基本介紹
- 中文名:
- 工法編號:
- 完成單位:
- 主要完成人:
- 套用實例:
- 主要榮譽:
形成原因,工法特點,操作原理,適用範圍,工藝原理,施工工藝,材料設備,質量控制,安全措施,環保措施,效益分析,套用實例,榮譽表彰,
2.爐殼板全部使用數控火焰切割機進行切割,根據噴粉時的切割程式進行切割,對不要切割的部位在CAD中刪除,重新形成切割語言進行火焰切割。爐殼板厚在50~100毫米。割嘴選擇6號以上,切割時控制割嘴的行走速度。氣割表面精度按表1執行,氣割的誤差控制按表2執行。
項目 | 主要構件 | 次要構件 | |
表面粗糙度 | 50S以下 | 100S以下 | |
凹陷深度 | 不得有缺口凹陷 | 在1毫米以下 | |
溶渣 | 可有塊狀溶渣散布,但不得留有痕跡或易剝離 | ||
上緣溶化 | 略成圓形,但須平滑 |
項目 | 允許偏差 | ||
零件的寬度和長度 | ±1.5毫米 | ||
切割面不垂直度 | 0.05噸,且≤2.0毫米 |
切割後爐殼鋼板的尺寸極限偏差為±2毫米,兩對角線長度之差不大於3毫米,並應考慮留有焊接收縮餘量。
3.爐殼坡口均採用火焰進行切割,橫縫坡口採用裝有導向裝置的半自動火焰切割機切割,豎縫坡口在餘量切割後採用軟軌切割機切割,對於不同板厚的對接坡口採用1:4的比例進行過渡。
二、爐殼成形
1.爐缸、爐腹、爐腰、爐身段為直段或小錐角段,成形時採用卷板機卷製成形。卷制時先進行預彎,成形過程中採用立體樣板在檢查線部位進行檢查,當樣板與成形後爐殼間隙最大不大於2毫米視為合格。檢查樣板的長度不得小於1.5米。樣板檢查見圖3。

圖3 樣板檢查示意圖
2.煤氣封罩成形
1)煤氣封罩捕集段∶煤氣封罩捕集段為雙曲面,由於尺寸較大,成形採用鋼板加熱後模壓成形。模具採用鋼板製作,分為上模和下模,內部填充耐高溫的填充料,以減少模具的用鋼量,模具簡圖見圖4。
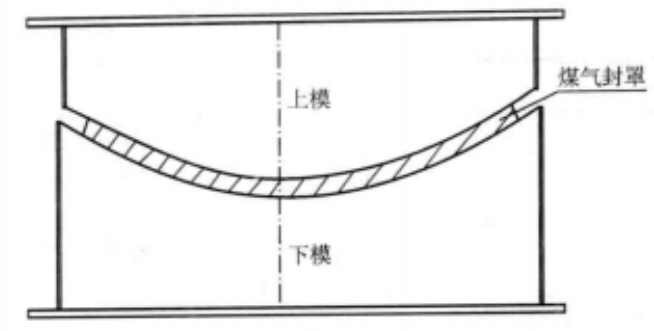
圖4 煤氣封罩模具簡圖
鋼板加熱採用加熱爐加熱,入爐時設有支墊,避免工件直接與爐底接觸。入爐溫度在300~400℃左右,升溫速度控制在100℃/小時以內,加熱溫度升至900~930℃,保溫65~90分鐘,放置於專用模具上壓制。加熱溫度曲線見圖5,成形後用立體模具進行檢查。
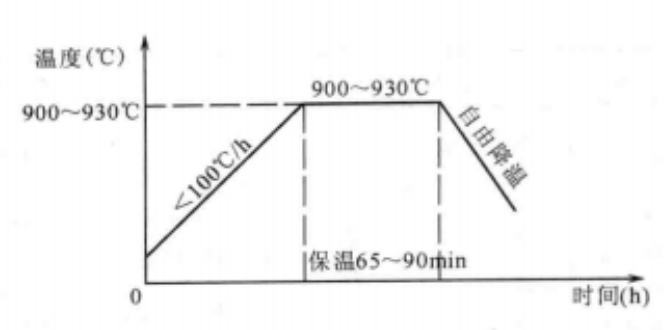
圖5 溫度曲線圖
2)煤氣封罩錐體段;煤氣風罩錐體段成形採用壓力機壓製成形,下料噴粉時噴出壓制線,壓制刀具採用圓型刀具,以防止壓制過程中出現壓痕。
三、爐殼校正
爐殼成形後進行單塊爐殼檢查,在單塊檢查平台上放出落位線,落位畫線半徑比設計圖紙大3毫米彌補豎縫焊接收縮,設定內卡板,上口吊線錘檢查上口圓度,檢查項目見表3,變形部位局部火焰校正,劃好餘量切割線。單塊檢查見圖6。校正後的爐殼容許偏差見表3。
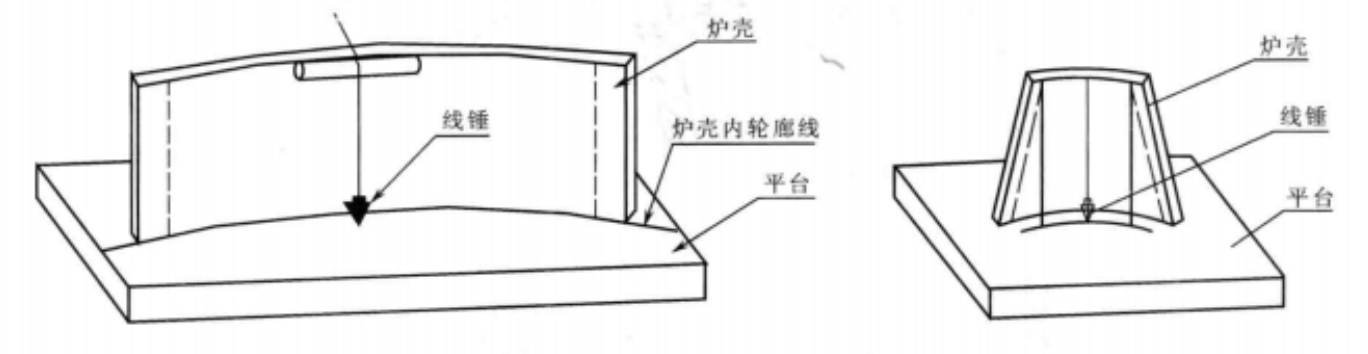
圖6 單塊爐殼檢查示意圖
序號 | 檢查項目 | 允許極限偏差允差(毫米) |
1 | 爐殼弧長 | ≤3 |
2 | 下口與平台間隙 | ≤2 |
3 | 上、下口圓弧 | ≤2 |
4 | 上口高度 | ≤3 |
5 | 爐殼垂直 | ≤3 |
四、爐殼制孔
高爐爐殼由於工藝要求爐身分布著各種孔洞,有冷卻壁水管孔、螺栓孔、灌漿孔、測溫孔、測壓孔、保護板吊掛孔等20多類孔洞,數量達萬個以上,需要進行詳細的計算和施工圖設計,以保證材料的定購和爐殼的製造。
對各種孔洞的制孔分為二種方法進行∶第一種是平板狀態下制孔然後輥壓成形;第二種是輥壓成形後再制孔。圖7為典型孔洞形式圖,針對不同的孔洞形式,制孔方法見表4。
序號 | 孔洞形式 | 孔洞名稱 | 制孔 |
