蝸室是把擴壓器後面或葉輪後面的氣體收集起來,傳輸到壓縮機外部去,使氣體流向氣體輸送管道或流到冷卻器中進行冷卻。此外,在匯集氣體的過程中,由於蝸室外徑的逐漸增大和通流截面逐漸擴大,也對氣流起到一定的降速擴壓作用。
基本介紹
- 中文名:蝸室
- 外文名:volute
- 領域:壓縮機工程
簡介,壓縮機焊接機殼蝸室型線設計,相關研究,採用雙流道蝸室減振降噪,雙蝸室離心泵,
簡介
蝸室作為壓縮機的基本元件之一,承擔著收集壓縮介質、引導介質流向並進一步擴壓的作用,其結構好壞直接影響著蝸室內氣體流動和壓縮機整機的效率。因此,研究壓縮機排氣蝸室內流動,最佳化排氣蝸室的設計對提高設計質量有著重大的意義。
壓縮機焊接機殼蝸室型線設計
對於蝸室型線的設計基於兩個認識前提:
①蝸室中不同截面處的流量是不同的,在任意截面處,氣體的容積流量是與位置角成正比的;
②如果蝸室的型線能保證氣體自由流動,這時蝸殼壁對氣流即不發生作用(理想狀態下,實際上是應該努力消減這種相互作用),則在不考慮粘性的情況下,氣體在蝸室內的運動將遵循動量矩不變定律。確定蝸室的型線主要有下面兩種方法:一種是蝸室的型線按氣體自由流動的軌跡來設計,這樣,蝸室外壁和氣流之間沒有相互的作用,氣體在蝸室中的流動規律便為動量矩不變規律(不計摩擦的影響)。根據動量矩不變,可得到速度沿徑向分布規律,然後由通過截面的流量來求得截面積大小和蝸室外壁的直徑。另一種方法為給定蝸室內各截面的平均速度Cm的變化規律,再由通過截面的流量來計算截面積的大小和確定蝸室外壁的型線。
相關研究
採用雙流道蝸室減振降噪
對於單流道螺旋型蝸室,其線型關於葉輪中心軸是不對稱的。 蝸室的這種非軸對稱性造成了蝸室和葉輪流道內速度場和壓力場的分布不均勻, 從而使葉輪產生不可平衡的徑向力。由於泵內的速度和壓力有脈動,因此葉輪受到的徑向力也是脈動的。可見,要從根本上消除或降低葉輪的徑向力就必須改變蝸室的單螺旋結構。
一種簡單可行的方法是將單螺旋線型蝸室變為雙螺旋線型蝸室,或稱雙流道蝸室,即在單螺旋線繞過葉輪軸心 180°後再拷貝一次同樣的螺旋線,如圖1所示。
由於雙螺旋線型關於葉輪軸中心是對稱的,可使葉輪內外的流動接近軸對稱, 故採用雙螺旋蝸室可大大減小葉輪受到的徑向力。 Agostinelli 等人(1960)對單螺旋蝸室、雙螺旋蝸室及改進的同心圓蝸室配同一葉輪的 3 個泵進行了葉輪徑向力的試驗,測試結果表明:採用雙流道蝸室的葉輪徑向力比標準單螺旋蝸室大大降低,降幅超過 50%,且徑向力隨流量的變化很小而不像單螺旋蝸室那樣一旦偏離設計工況就急劇升高。
圖1
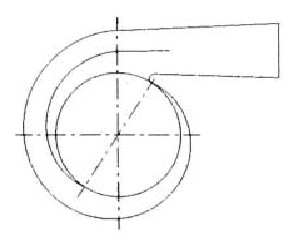
雙蝸室離心泵
了解發現,國產的大型雙吸離心泵幾乎都是單蝸室泵,即採用螺旋形壓水室。造成使用螺旋形壓水室的原因有兩方面,其一是設計方法,一般對於大型泵可靠的設計方法是相似換算,即選取一個各方面性能優良、泵型和比轉數相同的小泵作為模型泵,相似放大流道尺寸,通常小泵是單蝸室也就造成了大泵也是單蝸室;其二是追求泵的高效率,因擔心使用雙蝸室等其他結構會增加過流表面,增大水力損失而降低效率。當然單蝸室泵具有製造比較方便、泵性能曲線高效區域比較寬、車削葉輪後泵效率降低比較小等優點,所以多數大型離心泵仍採用單蝸室結構。
單蝸室泵在偏離設計工況運行時,水力上會產生與泵軸垂直方向的徑向力。特別是大型泵在啟動(零流量)時,將產生很大的徑向推力作用於葉輪上,造成過度增加軸的撓度,這能引起密封環的快速磨損,或者對於使用粘性材料的密封環將發生咬合粘接,造成事故。撓度過大會造成泵軸與電機軸偏心,使電機竄軸。同時,徑向力對於轉動軸是一個交變載荷,在軸承跨度較大的雙吸泵內,由於金屬材料的疲勞,常常發生泵軸的損壞。大型單蝸室泵在啟動時會形成較大的徑向力,它可造成密封環磨損或粘接以及電機竄軸等問題,這一點是不容忽視的,應儘量避免頻繁啟動和偏離設計工況運行,以防形成過大的徑向力。
採用雙蝸室泵體能在大、小流量工況下改善效率,原因在於葉輪出口周圍的壓力分布比單蝸室中更加均勻,葉輪出流情況更好。在雙蝸室中速度頭轉化為壓力能發生在擴散管中,引導第一個蝸室中的液體流出的流道(第二個蝸室的外側)是等斷面的,否則效率降低會超過1%。
所以,大型離心泵設計為雙蝸室能為高效安全運行創造條件。
設計大型離心泵時,可採用結構對稱的雙蝸室壓水室,能基本平衡徑向力,消除因軸產生撓度而引起的問題,擴大泵的運行範圍,提高容積效率。