特點
飛機裝配是將各零件或組合件按產品技術要求相互準確定位,並用規定的連線方法裝配成部件或產品的過程。受結構特點和結構剛性等因素影響,在飛機裝配中大量採用鉚接和螺接等連線手段,同時,為了保證裝配協調及外形準確度要求,並保證裝配過程中組件、部件具有一定的結構剛度,飛機裝配巾採用了大量的結構複雜、準確度高的裝配型架這一切均顯示出,與一般機械產品的裝配過程相比,飛機裝配具有非常顯著的特點。
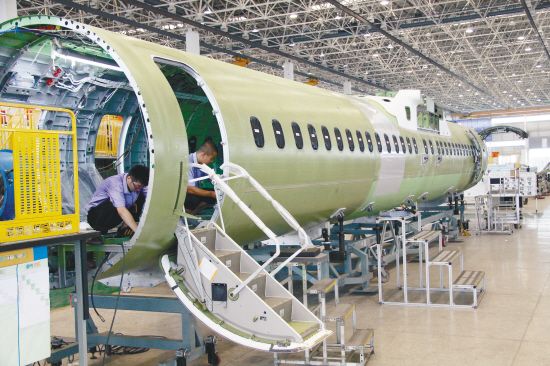
(1)產品幾何定義與協調方法
由於飛機零件形狀複雜,難以在二維圖樣上用尺寸描述零件的尺寸和形狀,長期以來一直用模線樣板的方式進行飛機產品的幾何定義。隨著計算機技術的發展,20世紀70年代產生了計算機輔助設訓+製造技術,飛機的幾何尺寸與形狀定義採用了以B樣條等函式構建的三維線架結構,使模線由人工繪製變為由繪圖機自動繪製。複雜的機械加工可以利用零件的數模進行編程,實現數控加工。直到20世紀90年代,以波音、空客為代表的三維數位化設計製造技術套用,徹底改變了飛機設計製造模式。
(2)裝配工藝裝備的特點與作用
飛機結構不同於一般機械產品,在它的裝配過程中,不能僅僅依靠零件自身形狀與尺寸的加工精度來保證裝配出合格的組、部件。因此,除了採用各種通用工具機、常用工具和試驗設備以外,還需針對不同機型的組件及部件,制定專門的裝配工藝裝備,如裝配型架、對合型架、精加工型架、壁板裝配夾具等。這些專用的生產裝備用於完成飛機產品從零組件到部件的裝配以及總裝配過程,一般尺寸較大的稱為裝配型架,而尺寸較小的稱為裝配夾具,二者不存在嚴格、明確的界限。
裝配工裝的主要功用有如下幾點:①定位夾緊,保證產品的尺寸、形狀和零件問相對位置的準確性。②確保產品滿足準確度和協調互換的要求,在一般機械製造中,保證產品互換性主要是通過公差、配合制度和通用量具來實現,而飛機製造中則是通過相互協調的裝配工裝來實現。③保持尺寸形狀穩定性,飛機結構中存在大量鈑金件,其尺寸大而剛性小,所以無論是鉚接還是焊接.在連線時都會產生不同程度的變形,而裝配能夠確保鈑金件及其組合件的形狀,控制裝配過程的變形。④改善裝配過程的勞動條件,提高勞動生產率,降低成本。
在批生產中,一個部件的裝配往往需要用一套具有多種功能的工裝完成全部的裝配工作,如骨架裝配夾具、總裝型架、架外補鉚型架等。這種情況下,每個工裝必須與裝配過程前後相關的工裝相互協調,同時還需要與相關的零件工裝協調。
(3)裝配連線方式
飛機的機體結構由上萬項零件組成,連線方式以鉚接為主。鉚接的優點是連線強度穩定可靠,易於檢查和排除故障,能適應較複雜的結構和不同材料之間的連線且操作技術簡便易行。但是鉚接也存在自身的缺點,主要表現在:鉚縫應力分布不均勻;手工勞動量大,生產效率低;鉚接質量受人為因素影響較大,不易控制。
為了解決人工鑽鉚所出現的問題,能夠完成定孔位、制孔、送釘、施鉚全過程的自動鑽鉚設備開始出現。隨著數控技術的發展,自動鑽鉚技術日益成熟,小現了不同結構形式的自動制孔設備和與其配套的自動調平托架。自動鑽鉚設備本身比較龐大。與人工鉚接相比其靈活性較差,因此適合鉚接工作面開敞的部組件,常用於大型飛機鉚接裝配。對於戰鬥機中空間狹小且鉚接部位形狀複雜的裝配件而言,其套用受到了一定的限制。為此,目前又出現了各種類型的自動制孔設備,如機器人自動制孔設備、五坐標自動制孔設備等。
發展趨勢
從20世紀50年代以來,數位化技術在國外
航空工業中的套用,經歷了從數位化技術的單項套用。到數位化系統集成套用,再到數位化協同設計製造和產品全壽命周期數據管理的發展歷程。以波音公司為例,波音公司在20世紀90年代研製
