形成原因
截至2005年,中國國內橋樑建設的一個明顯趨勢是
跨徑越來越大,這樣就為大直徑超長樁基礎和大型承台的套用開闢了更為廣闊的空間。如潤揚大橋北汊斜拉橋、
白沙洲長江大橋、鄂黃長江公路大橋以及
蘇通長江公路大橋主墩均採用樁基承台形式。
鋼吊箱作為承台施工的圍水結構,是整個橋樑深水基礎施工中至關重要的環節。對於超大規模的鋼吊箱,如蘇通大橋南塔墩鋼吊箱,平面尺寸為117.35米×51.7米×14.4米(相當於一個半足球場大),重達5880噸,具有相當大的施工難度和技術難度。對於常規尺度的鋼吊箱,2005年前在中國國內通常採取分節分塊散拼及下放工藝。其中下放工藝2005年前普遍的做法是通過在底板上滿布吊點,採用大量小型千斤頂通過人工控制下放。但該工藝對於超大規模的鋼吊箱來說,其同步控制顯然是不能滿足要求的,而且工期及質量都無法得到保證。
經過科技攻關,蘇通大橋南塔墩鋼吊箱首次在中國國內實現了在水上施工現場整節由上下游向承台中部對稱拼裝,實現合攏;在壁板上布置12個吊點,採用計算機控制鋼吊箱整體同步下放;完成定位後,分5區3次完成吊箱封底的施工工藝。工程實踐證明《超大型鋼吊箱水上整體拼裝下放施工工法》具有進度快、質量易保證、施工精度高、安全可靠等特點,具有社會效益和經濟效益。
工法特點
《超大型鋼吊箱水上整體拼裝下放施工工法》的工法特點是:
1.鑽孔平台頂板兼作吊箱底板,方案設計階段統籌考慮。
2.吊箱在有資質的鋼結構加工廠分塊整節加工,生產條件較好,加工質量較傳統的水上分節拼裝更容易控制。
3.吊箱在固定的平台(以底板為主)上14.4米高整節拼裝,比傳統的水上分節拼裝更安全、拼裝平面準確度和垂直度更容易得到保證。
4.吊箱拼裝以豎向接縫為主,基本無水平接縫;與傳統的水上分節拼裝工藝相比接縫少、工作量小。
5.吊箱下放吊點布置於壁板上,靠壁板懸吊底板,和傳統的在底板上布置吊點並靠底板懸吊壁板的工藝相比,對底板的剛度要求更高。
6.吊箱整體下放工藝與傳統的在底板上滿布吊點的工藝相比,吊點布置少且更為集中。
7.吊箱整體下放工藝採用計算機對全部12個吊點共40台千斤頂進行荷載位移同步控制,與傳統的人工控制大量千斤頂下放工藝相比,同步性精度高出很多,施工更安全,風險更小。
8.吊箱整體下放工藝整個施工過程只有一次下放,較傳統分多節(次)下放工藝相比,下放輔助工作量更小,更節省工期。
9.吊箱下放過程中,對結構進行安全檢測,適時測試關鍵部位應力,適應了信息化施工的發展趨勢。
操作原理
適用範圍
《超大型鋼吊箱水上整體拼裝下放施工工法》適用於長江中下游、海上施工水域大型深水橋樑,吊箱規模較為龐大常規大型浮吊無法滿足施工要求或因施工不便而不能整體吊裝的深水基礎施工;對於風浪潮頻繁的長江口和近海區域,更具優勢。同時,對於其他行業大型水工結構長距離下放入水落床也十分適用。
工藝原理
《超大型鋼吊箱水上整體拼裝下放施工工法》的工藝原理敘述如下:
1.利用水中樁基為依託和支撐,大型千斤頂採用計算機進行群頂同步控制,整體拼裝下放鋼吊箱入水,作為深水承台施工的圍水結構,實現水下基礎向水上塔身的施工轉換。
