內部結構
隨著加氫反應器向大型化發展,生產和科研單位對反應器的內部結構設計都非常重視,特別是對兩相進料的反應器,進料分配的好壞直接影響反應效果、催化劑壽命以及操作周期。

加氫反應器的內部結構均由以下幾部分組成:入口擴散器(或稱分散器),液(流)體分布盤,筒式濾油器(或稱過濾籃筐),催化劑床層支件,急冷箱和再分布板以及反應器出口集油器。
(1)反應器入口擴散器(或稱分散器)
加氫反應器頂部及入口分散器結構如圖所示。反應器進料從入口進人反應器,一般流速較大,而且集中在反應器橫截面中心,為防止其直接衝到分布板上,在反應器入口處安裝一個擴散器。擴散器有兩個孔道。進入反應器的油氣流向和孔道垂直,這樣當液流進入反應器的擴散器後不會從某一孔道處短路流出,造成分配不勻。
(2)液體分布盤
液體分布盤及泡帽結構見右圖,這是保證液體分布均勻的最重要的部分。分布盤上裝有帶齒縫的圓形泡帽。當氣液兩相物料進到分布盤上後,在分布盤上就建立了液層。氣體從齒縫通過,同時把液體從環形空間帶上去進人下降管。如果液體負荷大,可能會淹沒一部分齒縫面積,但由於減小了氣體通路面積,增大了氣體的流速,從而相應地又會多帶走一部分液體,最終達到平衡。從下降管下來的液體呈錐狀噴灑到催化劑床層上。據文獻報導,這種結構型式的分布盤的另一個優點是傳熱效率高(達89%),而且對安裝水平度的敏感度不大。為了便於裝卸催化劑,這種分布盤是由兒部分做成的,升氣管與盤板滾壓嵌接成一體,達到基本密封。

(3)筒式濾油器(或稱過濾籃筐)
筒式濾油器安裝在反應器頂部,它給進料提供更大的表面積,這樣就允許催化劑床層積蓄較多的垢屑或沉積物而不致過度增大床層壓降。筒式濾油器是空心的,用鏈條結在一起,並用鏈條固在支持樑上,以防止卸催化劑時堵塞催化劑卸料管。鏈條的長度必須足夠鬆弛,以使濾油筒隨催化劑床層下沉。根據生產經驗,在運轉期間,催化劑床層下沉量約5%。
但是也有報導認為,過濾油筒安裝在液體分布盤的上部,反而效果更好。
(4)催化劑床層支件
支持催化劑床層的結構件是T形橫樑、格柵、篩網和瓷球。T形橫樑橫跨筒體,頂部逐步變尖,以減少阻力。
(5)急冷箱和再分布板

