形成原因
隨著煉油、石化等行業的發展,壓力容器設備逐步向大型化、有色金屬、超厚板方向發展,耐高溫、高壓、抗腐蝕等各類新型材料不斷套用到化工容器中,隨之對容器的製作提出了更高的要求。中油吉林化建設備製造公司於1994年創立大型容器套用懸空雙面埋弧自動焊工藝,通過近幾年對懸空雙面埋孤自動焊工藝進行不斷完善,在原工法只適用碳鋼和低合金鋼的基礎上,通過各種工藝試驗和工程實踐,又成功地開發套用了耐熱鋼、低溫鋼、不鏽鋼及複合鋼板等材料的焊接;施焊厚度範圍由原來的20毫米擴大到62毫米;焊接質量有了進一步提高;套用範圍也由單一的工廠化製造,擴大為既適用於工廠化製造又適用於現場大型容器組焊。中油吉林化建工程有限公司在工程經驗的基礎上完成了《套用懸空雙面埋弧自動焊工藝焊接大型容器工法》。
工法特點
《套用懸空雙面埋弧自動焊工藝焊接大型容器工法》具備以下的特點:
由於母材不開坡口或採用專有的特殊坡口形式,合理的工藝規範,實現不清根、不用手工填充的全自動焊工藝,比傳統手工焊焊接減少人員投入2/3,是普通埋弧焊工藝方法效率的3~5倍。同時填充金屬量減少,焊接層數少,減少焊接材料消耗及機械費用,可比普通埋弧自動焊成本節約40%左右。
因為熔渣的保護,熔化金屬不與空氣接觸,焊縫金屬中含氮量降低,僅為手工電弧焊的十分之一,因而提高了焊縫金屬的塑性和韌性,而且熔池金屬凝固較慢,減少了焊縫中產生氣孔、裂紋的可能性。焊接工藝參數通過自動調節保持穩定,因此焊縫幾何尺寸穩定,焊工操作技術要求不高,焊縫外觀成形美觀,焊縫的化學成分比較均衡、穩定,力學性能好,焊縫內部質量高且均勻一致,提高了焊縫質量。
由於減少了開坡口的工序,對於厚板採用特殊的台式組合型坡口,坡口加工難度不高,正反面各焊一遍,填充金屬量減少,焊接層數少,而且不需清根打磨,焊接一次合格率很容易達到98%以上,焊接返修少,是普通埋孤焊工藝方法效率的3~5倍,有利於保證施工進度,提高了焊接效率。
由於取消了清根打磨的環節,杜絕了浪費,環境污染和清根對操作人員身體的損害;埋孤自動焊是機械化操作,勞動強度低;埋弧焊弧光不外露,沒有弧光輻射,沒有飛濺。安全作業環境好,焊工疲勞程度降低。
各焊接技術參數調節好後,在施焊過程中小車只需按裝配縫找正安裝軌道,或者埋弧焊機在焊接工件時伸臂運行軌跡和焊縫一次對正,添加焊劑和回收焊劑。參與焊接人員少,對焊工技術水平要求不高,焊工培訓成本也低。
操作原理
適用範圍
《套用懸空雙面埋弧自動焊工藝焊接大型容器工法》主要適用於碳鋼板厚度在8~20毫米或低合金高強鋼、耐熱鋼、不鏽鋼厚度在8~16毫米對接焊縫,不開坡口、正反面各焊一遍即成,正面焊熔深達到焊件厚度的40%~60%,反面焊熔深達到焊件厚度的60%~70%。如厚度再增加4~10毫米時,可以採用留8~10毫米鈍邊,小坡口、0~1毫米間隙,雙面各焊接1~2遍即可;普低鋼厚度在30~60毫米或不鏽鋼厚度在20~60毫米範圍內,可以採用特殊的台式組合型坡口,不加焊劑墊或墊板、間隙0~1毫米、不清根、不用手工焊填充、正反面全部實現埋弧焊接(多層焊接)的工藝方法,筒體直徑不小於1米。
