分類
磨損失效
磨損是零件表面在互相接觸的狀態下運動時,因摩擦等因素引起的金屬小顆粒逐漸從表面脫落的破壞現象。工程套用中,表面相互接觸只能是在一些凸點上,這些點形成摩擦連線的接觸點,而且接觸是不連續的。當接觸表面相互移動時,由於表面接觸點的相互作用,將產生彈性和塑性形變。這個過程一經產生,並且繼續進行下去,還會在摩擦表面和表層同時伴生一系列物理舉精辯愚的、化學的和機械的過程。這些典型過程和現象有:局部高溫;形成氧化膜或其他化合物的化學過程;材料的轉移;潤滑劑作用過程。根據磨損過程的主導因素與磨損失效的機理,磨損可分為粘著磨損、磨粒磨損和腐蝕磨損三種基本類型。
1、粘著磨損
零件接觸面在很大的局部壓力下發生局部的粘著(焊合),然後粘著處在隨後的運動中被拉開,使金屬小顆粒不斷從接戶拔灶充觸面脫落,從而引起零件失效。粘著磨損通常發生在接觸表面缺乏潤滑和氧化膜的滑動摩擦條件下,但是當在高速、重載和高溫的情況下,即使存在潤滑和有氧化膜的條件下也會使潤滑油膜和氧化膜斷裂,主要包括粘著點的形成、剪下、材料轉移、轉移材料脫落牛棄榆四個過程,如圖1(左面圖)所示。粘著磨損的破壞特徵是在被磨損零件的表面常呈現出細長條狀的摩擦痕跡和撕裂痕跡,在硬面上會粘附多餘的材料。粘著磨損的破壞範圍視摩擦條件而異,塑性材料常發生在離表面一定深度處,磨損下來的粒較大。而
脆性材料的破壞深度較淺,磨損產物常呈磨屑狀。粘著磨損表面特徵包括錐形坑犁道精、魚鱗凹坑以及拉傷,如圖1(右面圖)所示。

圖1
粘著磨損通常發生在接觸表面缺少潤滑和氧化膜的滑動摩擦條件下,有時潤滑和氧化膜破裂,也會造成零件表面直接接觸而發生粘著,例如高速重載齒輪傳動中常易發生熱咬合”,粘著磨損失效常發生在活塞環與缸套、滑動軸承與輪頸、蝸輪與蝸桿、液壓泵配流盤與缸體和齒輪等摩擦副零件上。
2、磨粒磨損
由硬顆粒或硬突起引起材料破壞,分離出磨屑的磨損,稱為磨粒磨損,是常見的一種磨損。磨粒磨損又是危害最嚴重的一類磨損,其磨損速率或磨損強度都很大,致使裝備的使用壽命大大降低。磨粒磨損的典型過程包括:磨粒壓入表面、切削金屬、形成溝槽,如圖2所示。

圖2
根據摩擦表面所受的應力和衝擊大小不同,磨粒磨損分為:
(1)鑿削式磨粒磨損。其特徵是磨粒以很大的衝擊力作用切入摩擦件金屬表面,由於受到很高應力,造成摩擦件表面巨觀變形,並可從金屬表面切削分離出金屬屑,使摩擦件表面產生較深的溝槽和壓痕。
(2)高應力碾碎式磨粒磨損。其特徵是磨粒與摩擦件表面作用應力高,超過磨粒本身的壓碎強度。磨粒夾在兩摩擦表面之間,產生很高的接觸應力,磨粒不斷被碾碎,並劃傷金屬表面,在摩擦表面產生溝槽和凹坑。
(3)低應力擦傷式磨粒磨損。其特徵是磨粒對摩擦面作用的應力低,不超過磨粒自身的壓碎強度,磨粒對摩擦表面擦傷,形成細而淺的犁痕。
3、腐蝕磨損
摩擦零件在運動時,其摩擦表面受到周圍環境介質化學作用,導致摩擦表面損失或遷移的現象稱為腐蝕磨損。其重要特點是摩擦過程中兼有腐蝕和磨損,並且以腐蝕為主導。腐蝕磨損可分為氧化磨損和特殊介質下的腐蝕磨損。
(1)氧化磨損。摩擦過程定獄達中,摩擦表面受到空氣中的氧或潤滑劑中氧的作用而形成的氧化膜層被磨損,稱為氧化磨損。在相對運動時,摩擦表面已形成的氧化膜因塑性微堡變形在拒項估接觸點不斷發生破壞而脫落,隨後又在該處形成新的氧化膜。如此反覆,使摩擦表面逐漸受到損耗。其基本條件是周圍環境。通常在空氣中所發生的氧化磨損速度是較小的也是生產中允許存在的一種磨損形式,氧化磨損常發生在曲軸軸頸和鋁合金等零件的摩擦件表面上。
