基本介紹
- 中文名:粉末冶金機械零件
- 提出時間:70年代
- 套用學科:機械
- 適用領域範圍:農業機械、汽車、工具機、儀表、紡織、輕工
正文內容
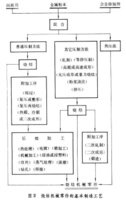
粉末冶金機械零件是指用粉末冶金方法製造的機械零件,又稱燒結機械零件。到70年代,燒結機械零件在生產上已頗具規模,在農業機械、汽車、工具機、儀表、紡織、輕工等工業...
《粉末冶金機械零件實用技術》是2006年化學工業出版社出版的圖書,作者是周作平,申小平。...
《粉末冶金汽車零件》是2013年5月化學工業出版社出版的圖書,作者是韓鳳麟。...... 《粉末冶金汽車零件:設計·生產·套用》可供汽車製造、機械製造及粉末冶金零件生產...
粉末冶金齒輪,在整個粉末冶金零件中難以單獨統計,但無論是按重量還是按零件數量,粉末冶金齒輪在各種機械、汽車、機車中所占的比例都遠遠大於其他領域中的粉末冶金...
粉末冶金產品的套用範圍十分廣泛,從普通機械製造到精密儀器;從五金工具到大型機械;從電子工業到電機製造;從民用工業到軍事工業;從一般技術到尖端高技術,均能見到粉末...
20世紀30年代,旋渦研磨鐵粉和碳還原鐵粉問世後,用粉末冶金法製造鐵基機械零件獲得了很快的發展。第二次世界大戰後,粉末冶金技術發展迅速,新的生產工藝和技術裝備、新...
《粉末冶金模具模架實用手冊》一書的出版社是冶金工業出版社,出版時間是1998-09。...... 粉末冶金模具和模架是粉末冶金機械零件壓製成形的基本工具。本手冊系統闡述了...
從2016 年獲得中國機械零部件工業協會的粉末冶金獲獎產品中,可以看到優異的燒結零件性能是以原輔材料的性能為基礎的。2016 中國機械零部件優秀新產品的獲獎產品中,較...
經濟效益高等優點,而且克服了傳統粉末冶金工藝製品材質不均勻、機械性能低、薄壁成型困難、結構複雜等缺點,特別適合於大批量生產小型、複雜以及具有特殊要求的金屬零件...
具滲透性產品的密度(Permeable Density) 所定義之體積含開放孔及封閉孔,粉末冶金...如結構性粉末燒結機械零件、含油軸承、精密陶瓷被動組件...等都是屬於吸水性粉末...