工藝原理
埋弧焊是以電孤作為熱源的機械化焊接方法。埋弧焊由4個部分組成:焊接電源接在導電嘴和工件之間用來產生電弧;焊絲由送絲機構和導出嘴送入焊接區;顆粒狀焊劑由焊劑漏斗經軟管均勻地堆敷到焊接接口區;焊絲及送絲機構、焊劑漏斗和焊接控制盤等通常裝在一台小車上,以實現焊接電弧的移動。
套用不開坡口不留間隙懸空雙面埋弧自動焊工藝現場焊接大型容器,關鍵是解決如何保證裝配間隙不大於1毫米和在焊接過程中如何保證焊接工藝參數基本不變使電弧穩定燃燒兩個問題。
裝配間隙不大於1毫米,其裝配面的平面度公差應按裝配最大間隙等於兩裝配面最大上偏差之和減兩裝配面最大下偏差之和計算。設最大上偏差為ΔX,最大下偏差為-ΔX,則:(ΔX+ΔX)-(+ΔX-ΔX)=1毫米;ΔX=0.25毫米;即裝配面的平面度公差為±0.25毫米。
該工法採用高精度吸附式軌道作為氣割小車靠模,同時對板料進行精密切割,通過精細加工達到尺寸精確,在卷制過程中的精準操作和精心組對,達到縱縫組對零間隙0~1毫米,環縫組對零間隙,最大不超過1毫米。
為了保證焊接工藝參數基本不變和維持電弧穩定燃燒,該工法採用高精度吸附式軌道作自動焊小車(加導向器)靠模,保證了焊嘴與裝配縫的水平距離;小車在筒體上的軌道上或在筒體上運行施焊不受筒體不圓度的影響,保證了焊嘴與裝配縫在豎直方向的距離始終不變。
工藝流程
1.工藝程式(下圖所示)
由於不開坡口不留間隙懸空雙面埋弧自動焊對裝配間隙要求精度較高因此必須有一套適合這一要求的施工程式和工藝。該工法要求按下列施工工序流程圖作業。

工藝程式圖
2.下料
鋼板捲筒前對角線公差應控制在小於1毫米。氣割面氣割支線度公差應儘可能控制在±0.25毫米,不得超過±0.5毫米;平面度公差控制在±0.25毫米。
劃線工具:Φ0.2或Φ0.3鋼線、緊線器、鋼捲尺、12千克彈簧秤,2米長鋼板尺、直角尺、劃針、樣沖和手錘。
劃線要點:
1)將鋼板放置於號料平台(或胎架)上;
2)號料確定下料輪廓線的四個頂點並打上沖眼;
3)用緊線器拉鋼線,以四頂點為基準,將鋼線繃緊;
4)用直角尺向鋼板上返線定點;
5)用2米鋼板尺和劃針連點劃線、同時內返50毫米號下料查線;
6)用樣沖沿線打沖眼,間距40~50毫米,沖眼必須正,打偏的沖眼要改正,在改正的沖眼兩端各打一正確的沖眼,兩沖眼距離4~6毫米。
1)氣割機械與工裝
氣割採用半自動膠輪或磁輪小車式切割機,配超音速丙烷氣割設備。小車加導向器,與吸附式軌道配合。
2)氣割用氣體