基於此,氧化磨損必須同時具備以下條件:
①摩擦表面能夠發生氧化,而且氧化膜生成速度大於其磨損破壞速度。
②氧化膜與摩擦表面的結合強度大於摩擦表面承受的剪下應力。
③氧化膜厚度大於摩擦表面破壞的深度。氧化磨損的損壞特徵是,摩擦表面滑動方向呈現較均勻的細磨痕,磨損產物為紅色的片狀Fe2O3或灰黑色絲狀Fe3O4。因此,為提高零件抗氧化磨損的能力,通常可採用發藍處理、磷化處理、蒸氣處理以及滲硫等表面處理,使零件表面形成緻密而非脆性的氧化膜,且與基體牢靠結合,從而可減低磨損速率。
(2)特殊介質磨損。摩擦表面金屬與酸、鹼、鹽等介質發生反應,反應生成物質損失的現象。由於腐蝕本身可能是化學的或電化學的性質,故腐蝕磨損的速率與介質的腐蝕性質和作用溫度有關,也與相互摩擦的兩金屬形成
電化學腐蝕的電位差有關。介質腐蝕性越強,作用溫度越高。腐蝕磨損速率越大。但是,若摩擦表面受腐蝕時能生成一層結構緻密且與基體結合牢固、阻礙腐蝕繼續發生或使腐蝕減緩速度的保護膜,則腐蝕磨損速率將減小。
4、其他磨損形式
(1)微動磨損。壓緊配合的零件,在外部變動載荷和振動的影響下,在緊配合表面受到微小的振動和滑動,導致形成大量微小的氧化粉末,由此而造成的磨損稱為微動磨損。這種磨損易被忽視,因為它恰恰發生在相對靜止的接合零件上。這種磨損的最大特點是在外界變動載荷作用下,產生振幅很小(小於100um,一般為2-20um)的相對運動,由此發生摩擦磨損。通常發生在裝備
滾動軸承、燃汽輪機葉片根部與輪盤槽、鍛錘錘杄與錘頭的配合處以及各種壓緊合件的連線處,如在鍵連線、過盈配合、螺栓連線、鉚釘連線接頭等之類結合。微動磨損使配合精度下降、緊配合部件緊度下降甚至鬆動、連線件鬆動乃至分離,嚴重者引起事故。
(2)汽蝕浸蝕。當零件與液體接觸並產生相對運動,接觸處的局部壓力低於液體蒸發壓力時,形成氣泡。溶解的氣體也會析出形成氣泡。氣泡形成與破滅的反覆作用,使零件表面材料產生疲勞而逐漸脫落,呈麻點狀,逐漸擴展成泡沫海綿狀,這種現象稱為汽蝕。當汽蝕嚴重時,可擴展為深度20mm的孔穴,直到穿透或開裂而形成破壞,因此又稱為穴蝕。汽蝕常發生在缸套外壁、水泵零件、水輪機葉片、液壓泵等。這種破壞形式的主要特點是在局部區域出現麻點、針孔、嚴重時呈聚集的蜂窩狀的孔穴群。
接觸疲勞破壞失效
零件表面在交變壓應力長期反覆作用下引起的一種表面疲勞剝落破壞現象,稱為接觸疲勞破壞。這種損壞形式介於疲勞與磨損之間,通常發生在齒輪、滾動軸承、鋼軌和軋輥等零件上。根據接觸與相對運動情況,可分為以下兩種類型。
(1)滾動接觸疲勞。在
滾動軸承和傳動齒輪輪齒的接觸表面上出現的麻點和脫落現象就是接觸疲勞。這類零件的接觸表面出現麻點和脫落,往往是在接觸應力作用下經過一定循環次數後才發生的。理論上講,這類滾動元件相互接觸可認為是點接觸或線接觸。但是,實際上在載荷作用下滾動元件之間的接觸總有一定程度的彈性變形,直到形成的接觸區能有效承載為止。此時接觸表面上受到的局部壓力就是接觸應力。當兩圓柱體在平面應變狀態下相互對稱接觸時,在壓縮條件下接觸區為一平面。根據理論分析計算,實際接觸區的接觸應力是三向不等壓應力,它們沿深度Z方向的分布,如圖3所示。圖3中,三個方向的正應力最大值都在接觸表面,其中以Z方向的正應力為最大。而剪應力沿Z方向的分布則不同,它的最大值作用在表面下0.786b處(b—平面接觸區的半寬度)。