2.鋼吊箱與永久結構防撞體系相結合,在吊箱底板上增設桁架,使封底混凝土、吊箱壁板、底板等結構結合為整體;同時增強底板剛度以及壁板懸吊底板的能力,為在壁板上布置吊點靠壁板懸吊底板創造了條件。
3.在施工現場,下放鑽孔平台頂板至水面上一定高度,並固定於護筒牛腿上轉換成為吊箱底板;以此為拼裝平台,整節拼裝鋼吊箱壁板等其他構件。
4.吊箱下放利用已完成的樁基及吊箱外圍的靠船樁為支撐,在壁板上布置12個吊點,利用40台千斤頂整體下放。
5.通過感測器及計算機集中控制櫃對全部的千斤頂位移及荷載進行同步控制,保證荷載均勻分配,避免因個別吊點下放不同步造成荷載不均勻而產生事故的現象。
6.施工過程中,通過在吊箱結構及支撐樁上布置的應力應變測點,對結構下放過程中的應力、支撐樁不均勻沉降進行實時監控,實現信息化管理,確保了施工安全。
7.利用吊箱壁雙壁箱式結構的特點,合理抽水、加水以克服潮差的影響,調整吊箱在水中的姿態及標高,便於豎向定位。利用內側鋼護筒和外側鋼管樁受力,通過下放吊點位置設定反壓桿豎向鎖定,通過水平千斤頂可調水平定位系統定位。
8.利用已完成的樁基作為支撐,通過焊接與吊箱底板與樁基護筒之間的拉壓桿,將封底混凝土及吊箱荷載傳遞至樁基。
施工工藝
《超大型鋼吊箱水上整體拼裝下放施工工法》的工藝流程如圖1所示。

圖1 大型鋼吊箱水上整體拼裝下放施工工藝流程圖
《超大型鋼吊箱水上整體拼裝下放施工工法》的操作要點如下:
一、鋼吊箱構件的加工運輸
1.構件的加工主要包括壁板、內支撐及底板桁架,均在有資質的鋼結構加工廠分塊加工。
2.壁板的加工組裝要求在胎架上完成,要保證胎架有足夠的剛度和平整度,確保壁體加工質量。
壁板加工質量要求:單塊長度方向尺寸偏差±15毫米;壁體厚度偏差±2毫米;外形對角線偏差±20毫米;高度方向尺寸偏差0/+30毫米。
3.壁板的分塊充分考慮吊裝設備的起吊能力,接頭應避開鋼箱(龍骨)50厘米左右;為保證拼裝精度,每塊壁板加工時均留有50毫米的餘量,現場定位後切割,從而避免誤差累計。
4.內支撐為空間桁架結構,其分塊應充分考慮運輸便利與吊裝能力;拆分成片狀平面桁架結構,接頭避開節點20厘米以上;為方便內支撐與壁板的連線,管端採用弧形鋼板(哈佛板)連線,便於調整現場拼裝偏差;為便於現場操作,內支撐塊件之間的連線採用螺栓預連線後焊縫補強的形式。
5.施焊前必須徹底清理待焊區的鐵鏽、氧化鐵皮、油污、水分等雜質;焊接過程中儘量減少立焊、仰焊;焊後必須清理熔渣及飛濺物等。當焊縫高度超過6毫米時,應分層焊接,每層焊縫4~5毫米,必須嚴格清除每層焊渣。
6.所有構件的加工應在樁基結束前1個半月啟動,以保證現場拼裝的連續性。
二、分區下放底板至下平聯,並調平合攏
1.利用鑽孔平台頂板作為吊箱底板,鑽孔完成後,對平台頂板進行測量、檢修並加固。
2.底板須由原鑽孔平台位置下放到吊箱拼裝標高(吊箱拼裝標高應儘可能低,同時高出施工期間高水位+0.5米)。
3.安裝底板下放至壁板拼裝高度處的支撐牛腿,頂面統一調平標高。
4.底板下放作為吊箱整體下放的試驗工藝,採用計算機控制同步下放技術,分上、下游兩次下放完成。
5.在上游底板上安裝底板下放系統,包括因底板剛度不夠而增設的吊具梁、千斤頂及支撐墊梁等結構。底板分區下放系統如圖2所示。

圖2 南塔墩鋼吊箱底板分區下放系統布置圖
