“手機面殼”,即手機前面起固定手機螢幕和固定手機鍵盤以及裝飾等作用的塑膠件。在工業生產中,“手機面殼”是依靠“手機面殼注射模具”來實現批量生產的。“手機面殼注射模設計”,是運用pro/e軟體來設計手機面殼注射模具的。
基本介紹
- 中文名:手機面殼注射模設計
- 類型:儀器設備
塑件分析,設計要點,設計方案,設計步驟,型腔設計,型芯設計,分型設計,澆口設計,導向設計,冷卻系統,脫模設計,工作過程,
塑件分析
手機面殼,要求具有一定的強度、剛度、耐熱和耐磨損等性能,同時還必須滿足絕緣性。ABS合成塑膠以其具有很好的韌性(抗震性) 、密封性,很高的機械強度,耐化學腐蝕,拿在手上具有質感。根據以上特點以及經濟因素,採用ABS與PC合成塑膠,其收縮率為0.6%。如結構示意圖所示。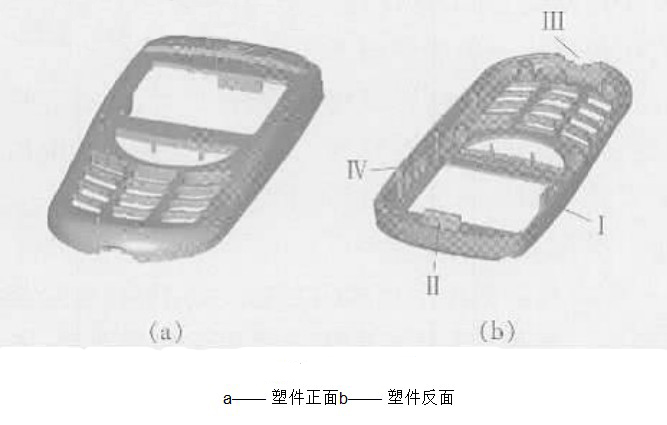
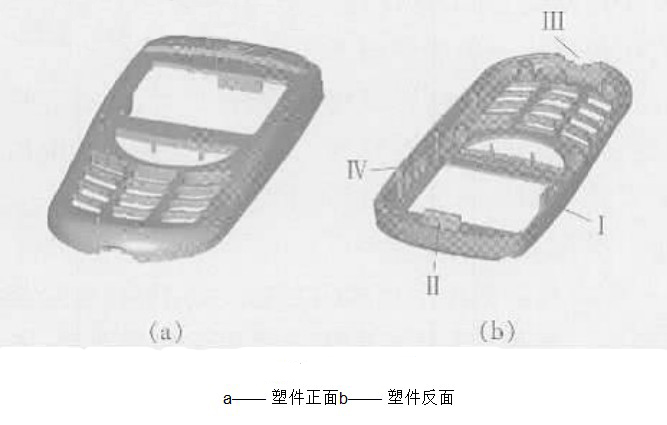
結構示意圖
設計要點
1、脫模斜度。
設計脫模斜度的目的是便於塑件的脫模,避免在脫模過程中拉傷塑件表面,其大小取決於塑膠的收縮率。脫模斜度的取向要根據塑件的內外型尺寸而定。
塑件外形以型腔大端為準,尺寸要符合圖紙要求,斜度沿形狀減小方向。要求開模後塑件留在型芯上,塑件內表面的脫模斜度應小於外表面的脫模斜度。根據ABS 的性能,型芯的脫模斜度取1.5°。
2、加強筋。
為了使塑件與底殼便於裝配,並有一定的強度和剛度,同時又能避免因壁過厚而產生成型缺陷,在塑件內表面外側增設了多處加強筋,小端厚度0.6mm,並做1°斜度。
3、塑件尺寸公差與精度。
