高爐熱交換是高爐連續鑄鋼煉鐵過程中爐內上升煤氣流與下降爐料之間的熱傳遞現象。從熱工角度看高爐熱交換屬逆流式高溫氣流將熱傳輸給運動著的散料床,使散料溫度升高,而煤氣自身溫度降低的現象。它是高爐冶煉的主要過程之一。
基本介紹
- 中文名:高爐熱交換
- 外文名:exchange of heat in blast furnace
- 學科:冶金工程
- 傳熱方式:傳導、對流、輻射
- 影響因素:風溫等
- 相關方程:熱平衡方程、傳熱速率方程
介紹,傳熱和控制,熱交換係數,工藝影響,
介紹
從熱工角度看高爐熱交換屬逆流式高溫氣流將熱傳輸給運動著的散料床,使散料溫度升高,而煤氣自身溫度降低的現象。它是高爐冶煉的主要過程之一。熱交換不僅決定著高爐內溫度場分布,而且還影響著冶煉過程的還原、造渣等一系列物理化學反應,因為上升的高溫煤氣既是載熱體,又是還原劑,也就是在與爐料熱交換過程中既提供爐料升溫的熱量,還提供各種物理化學變化所需的熱量,保證還原等過程的進行。高爐內的溫度場雖然因各高爐具體情別,但是沿爐子高度的溫度分布卻有共同規律(見圖1):在爐料裝入爐內的上部地區和從風口燃燒帶形成煤氣往上升的地區,由於煤氣與爐料之間的溫度差很大,進行著很強烈的熱交換,形成高爐上部熱交換區和下部熱交換區;而在高爐的中部,煤氣與爐料的溫差較小(25~50℃),是熱交換進行得極其緩慢的地區,被稱為熱交換空區或熱儲備區。熱儲備區的存在說明高爐是一種熱交換很完善的設備。這種熱交換規律是由前蘇聯學者基塔耶夫(В.И.Кumаев)教授發現,並通過熱平衡方程和傳熱速率方程的聯解給出了其傳熱規律的數學表達式。

傳熱和控制
高爐內以傳導、對流、輻射三種方式將熱量由煤氣傳給爐料。其傳熱過程是由煤氣向料塊表面的外部傳熱和料塊表面向料塊核心的內部傳熱完成的。傳導傳熱主要是在料塊內部傳熱中起主導作用,也就是料塊表面的熱通過傳導傳熱傳到料塊中心。由於高爐料柱內料塊之間的接觸絕大部分是點接觸,所以料塊之間的傳導傳熱很小而常被忽略不計。
傳導傳熱的傳熱方程為:QC=λ/r(t料表-t料核)=hc(t料表-t料核);
式中Qc為通過傳導傳送的熱量,kJ/m·s;λ為爐料的導熱係數,W/m·℃;t料表、t料核為爐料表面和核心的溫度,℃;hc為導出的導熱係數W/m·℃;r為爐料的半徑,m。對流傳熱是運動的煤氣流對料塊外表面的主要傳熱方式,其規律為Qt=α(t氣-t料表);式中Qt為對流傳熱量,kJ/m·s;α為對流給熱係數,W/m·℃,它與煤氣的流速(以雷諾數為特徵的流動狀態)、煤氣的運動黏度與料塊的直徑有關;t氣為煤氣溫度,℃。
輻射傳熱是高溫煤氣以輻射方式向料塊表面傳送熱量,它與料塊的黑度、煤氣的溫度和煤氣中三原子氣體(例如CO2、H2O)含量和不對稱雙原子氣體(CO)的含量等有關。
輻射傳熱規律為:Qr=εCr(T4氣-T4料表)=hr(t氣-t料表);
式中Qr為通過輻射傳送的熱量,kJ/m·s;ε為黑度;Cr為輻射係數,W/m·K;hr為導出的輻射係數,W/m2·℃。研究和測定的結果說明:礦石的導出導熱係數hC高於焦炭的,而礦石和焦炭的hc又分別高於它們的對流給熱係數α,所以在高爐的熱交換過程中對流給熱是限制性因素。研究還證明不同溫度下礦石的hc遠高於(α+hr),因此對流給熱仍然是控制環節,但是焦炭在高溫下(725℃以上)hc小於(α+hr),這時焦炭本身的傳導傳熱成為控制性環節。
熱交換係數