形式1 | 孔方向垂直爐壁中心線交於爐中心 | 螺栓孔、測壓孔、灌漿孔、十字測溫孔 | 先平板狀態下火焰制孔,後爐殼成形。十字測溫孔成形後開孔,≤50毫米的孔機械制孔 |
形式2 | 孔方向平行於地面中心線平行冷卻壁中心 | 冷卻壁單水管孔、雙管型冷卻壁水管孔 | 直筒段平板狀態下火焰制孔,錐體段成形後制孔,採用具有角度調節裝置的切割設備進行火焰切制 |
形式3 | 平行於地面中心線交於爐中心 | 鐵口孔、風口孔、測溫孔、煤氣取樣氣孔、冷卻板孔 | 風口孔、鐵口孔和煤氣取樣孔在爐殼成形後,立式制孔,其餘平板狀況下平板火焰制孔 |
形式4 | 與爐壁成一定角度中心線交於爐中心 | 保護板吊掛孔 | 平板狀態下火焰制孔,採用具有角度調節裝置的切割設備進行火焰切割 |
形式5 | 煤氣封罩孔洞 | 爐頂點火孔、導出管孔、氮氣孔、蒸汽孔、爐頂灑水孔、爐頂溫度計孔、紅外線攝像裝置孔 | 爐殼成型後組裝,在組裝狀態下制孔 |
形式6 | 工廠拼縫周圍50毫米內或跨帶孔 | ╱ | 爐殼成型後組裝,焊接完後,在組裝狀態下制孔 |
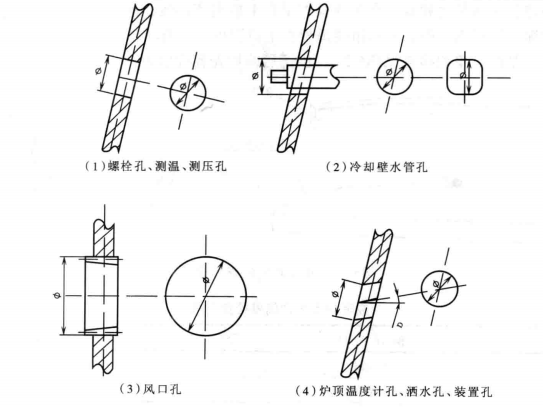
圖7 典型孔洞形式
1.平板狀態下制孔∶爐殼直段上的冷卻壁水管孔包括螺栓孔、灌漿孔、測溫孔、測壓孔,對此類孔採用平板制孔。採用平板制孔的孔特點∶
1)孔徑不大,平板制孔後再成型孔徑變化較小。
2)除保護板吊掛孔及冷卻壁水管孔外,其他孔的孔中心線均垂直於其所在的爐帶。
3)螺栓孔、灌漿孔、測溫孔、測壓孔等孔中心線交於爐心。
4)冷卻壁中心線交於爐心,冷卻壁上水管孔平行於冷卻壁中心線。冷卻壁水管平行於地面。
板材在成型前平板制孔,然後再卷板,板材在卷板過程中會出現板材中性層向外擴展,中性層向內收縮的情況,擴展和收縮量根據孔洞大小和板材成型後的曲率大小不同變化。但高爐爐殼半徑很大,可以視板厚中心為中性層。平板狀態下的開孔因板厚造成成形後板內、外壁尺寸不同,ф50毫米左右的孔洞孔徑變化只有0.3毫米,可以按設計尺寸制孔,對於十字測溫孔、冷卻壁水管孔、冷卻板孔、保護板吊掛孔等需要計算放大進行包絡,圖8為平板狀態下制孔後的內外壁變化,圖9為孔中心平行於爐中心孔徑計算簡圖。
2.成型後制孔工藝
1)對開孔中心不垂直於爐殼鋼板的水管孔等採用具有角度調節裝置的小池火焰切割機進行切割。
2)對於風口、鐵口、煤氣導出管孔由於開孔尺寸大,精度要求高,制孔時採用自主開發的吸附式雷射跟蹤火焰切割機切割。
五、爐殼風口段加工
1.風口大套裝配
風口大套加工時要求內外口機加平行,兩口徑同心,並在與中套接觸面預留二次加工餘量,將內口內半徑縮小15毫米作為焊接熱處理變形的加工餘量,並在大套內外口做好四芯標記,見圖10。風口大套裝配前在鋼平台上進行放樣,放出1/8風口段及各大套在平台上的投影,打上樣沖標記,便於大套裝配時進行定位檢查。
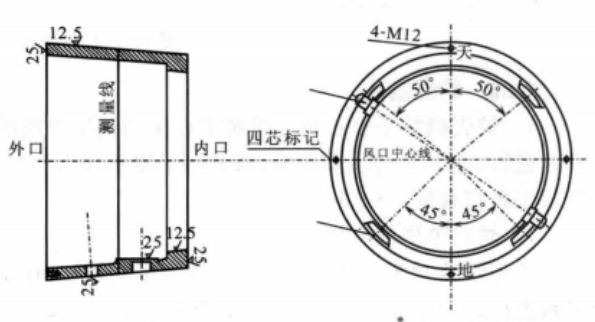
圖10 風口大套四芯標記
大套和法蘭進廠後檢查四芯線,採用專用吊板進行大套和法蘭的裝配,大套裝配過程見圖11,大套送入風口大套孔後用導鏈調平,法蘭的裝配方法與大套相同。
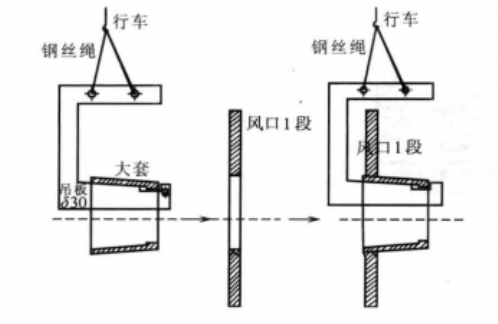
圖11 大套裝配
裝面配時與風口帶大套制孔四芯線對準,通過全站儀測定大套中心的安裝高度和角度,利用角度調節板調整大套安裝角度,高度調節板調節大套組裝高度,調整合格後,調整板間焊接固定,大套與風口帶點焊固定。調整及加固見圖12。
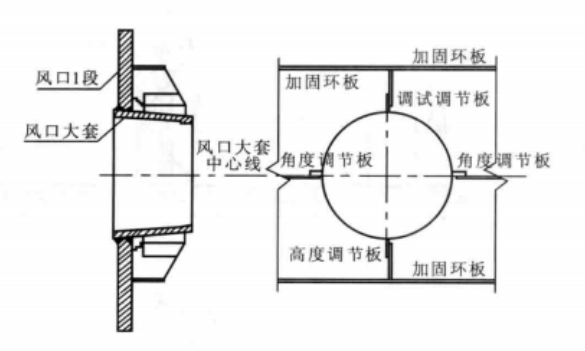
圖12 風口大套調節及加固簡圖
2.大套二次加工定位
爐殼組裝調整結束後在中央測量架上放置全站儀,確定大套二次機加工的準確位置,按照測量結果重新設定大套內口四芯線,做好樣沖標記,並用劃規畫出機加線,採用三維雷射動態跟蹤儀進行覆核,見圖13。
