真空獲得技術是通過機械、物理或化學等手段在特定容器中獲得真空的專門技術。
基本介紹
- 中文名:真空獲得技術
- 方法:機械、物理或化學等
- 目的:產生、改善和維持真空的裝置
- 套用領域:真空、固態電子器件工藝等
技術原理
技術公式

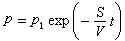
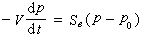
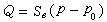
技術參量
現代真空技術可獲得從大氣壓強直到約10帕的寬達18個數量級的範圍。任一真空泵都很難覆蓋如此寬的量程,必須按照要求將各種泵組合套用。圖1為各種泵大致的工作壓強範圍。
真空獲得技術真空泵可分為兩大類。一類是將容器中氣體傳輸到下一級泵或大氣中去,包括變容積真空泵和動量傳遞真空泵。另一類是容器中的氣體被吸附或冷凝在泵的內表面上,包括吸附泵、低溫冷凝泵、吸氣劑泵、濺射離子泵等。
屬變容積泵,有旋片式、定片式和滑閥式三種。它們採用機械的方法周期性地改變排氣腔內的體積以達到排氣目的。以旋片式為例(圖2),氣體從入口 1入腔(圖2a),旋片2把進氣腔3和排氣腔4隔離(圖2b、c),最終氣體被壓縮並通過出口5被排放到大氣中去(圖2d)。整個腔體浸沒在油內,以保證出口和入口之間、進氣腔和排氣腔之間的密封和潤滑。如需要排除可凝性蒸氣,則要採用氣鎮結構泵,這種泵在排氣腔的壓縮區裝一氣鎮閥,定時送入一定量空氣,以防止蒸氣在壓縮過程液化而溶入油內,這樣便使可凝性蒸氣隨空氣一起由出口排出。
真空獲得技術屬變容積泵,圖3a為一種羅茨泵的結構。它有一個近橢圓形腔體,其中有一對以相反方向旋轉的 8字型葉輪。葉輪之間和葉輪與腔體內壁之間彼此互不接觸,其間隙約為0.1~0.5毫米,故可作高速旋轉。羅茨泵的工作過程如圖3b所示。羅茨泵一般配備一個前置油封機械泵。羅茨泵在低於10帕的壓強下工作,在10~10帕範圍有較高抽速,可用以獲得中真空,或用作高真空泵(如擴散泵)和機械泵之間的中間泵。