氣割用氧丙烷氣切割,得到的切割面光潔整齊,粘渣少,割後可見劃線時留下的半個沖眼;產生回火和爆炸的可能性小;切口硬度低含碳量低;比使用乙塊總成本低30%以上。
3)操作方法要點
安裝軌道時按劃好的線將軌道找正;放好半自動氣割小車,使小車導向器與軌道正確配合。氣割前將火焰調好,如火焰分叉應對割嘴進行修理或更換。
4)氣割工藝參數
割嘴後傾角選擇見下表。
超音速割嘴切割工藝參數氧氣壓力(690~790)千帕,燃氣壓力(20~40)千帕。割嘴與切割速度的選擇見下表。
5)封頭氣割加工
成形後的封頭到現場後裝配面沒有加工的需要氣割加工。
氣割時將筒節立起與封頭裝配的一面朝上,封頭置於筒節上方相隔300毫米左右與筒節對正,將封頭與筒節定位。定位前封頭和筒節均需找圓合格。以筒節上端面為靠模,用氣割機切割封頭,切割後按原位置落下封頭可得到與筒節相吻合的配合面注意封頭落下前要在筒節與封頭上作好標記以免封頭落下後錯位。
定位焊縫一般採用手工電弧焊,拼板、筒節縱縫、環縫、筒節與封頭的裝配均採用不開坡口小間隙懸空雙面埋弧自動焊。
1)定位焊縫
定位環縫宜選在雙面焊後焊的一面,一般在筒體的內側。焊接完先焊的一面後,將定位焊縫磨除,再進行背面焊接。定位焊縫的尺寸見下表。
2)懸空雙面埋弧自動焊焊接工藝
採用懸空雙面埋弧自動焊工藝,為保證正面焊接時不燒穿,第一層的焊接電流,應根據實際工作中總結出來的參數進行(下表,一般為反面焊接電流的80%~90%,熔深為整個焊件金屬厚度的40%~60%;反面焊接,因為必須保證整個焊縫的熔透(熔深約達到焊件厚度的60%~70%),要加大反面焊接電流,以達到足夠的熔深效果。
焊絲直徑(毫米) | 焊接厚度(毫米) | 焊接順序 | 焊接電流(安) | 焊接電壓(伏) | 焊接速度(米/小時) |
---|
| | | | | |
| | | | | |
| | | | | |
| | | | | |
| | | | | |
| | | | | |
| | | | | |
| | | | | |
| | | | | |
3)拼板及縱縫焊接
因起弧和收弧部位是埋弧焊縫薄弱部位,且成型不好,一般拼板焊縫及筒節縱縫焊接應使用引弧板;拼板在平台上進行,筒節內縱縫焊接在地面進行;外縱縫利用焊接操作機施焊;也可利用地坑施焊(如下圖),拼板和筒節的外縱縫焊接利用吸附式軌道,自動焊小車要裝配導向器。
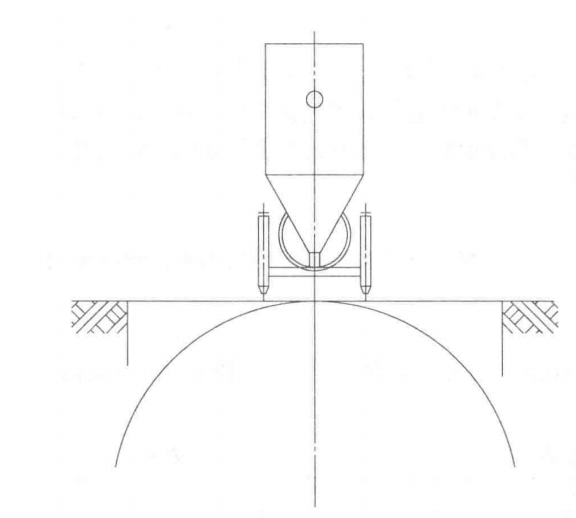
利用地坑焊接筒節外縱縫示意
3)環縫焊接
環縫焊接在焊接滾輪架上進行,先焊內環縫後焊外環縫。內側焊縫焊接時,宜先進行焊嘴與焊縫對正,然後再進行焊接,焊接時,應有人員注意外側觀察焊縫熔深情況;焊接外環縫前磨平定位焊縫。施焊前以裝配縫為基準,安裝好吸附式軌道。調整好焊接滾輪架滾輪轉數使筒體轉動的線速度與小車運動速度相同。焊接時自動焊小車應處於水平位置。焊嘴應偏離筒體中心線10~20毫米,位置在筒體旋轉的反方向(如下圖)。