6.提升底板脫離支撐上平聯,鎖定下放系統,快速切割完畢後,下放底板至壁板拼裝平台高度處的支撐牛腿上。
7.將上、下游底板焊接為整體,並對底板各結構進行補焊,最終完成由樁基支撐平台向鋼吊箱底板的轉換。
三、分片區安裝底板桁架及拉壓桿下鉸座
1.底板上設定桁架,伸入承台內40厘米,將水下封底混凝土、承台、底板、壁板等結構連為整體,共同形成防撞體系。
2.防撞桁架在加工廠分件加工,並嚴格編號。
3.在鋼吊箱底板上測量、繪製防撞桁架安裝後的輪廓線。
4.依據繪製好的輪廓線,分件安裝防撞桁架及內支撐支架,拼裝順序為先周邊、後中間核心部位
5.接頭應避開交義點1米左右,並儘可能設在直線位置以便於定位和調整,交叉點處的結構可在後場加工成整體,在現場整塊安裝。
6.將各防撞桁架分件連線為整體,並將防撞桁架與底板(主梁)焊接為整體,完成防撞桁架的安裝。
7.弦桿作為主受力構件,要按《鋼結構結點手冊》中相關要求連線。
8.防撞桁架拼裝就位後,同時作為壁板拼裝過程中的內靠架,便於壁板定位和穩定。
四、水上整節拼裝壁板
1.壁板低水位以下的箱體內腔灌注混凝土而作為防撞結構的一部分。
2.壁板在專業加工廠平面分塊、豎向整節加工,並嚴格編號。
3.分塊原則:分塊大小以吊裝設備性能控制,並儘可能減少分塊,避免在結構轉角、豎向龍骨位置分塊。
4.加工順序:與拼裝順序一致即由上下游側向承台中部縱軸線位置合攏,分4個工作面對稱進行。壁板分塊如圖3所示。

圖3 南塔墩鋼吊箱壁板分塊平面布置圖
5.利用運梁船將壁板從水上運輸至現場。
6.採用動臂吊機(或浮吊)吊裝壁板,並將其安放於壁板支撐平台上。
7.壁板水上整節拼裝穩定工藝:拼裝高度在10~15米左右,按8級風力驗算單塊及整體穩定性;起始塊段拼裝階段,穩定性最差,採用壁板頂端內外拉纜、防撞桁架及時與壁板焊接形成內靠架等形式抗傾覆。
8.每吊裝一塊壁板,即將其與已安裝的壁板焊接為一個整體,並將壁板與底板、防撞桁架焊接為一個整體。
9.拼裝誤差採用單塊測控消除法,即每塊壁板安裝前,根據測量放樣情況,切割餘量後安裝於設計位置,避免拼裝誤差的累積。
10.在承台中部縱軸線處對壁板進行合攏焊接,完成壁板的拼裝。為保證合攏精度,合攏塊兩側均設定50毫米的餘量,在精確測量並切割餘量後,進行合攏。
11.壁板安裝時的偏差可利用50噸千斤頂糾正,垂直度偏差利用錨固於底板或護筒的纜風,通過5噸鏈條葫蘆調整。
12.拼裝質量要求:
外形平面尺寸偏差:0/+50毫米;內口平面尺寸偏差:0/+50毫米;外形對角線尺寸偏差:0/+70毫米;內口對角線尺寸偏差:0/+70毫米;壁板傾斜度:≤H/1000;壁板面板平整度:≤3毫米(3米尺);高度偏差:0/+30毫米。
五、安裝內支撐
1.在加工廠分塊加工內支撐,並試拼、編號。
2.加工順序與拼裝順序一致:即由上下游側向承台中部,跟進壁板拼裝施工形成整體結構。內支撐分塊如圖4所示。
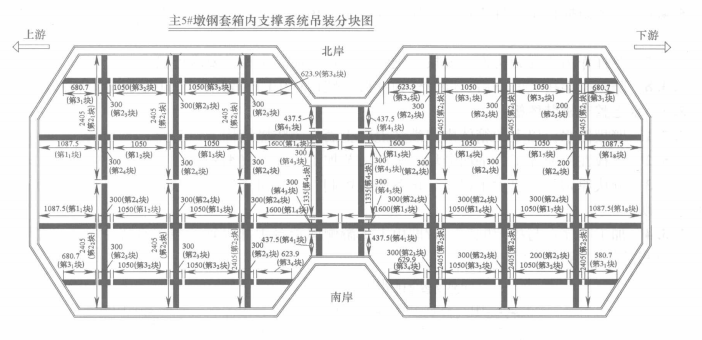
圖4 南塔墩鋼吊箱內支撐分塊布置圖
3.利用甲板駁船將內支撐運輸至現場。
4.利用動臂吊機(或浮吊)吊裝分塊內支撐,並將分塊內支撐與已安裝的壁板及內支撐焊接為一個整體。