大套機加工時,以爐殼上的高度基準線為參照線將風口1段找平,爐殼垂直放置,固定在數控落地鏜銑床操作台上,爐殼與操作台間設定放傾斜裝置,防止加工過程中顫動或傾倒。調整中間大套中心線與鏜銑軸平行,通過數控系統進行調整動力頭,加工大套連線面,加工過程中注意進刀量,採用多次加工,最後用球墨鑄鐵錐套進行碾磨。一個大套加工完成後,旋轉操作台,使大套中心與鏜銑軸平行依次進行加工。
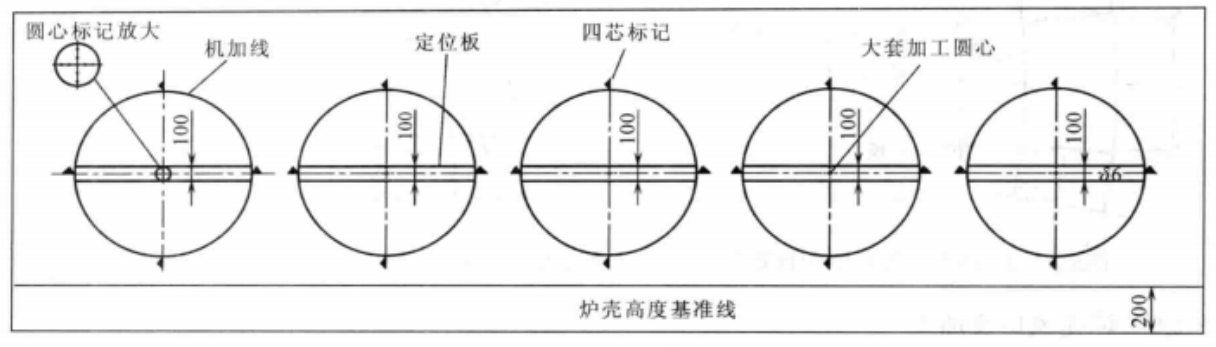
圖13 風口大套劃線定位
六、爐殼組裝
1.爐殼組裝平台:爐殼組裝平台採用鋼平台或鑄鋼平台進行,組裝平台表面超平,整體不平度不得大於2毫米,組裝平檯布置見圖14。
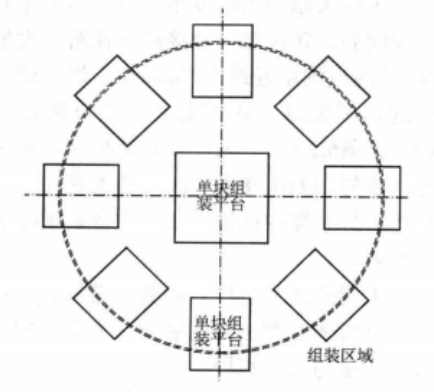
圖14 組裝平檯布置及尺寸
2.爐殼單帶預組裝
爐殼組裝時在組裝平台中心放置測量胎架,在組裝平台上標好爐殼的落位輪廓線、爐殼中心及四芯線。將爐殼按地樣的落位輪廓線,按殼體下料時標記的角度線對照四芯線落位,落位後防止爐殼傾倒,設定臨時支撐。在組裝平台的落位輪廓線兩邊根據每帶爐殼的斜度做好卡板,方便爐殼落位,見圖15。
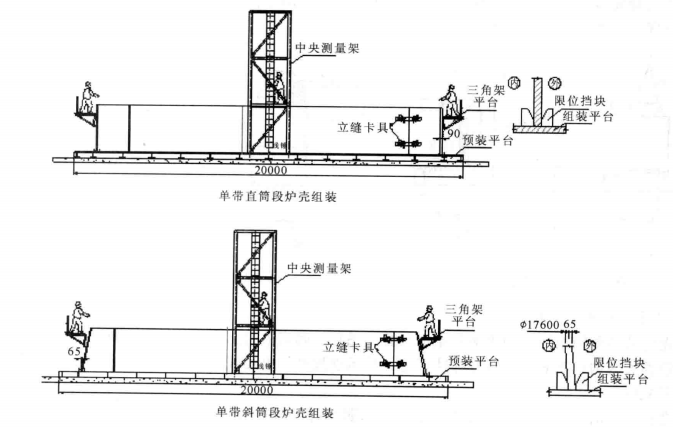
圖15 爐殼單帶組裝示意圖
3.爐殼循環預組裝
為了保證爐殼整體製作精度,爐殼加工完成後進行循環預組裝,方便現場安裝。爐殼多段組裝時,第一段按照單帶組裝的方式先組裝成整圈。然後在下帶的上口焊接限位擋塊。上段爐殼插入限位擋塊中。然後每塊用夾具連線成整圈。最後加上臨時支撐,見圖16。爐殼循環預組裝見下圖17。
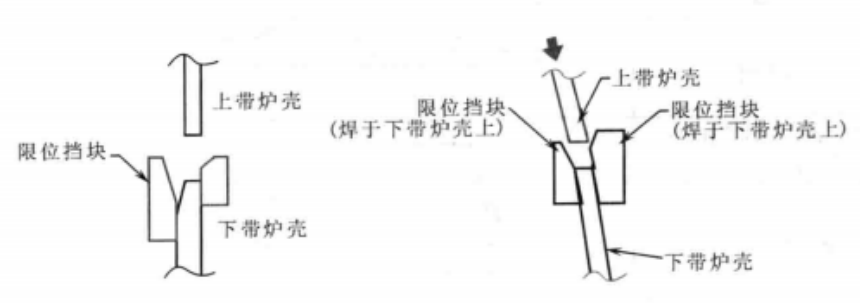
圖16 多段爐殼組裝擋板示意圖
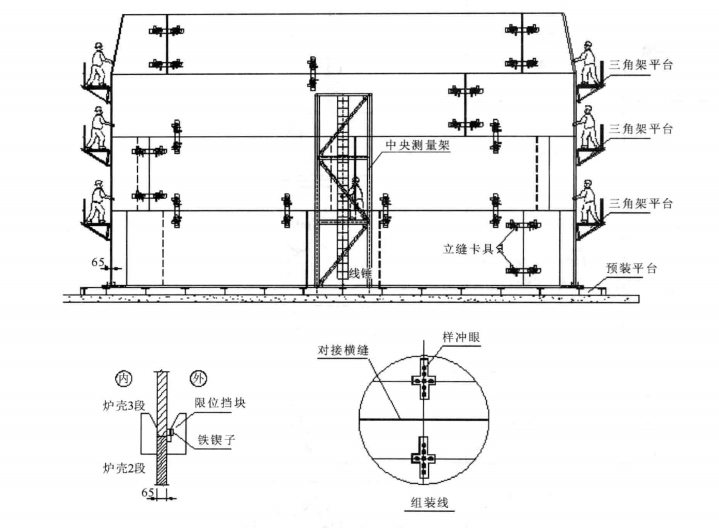
圖17 爐殼循環組裝示意圖
4.爐殼組裝檢查
除調整塊爐殼外,其他爐殼落位後對該帶爐殼進行檢查,檢查項目如下∶
1)爐殼橢圓度的檢查(上下口均分16點);
2)爐殼標高(上下口分均16點);
3)爐殼上口水平度(上下口均分16點);
4)爐殼上下口同心度;
5)爐殼錯邊量(上下口均分16點);
6)爐殼制孔檢查。
爐殼預組裝後尺寸允許偏差見表5。
序號 | 項目 | 簡圖 | 允許偏差(毫米) | |
1 | 爐底板 | 圓度 | ![]() | ▕RMAX-RMIN▏≤R/1000 |
環板平面度 | f1、f2、f3:±1 圓周≤6毫米 | |||
2 | 爐殼上口中心對預裝平台檢查中心的位移 | ![]() | e≤H/1000 且≤5 | |
3 | 爐高殼度 | H≤±5 | ||
4 | 爐殼橢圓度(在圓周16點等分檢查) | ![]() | ▕RMAX-RMIN▏≤2D/1000且≤8 | |
5 | 爐殼上口高低差(在圓周16點等分檢查) | e≤4 | ||
6 | 縱縫 | 錯邊 間隙 | ![]() | t≤40 δ≤3 t>40 δ≤5 S=0~3 |
7 | 橫縫 | 錯邊 間隙 | ![]() | δ≤t/10,但≤5 S=0~3 |
8 | 出鐵口 | 中心標高 | ![]() | h≤±5 |
法蘭面中心位置 | ![]() | Q≤±4‘ | ||
法蘭面水平中心線水平度(在法蘭全寬內) | ≤3 | |||
9 | 風口法蘭 | 法蘭中心標高 | ![]() | h≤±5 |
法蘭中心夾角 | ![]() | Q≤±4‘ | ||
全部法蘭中心高低差 | ![]() | e≤5 | ||
相鄰法蘭中心高低差 | e1≤3 | |||
相對法蘭中心水平連線與爐體中心偏移 | ![]() | e≤10 | ||
