板坯連鑄是以板坯為主要產品的連續鑄鋼煉鐵技術。鑄坯寬厚比大於3的即稱板坯,連鑄軋鋼板坯主要用於軋制扁平板(厚板、中板、薄板、帶卷)材。通常連鑄機澆鑄的板坯尺寸為:厚度150~250mm,寬度1000~1800mm;小板坯寬度可為600mm,厚度120mm。板坯厚度小於100mm的稱薄板坯。
基本介紹
- 中文名:板坯連鑄
- 外文名:slab continous casting
- 學科:冶金工程
- 出現時間:20世紀60年代
- 產品:板坯
- 類別:連續鑄鋼煉鐵技術
簡史
結構及工藝技術
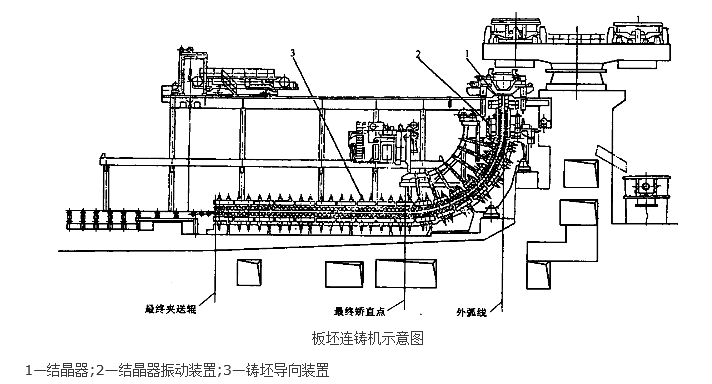
板坯連鑄是以板坯為主要產品的連續鑄鋼煉鐵技術。鑄坯寬厚比大於3的即稱板坯,連鑄軋鋼板坯主要用於軋制扁平板(厚板、中板、薄板、帶卷)材。通常連鑄機澆鑄的板坯尺寸為:厚度150~250mm,寬度1000~1800mm;小板坯寬度可為600mm,厚度120mm。板坯厚度小於100mm的稱薄板坯。
板坯連鑄是以板坯為主要產品的連續鑄鋼煉鐵技術。鑄坯寬厚比大於3的即稱板坯,連鑄軋鋼板坯主要用於軋制扁平板(厚板、中板、薄板、帶卷)材。通常連鑄機澆鑄的板坯...
連鑄即為連續鑄鋼(Continuous Steel Casting)的簡稱。在鋼鐵廠生產各類鋼鐵產品過程中,使用鋼水凝固成型有兩種方法:傳統的模鑄法和連續鑄鋼法。而在二十世紀五十...
把高溫鋼水連續不斷地澆鑄成具有一定斷面形狀和一定尺寸規格鑄坯的生產工藝過程叫做連續鑄鋼。完成這一過程所需的設備叫連鑄成套設備。澆鋼設備、連鑄機本體設備、...
《常規板坯連鑄技術》是 冶金工業出版社出版的圖書,作者是楊拉道,謝東鋼, 楊立道。...... 《常規板坯連鑄技術》回顧了常規板坯連鑄技術的發展進程,重點介紹了現代...
超低頭板坯連鑄指的是在超低頭弧型連鑄機進行的連續鑄鋼類型。連鑄指的是使鋼水不斷通過水冷結晶器,凝成硬殼後從結晶器下方出口連續拉出, 經噴水冷卻,全部凝固後...
板坯,是鋼坯的一種,為鋼水通過連鑄機連鑄形成,一般鑄坯寬厚比大於3的即稱板坯,其主要用於軋制板材,但尚未開始軋制。...
連鑄轉爐生產出來的鋼水經過精煉爐精煉以後,需要將鋼水鑄造成不同類型、不同規格的鋼坯。連鑄工段就是將精煉後的鋼水連續鑄造成鋼坯的生產工序,主要設備包括迴轉台...
高效連鑄是指中國的一種高效率連鑄技術。中國常規連鑄機的技術經濟指標是:150mm×150mm方坯的拉速在2.0m/min以下;120mm×120mm方坯在3.0m/min以下,板坯連鑄的...
薄板坯連鑄軋鋼(thin slab continous casting)是一種近終形連續鑄鋼煉鐵技術,這種技術的實質是在保證成品鋼材質量的前提下,儘量縮小鑄坯的斷面來取代壓力加工。...