5.內支撐接頭離開交叉點1米,使單件塊段形成"+"字形穩定結構,同時現場接頭為標準環形截面形式,避免了空間交線。
6.隨著壁板的安裝跟進安裝內支撐,最終在承台啞鈴處完成內支撐的安裝。
六、拉壓桿的安裝
1.拉壓桿的工作原理;封底混凝土澆築階段,作為"拉桿"。上下端分別與吊箱底板及樁基護筒相連,直接承受混凝土自重,並將荷載傳遞至樁基;抽水後,作為壓桿,在封底頂面與護筒相連,與封底混凝土一起承受水浮力,增強抗浮穩定性。
2.在加工廠加工拉壓桿桿件、拉壓桿上鉸座及下餃座等,並嚴格編號。
3.在底板上焊接拉壓桿下較座。
4.採用動臂吊機安裝拉壓桿,並臨時固定於內支撐上。
5.拉壓桿在條件許可時宜做成整節形式,便於臨時固定;在與護筒焊接前,不需預拉緊固。
七、水平定位系統及導向系統的安裝
1.導向系統主要是在吊箱下放過程中起平面位置約束作用,隨著吊箱的下放以及水流衝擊,呈現為動態約束,因此選擇球形橡膠護弦,這樣與吊箱、護筒彈性摩擦接觸,避免了下放過程中出現卡死或局部破壞的現象。
2.定位系統在吊箱下放到位後、封底施工階段對吊箱平面位置起約束作用,通過剛性結構將吊箱與樁基固結成整體,定位系統結構強度必須足以克服迎水壓力和漲落潮豎向力,確保封底過程中,吊箱結構紋絲不動。
3.水平定位系統和導向系統在後場預加工。
4.在現場根據護筒偏位情況,測量安裝水平定位系統和導向系統。
5.導向系統安裝時,必須確保在鋼吊箱下放過程中,導向系統與護筒之間有5厘米的空隙。
6.水平定位系統預安裝與設計位置,與護筒之間的距離以不影響下放為原則;吊箱下放到位並糾偏後,水下利用千斤頂推出定位系統卡緊護筒。
八、鋼吊箱整體下放
1.安裝整體下放系統,參照支撐樁位置精確安裝,其中:懸吊梁安裝允許偏差:±20毫米;千斤頂安裝允許偏差:±10毫米;吊索(鋼絞線)安裝垂直度;與鉛垂面夾角≤3°。
鋼吊箱下放系統如圖5所示。

圖5 南塔墩鋼吊箱整體下放系統布置圖
下放設備的總體及單點承載能力均應大於理論荷載2倍以上。
2.布置下放系統同步監測系統。
3.布置結構安全監測系統。
4.在鋼吊箱各構件均焊接完成以後,對各吊點進行單點試提。
5.單點試提無異常,即對鋼吊箱進行整體試提。
6.鋼吊箱整體試提無異常,正式提升鋼吊箱。
7.拆除底板下放的支撐牛腿及平聯。
8.下放範圍內的障礙物探測、河床探測。
9.下放鋼吊箱直至入水自浮,選擇下放時機,確保低平潮入水,下放速度控制在1.5~2.0米/小時。
10.拆除懸吊系統。
11.對各箱室獨立對稱加水以下沉鋼吊箱;通過加水,使其在低潮位時在設計標高以下。
九、吊箱下放過程中的信息化控制手段
1.布置安全監測元件,包括關鍵結構應力監測元件、支撐樁差異沉降元件及底板變形監控元件。元件的布置以結構仿真計算數據為依據,對稱布置於應力較大的部位。
2.群頂同步性監測元件,包括荷載同步性監測元件(壓力感測器)及位移同步性監測設施(長距離感測器以及雷射測距儀)。儀器布置要求每個吊點、每台千斤頂均處於位移荷載雙控狀態。
3.結構應力測試,在拼裝及試吊階段,每工班測試一次,下放階段每30分鐘測試一次;同時,在吊箱完全懸空、接近水面、入水1米這三種關鍵狀態下必須各測試一次;測試過程中,停止下放,監測結果正常並與計算基本吻合(正負偏差不超過20%)時再繼續下放。