波音777飛機的過程中已全面實施了產品數位化設計,該型飛機作為世界上第一種全數位化定義和無紙化生產的飛機.是飛機製造業全面套用數位化技術的里程碑。歐洲的空客公司也建立了多地區、多製造廠之問的飛機異地協同數位化設計製造及管理體系.為空中“巨無霸”飛機A380的成功研製提供了堅實的數位化技術套用基礎。
目前,飛機數位化設計製造技術已在波音、洛克希德·馬丁、空客等公司的飛機研製過程中廣泛套用,先進飛機設計製造技術以全面採用數位化產品定義、產品數據管理、並行工程和虛擬製造技術為主要標誌,從根本上改變了飛機傳統的設計製造方式,大幅度提高了製造技術水平,並取得了良好的效益、例如,空客公司採用虛擬製造技術,將其新機試製周期從4年縮短為2.5年,顯著降低了研製費用及生產成本。
飛機數位化裝配技術興起於20世紀80年代後期.並在西方航空工業已開發國家獲得了迅速發展,數位化裝配技術集成了工業界各領域最先進的科技成果,如數位化技術、
虛擬現實技術、雷射跟蹤定位技術、自動控制技術等,它已經完全不同於傳統的飛機裝配技術。現代飛機數位化裝配技術以
自動化、數位化、柔性化與信息化為特點,顯著提高了飛機裝配質量和效率,同時也提高了飛機的疲勞壽命。
目前,波音公司和空客公司代表了全球航空製造業的最先進水平,其數位化裝配技術體系已逐漸成熟。在波音777/787飛機、空客A380飛機等的研製過程中,機身部件的裝配均已採用數位化裝配技術.同時.為適應飛機數位化裝配技術發展的要求,國外相關的沒備製造公司與飛機製造公司合作。不斷在數位化裝配技術及裝備方面進行探索研究。在各種新機型研製過程中,飛機數位化裝配技術也在不斷向前發展。
準確度
飛機機體的裝配準確度.直接影響到飛機的使用性能以及生產的互換性,因此保證飛機機體的裝配準確度,是飛機裝配工作的主要任務。對於飛機機體裝配準確度的要求主要包括下述幾方面。
外形準確度
(1)外形要求。
對於不同類型的飛機.其要求是不同的。對於外形準確度,翼面部件比機身部件要求高,部件最大剖面之前比最大剖面之後要求高。
高速殲擊機允許的
翼面展向波紋度不大於0.5/400。由於機翼一般為單曲度部件,可用直尺沿等百分比(如5%,10%,15%,20%,40%,60%和80%)弦線處進行檢查。
因為要檢查出外形的正向誤差,所以必須使用等距樣板。當要檢查各截面間的相對扭轉和相對位移時,則必須用部件檢驗型架或在裝配型架上安裝檢驗卡板(即各截面的等距檢驗卡板)進行檢驗。這時檢驗出的外形誤差是外形的綜合誤差。
(2)表面平滑度要求。
表面不平滑誤差包括
鉚釘、螺釘、焊點處的局部凸凹缺陷,蒙皮對縫間隙和階差等。蒙皮對縫間隙允許值是按平行和垂直氣流方向分別規定的.對縫階差允許值是按順氣流和逆氣流方向分別規定的。對結構比較複雜、難以保證精密配合的部位,則根據具體情況制定允許值。例如,對於“三叉載”型客機的乘客艙門與周圍機身配合處,允許的間隙:上部為7.0±1.9mm,側部為4.4±1.9mm,下部為3.8±2.5mm;允許與機身的階差要求:凸出為2.5mm,凹進為5.0mm。
位置準確度
部件內部組合件和零件的位置準確度是對基準軸線的位置要求,如大梁軸線、翼肋軸線、隔框軸線、長桁軸線等的實際裝配位置相對於理論軸線的位置偏差。一般規定梁軸線允許的位置偏差和不平度範圍為±0.5~±1.0mm,普通肋軸線的位置偏差範圍為±1~±2mm,長桁的位置偏差為±2mm等。
位置準確度
表示飛機尾翼相對於機身的位置準確度參數是上反角(或下反角)口、安裝角a和後掠角。一般將其允差值換算成線性尺寸在飛機水平測量時檢驗。
表示各操縱面相對於固定翼面的位置準確度參數是階差、剪刀差和問隙。
表示機身各段問的相對位置準確度參數是同軸度。同軸度本身的要求並不高.一般在幾毫米以內,但必須保證各段對接處的階差不超過表面平滑度的要求。
生產線