法蘭面的向心度 | ![]() | ▕L1-L2▏≤2 | ||
法蘭水平中心線水平度(在法蘭直徑內) | ≤2 | |||
法蘭伸出爐殼表面距離 | ![]() | L≤0~5 | ||
法蘭垂直面的傾斜(在法蘭面直徑內) | e≤±2 | |||
10 | 冷卻板法蘭 | 法蘭沿爐殼圓周中心間隔 | ![]() | E≤±5 |
相鄰兩層法蘭中心距 | F≤±5 | |||
法蘭水平中心線兩端至爐殼表面距離 | ![]() | ▕L1-L2▏≤2 | ||
法蘭面垂直度(在法蘭全高內) | e≤2 | |||
11 | 冷卻壁孔 | 同組孔間距 | ![]() | A、B、C、D±2 |
相鄰組孔中心距 | M、N±3 | |||
12 | 爐頂法蘭 | 圓度 | ![]() | ▕DMAX-DMIN▏≤D/1000 |
上平面任意兩點高低差 | ≤3 |
七、爐殼焊接
爐殼用材料根據爐型、廠家、區域不同分為Q235C、O345C、BB503等,表6中給出焊接方法和材料是以某鋼廠5000立方米高爐為參照選用,在製作時焊接材料依據母材來選用。
1.焊接方法及焊接材料
爐殼製作主要焊縫類型、焊接方法及焊接材料選用見表6。
部位 | 母材 | 焊接位置 | 接頭型式 | 焊接方法 | 焊接材料 |
爐殼鋼板拼接 | BB503 | 平焊 | 對接 | 埋弧自動焊 | H10Mn2+SJ101 |
爐殼間立焊 | BB503 | 立焊 | 對接 | CO2氣保焊 | ER50-6 |
絲極電渣焊 | H08MnMoA+HJ431 | ||||
自保護自動立焊 | NR431 | ||||
兩帶爐殼間橫縫 | BB503 | 橫焊 | 對接 | CO2氣保焊 | ER50-6 |
爐底板拼接 | Q235-C | 平焊 | 對接 | 埋弧自動焊 | H08MnA+HJ431 |
爐缸與爐底環板焊接 | BB503 | 橫焊 | T形接頭 | CO2氣保焊或埋弧自動橫焊 | ER50-6或H10Mn2+SJ101 |
爐頂法蘭與爐殼焊接 | BB503 | 橫焊 | T形接頭 | CO2氣保焊 | ER50-6 |
鐵口框與爐殼焊接 | Q345C+BB503 | 平焊 | T形接頭 | CO2氣保焊 | ER50-6 |
風口法蘭與爐殼焊接 | ZG20Mn+BB503 | 平焊 | T形接頭 | CO2氣保焊 | ER50-6 |
各部位 | ╱ | ╱ | ╱ | 手工電弧焊 | E5015 |
2.焊接工藝
1)焊前準備
焊前進行技術和安全交底。
焊前,焊縫坡口及附近20毫米(手工電弧焊、CO2氣體保護焊)或40毫米(自動焊)範圍內清除淨油、銹等污物。
定位焊焊接方法與打底焊相同,焊接要求同正式焊接。定位焊牢固可靠,定位焊不得有裂紋、氣孔、夾渣等缺陷。
施焊前,複查組裝質量、定位焊質量和焊接部位的清理情況,如不符合要求修正合格後方施焊。爐殼裝配質量要求見表7。
部位 | 項目 | 板厚 | 允許偏差 | 備註 |
立焊縫 | 錯邊量 | 1 | ≤3毫米 | ╱ |
橫焊縫 | 錯邊量 | δ≤40毫米 | ≤δ/10,且≤3毫米 | ╱ |
δ>40毫米 | ≤δ10,且≤5毫米 | ╱ |
現場施焊前檢查腳手架等臨時設施是否安全可靠。
預熱∶
(1)對於板厚大於36毫米的BB503鋼板,施焊前進行預熱(自保護立焊除外),預熱溫度為120℃。預熱範圍為焊縫兩側,每側寬度不小於板厚的2倍,且不小於100毫米,預熱測溫點在距焊縫50毫米處。
(2)施焊現場環境溫度低於0℃時,在始焊點附近100毫米範圍內採用火焰預熱30℃以上方可施焊。
2)焊接過程
(1)引弧在焊道內進行,不能在焊道區以外的母材上起弧。
(2)施焊中,應特別注意接頭和收弧的質量,收弧時應將熔池填滿。