從傳熱來說可用高爐內控制性環節的對流給熱係數來評價高爐內料層中的熱交換強度。在散料的熱交換計算中有兩種形式的給熱係數:單位料塊表面積的(αF)和單位料層體積的(αv),它們之間的關係為:單一球徑的爐料αv=αF[6(1-ε)d];任何形狀的爐料αv= αF[7.5(1-ε)d];式中ε為爐料的空隙度;d為爐料的直徑,m。基塔耶夫根據C.費爾涅斯用高爐爐料和其他物料所做傳熱試驗數據,導出αv的計算式αv=186(w0.9氣T0.3/d0.75) M,W/m3·℃;式中w氣為氣體流速,m/s;T為氣體的平均溫度,K或273+t氣℃;d為料塊直徑,m;M為與料層透氣性有關的係數,對一般高爐爐料M=0.5,對無粉末單一粒徑的理想爐料M=1.0。季莫費耶夫(В.Н.Тимофеев)根據他人所做實驗資料整理出的αF計算式為αF=B[(w氣ρ氣d)7/d];式中係數B=λ/η0;λ,η為氣體的導熱係數和黏度;w氣為氣體的流速,m/s;ρ氣為氣體的密度kg/m;d為散料的直徑,m。如果考慮爐料內部傳熱,則綜合熱交換係數為:
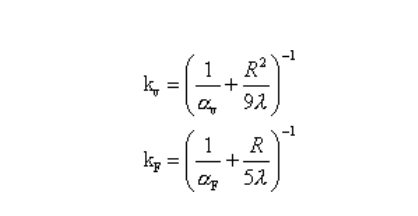
對於高爐所用實際爐料來說,綜合熱交換係數kv在1100~6300W/m·℃,或kF=25~130W/m·℃。
工藝影響
煉鐵工作者用料流和煤氣流的水當量變化及m值的升降來評價冶煉工藝因素對熱交換和爐內溫度場分布的影響。
(1)風溫。風溫提高以後,風口前燃燒的焦炭量減少,單位生鐵形成的煤氣量減少,W氣也隨之降低,W氣/W料下降;理論燃燒溫度升高,即t氣缸上升,使高爐下部熱交換區傳熱加強,H下縮短,也就是高溫區下移,進入上部熱交換區時煤氣流的熱量減少,從而使爐身溫度和爐頂溫度下降。
(2)富氧。富氧鼓風以後,最明顯的特徵是風中N2減少,燃料在風口前燃燒形成的煤氣量減少,W氣隨之下降,而爐料的總消耗沒有發生明顯變化,W料不變,因此W氣/W料下降;理論燃燒溫度的提高也使t氣缸上升,其結果同提高風溫相似:高溫區下移,爐身溫度和爐頂溫度降低。而且富氧比提高風溫所造成的影響更大。因為進入上部熱交換區煤氣流帶入的熱量更少。所以在採取措施時,W氣/W料下降到1.0是鼓風富氧的極限。為解決高富氧後爐身部位熱量緊張,要減少該部位吸熱過程的熱量消耗或增加該部位的熱量收入,前者可以採取不用含結晶水爐料,不用熔劑,降低熱損失等,而後者可向爐身部位噴入熱還原性氣體等。
(3)噴吹燃料。高爐噴吹燃料以後,因為噴吹燃料中碳氫化合物含量高,碳氫化合物在風口前轉化為CO和H2放出的熱量少於焦炭中碳轉化為CO時放出的熱量(例如CH4+0.5O2—→CO +2H2+成的煤氣體積卻相反,1mol碳氫化合物形成的氣體體積比1mol碳形成的氣體體積多了2倍H2的體積。結果爐缸的理論燃燒溫度降低了,W氣增大了:而噴吹燃料置換了焦炭,從爐頂加入爐內的爐料的總消耗量降低,使W料減小了,最終是W氣/W料增大。t理的降低減弱了爐子下部的熱交換,m的增大使爐身溫度和爐頂溫度升高。
(4)焦炭負荷。負荷增加使高爐上、下部的溫度都降低,因為這時爐子上部和下部的W氣/W料都降低了,而爐子中部的空區擴大。從熱交換的角度看,高爐焦炭負荷增大的極限是W氣/W料=1。在現代高爐上,原料準備很好,爐子上部的W料已經達到0.8~0.9W氣。高爐的熱能和化學能利用程度已經接近傳熱上和熱力學上的最高值,這是任何火法冶金設備所不能比擬的。