圖3
(2)滑動疲勞磨損。滑動接觸疲勞的過程,是由於任何固體的摩擦表面都具有粗糙度和接觸的不連續性,摩擦表面在法向載荷下相互壓入或壓平,在實際接觸斑點區內將產生相應的應力和應變。當表面摩擦時,這種作用將在材料表層下一定的體積內反覆進行,而且,由於載荷和溫度對一些微凸體的多次作用,不可逆變化過程的不斷積累,造成了結構、應力狀態的不均勻,微凸體成為應力集中源。在應力和應變反覆作用下產生微裂紋,這些裂紋匯合擴展,最後材料以微粒形態脫落形成磨屑。
總之,接觸疲勞破壞的特徵:接觸疲勞失效的特徵與應力狀態、潤滑條件、零件幾何形狀、表面形貌材料的組織結構和性能以及環境和介質的化學作用等因素有關,隨著服役條件和材料性質的改變其失效特徵也隨之而變。根據裂紋起始部位和擴展方式可分為亞表面麻點剝落、表面麻點剝落和深層剝落三種形式。
腐蝕損傷失效
腐蝕損傷是指零件與周圍介質的化學的或電化學的作用而導致的破壞。
金屬零件由於所處的環境以及其材料內部、成分和組織結構的不同,腐蝕破壞形式也不同,如圖4所示。
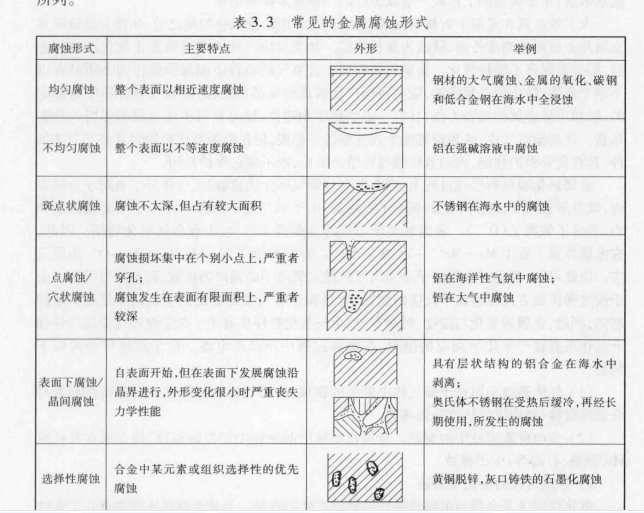
圖4
金屬腐蝕的形式雖然多種多樣,但按金屬與介質作用機理可以分為化學腐蝕與
電化學腐蝕。
腐蝕過程雖然是緩慢的,但危害卻相當大,破壞裝備的正常工作,降低使用壽命,是普遍性的嚴重問題。因此,減輕腐蝕的主要措施有:
(1)正確選材。根據環境介質和使用條件,選擇合適的耐蝕材料,如含有鎳矽、鈦等元素的合金鋼。
(2)合理設計。在裝備製造時,套用較優良的材料,在結構的設計上從金屬防護角度加以全面考慮,努力使整個部位的所有條件儘可能地均勻一致,做到結構合理、外形簡化
表面粗糙度合適。
(3)覆蓋保護層。在金屬表面上覆蓋一層不同的材料,改變表面結構,使金屬與介質隔離開來,用以防止腐蝕。主要方法包括覆蓋金屬保護層、非金屬保護層、化學保護層以及
表面合金化。
3、腐蝕磨損
摩擦零件在運動時,其摩擦表面受到周圍環境介質化學作用,導致摩擦表面損失或遷移的現象稱為腐蝕磨損。其重要特點是摩擦過程中兼有腐蝕和磨損,並且以腐蝕為主導。腐蝕磨損可分為氧化磨損和特殊介質下的腐蝕磨損。
(1)氧化磨損。摩擦過程中,摩擦表面受到空氣中的氧或潤滑劑中氧的作用而形成的氧化膜層被磨損,稱為氧化磨損。在相對運動時,摩擦表面已形成的氧化膜因塑性變形在接觸點不斷發生破壞而脫落,隨後又在該處形成新的氧化膜。如此反覆,使摩擦表面逐漸受到損耗。其基本條件是周圍環境。通常在空氣中所發生的氧化磨損速度是較小的也是生產中允許存在的一種磨損形式,氧化磨損常發生在曲軸軸頸和鋁合金等零件的摩擦件表面上。
基於此,氧化磨損必須同時具備以下條件:
①摩擦表面能夠發生氧化,而且氧化膜生成速度大於其磨損破壞速度。
②氧化膜與摩擦表面的結合強度大於摩擦表面承受的剪下應力。
③氧化膜厚度大於摩擦表面破壞的深度。氧化磨損的損壞特徵是,摩擦表面滑動方向呈現較均勻的細磨痕,磨損產物為紅色的片狀Fe2O3或灰黑色絲狀Fe3O4。因此,為提高零件抗氧化磨損的能力,通常可採用發藍處理、磷化處理、蒸氣處理以及滲硫等表面處理,使零件表面形成緻密而非脆性的氧化膜,且與基體牢靠結合,從而可減低磨損速率。