焊接開始,自動焊小車與滾輪同時運動,自動焊小車運動方向與筒體旋轉方向相反速度相同,使自動焊小車始終處於水平位置。
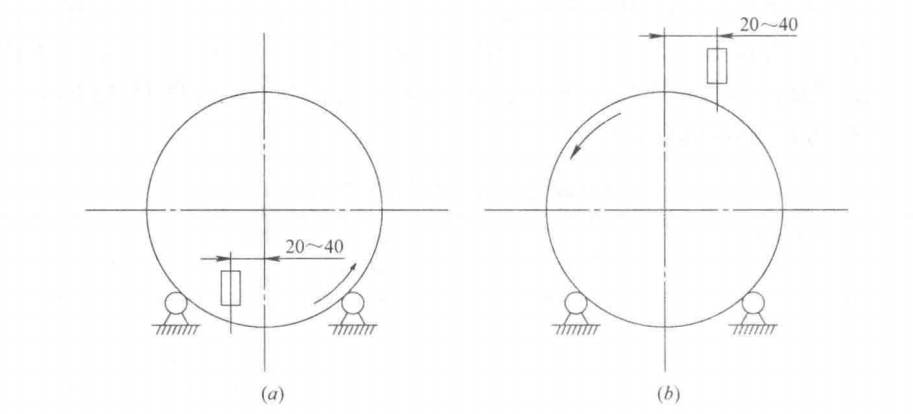
環縫焊接:(a)內環縫焊接;b)外環縫焊接
5)底盤焊接
當底盤厚度允許採用懸空雙面自動埋弧焊接工藝焊接時應儘量採用。底板與基礎圈焊接時可用下圖所示方法進行。
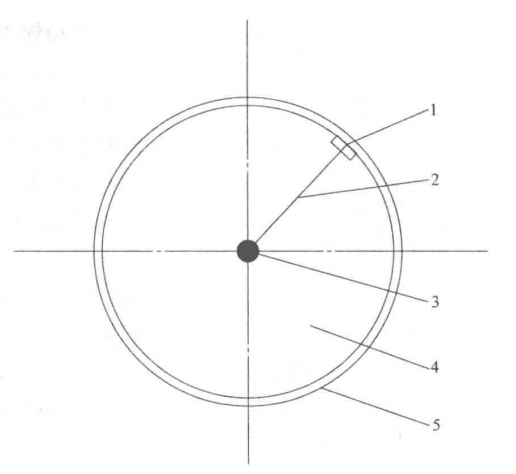
底盤焊接
上圖注釋:1-自動焊小車;2-定位桿;3-滾動軸定心器;4-底板;5-基礎圈
下圖為焦化廠氨洗塔現場製造施工計畫,僅以該塔為例,其他四台均有施工計畫,這裡不用逐一划出。
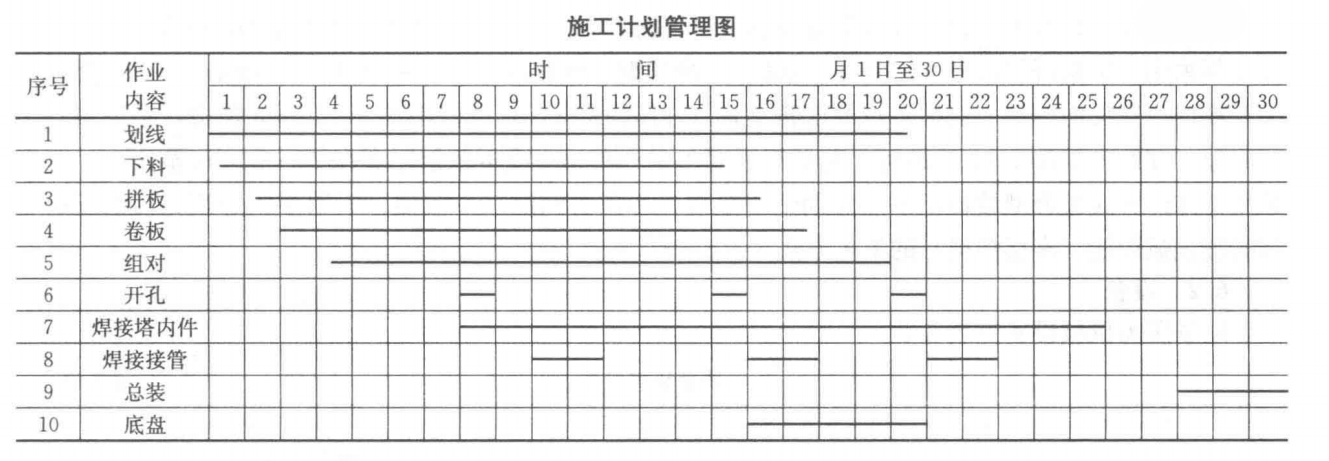
施工計畫管理
現場場地應平整、無積水、有足夠的面積供焊接設備使用。場地應安置龍門吊,焊接滾輪架等機械;有堆放鋼材和足夠的拼板場地。場地布置應有利於流水作業,最好能將大件都控制在龍門吊的工作範圍以內。理想的施工總平面布置見下圖。

施工總平面布置圖
上表注釋:1.龍門吊;2.半自動氣割機;3.直流弧焊機;4.埋弧自動焊機;5.軌道;6.卷板機;7.焊接滾輪架;8.防風工作檯
操作要點
1.埋弧自動焊機要有自己單獨的電源,以避免電壓波動,影響焊接質量。
2.裝配間隙要確保小於1毫米。
3.要儘量放置裝配縫焊前生鏽和進入顆粒狀砂土等雜物,如有鏽蝕及灰塵應設法清除。
4.吸附軌道安置時不得用手錘直接敲打,一以免破壞軌道精度。施焊前應認真檢查導向裝置;調整好導向裝置與軌道間隙。
5.防風工作檯
在現場只焊接同一種直徑的設備,防風工作檯可不帶升降機構,但應能沿軌道移動並能牢固定作台底部應略高於筒體外圓的最高點,在平台底部開長方形孔,以便自動焊小車在筒體位。工上施焊。防風工作棚內應具有擺放焊劑回收機、自動焊小車及其他工具的位置,並有可供四人操作的空間。防風工作棚的行走輪可採用鋼板焊接。防風工作檯支腳要有足夠的強度和剛度。
6.自動焊小車與半自動氣割小車的導向裝置
1)軌道
自動焊小車可採用兩種軌道:即吸附F型和吸附柔性軌道。吸附F型軌道小車在軌道上運行。吸附柔性軌道小車在筒體上運行。吸附F型軌道式軌道的優點是:軌道僅有四點與筒體接觸,焊接環縫時小車運行不受筒體縱焊縫的影響(如下圖所示)。
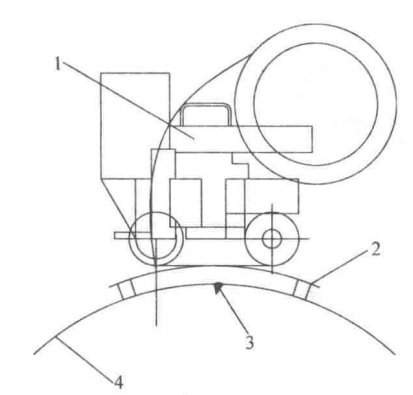
軌道圖
上圖注釋:1-自動焊小車;2-吸附F型軌道;3-筒體縱焊縫;4-筒體
吸附柔性軌道的優點是:輕便、精確適應面廣,一條軌道可以用於各種直徑的筒體內外環縫及縱縫的焊接上。缺點是焊接內外焊縫時自動焊小車,車輪在筒體上運行經過筒體縱焊道時小車產生一定的起伏;但這種起伏由於埋弧自動焊自身的調節功能的作用,沒有影響到焊接質量。
