我國轉爐底吹技術近幾十年取得了很大進步,轉爐底吹氣源已有 N2、Ar、O2、CO2等多種氣源,底吹供氣元件也多樣化,通過對供氣元件的材質、成型工藝、結構、供氣元件保護磚的改進,並且最佳化了轉爐爐底砌築工藝、復吹工藝及維護制度,從而大大提高了轉爐復吹系統的壽命。
基本介紹
- 中文名:底吹轉爐
- 外文名:bottom-blown converter
- 用途:煉鋼
轉爐底吹工藝
氣體的選擇
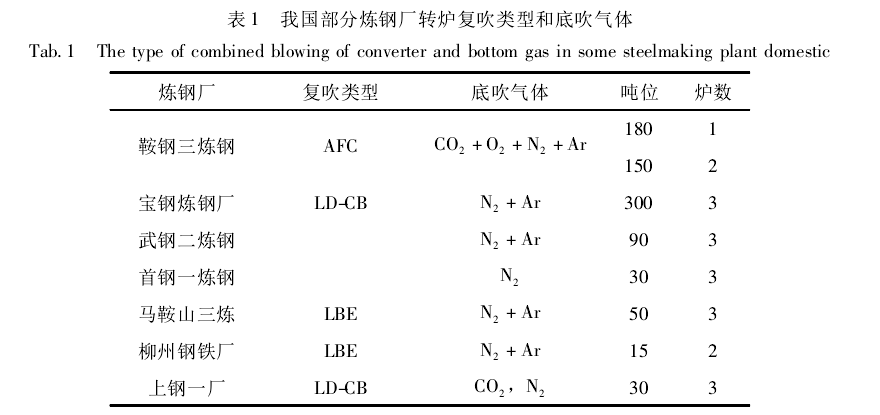
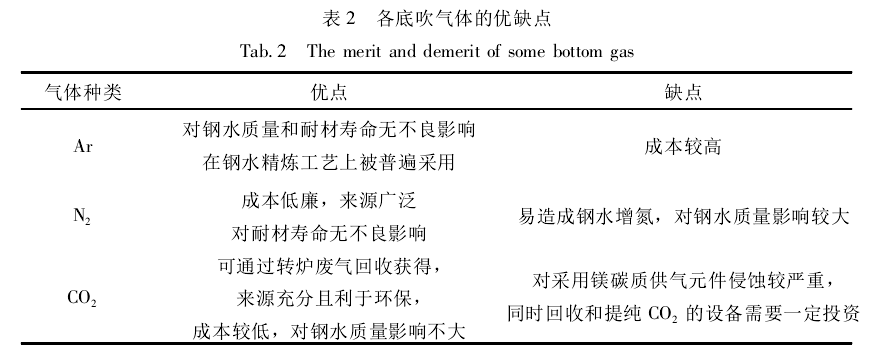
供氣元件選擇
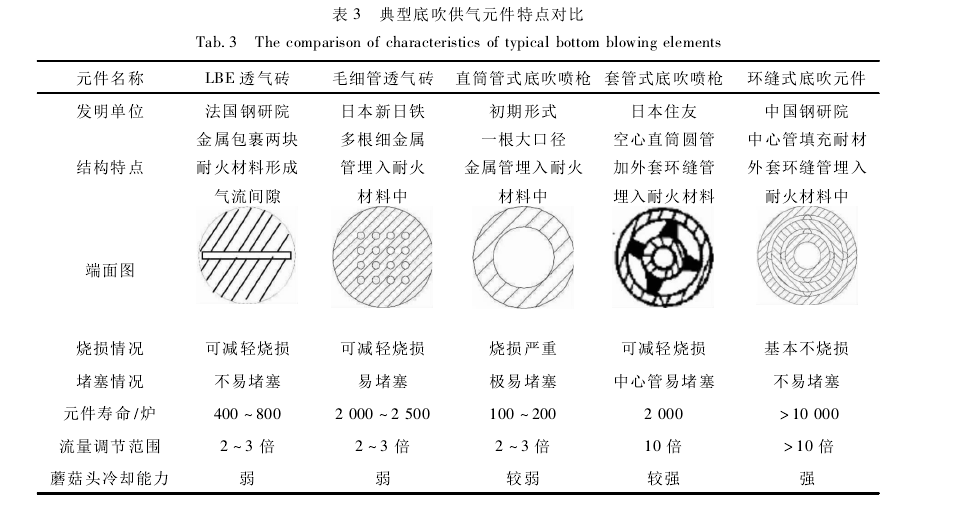
工藝流程

工藝最佳化
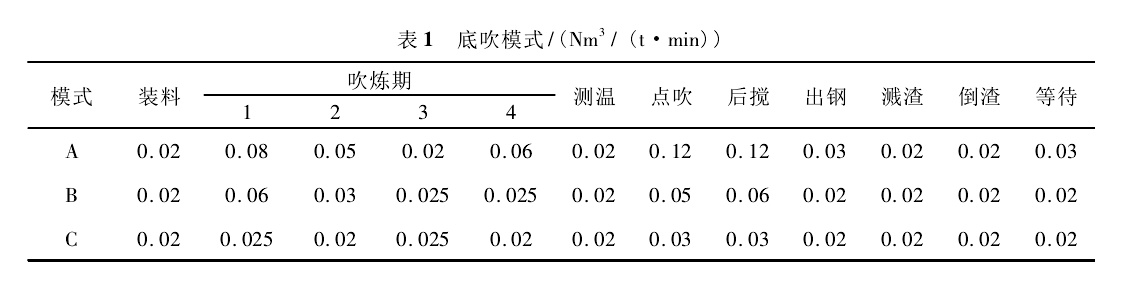
我國轉爐底吹技術近幾十年取得了很大進步,轉爐底吹氣源已有 N2、Ar、O2、CO2等多種氣源,底吹供氣元件也多樣化,通過對供氣元件的材質、成型工藝、結構、供氣元件保護磚的改進,並且最佳化了轉爐爐底砌築工藝、復吹工藝及維護制度,從而大大提高了轉爐復吹系統的壽命。
我國轉爐底吹技術近幾十年取得了很大進步,轉爐底吹氣源已有 N2、Ar、O2、CO2等多種氣源,底吹供氣元件也多樣化,通過對供氣元件的材質、成型工藝、結構、供氣元件保護磚的改進,並且最佳化了轉爐爐底砌築工藝、復吹工藝及維護制...