急冷箱的作用是將上面床層流下來的反應物料和冷氫充分混合,使物料進人卜一層催化劑床層之前重新分布均勻,急冷箱結構見圖。急冷箱是由安裝在冷氫管下面的三塊板組成。第一層板是截流板,把反應物料集合起來排人急冷箱。在這層板下,只開有兩個孔,全部物料和氫氣都必須從這兩個孔通過,使冷氫和反應物料充分混合。急冷箱置於急冷盤和噴散盤(篩板)之間,油氣在此混合,噴散盤上開有很多小孔,使急冷箱物料由此進到第三塊板(即泡帽再分布板),再從再分布板進人下一層催化劑床層。使用裝有這種結構急冷箱的加氫裂化和加氫精制反應器的實踐證明,這種結構可以保證床層溫度分布非常均勻,每個床層底部的徑向溫差都小於1℃。
(6)反應器出口集油器
反應器出口集油器如圖所示,起支撐下層催化劑床層的作用,在集油器周圍填入陶瓷球。
加氫精制反應器內催化劑一般只分兩層,所以採用在床層內部連通的四根卸料管,可把催化劑卸至反應器底部排出。
對於加氫裂化反應器,因為床層多,採用連通管時在床層之間會有氣體互相串通,對加氫裂化反應不利,所以採用在每個床層的側壁開口卸催化劑。
工作過程
由反應段出來的
加氫生成油首先被送到熱交換器,用新鮮原料冷卻,然後進入空冷器。在高低壓分離器中脫除溶解在液體產物中的氣體。將從分離器內分離出的循環氣通過吸收塔,以脫除其中的大部分硫化氫。在某些情況下,可以將循環氣進行吸附精製,完全除去低沸點烴。有時還要對液體產物進行鹼洗和水洗;加氫生成油經過蒸餾,可製得柴油(200-350℃餾分)、催化裂化原料油(350~500℃餾分)和大於500℃的殘油。
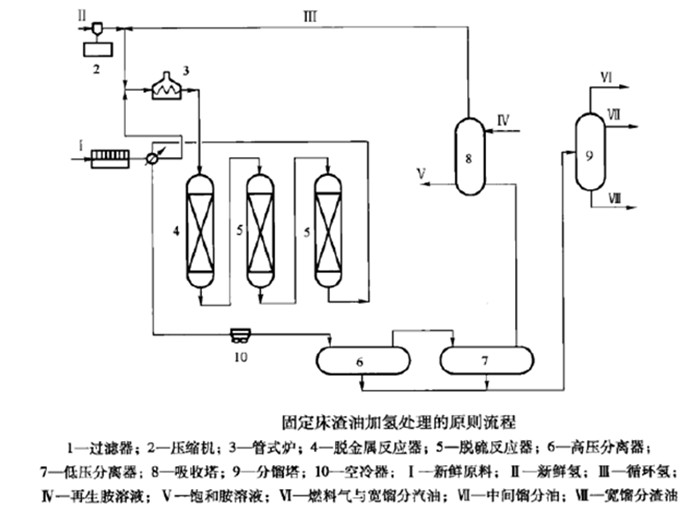
根據原料油的質量以及對最終產品的要求,加氫脫硫工藝的流程型式可以是一段式、二段式或多段式。可以不循環操作,也可以令部分加氫油與原料混合,實行部分循環操作以提高總精製深度。
分類
按照催化劑固定方式的不同,Biardi等將固定床反應器分為傳統型與非傳統型兩種。傳統型固定床是指催化劑以粒子形式進行堆積,主要有並流下行泡沫床和並流上行泡沫床;非傳統型固定床是指將催化劑以某種形態負載或固定於某種結構填料上,通常使用Monolith催化劑和Katapak—Sandwich催化劑等。
1、並流下行泡沫床
Solvay公司認為當氣、液相併流下行時,如果同時成倍地提高工作液和氫氣的流量,可以從滴流床過渡到泡沫床。因為泡沫床的氣液接觸面積較滴流床有了明顯的提高,所以氣液相間的傳質作用明顯增強。並且,這種改進不需增加輔助設備就可方便地實現。同時,為了解決快速反應和加壓條件下泡沫的淬滅、聚並,以及由此引起的床層壓降波動較大、進料難以控制的問題,該專利採用惰性氣體(最好是氮氣)來稀釋氫氣,並給出了氮氫最優比。這樣,不僅可以穩定床層壓降,還可提高催化劑的選擇性。與之相反的一種稱為並流上行泡沫床。
2、並流上行泡沫床
1、Solvay公司採用高1.4m、直徑18mm的反應器,使用不同粒徑的球形Pd—SiO:催化劑,讓氣液由反應器的底部進料,並流上行,通過調整氣液流量比使其達到泡沫狀態。並認為並流上行泡沫床優於並流下行泡沫床,對加氫過程更為有利。其一,與並流下行泡沫床相比,並流上行泡沫床的床層壓降更小,床層穩定性更好;其二,並流上行泡沫床的氣液相流速低,甚至可以和液相以化學計量比進料,就町以獲取較高的單程加氫效率。這種方法的缺點是催化劑周圍的滯液量較大,加速了催化劑的失活。
2、Monolith固定床反應器
Monolith固定床反應器是通過利用平行於道內載催化劑為固定床,從而達到提高三相接觸效率和固定床時空收率,降低床層壓降的目的。當氫氣經分布器後形成的氣泡直徑通常比Monolith固定床的孔道要小。根據氣液流速的變化,兩相流的流型有4種,即鼓泡流、Taylor流、環狀流和彈狀流。EkaNobel公司建議使Monolith孔道內的流型處Taylor流,此時對反應最為有利。液相蒽醌工作液從反應器的頂部進料,氫氣從反應器的底部進料與液相反應,未反應的部分經外循環去塔頂繼續參與反應,使床層壓降為零,反應器內的壓力接近常數,這對於提高反應的選擇性有鶯要的作用。實驗證實,與傳統工藝相比,該工藝的放大效果很好,工業規模對實驗室規模的放大效應遠小於傳統工藝。目前,該工藝已被EkaNobel公司套用到工業生產過氧化氫中,成為Monolith固定床反應器工業化的經典範例。
特點
固定床反應器床層薄,流速低,床層內的流體軸向流動可看作是理想置換流動,因而化學反應速率較快,完成同樣的生產任務所需的催化劑用量和反應器體積較小,流體停留時間可嚴格控制,溫度分布可適當調節,有利於提高化學反應的轉化率和選擇性;固定床中催化劑不易磨損,可在高溫高壓下操作。當然,固定床也存在一些缺點,如傳熱性能差;不能使用細粒催化劑(不能充分利用催化劑內表面),催化劑的再生、更換均不方便。
套用
固定床加氫反應器在化工領域套用十分廣泛。基本有機化工中,乙烯氧化制環氧乙烷、乙苯脫氧制苯乙烯、乙烯水合制乙醇等反應均在固定床反應器中進行。