該塑件長98mm,寬43mm,最高13mm,其粗糙度值為Ra0.06!m。影響塑件公差的主要因素是: 模具製造誤差及磨損誤差,尤其是成型零件的製造和裝配誤差以及使用中的磨損、塑膠收縮的波動、注射工藝條件的變化、塑件的形狀和飛邊厚度的波動、脫模斜度及成型後塑件的尺寸變化。該塑件選用尺寸精度等級為6級,公差為GB/T14486- 93尺小公差數值。
設計方案
在設計手機面殼時,必須考慮成型時分型面的形狀和位置,否則無法用模具成型。因側向合模鎖緊力較小,故應將投影面積大的分型面放在動、定模的合模主平面上,而將投影面積較小的分型面作為側向分型面。
手機面殼注射模具的分型面選擇在塑件的大平面處。根據所用注塑機的工藝參數,如開模行程、注射壓力、裝模空間等決定將該產品用1 模1 腔的形式生產。
設計步驟
型腔設計
手機面殼注射模設計採用嵌入式型腔結構。加工方法可採用普通機加工、數控工具機、電火花、電鑄成型等方法。將一個整體型腔嵌入到型腔固定板中,嵌入的型腔材料定模為SHD61,硬度為35HRC;動模為NAK80,硬度達40HRC。該結構廣泛套用於中小型塑件的模具中。
型芯設計
型芯是用來成型塑膠塑件的內表面的成型零件。手機面殼注射模具中動模型芯採用鑲拼式型芯結構。目的是既可節省優質模具鋼,便於機加工和熱處理,又利於型芯冷卻和排氣。
分型設計
由於抽芯距離不大,為使模具結構緊湊,採用整體式側向抽芯機構。其結構示意圖如側向抽芯機構示意圖所示,主要結構有: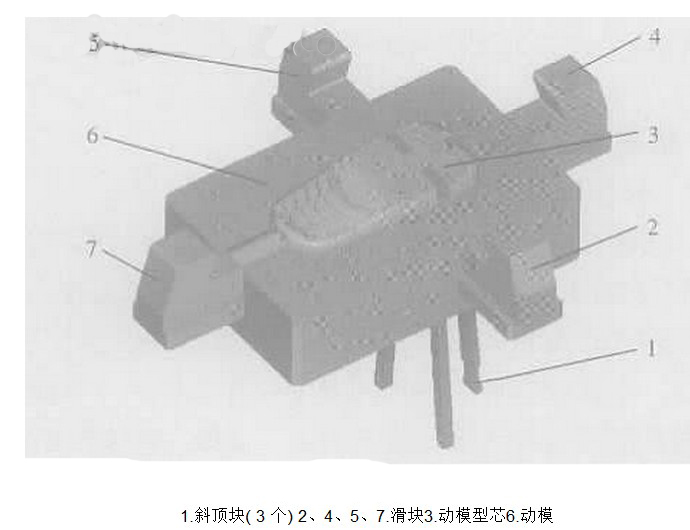
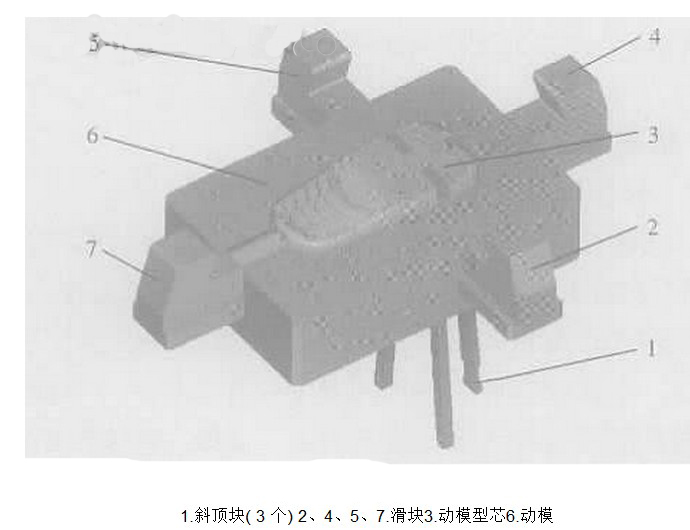
側向抽芯機構示意圖
( 1) 側向抽芯機構示意圖中2、4、5、7各為一個整體滑塊,將側向型芯固定在該滑塊上,利用滑塊上的斜面對產品外側面的凹坑( 結構示意圖中Ⅰ、Ⅱ、Ⅲ、Ⅳ處) 進行抽芯。經過充分考慮各項工藝參數,斜面與垂直面的傾斜角度確定為18°,既達到了抽芯目的,又確保了模具的整體結構合理。