(3)多層多道焊時,接頭錯開50毫米以上,並連續施焊。
(4)每一層焊道焊完後及時清理檢查,清除缺陷後再焊。
(5)焊縫出現裂紋時,焊工不得擅自處理,立即上報,由技術人員查清原因、訂出修補工藝後,方可處理。
3)焊後
焊接完畢,焊工及時清理焊縫表面的熔渣及兩側的飛濺物,檢查焊縫外觀質量。檢查合格後在規定部位打上焊工鋼印或做好記錄,利用預熱設備進行消氫處理。橫縫焊完後,立即升溫到250℃,恆溫2.5~3小時,然後緩冷。對於風口大套與風口段,焊後進爐進行熱處理,熱處理曲線見圖18。
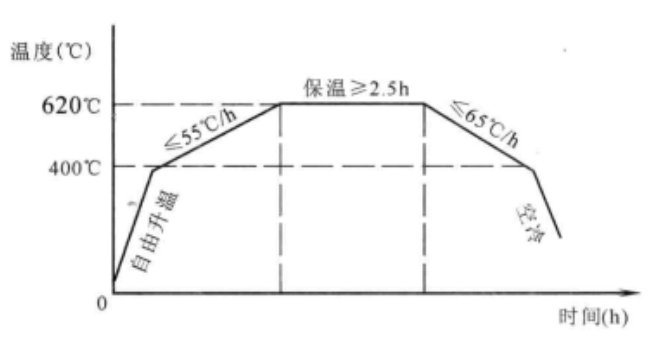
圖18 風口段熱處理曲線
4)焊接參數
(1)手工電弧焊焊接工藝參數見表8。
焊接位置 | 焊接材料 | 焊接工藝參數 | |||
型號 | 規格(毫米) | 電流(安) | 電壓(伏) | 備註 | |
平、橫焊 | J507J507RH | ф3.2 | 110~130 | 22~24 | ╱ |
ф4 | 160~200 | 24~26 | ╱ | ||
ф5 | 220~260 | 24~30 | ╱ | ||
立焊 | J507J507RH | ф3.2 | 100~120 | 22~24 | ╱ |
ф4 | 150~170 | 24~26 | ╱ | ||
ф5 | 160~240 | 26一30 | ╱ |
(2)CO氣體保護焊焊接工藝參數見表9。
焊接方法 | 焊接材料 | 焊接工藝參數 | |||
型號 | 規格(毫米) | 電流(安) | 電壓(伏) | 氣流量(L/分鐘) | |
GMAW | ER50-6 | ф1.2 | 240-260 | 26-28 | 15-20 |
(3)KES法電渣焊工藝參數見表10。
層次 | 焊材牌號 | 焊材規格 | 電流(安) | 電壓(伏 | 備註 |
內側 | H08MnMoA+HJ431 | ф2.4毫米 | 400~450 | 42-44 | ╱ |
外側 | H08MnMoA+HJ431 | ф2.4毫米 | 400~450 | 42~44 | ╱ |
3.焊縫質量檢驗
1)外觀檢驗
焊縫質量檢驗按《煉鐵機械設備工程安裝驗收規範》GB 50372-2006進行,低碳鋼焊接完畢冷卻後即可進行外觀檢查。低合金鋼焊縫焊接完畢24小時後方可進行外觀檢查。
對接焊縫的外觀質量應符合表11中Ⅲ級的規定。
角焊縫的焊角高度應符合設計檔案的規定,其外形應平緩過渡,表面不得有裂縫、氣孔、夾渣等缺陷,咬肉深度不得大於0.5毫米。
項次 | 項目 | 等級(單位∶毫米) | |||
I | II | III | IV | ||
1 | 表面裂紋、表面氣孔、表面夾渣、綜合性飛濺 | 不允許 | 不允許 | ||
2 | ![]() | 深度:e1≤0.5 焊縫兩側咬邊的總長度不大於焊縫全長的10%,且小於 100 | |||
3 | ![]() | e≤1+0.10b且不大於 | e≤1+0.20b且不大於4 | ||
4 | ![]() | 蓋過每邊坡口約2 | |||
5 | ![]() | 不允許 | 不允許 | ||
6 | ![]() | e2≤0.1δ且不大於3 | e2≤0.1δ但: δ≤40時,≤3 δ>40時,≤6 |
2)無損檢測
無損檢測在外觀檢查合格後進行。對接焊縫及熔透T形焊縫內部質量採用超音波探傷,按《承壓設備無損檢測》GB11345執行。合格級別∶B類Ⅱ級。檢測比例∶10%。
材料設備
1.使用的主要材料
《大型高爐爐殼製作工法》使用的主要材料見表12。
名稱 | 型號 | 數量 | 用途 |
CO2氣保焊絲 | ER50-6 | 500千克 | 風口大套焊接 |
鋼板 | -25 | 20噸 | 加固、組裝 |