在弧型連鑄機上進行的連續鑄鋼類型。這種連鑄機的結晶器及二次冷卻裝置布置在同一半徑的圓弧上,大致占一個圓的1/4,從二冷區出來的弧型鑄坯在圓弧的最低點(1...
結晶器是連鑄機非常重要的部件,是一個強制水冷的無底鋼錠模。稱之為連鑄設備的“心臟”。...
高速連鑄軋鋼是國外80年代初期發展起來的一項連鑄|軋鋼新技術。...... 目前,國外己經成功地開發了拉速達5m/min的高速板坯連鑄機。分析國外高速連鑄技術的發展,除設...
立式連鑄指的是澆鑄和鑄坯凝固全部過程都是在垂直狀態中進行的連續鑄鋼類型。立式連鑄具有鑄坯的冷卻均勻,凝固組織對稱性好等特點。...
整體塞棒、長水口(大包長水口)、浸入式水口(中包所用水口)、中包水口等功能性耐火元件,統稱為連鑄三大件。其材質主要有鋁碳質、鋁鋯碳質、鎂碳質或鎂鋁尖晶石...
直弧型連鑄是鋼水注入垂直放置的直型結晶器,在結晶器下有2~3m的垂直鑄坯導向段的連續鑄鋼煉鐵類型。由於直弧型鑄機生產的鑄坯內部質量比弧型連鑄機的好,基本...
薄板坯連鑄|軋鋼技術屬於近終形連鑄連軋技術,可生產出接近成品規格的薄板(帶)坯,是連續緊湊化流程,所以薄板坯連鑄一連軋工藝是鋼鐵工業現代化流程最新的標誌。我國...
連鑄生產線組成:由澆鑄和出坯兩大機組組成。主要設備有:鋼包迴轉台、結晶器及震動裝置、一冷段、扇形段、拉矯機、火焰切割機、轉盤、出坯錕道、引錠桿及存放台...
《薄板坯連鑄連軋》是冶金工業出版社出版的圖書,作者是田乃媛。本書詳細論述了薄板坯連鑄連軋工藝中的關鍵技術以及薄板坯連鑄連軋帶卷的品種和質量問題,可供學習者...
從結晶器出來的板坯厚度為60㎜,經帶液芯鑄軋後出:拉矯機鑄坯厚為22㎜,其...義大利的阿爾維第(Arvedi)公司已建成一套直弧結晶器,帶液芯軋制薄板坯連鑄連軋...
近終形連鑄指的是所有澆鑄接近最終產品尺寸和形狀的澆鑄方式。隨著連鑄技術的發展,採用方 (圓) 坯連鑄機生產的鑄坯生產條形產品, 採用厚度為150-250mm連鑄板坯...
由連鑄得到的較薄的板坯直接送入連軋機組軋成板材的生產工藝。 套用學科 材料科學技術(一級學科),金屬材料(二級學科),鋼鐵材料(三級學科),鋼鐵材料生產技術(四級學...
《薄板坯連鑄裝備及生產技術》是2007年冶金工業出版社出版的圖書,作者是張金柱、潘國平、楊兆林。該書系統地總結了薄板坯連鑄裝備與生產技術的發展歷程、取得的經驗、...
《連鑄設備及工藝》是2009年9月1日由中國勞動社會保障出版社出版的圖書,作者是馮阿強。本書針對中等職業技術學校學生的認知特點和職業需求,深入淺出地講解了中職...
《薄板坯連鑄及熱裝直接軋制》是1993年冶金工業出版社出版的圖書。...... 4.8板帶鋼連鑄―熱裝及直接軋制工藝 4.8.1厚板坯連鑄―熱裝軋制(CC-HCR)工藝 4.8.2...
連鑄坯拉矯指的是把連鑄坯從弧形連鑄機的結晶器中以一定的拉坯速度拉出並矯直的工藝過程。現代連續鑄鋼的基本工藝之一,由拉矯機完成。...
《連續鑄鋼板坯(YB 2012-1983)》適用於供熱軋用普通碳素結構鋼、優質碳素結構鋼和低合金結構鋼的連續鑄鋼板坯(以下簡稱連鑄板坯)。中華人民共和國冶金工業部部標準,...
近終形連鑄指的是所有澆鑄接近最終產品尺寸和形狀的澆鑄方式。...... (圓) 坯連鑄機生產的鑄坯生產條形產品, 採用厚度為150-250mm連鑄板坯生產板材的技術已逐漸成...