( 2) 側向抽芯機構示意圖中設計有3 個斜頂塊,目的是成型塑件內側凹坑( 圖1 中Ⅰ、Ⅱ、Ⅳ處的內側面) 。將斜頂塊固定在頂桿固定板上,頂出時,斜頂塊隨著固定板一起運動,斜頂塊在向前運動的同時,也作側向移動,達到抽芯的目的。
斜頂塊採用優質合金材料,選用718 材料,並用經過調質處理的螺釘緊固在頂桿固定板上;通過對塑件結構的分析計算,斜頂塊傾斜角度為6°。這樣既保證了側向抽芯動作的順利完成,又使模具工作順暢,受力均勻。
澆口設計
澆口是澆注系統的關鍵部分,澆口的形狀、數量、尺寸和位置對塑件的質量影響很大。根據塑件的結構要求,手機面殼注射模設計採用點澆口形式。點澆口的直徑由推薦值取d=1.0mm。而且,為了更有效地充滿型腔,採用熱唧嘴。如單點熱澆注口結構示意圖所示。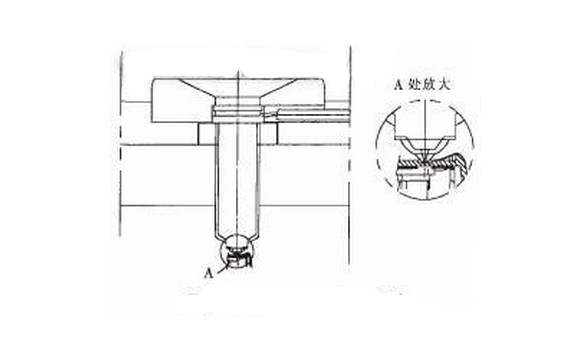
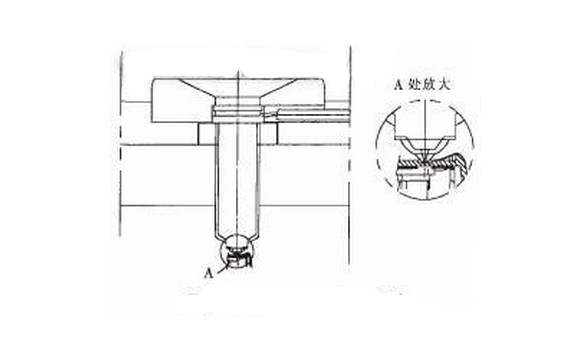
單點熱澆注口結構示意圖
採用熱唧嘴的主要優點是:
( 1) 無水口料,不需要後續加工,使整個成型過程完全自動化,節省工作時間,提高工作效率。
( 2) 壓力損耗小。熱澆道溫度與注塑機射嘴溫度相同,避免了原料在澆道內的表面冷凝現象,注射壓力損耗小。
( 3) 水口料重複使用會使塑膠性能降解,而使用熱流道系統沒有水口料,可減少原材料的損耗,從而降低產品成本。在型腔中溫度及壓力均勻,塑件應力小,密度均勻,在較小的注射壓力下,較短的成型時間內,注塑出比一般的注塑系統更好的產品。
( 4) 熱唧嘴採用標準化、系列化設計,配有各種可供選擇的噴嘴頭,互換性好。獨特設計加工的電加熱圈,可達到加熱溫度均勻,使用壽命長。
導向設計
