懸浮床加氫工藝是指流體流速帶動一定顆粒粒度的催化劑運動,形成氣、液、固三相床層,從而使氫氣、原料油和催化劑充分接觸而完成加氫裂化反應。
基本介紹
- 中文名:懸浮床加氫工藝
- 外文名:Suspension bed hydrogenation process
- 學科:石油煉製工程
- 特點:操作流程簡單
- 設備:懸浮床加氫反應器
- 趨勢:高度分散的催化劑體系等
工藝流程
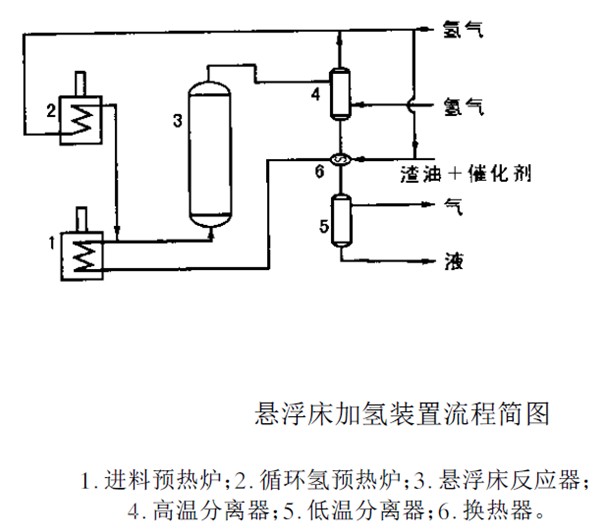
懸浮床加氫工藝是指流體流速帶動一定顆粒粒度的催化劑運動,形成氣、液、固三相床層,從而使氫氣、原料油和催化劑充分接觸而完成加氫裂化反應。
懸浮床加氫工藝是指流體流速帶動一定顆粒粒度的催化劑運動,形成氣、液、固三相床層,從而使氫氣、原料油和催化劑充分接觸而完成加氫裂化反應。...
均相懸浮床工藝以全餾分煤焦油為懸浮床加氫進料,將水溶性催化劑分散在原料油中,反應產物經分餾後得到的石腦油和柴油組分進入到固定床反應器繼續深度加氫精制及加氫...
《〈煉油技術與工程〉加氫專輯(2006-2010年)》由朱華興和張立新主編,收入了《分餾塔進料溫度先進控制系統在加氫裂化裝置的套用》、《外加催化劑對渣油懸浮床加氫...
2. 中國石油集團重大攻關項目 ,重油懸浮床加氫工藝的研究與開發。主要研究人員(子課題主持人)3. 中國石油科技創新基金 ,重油加氫裂化分散型納米催化劑的製備與小試...
中國石油大學(華東)所開發的重油懸浮床加氫新工藝,達到世界先進水平。但從國內、外試驗過程中發現,運行過程中膠質以微細催化劑顆粒和其它機械雜質為載體逐漸生成焦碳...
2001.07-至今負責中國石油天然氣股份有限公司專項“重油懸浮床加氫新型反應器開發研究”子項“液固旋流分離器在懸浮床加氫工藝中的套用”和專項“硫化氫製取氫氣技術...
減粘裂化—渣油加氫脫硫組合工藝研究”,, 煉油設計催化劑對渣油懸浮床加氫裂化的影響”,油氣加工“渣油懸浮床加氫裂化催化劑的研究”,石油科技進展...
vcc工藝技術 編輯 懸浮床加氫裂化技術是煤高壓懸浮床加氫液化技術的延伸和發展,目前有德國VEBA石油公司的VCC懸浮床加氫裂化技術、加拿大石油公司的Canmet懸浮床加氫技術...
兩段提升管催化裂化新技術及先進裝備開發;重油懸浮床加氫新工藝的工程化研究;重質油轉化催化材料新型孔結構的設計和製備研究;水合物法分離氫氣技術;低碳烯烴及清潔...
多年潛心重油加氫及相關領域的技術研究、開發工作,主要致力於我國中、高壓加氫裂化,潤滑油加氫動力學,渣油懸浮床及煤焦油固定床、懸浮床加氫,清潔燃料生產等工藝技術...
5.2.2煤焦油延遲焦化—加氫技術364/ 5.3煤焦油懸浮床加氫工藝技術367/ 5.3.1均相懸浮床煤焦油加氫367/ 5.3.2非均相懸浮床煤焦油加氫裂化370/ ...
5.9 重質煤焦油加氫234 5.9.1 焦油加氫精制——加氫裂化工藝235 5.9.2 煤焦油聯合加氫裂化240 5.10 焦油加氫裂解243 5.11 焦油懸浮床加氫249 ...
參加完成的重油懸浮床加氫裂化催化劑及工藝開發項目已通過中型試驗,現正在進行工業裝置論證和初步設計。主持進行的石油餾分加氫精制新型催化劑的研究取得重大進展,已經在...
重油懸浮床加氫技術催化裂化反應集成技術催化裂化汽油MCSP脫臭技術催化裂化液化氣固體鹼脫硫精製技術催化裂化汽油固體鹼脫硫-固定床脫臭組合工藝FCC柴油加氫改質催化劑...
復配助劑對渣油懸浮床加氫裂化反應的抑焦作用,石油學報(石油加工), [EI收錄]羅輝,鄧文安, 高靜潔,張數義,闕國和. 懸浮床加氫裂化助劑對渣油中瀝青質的作用,...
獲得山東省科技進步獎三等獎1項;山東省教育廳二等獎一項;獲得國家發明專利3項;完成省部級縱向項目“重油懸浮床加氫裂化新工藝”多項;承擔並完成中石油中青年創新...
先後完成我國多種原油渣油的化學組成結構研究及重油加氫—催化裂化組合工藝,供氫劑減粘裂化工藝和渣油懸浮床加氫新工藝的開發, 渣油懸浮床加氫新工藝的開發目前已處...
主要業績:早年從事煤液化製取合成液體燃料的研究,負責研製成功的煤焦油懸浮床加氫催化劑,活性達到了德國生產的10927催化劑水平,並經工業放大使用。