槽鋼 | 25號 | 50噸 | 加固 |
焊材 | H08MnMoA+HJ431 | 500千克 | 立縫焊接 |
沖子 | ф30 | 100個 | 組裝 |
2.採用的機具設備
《大型高爐爐殼製作工法》採用的主要機具設備見表13。
名稱 | 規格型號 | 數量 | 用途 |
數控切割機 | CSII-6000D | 1 | 用於數控噴粉、下料 |
三輥卷板機 | W11S-100x4500 | 1 | 用於卷板成形 |
壓力機 | 5000噸 | 1 | 用於煤氣封罩成形 |
播壁鑽床 | ZW3725 | 2 | 用於爐殼制孔 |
半自動火焰切割機 | RA6 | 4 | 用於坡口加工 |
可調角度火焰切割機 | LGK-200 | 2 | 用於爐殼制孔 |
電渣焊機 | FABARCESW-2 | 3 | 用於爐殼豎縫焊接 |
吸附式雷射跟蹤大圓切割機 | FABARC | 1 | 用於爐殼制孔 |
全站儀 | WILD-TC702 | 1 | 用於爐殼組裝測量 |
落地鏜銑床 | HCW3-250NC | 1 | 用於風口大套二次機加工 |
參考資料:
質量控制
《大型高爐爐殼製作工法》的質量控制要求如下:
一、質量控制標準
1.《高爐爐殼技術條件》YB/T 4079。
2.《冶金機械設備安裝工程安裝驗收規範》GB 50372。
3.《承壓設備無損檢測》JB 4730。
二、關鍵工序質量要求
1.下料尺寸極限偏差(表14)
項目 | 簡圖 | 極限偏差 |
下料長度L | ![]() | ±2 |
下料寬度L' | ±2 | |
對角線之差▕L1-L2▏ | 3 |
2.爐殼成形質量要求(表15)
序號 | 檢查項目 | 允許極限偏差允差(毫米) |
1 | 爐殼弧長 | ≤3 |
2 | 下口與平台間隙 | ≤2 |
3 | 上、下口圓弧 | ≤2 |
4 | 上口高度 | ≤3 |
5 | 爐殼垂直 | ≤3 |
3.風口法蘭組裝尺寸偏差(表16)
項目 | 簡圖 | 極限偏差 |
風口法蘭中心線角度偏差α平面度 | ![]() | ±4‘ |
風口法蘭伸出爐殼表面距離L | ![]() | 0≤L≤5 |
風口法蘭偏角θ的偏斜邊長偏差L1 | ±2 | |
θ=0時法蘭垂直面傾斜L1 | ≤2 | |
各法蘭中心標高偏差△h | ![]() | ±3 |
相鄰兩法蘭中心高低偏差△h | ≤3 | |
全部法蘭高低差△h | ≤5 | |
風口法蘭不平度△ | ≤2 | |
法蘭面水平中心線與法蘭內圓圓周相 交點A、B至風口同一點距離之差 | ![]() | ▕L1-L2▏≤2 |
4.單體爐殼預裝幾何形狀和尺寸偏差(表17)
項目 | 簡圖 | 極限偏差 | |
爐底板 | 圓底 D:爐底板直徑 | ![]() | ▕DMAX-DMIN▏≤0.02D |
平面度 | ≤4 | ||
單體爐殼 | 上口中心對預裝平台上 檢查中心線的位移H: 預裝高度 | ![]() | ≤H/1000 當H≤3000時 ≤3 當H>3000時 ≤10 |
圓度 Di i=1、2 | ![]() | ▕DMAX-DMIN▏≤0.02Di | |
垂直高度 | ![]() | ±5 | |
上口平面度 | ≤4 | ||
爐頂圈 | 圓度 | ![]() | ▕DMAX-DMIN▏≤D/1000 |
上平面任意兩點高低差 | ≤4 | ||
冷卻板法蘭 | 法蘭沿爐殼圓周中心間隔 | ![]() | E≤±5 |
相鄰兩層法蘭中心距 | F≤±5 | ||
法蘭水平中心線兩端至 爐殼表面距離 | ![]() | ▕L1-L2▏≤2 | |
法蘭面垂直度 | e≤2 | ||
冷卻壁孔 | 同組孔間距 | ![]() | A、B、C、D≤±2 |
相鄰組孔中心距 | M、N≤±3 |
