“彩電前殼”即彩電前面起固定顯示屏和裝飾作用,且結構複雜的四邊形塑件。隨著人們生活水平的提高,對彩電尺寸大小的要求也逐步提高。而彩電越大所需的前殼也就越大,對“彩電前殼注射模具”的要求也就越高。所以研究“彩電前殼注射模設計”,具有現實意義。彩電前殼注射模設計,是運用pro/e軟體來設計彩電前殼注射模具的。
塑件分析
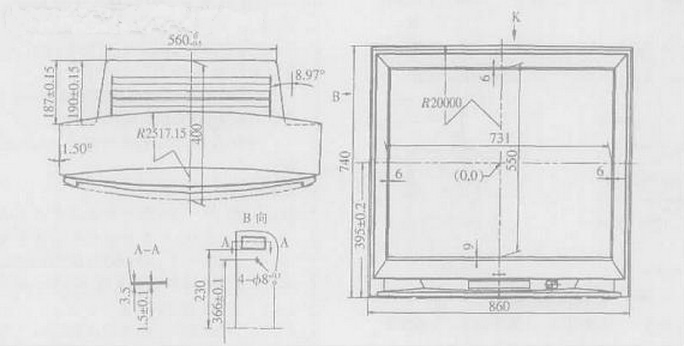
模具分析
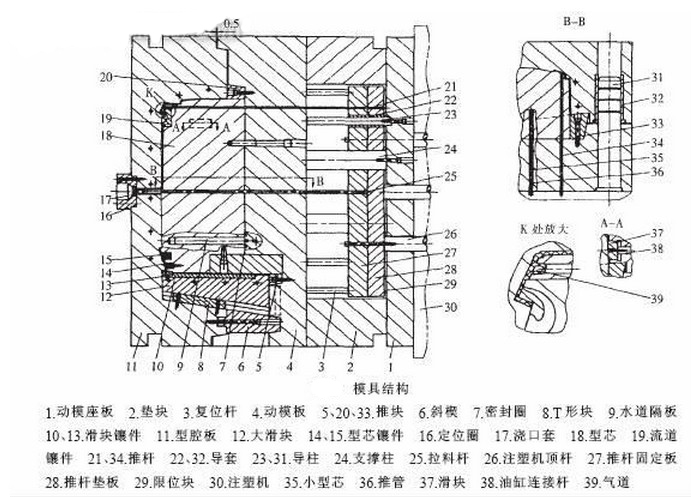
設計步驟
滑塊設計
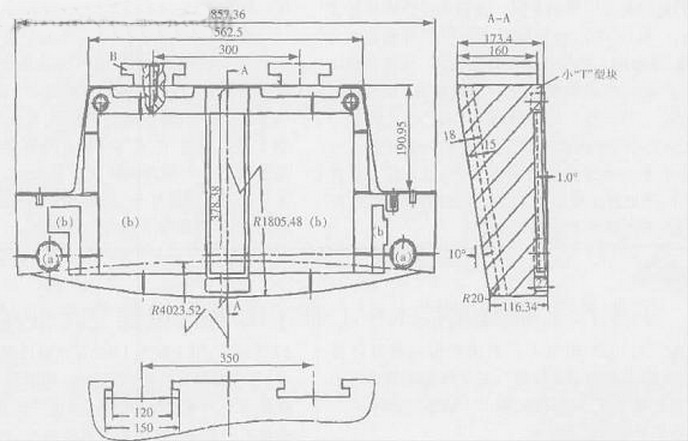
澆口設計
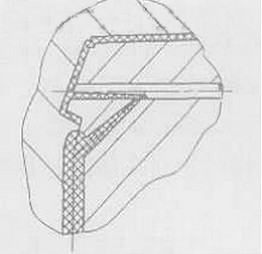
頂出系統
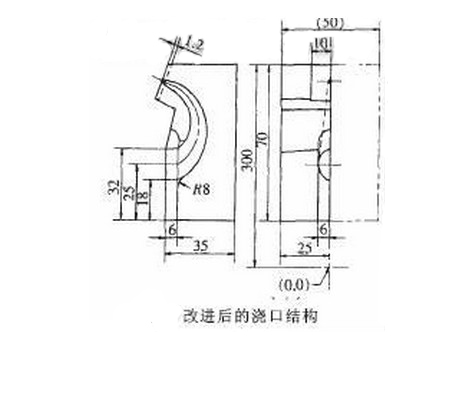
“彩電前殼”即彩電前面起固定顯示屏和裝飾作用,且結構複雜的四邊形塑件。隨著人們生活水平的提高,對彩電尺寸大小的要求也逐步提高。而彩電越大所需的前殼也就越大,對“彩電前殼注射模具”的要求也就越高。所以研究“彩電前殼注射模設計”,具有現實意義。彩電前殼注射模設計,是運用pro/e軟體來設計彩電前殼注射模具的。
“彩電前殼”即彩電前面起固定顯示屏和裝飾作用,且結構複雜的四邊形塑件。隨著人們生活水平的提高,對彩電尺寸大小的要求也逐步提高。而彩電越大所需的前殼也就越大,對“彩電前殼注射模具”的要求也就越高。所以研究“彩電前殼注射模設...
“手機面殼”,即手機前面起固定手機螢幕和固定手機鍵盤以及裝飾等作用的塑膠件。在工業生產中,“手機面殼”是依靠“手機面殼注射模具”來實現批量生產的。“手機面殼注射模設計”,是運用pro/e軟體來設計手機面殼注射模具的。塑件分析...
《注射模設計方法及實例解析》是2013年機械工業出版社出版的圖書,作者是王暉、劉軍輝。內容簡介 王暉、劉軍輝主編的《注射模設計方法及實例解析》系統地介紹了注射模具設計的基本方法與實踐經驗,包括塑膠產品設計、注塑機及注塑成型工藝、...
59.副駕駛氣囊蓋注射模 60.空調進風面板注射模 61.喇叭罩蓋注射模 62.顯示燈導向條注射模 63.下通風管注射模 64.指示燈架的外殼注射模 65.中央出風面板注射模 知識點:冷卻系統設計 66.手套箱注射模 67.出風管注射模 四 其他...
第二節 側抽芯注射模具製造 一、斜導柱的製造 二、滑塊的加工 三、斜導柱側抽芯機構的裝配 第三節 側抽芯注射模具設計與製造案例 一、設計任務 二、殼件注射成型工藝設計 三、殼件側抽芯注射模具設計 四、殼件側抽芯注射模具...
35AMI注射流動分析過程及模擬結果解釋153 351利用AMI軟體運行流動分析的主要實現過程153 352流動分析後處理主要結果的解釋159 第4章 基於CAE的注射模澆注系統最佳化設計實例分析/179 41空調外殼注射模澆注系統設計與最佳化180 ...
2.1 塑膠注射模具設計流程簡介 2.2 塑膠注射製品的設計 2.3 塑膠注射模具結構簡介 第3章 塑膠注射製品設計實例 3.1 音響按鈕設計範例 3.2 遙控器電池門設計範例 3.3 鏡盒式計算器底蓋設計範例 3.4 電視機前殼製品設計範例 3...