2)導向輪
導向輪可用兩組或四組兩面密封的微型滾動軸承代替。
材料設備
材料
《套用懸空雙面埋弧自動焊工藝焊接大型容器工法》所用材料為碳鋼、低合金高強鋼、耐熱鋼、不鏽鋼等,筒體直徑不小於1米的容器對接焊縫可全部採用,碳鋼板厚度在8-20毫米或低合金高強鋼、耐熱鋼、不鏽鋼厚度在8~16毫米對接焊縫中,不開坡口、正反面各焊一遍即可;厚度再增加4~10毫米時,可以採用留8~10毫米鈍邊,小坡口、不留間隙,雙面各焊接1~2遍即可;普低鋼厚度在30~60毫米或不鏽鋼厚度在20~60毫米範圍內,可以採用特殊的台式組合型坡口,不加焊劑墊或墊板、不預留間隙、不清根、不用手工焊填充、正反面全部實現埋弧焊接(多層焊接)的工藝方法。
設備
現場所需機械設備見下表。
質量控制
《套用懸空雙面埋弧自動焊工藝焊接大型容器工法》的質量控制要求如下:
1.規範標準
焊接工藝評定的試件尺寸、試驗項目及合格標準等,必須按照《鋼製壓力容器焊接工藝評定》JB4708-2000的規定執行。
2.執行廠質量目標,無損檢測一次合格率不低於90%。
3.技術措施和管理措施施工中要嚴格遵守該工法所制定的工序流程,施工前要認真檢查機械化和工裝,發現問題及時解決。設備製造的全過程按照全面質量管理的要求開展自檢互檢和質量分析活動,不合乎要求的工件不得進入下道工序。焊縫按要求進行射線探傷。需要返修的的部位返修前應作焊接返修工藝卡,返修工作由合格的焊工擔任。
檢查員重點對進入捲筒前的板料尺寸和組對間隙進行嚴格檢查。檢驗標準見下表。檢驗工具:支線度、平面度,組對間隙採用塞尺和直尺,其他項目使用鋼板尺和鋼捲尺。
序號 | 工序 | 檢驗控制內容 | 允許偏差毫米 |
---|
| | | |
| | | |
| | | |
| | | |
| | | <1 壁厚S<10時小於1/5S S>10時小於1/10S+1 |
| | | |
| | | |
4.組織保障(見下表)
5.對人員要求
1)使用埋弧焊機操作的焊工必須經過培訓,經考核合格取得相應合格證書、方可從事焊接工作。
2)焊工應了解埋弧焊機的結構和工作原理,能處理簡單的機械故障。
3)焊工應懂得焊絲、焊劑的保存方法,能正確選擇焊絲、焊劑等有關方面知識。
維修電工必須具有修理埋弧自動焊機的能力。對自動焊機的電器故障能及時排除。
安全措施
使用《套用懸空雙面埋弧自動焊工藝焊接大型容器工法》施工時,除應執行國家、地方的各項安全施工的規定外,尚應遵守注意下列事項:
1. 電焊工和氣焊工作業必須符合《焊接與切割安全》GB9448-99中有關規定。
2.要設計好防風工作檯,底部開孔應即方便作業,作業時不得有掉下一人的孔隙。
3.在防風工作檯作業應逐一拴好小工具,以免工具從防風工作檯底孔隙處落下傷害人或工具。