4.同步性監測由計算機控制櫃自動適時採集。一旦不同步性超過5%時,自動報警,所有千斤頂自動鎖死,停止下放以確保全全。
5.下放同步性採用位移荷載雙控,具體控制要求為±5%。
十、吊箱豎向鎖定
1.選取低潮位時將豎向限位梁安放於壁板上,並安放連線鋼管
2.在高潮位時,壁板上浮至設計位置,焊接連線鋼管及原有懸吊梁。豎向定位裝置如圖6所示。

圖6 南塔墩鋼吊箱豎向定位裝置圖片
3.對鋼吊箱進行抽水,使其在低潮位時也在設計標高處。
十一、吊箱平面糾偏定位
1.在上兩層水平定位系統處安放千斤頂,調整鋼吊箱的水平位置。水平定位裝置如圖7所示。

圖7 南塔墩鋼吊箱水平定位裝置圖片
2.鋼吊箱調整到設計位置後,由潛水員將楔塊安放於最下層水平定位系統處。
3.將千斤頂用型鋼替換,完成鋼吊箱的水平鎖定。
4.將拉壓桿上鉸座與鋼護筒焊接。
5.受漲落潮影響(3米潮差),豎向水平定位必須相互協調配合,通常先豎向定位,再快速頂升水平調節千斤頂,完成水平鎖定。
6.吊箱完成定位後,應及時加固,採用型鋼和鋼管將壁板和護筒焊接牢固,確保封底過程中吊箱不產生位移。
7.吊箱定位穩定後,及時焊接拉壓桿,按先周邊後中心的順序安裝拉桿。首先,在護筒上用油漆標明上鉸座的準確位置和標高;其次,在拉桿頂端穿上銷子與上鉸座固定在一起,拉直拉桿,將鉸座耳板與護筒焊接牢固。為避免拉桿掛錯護筒,拉桿上鉸座應按設計院提供的樁位護筒編號統一作出標記,現場焊接時統一對號入座,並便於檢查。
十二、底板封堵與清理、封底混凝土澆築
1.拉壓桿與鋼護筒焊接完成後,由潛水工在水下用鋼絲刷清洗護筒,並清除底板上殘留的雜物。
2.底板封堵:採用弧形板及麻袋乾混凝土封堵,每個護筒周邊的弧形板等分為4~6塊,單件重40千克左右。下放前將各塊封堵板分開、後移布置於底板開孔邊各處,利用螺栓臨時固定;吊裝定位後,潛水員水下緊固封堵板貼緊護筒。底板封堵如圖8所示。

圖8 鋼吊箱底板封堵圖片
3.以滿足導管布點為原則進行封底施工平台搭設,布置導管。
4.水下混凝土澆築:封底厚度在3米以內時,採用全高度推進的形式澆築,推進過程由兩側向中間,基本對稱進行。
結合混凝土供應能力,對封底混凝土進行分倉分區,相對獨立施工,降低混凝土供應中斷造成的風險。分倉分區應儘量對稱,混凝土澆築時先中間倉後兩邊倉,逐倉對稱進行。
5.標高監控:通過改善混凝土的工作性能和加密導管布置,儘可能使封底混凝土頂面平整;為減小抽水後的鑿除量,同時保證有足夠的封底厚度,封底混凝土頂標高控制在[-20厘米,+10厘米]以內較合理。
十三、拉壓桿轉換
抽水、轉換拉壓桿拉壓桿轉換如圖9所示。

圖9 拉壓桿轉換示意圖
1.待封底混凝土達到一定強度後,封閉連通管,抽出吊箱內的水
2.將拉桿與護筒連線位置由水面以上,轉換至封底混凝土頂面,最終形成壓桿。
3.找平封底混凝土。
至此,吊箱施工完成,乾施工環境形成轉入水上承台施工環節。
《超大型鋼吊箱水上整體拼裝下放施工工法》勞動力組織如表1所示。
材料設備
《超大型鋼吊箱水上整體拼裝下放施工工法》主要配套設備如表2所示。
質量控制