轉爐底吹透氣磚熱更換採用的透氣芯磚由上段、中段、下段三段連線組成;保護套磚由上套磚和下套磚連線組成,上套磚為鎂碳磚,下套磚為剛玉澆注料,保護套磚套裝在透氣芯磚外;爐底法蘭焊接在爐底開口處,爐底法蘭與專用鑽孔機相...
這是在氧氣頂吹轉爐煉鋼法和氧氣底吹轉爐煉鋼法兩種方法(簡稱頂吹法和底吹法)的基礎上發展起來的一種方法。它發揮了氧氣頂吹轉爐和氧氣底吹轉爐兩種煉鋼方法的優點,從而在一定程度上彌補了這兩種方法的不足之處。簡史 在研究氧氣煉鋼...
轉爐煉鋼(converter steelmaking)是以鐵水、廢鋼、鐵合金為主要原料,不藉助外加能源,靠鐵液本身的物理熱和鐵液組分間化學反應產生熱量而在轉爐中完成煉鋼過程。轉爐按耐火材料分為酸性和鹼性,按氣體吹入爐內的部位有頂吹、底吹和側吹...
氧氣底吹轉爐煉鋼 氧氣底吹轉爐煉鋼是材料科學技術名詞 定 義 從轉爐底部的氧氣噴嘴把氧氣吹入爐內熔池的轉爐煉鋼工藝。套用學科 材料科學技術(一級學科),金屬材料(二級學科),鋼鐵材料(三級學科),鋼鐵材料生產技術(四級學科)
酸性底吹轉爐煉鋼法是指將空氣由酸性爐襯的轉爐爐底吹入鐵水以氧化其中的雜質元素並發生大量的熱,藉以煉成鋼水的轉爐煉鋼方法。又稱為貝賽麥法。在19世紀中葉,歐洲資本主義工業蓬勃發展,當時已有的普德林法和坩堝煉鋼法等古代煉鋼方法...