4.安裝漏電保護器,確保用電安全。
環保措施
採用《套用懸空雙面埋弧自動焊工藝焊接大型容器工法》應採取以下環保措施:
1.按照國家和地方政府下發的有關環境保護的法律、法規和規章制度,成立健全的生產環境管理組織機構,在工程施工過程中嚴格遵守加強對工程材料、設備、生產生活垃圾、棄渣的控制和治理,遵守有防火及廢棄物處理的規章制度,充分滿足職工的要求,隨時接受相關單位的監督檢查。
2.環保工作以主管領導做起,抓好現場的宣傳,創辦了環保教育宣傳欄,使職工生動活潑,直觀加深環保印象,提高環保意識,要求操作者強化環保意識,端正環保態度,恪守崗位職責,精通崗位技能,懂得環保法規,掌握操作標準。
效益分析
中油吉林化建工程有限公司根據為包鋼焦化廠製造的五台洗滌塔的成本分析結果:採用《套用懸空雙面埋弧自動焊工藝焊接大型容器工法》與傳統工法比較,除了多一套造價不足2000元的工裝外,其他費用都有大幅度下降。
1.用焊絲和焊劑比用焊條成本降低75%左右。
2.碳棒消耗降低98%以上。
3.砂輪片消耗降低95%以上。
4.板材下料氣割總成本降低30%以上。
1.焊機台板費用降低85%左右。
2.坡口切割機費用降低100%。
1.所用焊工人數減少75%,焊接速度提高2倍,工人費降低80%以上。
2.總焊接成本降低80%左右。
註:施工費用以2007-2008年施工材料價格計算
套用實例
《套用懸空雙面埋弧自動焊工藝焊接大型容器工法》套用實例如下:
該工法自1994年創立以來,懸空雙面埋弧焊工藝不斷完善和創新,已經成為化建設備製造公司廠內壓力容器預製和現場大型容器對接焊縫的主要工藝方法,由於效率高,質量好,產品加工能力和市場不斷擴大,2005年生產了500多台容器設備。
1994年4月中油吉林化建工程股份有限公司設備製造公司承制的包鋼焦化廠五台洗滌塔,筒體焊接是1995年8月開始的,並採用此工法施工。焊道總長2422.5米,20%探傷檢查、拍1938張片,1880張合格,合格率為97%。筒體焊接工作於1995年11月完成。
設備製造公司為吉化煉油廠製作的“重整液氣提塔”,1995年10月10日開工,1995年11月20日交工,該塔內徑1.8米,高為35.297米,材質16MnR,厚度14毫米,焊縫總長160米,25%探傷。採用該工法施工,探傷結果Ⅰ級片110張,Ⅱ級片28張,Ⅲ級片9張,探傷合格率為100%。
中油吉林化建工程股份有限公司設備製造公司為吉化30萬噸乙烯工程製作“產品淨化倉”。該塔直徑4600毫米,高31485毫米,材質16MnR,厚度12毫米,採用該工法施工,焊縫總長291米,53%探傷檢查。共拍618張片,其Ⅰ級片462張,Ⅱ級片146張,Ⅲ級片5張,返修5張,合格率為99.2%。