《超大型鋼吊箱水上整體拼裝下放施工工法》的質量控制要求如下:
1.遵照中華人民共和國行業標準2005年前已實行的《公路工程質量檢驗評定標準》JTG F-80/1-2004(土建工程)的要求執行。
2.按該工程的招標檔案及業主確定的技術質量標準要求執行。
3.鋼吊箱壁板及內支撐委託加工能力強、技術水平高的專業鋼結構加工廠製造。鋼吊箱加工過程中採用有效措施防止焊接變形。
4.鋼吊箱焊接嚴格按圖紙要求,整個吊箱需做水密檢查。
5.焊縫需進行外觀檢驗、內部質量檢驗以及煤油滲透試驗。
所有焊縫均應在冷卻後按下表質量標準進行外觀檢查,並填寫檢查記錄。所有焊縫不得有裂紋、未熔合、焊瘤、夾渣、未填滿及漏焊等缺陷,外觀檢查不合格的焊接件,在未返修合格前不得進入下一道工序。焊縫外觀檢查質量如表3所示。
| | | |
| | | |
| | | |
| | | |
| | b<12毫米時,h≤3毫米 12<b≤25毫米時,h≤4毫米 | |
外觀合格後,對鋼吊箱所有關鍵受力焊縫及試板對接焊縫應沿焊縫全長進行超音波探傷,質量等級為I級;檢驗不合格件,在未返修合格前不得進入下一道工序。
6.下放系統,包括千斤頂、錨環、懸吊梁的安裝需精確放樣安裝,控制安裝偏差。
7.鋼絞線的安裝逐根進行,並用1噸鏈條葫蘆預緊,上、下錨孔用同一根鋼絞線嚴格對齊,不得成麻花狀或鬆緊不一。
8.嚴格底板封堵,並實施水下復檢制度;經歷兩個漲落潮考驗後,再次檢查底板封堵情況,防止混凝土澆築過程中的滲漏現象。
9.配備足夠的混凝土生產及供應系統,並儲備足夠的混凝土原材料;開始澆築後,要求混凝土連續不間斷供應,直至該區域澆築完成。
10.嚴格控制混凝土的頂面高程。測量人員應勤於檢測,尤其是在接近頂標高時,應每10分鐘量測一次,及時掌握混凝土頂面高程,以便採取對應措施。
11.嚴格控制混凝土的拌合質量,確保混凝土坍落度及和易性。
安全措施
採用《超大型鋼吊箱水上整體拼裝下放施工工法》施工時,除應執行國家、地方的各項安全施工的規定外,尚應遵守注意下列事項:
1.遵照中華人民共和國行業標準現行的《公路工程施工安全技術規程》(JTJ 076-95)及《公路項目安全性評價指南》(JTG/T B05-2004)的要求執行。
2.遵照國家頒發的有關安全技術規程和安全操作規程辦理。
3.嚴格按施工工藝、操作規程及施工組織設計的有關安全條款進行施工。
4.建立健全各工地、各施工環境下得施工安全規章制度,做好上崗前職工安全培訓工作;特殊工種必須持安全考核證上崗,嚴禁無證操作、違章作業。
5.對加工區水域航道、水深、流速及流向由拖帶船船長按通航安全要求進行確認。
6.下放系統的千斤頂在安裝前均應作對拉試驗,確保設計性能。
7.下放系統及與下放相關的結構、焊縫必須嚴格檢查,確保滿足受力要求,安全係數不得小於2。
8.成立吊箱施工現場指揮小組,並與協作單位統一,確保專人指揮;吊裝整體下放前對參與施工的人員資質進行審查確認,並召開一次專項安全交底和培訓,明確相應職責和分工。
9.下放前由結構設備安全檢查小組對起重設備、吊箱關鍵結構的可靠性及安全性等進行嚴格檢查;吊箱下放應選擇風力低於5級、潮汐處於相對穩定的時間段進行。
