可採用5KG或者30KG試驗力。
c、維氏硬度壓痕在顯微放大100倍下進行檢查,每件至少測3點,其中兩點以上處於相同級別時,才能定級。否則需重新檢驗。
d、滲氮層脆性應在零件工作部位或隨爐試樣的表面上檢測,一般零件為1-3級為合格,重要零件1-2級為合格,對於滲氮後留有磨痕的零件,也可在磨去加工餘量後的表面上進行測定
e、經氣體滲氮後的零件,必須進行檢驗。
化學成份
滲氮用鋼---凡含有Cr、Mo、V、Ti、Al等元素的低、中碳合金結構鋼、工具鋼、不鏽鋼(不鏽鋼滲氮前需去除工件表面的鈍化膜,對不鏽鋼、耐熱鋼可直接用離子氮化方法處理)、球墨鑄鐵等均可進行滲氮. 滲氮後零件雖然具有高硬度、高耐磨性和高的疲勞強度,但只是表面很薄的一層(鉻鉬鋁鋼於500--540C經35--65h滲氮層深只達0.3--0.65mm) .必須有強而韌的心部組織作為滲氮層的堅實基底,才能發揮滲氮的最大作用.總的來看,大部分滲氮零件是在有摩擦和複雜的動載荷條件下工作的,不論表面和心部的性能都要求很高.
如果用碳鋼進行滲氮,形成Fe 4N和Fe 2N較不穩定。溫度稍高,就容易聚集粗化,表面不可能得到更高的硬度,並且其心部也不能具有更高的強度和韌性.
為了在表面得到高硬度和高耐磨性,同時獲得強而韌的心部組織,必須向鋼中加入一方面能與氮形成穩定氮化物,另外還能強化心部的合金元素.如Al、Ti、V、W、Mo、Cr等,均能和氮形成穩定的化合物.其中Cr、W、Mo、V還可以改善鋼的組織,提高鋼的強度和韌性.
當前專門用於滲氮的鋼種是38CrMoAlA,其中鋁與氮有極大的親和力,是形成氮化物提高滲氮層強度的主要合金元素.AlN很穩定,到約1000C的溫度在鋼中不發生溶解.由於鋁的作用使鋼具有良好的滲氮性能,此鋼經過滲氮表面硬度高達1100--1200HV(相當67--72HRC).38CrMoAlA鋼脫碳傾向嚴重,各道工序必須留有較大的加工餘量.
注意事項
(1)滲氮前的預備熱處理調質--滲氮工件在滲氮前應進行調質處理,以獲得回火索氏體組織.調質處理回火溫度一般高於滲氮溫度.
(2)滲氮前的預備熱處理去應力處理--滲氮前應儘量消除機械加工過程中產生的內應力以穩定零件尺寸.消除應力的溫度均應低於回火溫度,保溫時間比回火時間要長些,再緩慢冷卻到室溫.斷面尺寸較大的零件不宜用正火.工模具鋼必須採用淬火回火,不得用退火.
(3)滲氮零件的表面粗糙度Ra應小於1.6um,表面不得有拉毛、碰傷及生鏽等缺陷.不能及 時處理的零件須塗油保護,以免生鏽.吊裝入爐時再用清潔汽油擦淨以保證清潔度.
(4)含有尖角和銳邊的工件,不宜進行氮化處理.
(5)局部不氮化部位的保護,不宜用留加工餘量的方法.
(6)表面未經磨削處理的工件,不得進行氮化.