本廠廠內焊接壁厚不大於22毫米的低碳鋼與壁厚不大於16毫米的低合金鋼設備筒體也全部採用懸空雙面埋弧自動焊工藝,全年工為吉化30萬噸乙烯工程及吉化其他工廠製造大小容器21台,焊接焊縫量達3375米,降低費用181.206萬元,加上包鋼五台洗滌塔降低費用130.066萬元,1995年度採用本工藝共降低費用約為311.272萬元。
2006年,吉林燃料乙醇項目2號不鏽鋼精塔,直徑3米、高39米、筒體厚度16毫米和18毫米,全部採用了雙面懸弧自動焊新工藝,無間隙組對,不用手工填充和氣刨清根,無焊劑托墊,雙面各焊接一遍,外觀成型良好,焊縫接頭的抗晶間腐蝕試驗符合國家標準。簡化了工序,不鏽鋼焊接一次合格率100%,焊接效率提高了10倍,縮短工期50d,節約焊接材料成本超過30%,減少人員投入16人,節約焊接施工成本14.4萬元。自動新工藝的成功套用,不僅保證了工期,而且提高了產品焊接一次合格率。自動焊接新工藝的套用也將提高設備製造公司的生產加工能力。成本的降低、效率和質量的提高將大幅度提高公司在設備製造市場中的競爭能力。
2007年大慶中藍石化40萬噸/年重油催化裂化裝置技術改造工程乙烯脫CO2罐,直徑3米,長度7米,材質16MnR厚度44毫米,低合金鋼焊接一次合格率100%。
2007年,吉化集團公司33萬噸/年丙烯臘裝置擴建項目回收塔,該塔直徑5.6米、高68米、重373噸,材質為16MnR和16MnR+00Cr19Ni10,板厚分別為14毫米、16毫米、18毫米、20毫米、28毫米和20+3毫米,設備要求100%射線探傷,把埋弧自動焊技術成功套用於超限塔器的現場製作,提高了產品的質量,整台塔探傷片數1420張,返修43張,一次探傷合格率近97%,施工工期提前了20天,受到甲方的高度讚譽,很多同行廠家到現場參觀學習。
2008年,遼寧華錦集團乙烯改擴建工程30萬噸/年高密度聚乙烯裝置氧化鋁處理罐,62毫米厚低溫鋼焊接一次合格率100%,受到業主和監理公司的良好評價。
2008年撫順石化原油集中加工、煉油結構調整技術改造工程焦化聯合裝置240×104延遲焦化裝置焦炭塔。塔體直徑9.8米,高37米,材質UCr1MoR鋼板,此鋼種是中油吉林化建工程股份有限公司第一次接觸,在中國未見此設備採用埋孤自動焊接工藝,又一次將埋孤自動焊工藝成功套用於超限設備現場焊接。
2008年,遼寧華錦集團乙烯改擴建工程30萬噸/年高密度聚乙烯裝置氧化鋁洗滌器,直徑2.3米,長度9.4米,厚度62毫米,材質為09MnNiDR,低溫鋼焊接一次合格率100%,受到業主和監理公司的良好評價。
榮譽表彰
2009年10月19日,中華人民共和國住房和城鄉建設部發布《關於公布2007-2008年度國家級工法的通知》,以文號建質[2009]162號公布《套用懸空雙面埋弧自動焊工藝焊接大型容器工法》為2007-2008年度升級版國家一級工法。