另外還有諾蘭達連續吹煉法,尚處於工業試驗階段。發明內容 專利目的 《一種採用氧氣底吹爐連續煉銅的工藝及其裝置》所要解決的技術問題是克服專利背景中相關技術的缺點,提供一種採用有效方法,解決銅冶煉PS轉爐吹煉的低空SO₂污染問題,...
轉爐3個風口的布置見圖2。耐火爐襯 耐火爐襯見圖3。工藝過程 還原電爐冶煉的高碳錳鐵液,從爐內放入鐵水包,稱重後裝入12t容量的底吹轉爐。測溫後加入石灰和根據上爐鐵水成分加入錳矽合金回爐品。先吹入空氣以防風口堵塞。倒爐後以7....
按爐襯化學性質可分為酸性轉爐和鹼性轉爐;按風眼和供氧管位置,分為底吹轉爐、側吹轉爐和頂吹轉爐 。有色金屬吹煉,採用酸性或鹼性側吹鼓形轉爐,利用熔融金屬中硫的氧化,產生所需要的熱能。在工業上主要用來煉鋼。轉爐爐體包括爐殼...
為了與其他工藝流程配合,轉爐過程計算機還與煉鐵、連鑄、初軋等車間的過程計算機進行數據通信。有關信息還傳送到生產管理計算機去進行生產管理計算。轉爐冶煉工藝不斷發展,除氧氣頂吹轉爐外,相繼出現了底吹和頂底吹相結合的轉爐。這些新型...
吹入氧氣的方式有頂吹、側吹、底吹三種。1952年,頂吹氧氣轉爐最早研究開發成功(見圖)。頂吹時,氧氣噴嘴不埋入鐵水中,和液面有1米左右的距離,可以用水冷卻噴嘴。為了使氧流達到液面時仍有必要的動能和動量,噴嘴出口的氧氣壓力達...
轉爐鋼按爐襯的耐火材料性質可分為鹼性轉爐鋼和酸性轉爐鋼。按氣體吹入爐內的部位可分為頂吹轉爐鋼、底吹轉爐鋼和側吹轉爐鋼,還有頂吹、底吹複合轉爐鋼等。現在氧氣轉爐鋼生產效率高,質量也很好,己被廣泛套用,成為世界上的主要鋼...
鐵合金氧氣轉爐生產法 氧氣轉爐按供氧方式:有側、頂、底吹和頂底雙吹,我國現以頂吹為主,但積極向底吹髮展。頂吹轉爐所用的原料是液態碳素合金。純氧以及冷卻劑。造渣料等。冶煉時將液態碳素合金兌入轉爐,高壓氧氣經氧槍入爐進行吹...
Q-BOP法是氧氣底吹轉爐煉鋼法的一種簡稱。Q代表這種煉鋼方法快速(quick)、平穩(quiet)和質量好(quality),BOP是鹼性氧氣煉鋼(basic oxygen process)的縮寫。氧氣底吹爐煉鋼是指通過轉爐底部的氧氣噴嘴,把氧氣吹入爐內熔池進行煉鋼的...
LWS法(LWS process)即氧氣底吹轉爐煉鋼,由轉爐頂部垂直插入的氧槍將工業純氧吹入熔池,以氧化鐵水中的碳、矽、錳、磷等元素,並發熱提高熔池溫度面冶煉成為鋼水的轉爐煉鋼方法。它所用的原料是鐵水加部分廢鋼,為了脫除磷和硫,要加入...