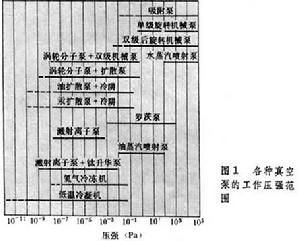
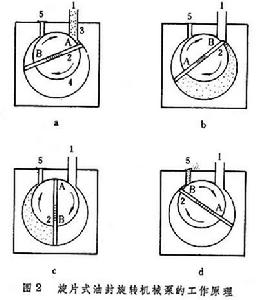
技術原理
真空獲得技術屬動量傳遞真空泵,它利用油蒸氣、水蒸汽或汞蒸氣噴流進行排氣。根據工作壓強範圍的不同分為擴散泵和增壓(噴射)泵,前者入口氣體處於分子流狀態,後者處於分子粘滯流狀態。圖5a是近代金屬擴散泵的剖面圖。油鍋內產生的蒸氣由各級噴嘴噴出,形成向下的噴流,射到水冷外壁後,冷凝而返回油鍋。蒸氣流是超聲速的,一直維持到與壁相碰為止。擴散到超聲速蒸氣噴流內的氣體分子得到向下的動量而射入較高壓強區。近代擴散泵一般有三、四級噴嘴,即氣體經三、四級壓縮,壓強逐級提高,直到出口壓強。前級泵的作用是保證一定前置壓強以維持噴流機能。泵的前置耐壓(即仍可工作時泵出口處的最大壓強)一般為25~70帕,而油鍋內的壓強一般為200帕左右。
真空獲得技術擴散泵的四個工作區是恆定抽速區、恆定排氣量區、機械泵影響區和壓縮比限制區(圖5b)。恆定抽速區是正常運行區,即擴散泵是恆定抽速裝置。對大多數氣體,恆定抽速區的壓強範圍為10~10帕。在0.1~10帕範圍,排氣量近似保持恆定,最高排氣量在監界點。在壓縮比限制區抽速隨壓強逐漸下降到零。假設泵的極限壓強為10帕(圖5b),前級壓強為1帕,則其壓縮比為10。
在擴散泵排氣系統中,工作液蒸氣的返流是一個有害因素,返流率還與阱、擋板和管路有關。套用高質量、低蒸氣壓、抗氧化的工作液如矽油和聚苯醚等加上液氮阱,可使返油率降低到8.7×10毫克/厘米·米。
如果擴散泵的前級採用機械泵,則機械泵油蒸氣返流是真空室污染的主要因素,尤其對於有旁通管路預抽真空室的系統,必須套用分子篩、活性氧化鋁或其他形式的擋油阱。
用多孔性吸附劑(分子篩丸、活性炭等)堆積於金屬翼片之間或壓結在金屬帶上並用液氮冷卻,被抽容器的氣體分子被具有大面積的吸附劑捕集。在空間內建立的平衡壓強取決於氣體在吸附劑表面的物理吸附的恆溫線。吸附泵主要用作前級泵,因為在液氮溫度(-196)下,分子篩5A對氦、氖的平衡壓約為10帕左右,它相當於大氣壓中氦、氖的分壓強。為了提高吸附泵的極限壓強,必須設法預先去除被抽容器中的氦、氖、氫,或把致冷劑的溫度降低到20K以下。氬氣的液化點高於氮,因此在液氮溫度下氬很容易被抽走。在吸附泵不工作時,原在低溫下吸附的氣體將釋出,使泵內壓強增高,故吸附泵設有安全閥。吸附劑經長期使用後吸附性能變差,可以通過加熱再生。
利用氣體凝結在低溫金屬壁面上形成固化層的原理而工作。其平衡壓強取決於氣體固化層的飽和蒸氣壓和周圍環境溫度,浸沒式液氦冷凝泵的典型結構見圖6。冷凝面在泵的底部,四周被液氮冷卻的面所包圍,氣流通過不透光的人字形擋板進入冷凝面,根據屏溫(即環境溫度)的不同可獲取10~10帕的真空度。另一種低溫冷凝泵是氦閉循環致冷機式, 冷源是致冷機的冷頭,直接置於被抽容器空間, 一般有兩級冷頭,第一級80~120K,第二級8~20K,這種泵可避免灌入液氦的困難,因而得到廣泛的套用。氫在液氦溫度(4.2K)下仍有較高蒸氣壓(10帕),因此難以凝聚。但是它易於被吸附劑或其他氣體的凝聚層所吸附,故常在低溫泵的冷凝面上塗復活性炭吸附劑層或引入氬、二氧化碳等氣體形成凝聚吸附層,以獲得更低壓強。
真空獲得技術利用濺射和電離兩種作用而工作。泵由陰極鈦板和陽極不鏽鋼筒組成 (圖7)。在陰極附近產生的電子(由場致發射、宇宙射線或正離子轟擊陰極產生)在正交的電場和磁場作用下作螺旋線運動(圖7中①),電子在運動過程與氣體分子不斷發生電離碰撞,由此產生的電子又加入螺旋線運動,而產生的正離子質量大,在電場作用下轟擊鈦陰極(圖7中②),引起陰極鈦濺射到陽極圓筒內壁,沉積形成新鮮的、化學性質活潑的鈦膜 (圖7中③),另一部分鈦沉積在正對不鏽鋼筒壁的陰極b區(圖7中④)。它是靠活性氣體和濺射產生的蒸發鈦膜發生反應而排除氣體。氬等隋性氣體(以及氮等活性氣體),在轟擊鈦陰極過程中以離子形式埋入陰極邊緣區或以原子形式被鈦膜埋在陽極筒內壁(圖7中⑤)。因此,泵對不同氣體的抽速差別很大。不同結構的離子泵對氬抽速約為氮抽速的1%~30%。
真空獲得技術吸氣劑是真空電子器件常用的一種材料。吸氣劑分蒸散式(如鋇合金)和非蒸散式(如鋯合金)兩種,器件內殘餘氣體分別與蒸散式吸氣劑化合或向非蒸散式吸氣劑體內擴散,而維持容器內的真空。利用吸氣劑原理可做成吸氣劑泵。吸氣劑泵也分為兩種,一類稱為升華泵,利用鈦、鉭等金屬加熱升華到冷壁形成的薄膜抽氣,氣體分子與膜碰撞,在膜表面發生反應而被排除,只有極少數氣體向膜內擴散。另一類稱為體效應吸氣劑泵,利用鋯、釷與鋁、矽、石墨的合金經高溫700~1000活化形成微孔型材料,在室溫或400左右溫度下工作,氣體分子與其碰撞後向體內擴散而被排除。吸氣劑泵不抽惰性氣體,因此常與其他泵聯合使用。
真空獲得技術
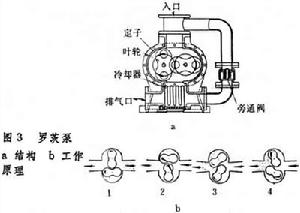
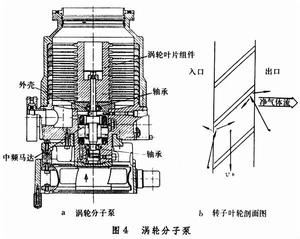
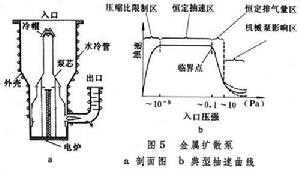



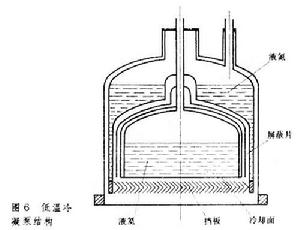
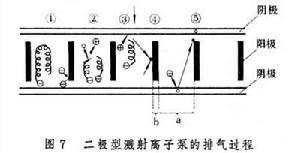


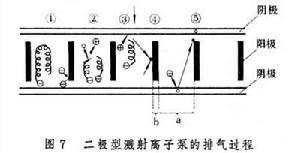