10.吊箱拼裝為交叉作業,應安排足夠的起重工在吊箱頂面或具有通視條件的位置進行吊裝作業;由於施工場麵點多面廣,施工現場應保證有3名安全員在場。
11.在封底混凝土澆築平台上鋪設通道、安裝欄桿以及掛設安全網;非通道區嚴格隔離。
12.吊箱下放過程中,儘可能減少吊箱內的人員數量,並專人、統一指揮下放作業。
13.在整個吊箱下放期間,設定明顯的警示標誌,防止碰撞。
環保措施
《超大型鋼吊箱水上整體拼裝下放施工工法》的環保措施如下:
1.按照《中華人民共和國環境保護法》以及地方法規和行業企業要求,堅持“預防為主、防治結合”的方針,努力實現可持續發展戰略。
2.加強施工管理和工程監理工作,嚴格檢查各種施工機械,防止油料發生泄漏污染水體。
3.施工材料如油料、化學品不堆放在地表水體附近,並應備有臨時遮擋的帆布。
4.採取所有必要的措施防止泥土和散體施工材料阻塞江河、水渠或2005年前已有的灌溉溝渠或水管。
5.根據現場情況設定排水溝及沉澱池,污水經沉澱後方可排放(沉澱物含量不大於施工前河流中所達到的含量);沉澱池內泥沙應定期清理,沉澱池一月清洗一次。
6.選用符合國家衛生防護標準的施工機械設備和運輸工具,確保其廢氣排放符合國家有關標準。
7.在施工過程中,操作人員要加強各種施工機械的維修保養,儘可能降低施工機械噪聲的排放。
效益分析
以蘇通大橋南塔墩鋼吊箱為例,現將《超大型鋼吊箱水上整體拼裝下放施工工法》與傳統的分節散拼方法的經濟效益分析對比如下:
1.工期比較
整體吊裝工藝較傳統分節散拼工藝節省工期40天左右。
2.設備費用對比分析
整節拼裝費用包括拼裝費(周期60天)及整體下放費用;
分節散拼及費用包括63噸浮吊費用、運梁船(甲板駁)等運輸費用(周期90天)及分節下放費用;整節下放費用較分節散拼下放費用節省50萬元。
3.材料費用對比分析
整體下放節省的主要材料包括底板總計1200餘噸。
4.人工費用對比分析
整體拼裝下放較分節散拼下放節省人工4000工日。
5.質量
整體拼裝減少了現場焊縫近4000米,整個拼裝均在穩定平台上,質量更容易保證;同時豎向不分節,吊箱垂直度較多節散拼更容易保證。
6.安全
整體拼裝下放工藝拼裝全過程均在穩定平台上,安全更容易保證;
整體下放通過計算機控制及結構應力安全檢測等信息化施工手段,施工更安全可靠。
註:施工費用以2005-2006年施工材料價格計算
套用實例
《超大型鋼吊箱水上整體拼裝下放施工工法》的套用實例如下:
蘇通大橋南塔墩鋼吊箱,平面尺寸為117.35米×51.7米×14.4米,有一個半足球場大,重量約5880噸,為2005年前世界上最大的鋼吊箱,施工難度和技術難度大。採用整體拼裝、下放工法於2004年9月5日開始吊箱整體拼裝,11月27日完成吊箱整體下放定位,定位最大偏差20毫米;12月14日一次性成功封底,抽水後無一滲漏,比契約工期提前40天完成,工程質量評定為優良,未發生一起安全事故,為下階段承台施工奠定了基礎。
榮譽表彰
2008年1月31日,中華人民共和國住房和城鄉建設部發布《關於公布2005-2006年度國家級工法的通知》建質[2008]22號,《超大型鋼吊箱水上整體拼裝下放施工工法》被評定為2005-2006年度國家一級工法。