托馬斯法是將空氣由鹼性爐襯的轉爐爐底吹入鐵水並以石灰為熔劑造渣去除鐵水中的磷而將高磷生鐵煉成鋼的轉爐煉鋼方法。又稱為鹼性底吹轉爐煉鋼法或鹼性貝塞麥法。簡史 貝塞麥法只能以低磷鐵礦石煉出的低硫低磷生鐵為原料,但西歐大陸的...
OBM法是指氧氣底吹轉爐煉鋼(oxygen bottom-blown converter steelmaking)。是通過轉爐底部的氧氣噴嘴,把氧氣吹入爐內熔池進行煉鋼的方法。簡介 OBM法是指氧氣底吹轉爐煉鋼(oxygen bottom-blown converter steelmaking)。是通過轉爐底部的氧氣...
含鈮鐵水兌入煉鋼爐前先提取鈮的鐵水預處理工藝。所得到的鈮渣可用作製取鈮鐵或鈮產品的原料。這種方法是中國開發的。常用方法有噴霧法、側吹轉爐法、底吹轉爐法、分段底吹連續法等。方法原理 進行鐵水提鈮時,希望磷儘量少氧化,以...
HI熔融還原法(HIsmelt process)是以底吹轉爐技術為基礎開發的一種熔融還原煉鐵工藝。工藝流程 該工藝熔池部分如底吹轉爐,以氮氣和天然氣為載體,通過底部噴嘴向熔池噴煤,煤中的碳溶解進入鐵水並還原熔渣中的鐵氧化物,反應產生的一...
隨氧氣底吹的風嘴技術的發展成功,1967年德國和法國分別建成氧氣底吹轉爐。1971年美國引進此項技術後又發展了底吹氧氣噴石灰粉轉爐,用於吹煉含磷生鐵。1975年法國和盧森堡又開發成功頂底複合吹煉的轉爐煉鋼法。
根據氧氣吹入的方式主要有:氧氣頂吹轉爐煉鋼法 氧氣底吹轉爐煉鋼法 氧氣側吹轉爐煉鋼法 發展現狀 20世紀60年代中期,我國設計、科研、製造、生產人員共同協作,開展了大型氧氣頂吹轉爐煉鋼廠的設計,1971年容量120t的大型轉爐煉鋼廠於1971...
氧氣底吹轉爐煉鋼 通過轉爐底部的氧氣噴嘴把氧氣吹入爐內熔池,使鐵水冶煉成鋼的轉爐煉鋼方法。其特點是;爐子的高度與直徑比較小;爐底較平並能快速拆卸和更換;用風嘴、分配器系統和爐身上的供氧系統代替氧氣頂吹轉爐的氧槍系統。由於...
隨氧氣底吹的風嘴技術的發展成功,1967年德國和法國分別建成氧氣底吹轉爐。1971年美國引進此項技術後又發展了底吹氧氣噴石灰粉轉爐,用於吹煉含磷生鐵。1975年法國和盧森堡又開發成功頂底複合吹煉的轉爐煉鋼法。
這是在氧氣頂吹轉爐煉鋼法和氧氣底吹轉爐煉鋼法兩種方法(簡稱頂吹法和底吹法)的基礎上發展起來的一種方法。它發揮了氧氣頂吹轉爐和氧氣底吹轉爐兩種煉鋼方法的優點,從而在一定程度上彌補了這兩種方法的不足之處。簡介 復吹煉鋼法LBE...
煉鋼方法是從生鐵或直接從礦石熔煉成鋼水的冶煉方法。1856年以後出現的大規模煉鋼方法主要分三大類:①轉爐煉鋼法,又分(1)空氣轉爐煉鋼法,即用酸性空氣底吹轉爐煉鋼,又稱貝塞麥(Bessemer)轉爐煉鋼法。此法是利用來自原料鐵水物理熱及所...
貝塞麥轉爐煉出的鋼含雜質較多,平爐和電爐的套用遂逐漸擴大。1952年第一座工業生產用的氧氣頂吹轉爐在奧地利的林茨廠投產。氧氣頂吹轉爐生產的每噸鋼投資少,冶煉周期短,產量高,鋼的質量好,獲得迅速發展。1970年氧氣底吹轉爐投入工業性...