該模具選用標準模架CI2330,採用導柱和導套機構導向,導柱、導套的布置方式均為標準布置,有關尺寸及布置形式詳見模架資料。
冷卻系統
冷卻系統的設計對於產品的成型至關重要,如果冷卻不好或冷卻不均勻,必然導致收縮不均勻,為了使冷卻效果好,在模具的定模型腔板和動模型腔板內開設了水道,橫向穿過這兩塊模板,這樣使塑件各處的冷卻均勻,模具的模溫均勻。 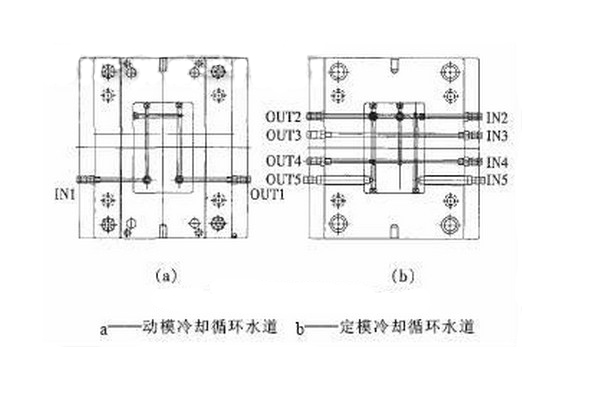
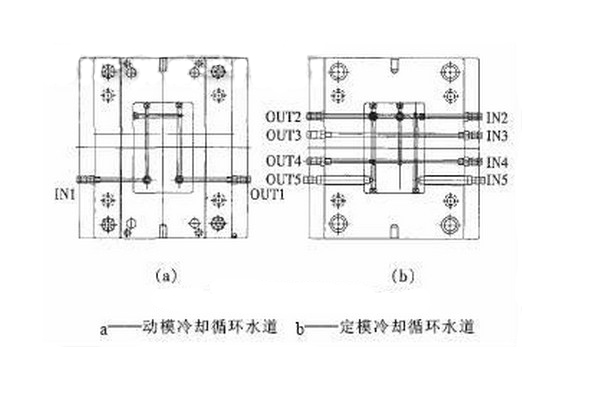
冷卻循環水道示意圖
動、定模冷卻水道孔徑採用!6mm 鑽頭加工。其冷卻循環示意圖如冷卻循環水道示意圖 所示,其中IN5~OUT5 通熱油,其餘通冷水,以加強冷卻。
脫模設計
該模具塑件的頂出主要採用7 根φ3mm 的頂桿、3 根φ4mm 的頂桿以及15 根φ1.5mm 的頂桿頂出。為確保塑件在出模過程中不傾斜、不變形,頂出機構應設導向裝置,以保證頂出機構平穩。
另外,前面介紹的3 個斜頂塊抽芯機構除完成抽芯任務外,還兼有頂出塑件的功能。
工作過程
如模具裝配示意圖所示。開模時,由主分型面分型,斜滑塊開始側向抽芯,當模具開啟到終點位置時,斜滑塊側向抽芯結束,在型芯包緊力的作用下,塑件從定模型腔中拉出,然後在頂出機構頂桿的作用下,頂桿固定板推動斜頂塊及頂桿同時向前運動,斜頂塊及頂桿將塑件頂出。合模時,通過整體滑塊上的斜面、復位彈簧及回程桿將滑塊、斜頂塊復位退回,完成合模,合模結束後開始下一個工作循環過程。 由於採用了熱流道系統,不需要設計定距分型機構,使模具的結構得到了簡化。 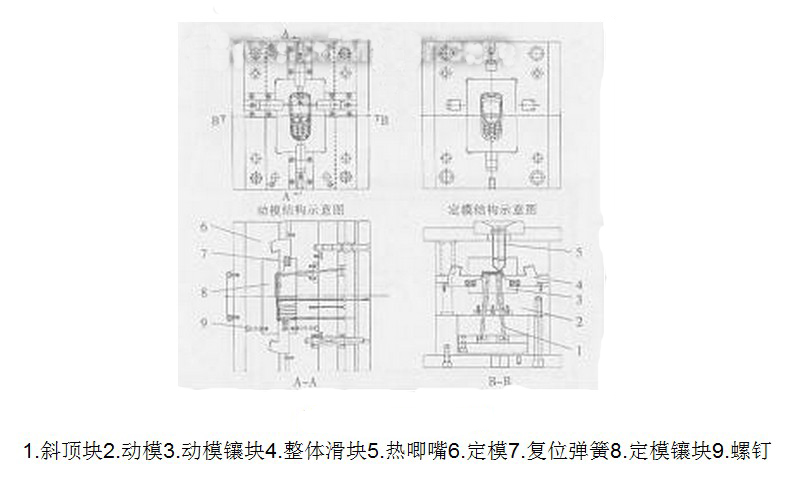
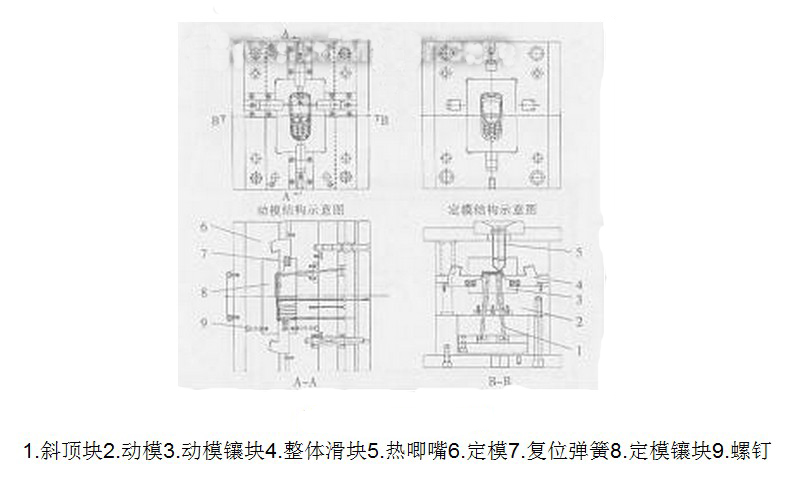
模具裝配示意圖