三、質量控制措施
1.建立健全的製造質量保證體系,精心策劃,落實措施,提高質量管理預見性。
2.培訓專業焊工,氣焊工。
3.嚴格工序管理,實行工序流轉制度,下道工序必須在上道工序的檢查合格後方可實施。
4.加工前嚴格按照國家標準和相關協定、契約進行材料的復檢,保證原材料的質量。
5.加工前認真核對爐殼製造詳圖,確認無誤後方可輸入數控切割機進行切割語言的轉換;數控切割機噴粉畫線後對照設計圖進行檢查,以確定製孔、切割的準確性。
6.卷板採用數控卷板和人工檢查相結合的施工方法,卷板前認真檢查成形用樣板、標記清晰,防止使用時混淆。
7.冷卻水管孔、鐵口、風口、煤氣封罩上的各種設備孔採用平板數控噴粉定位、成形後制孔的方法來保證爐殼制孔的質量。
8.焊接式焊接後風口大套採取多次組裝、二次機加工的方式來保證風口段質量。
9.爐殼校正、組對時嚴格檢查組裝地樣和組裝質量,不得強行組對。
10.便於現場安裝,進行循環預組裝,並進行調整,達到爐殼質量精度要求,做好組裝標記。
11.爐殼焊接時按照焊接工藝進行預熱和後熱,風口段採取入爐進行熱處理,消除焊接殘餘應力。
12.爐殼對接焊縫、風口、鐵口、設備接管與爐殼的焊接,嚴格按照《承壓設備無損檢測》的要求進行焊縫的驗收。
13.加工前每道工序對班組做好技術交底,施工過程中嚴格遵守,對質量進行全過程控制。
14.注重細部,精益求精,著力治理質量通病。
15.做好除銹塗裝、成品保護,保證構件外觀質量。
安全措施
採用《大型高爐爐殼製作工法》施工時,除應執行國家、地方的各項安全施工的規定外,尚應遵守注意下列事項:
一、執行的安全標準
1.《起重機械安全規程》GB/T 6067。
2.《建築施工扣件式鋼管腳手架安全技術規範》JGJ 130。
3.《建築施工高處作業安全技術規範》JGJ 80。
4.《建築機械使用安全技術規程》JGJ 33。
二、安全措施
1.認真貫徹"安全第一,預防為主"的方針,根據國家有關規定、條例,結合單位實際情況和工程的具體特點,組成專職安全員和班組兼職安全員以及車間安全用電負責人參加的安全生產管理網路,執行安全生產責任制,明確各級人員的職責,抓好工程的安全生產。
2.在生產前必須逐級進行安全技術交底,並做好記錄,明確安全責任制。嚴格按規定做好開工前、班前安全交底。
3.氧氣瓶與乙炔瓶隔離存放,嚴格保證氧氣瓶不沾染油脂、乙炔發生器有防止回火的安全裝置。
4.電渣焊和埋弧焊焊接、加熱設備應注意用電安全,按規定分線路接線,對於絕緣保護層裸露的線要嚴禁使用。
5.加工機械設備實行進廠驗收掛牌制度,並明確責任人和管理者,做好運行監視記錄。一切加工機械的進場必須符合質量和安全要求,機械進場執行驗收制度,實行人機配套管理。
6.卷板過程中嚴禁操作人員站在鋼板上進行指揮和操作,卷板過程中不得移動卷板機周邊護欄,防止卷板反彈傷人;卷板後緩慢將卷制後的爐殼移出卷板機。
7.爐殼鋼板校正和制孔時採用型鋼與鋼平台進行支撐臨時固定,防止爐殼傾翻。
8.吊耳、掛耳焊接牢固可靠、在掛耳上掛三角架和木挑板作為臨時組裝通道,用細鋼絲繩作為安全帶的掛點,臨時組裝通道使用前由安全員進行確認後方可使用。
9.爐殼組裝、循環組裝時,注意高空作業,佩戴好安全帶,做好防護措施;組裝區域做好安全警戒措施,爐殼吊運時下面不得站人,防止高空落物;爐殼組裝時,採用專用卡具固定牢固後行車方可松鉤,必要時用型鋼進行臨時固定。
10.爐殼在預熱、後熱、焊接過程中注意不要觸摸鋼板、使用紅外線測溫儀監測溫度,防止高溫灼傷。
11.爐殼的倒運,應使用專用吊具,重複使用的吊具在吊裝前嚴格檢查,吊裝時根據理論計算選擇合適吊點,確保吊運安全。
12.煤氣封罩上設備短管的焊接,內部架設排風扇進行通風,指派專人進行監護。