隨著自動鑽鉚技術與數位化技術緊密結合,分別形成了多種機型、多種部件的自動化裝配生產線。自動化裝配生產線有多種模式.按照裝配單元集中布置的單元生產模式、按照裝配流程布置的流水線生產模式以及混合布置模式等。傳統的裝配生產線一般採用按照裝配單元集中布置的單元生產模式,而新近規劃中的一些部件裝配生產線多是採用按照裝配流程布置的流水線生產模式。實際上所有的生產線很難完全採用單一理念,最終採用混合布局生產線。在部裝和總裝階段,最具代表性的是波音公司的總裝移動生產線,通過採用了移動生產方式。大大縮短了飛機總裝時間,降低了總裝成本,提高了裝配質量。
為了充分發揮裝配生產線的性能,保證生產效率和速度,需要按自動化裝配工藝流程對生產線進行整體規劃,針對生產線從管理、工藝和控制等方面進行完善的設計。
流程最佳化
飛機裝配過程複雜,工作量大,採用自動化生產線的裝配流程,既要考慮自動化裝配作業的空間開敝性,同時也要兼顧工位作業的平衡性,正確的進行結構分段,合理劃分裝配單元,安排裝配任務。而流程最佳化和改進是一個反覆循環的過程,這對自動化生產線的設計與規劃提出了更高的要求。生產線必須具有一定的柔性,以滿足流程最佳化的需求。
流程最佳化的另一個重要環節是飛機裝配作業的規範化和標準化,包括裝配動作、時間、業務流程、設備以及裝夾具等。完成裝配工作的標準化,是建立自動化裝配生產線的基礎。對於飛機裝配而言,其標準化工作主要包括以下幾個方面:
(1)裝配動作的標準化。針對批生產,將裝配操作步驟和操作方法具體化、固定化,保證過程的一致性、穩定性。
(2)業務工作標準化。繪製各類工作流程圖,固化工作流程,縮短裝配周期。如質量檢驗、生產計畫與調度等業務工作。
(3)設備維護標準化。編制統一的生產線設備維護保養手冊,定期對設備進行維護保養,提高設備的利用率。
(4)工裝夾具通用化。通過工裝夾具通用化,採用組合工裝和快換工裝等技術手段,保證工裝夾具的可持續操作性。
產能平衡
生產線平衡問題已被認為是生產流程設計及作業標準化過程中關鍵的一環。企業實現均衡生產不僅有利於保證設備、人力的負荷平衡,從而提高設備和工時的利用率,同時還有利於建立正常的生產秩序和管理秩序,保證產品質量和安全生產;均衡生產還有利於節約物資消耗,減少在制品數量.加速流動資金周轉.從而降低生產成本。
精益物流
精益物流是保障生產線順利運轉的重要環節,物流配送需將準備好的完全成套件,按指定的架次、在指定的時間、按照規定的路線送到指定的地點,保證裝配工作有序地進行。物流包括兩個層次,第一個層次主要指企業內部物流,尤其是與裝配生產線相關的物流配送和管理;第二個層次是企業外部的物流,涉及產品組成零組件的供應商,以供應鏈為基礎。
企業內部物流是伴隨著裝配生產過程而產生的。面向飛機裝配生產線的生產現場物流配送需要結合飛機的裝配流程、產品特徵、生產線布局,充分考慮到物流通道和配送手段.儘量減少傳送、等待的時間,降低倉庫、生產線的庫存。尤其是飛機零組件/大部件體積大、占用空間大、運送不方便,對物流通道和配送手段都提出了更高的要求。
在主製造商一供應商的製造模式下,企業外部物流的保障對於裝配生產線的連續運轉尤為重要。企業外部物流要整合供應鏈資源,加強對供應商的管理,提高零部件質量,統一信息、技術、設備、操作標準,建立供應商到貨時間視窗.提高到貨的準確性,確保供應商快速、高質量的安全供貨。
集成控制
生產線的集成控制包含生產任務的下達、生產數據的採集與上傳、物流、工藝規程與標準規範的傳輸等。同時生產線控制還與企業的實際生產流程和習慣密切相關,是充分發揮生產線設備性能、提升效率最為關鍵的環節。
生產線仿真
生產線的數位化仿真主要包括生產線布局仿真、干涉仿真、人機工程仿真以及物流仿真等。在生產線的規划過程中,通過仿真分析,可提前發現生產線中存在的干涉、生產瓶頸等問題,減少不必要的返工,節約時間和成本。