13.各種施工材料要分類有序堆放整齊,對余料注意定期回收,對廢料及時清理,定點設垃圾箱,保持施工現場的清潔整齊。結構運輸倒運必須綁紮牢固,堆放平穩牢靠,防變形,防坍塌傾倒。
環保措施
《大型高爐爐殼製作工法》的環保措施如下:
1.爐殼製作過程中嚴格遵守國家和地方政府下發的有關環境保護的法律、法規和規章,加強對施工燃油、工程材料、設備、廢水、生產生活垃圾、棄渣的控制和治理,遵守有防火及廢棄物處理的規章制度。
2.機械設備必須按相關規定進行保養維修,確保機械設備的消聲設備完好。
3.要做好對機械操作人員的教育培訓,正確使用各類機具,避免因不正確使用發出刺耳的噪聲。
4.成品車間除銹設備等產塵較大的作業必須封閉作業,有效的進行通風和灰塵的回收。
5.加強對作業人員的教育,有塵產生的作業動作要輕、速度要慢。
效益分析
《大型高爐爐殼製作工法》的效益分析是:
大型高爐爐殼製作工法的套用,確保了爐殼的製造質量和製造周期,同時也為爐殼的製造和安裝降低了成本投入。該工法已成功地套用於福建鑫海高爐爐殼、寶鋼一號高爐大修工程高爐爐殼、安鋼集團三號高爐等工程的製造,製造工程量15236噸,完成產值15017.1萬元,取得直接經濟效益1163.8萬元。
大型高爐爐殼製作工法的套用,為中國鋼鐵企業的高爐日趨大容積、高爐壓、自動化和長壽化創造了更多的條件,推動了中國鋼鐵行業的高爐大型化向生產效率高、能源消耗低、鐵水質量高、環境污染少等方面的發展,取得了顯著的社會效益。
註:施工費用以2009-2010年施工材料價格計算
套用實例
《大型高爐爐殼製作工法》已經成功地套用於福建鑫海高爐爐殼、寶鋼一號高爐大修工程高爐爐殼、浙江中天鋼鐵、浦鋼中厚板分公司非標容器、英國風力發電基礎樁和過渡樁卷圓工程、安鋼集團三號高爐等爐體設備工程的製造,實施效果良好。
- 實例1:福建鑫海高爐爐殼
1.套用地點∶福建鑫海;
2.工作量∶約145噸,最大板厚40毫米;
3.起止時間∶2007年7月~2007年9月。
4.套用效果∶爐殼製作質量好,現場組裝方便準確。
- 實例2:寶鋼一號高爐大修工程4966立方米高爐爐殼
1.套用地點∶寶鋼一號高爐大修工程;
2.工作量∶約1381噸,最大板厚100毫米;
3.起止時間∶2007年8月~2008年5月。
4.套用效果∶爐殼製作精度高,尤其是風口段的加工。
- 實例3:浦鋼中厚板分公司非標容器製造
1.套用地點∶中厚板分公司二期COREX煉鐵工程;
2.工作量∶約720噸,最大板厚130毫米;
3.起止時間∶2008年5月~2009年2月。
4.套用效果∶在非標容器類設備的製造中套用高爐爐殼製造技術,簡化了設備的製作工藝,節省了製作成本,且製作質量優良。
- 實例4:英國風力發電站基礎樁和過渡樁卷圓
1.套用地點∶上海振華港機英國海上風力發電卷圓;
2.工作量∶約11132噸,最大板厚85毫米;
3.起止時間∶2009年1月~2009年5月。
4.套用效果∶鋼樁成型、坡口加工質量好,製作周期短,效率高。
- 實例5:浙江中天鋼鐵高爐爐殼
1.套用地點∶浙江常州;
2.工作量∶約508噸,最大板厚50毫米;
3.起止時間∶2009年5月~2009年7月。
4.套用效果∶爐殼的大塊化生產,提高了爐殼的製作質量。
- 實例6:安鋼集團4700立方米高爐爐殼
1.套用地點∶河南安陽;
2.工作量∶約1350噸,最大板厚100毫米;
3.起止時間∶2010年7月~2010年12月。
4.套用效果∶安鋼三號高爐爐殼實現遠距離的大塊化、工廠化生產,套用大型高爐爐殼製作技術既保證了爐殼的製作質量。又安全快速的滿足現場的安裝需要,實現了爐殼的質量、安全生產的目標。
榮譽表彰
2011年9月,中華人民共和國住房和城鄉建設部發布《關於公布2009-2010年度國家級工法的通知》建質[2011]154號,《大型高爐爐殼製作工法》被評定為2009-2010年度國家二級工法。