(2)特殊介質磨損。摩擦表面金屬與酸、鹼、鹽等介質發生反應,反應生成物質損失的現象。由於腐蝕本身可能是化學的或電化學的性質,故腐蝕磨損的速率與介質的腐蝕性質和作用溫度有關,也與相互摩擦的兩金屬形成
電化學腐蝕的電位差有關。介質腐蝕性越強,作用溫度越高。腐蝕磨損速率越大。但是,若摩擦表面受腐蝕時能生成一層結構緻密且與基體結合牢固、阻礙腐蝕繼續發生或使腐蝕減緩速度的保護膜,則腐蝕磨損速率將減小。
4、其他磨損形式
(1)微動磨損。壓緊配合的零件,在外部變動載荷和振動的影響下,在緊配合表面受到微小的振動和滑動,導致形成大量微小的氧化粉末,由此而造成的磨損稱為微動磨損。這種磨損易被忽視,因為它恰恰發生在相對靜止的接合零件上。這種磨損的最大特點是在外界變動載荷作用下,產生振幅很小(小於100um,一般為2-20um)的相對運動,由此發生摩擦磨損。通常發生在裝備
滾動軸承、燃汽輪機葉片根部與輪盤槽、鍛錘錘杄與錘頭的配合處以及各種壓緊合件的連線處,如在鍵連線、過盈配合、螺栓連線、鉚釘連線接頭等之類結合。微動磨損使配合精度下降、緊配合部件緊度下降甚至鬆動、連線件鬆動乃至分離,嚴重者引起事故。
(2)汽蝕浸蝕。當零件與液體接觸並產生相對運動,接觸處的局部壓力低於液體蒸發壓力時,形成氣泡。溶解的氣體也會析出形成氣泡。氣泡形成與破滅的反覆作用,使零件表面材料產生疲勞而逐漸脫落,呈麻點狀,逐漸擴展成泡沫海綿狀,這種現象稱為汽蝕。當汽蝕嚴重時,可擴展為深度20mm的孔穴,直到穿透或開裂而形成破壞,因此又稱為穴蝕。汽蝕常發生在缸套外壁、水泵零件、水輪機葉片、液壓泵等。這種破壞形式的主要特點是在局部區域出現麻點、針孔、嚴重時呈聚集的蜂窩狀的孔穴群。
接觸疲勞破壞失效
零件表面在交變壓應力長期反覆作用下引起的一種表面疲勞剝落破壞現象,稱為接觸疲勞破壞。這種損壞形式介於疲勞與磨損之間,通常發生在齒輪、滾動軸承、鋼軌和軋輥等零件上。根據接觸與相對運動情況,可分為以下兩種類型。
(1)滾動接觸疲勞。在
滾動軸承和傳動齒輪輪齒的接觸表面上出現的麻點和脫落現象就是接觸疲勞。這類零件的接觸表面出現麻點和脫落,往往是在接觸應力作用下經過一定循環次數後才發生的。理論上講,這類滾動元件相互接觸可認為是點接觸或線接觸。但是,實際上在載荷作用下滾動元件之間的接觸總有一定程度的彈性變形,直到形成的接觸區能有效承載為止。此時接觸表面上受到的局部壓力就是接觸應力。當兩圓柱體在平面應變狀態下相互對稱接觸時,在壓縮條件下接觸區為一平面。根據理論分析計算,實際接觸區的接觸應力是三向不等壓應力,它們沿深度Z方向的分布,如圖3所示。圖3中,三個方向的正應力最大值都在接觸表面,其中以Z方向的正應力為最大。而剪應力沿Z方向的分布則不同,它的最大值作用在表面下0.786b處(b—平面接觸區的半寬度)。

圖3
(2)滑動疲勞磨損。滑動接觸疲勞的過程,是由於任何固體的摩擦表面都具有粗糙度和接觸的不連續性,摩擦表面在法向載荷下相互壓入或壓平,在實際接觸斑點區內將產生相應的應力和應變。當表面摩擦時,這種作用將在材料表層下一定的體積內反覆進行,而且,由於載荷和溫度對一些微凸體的多次作用,不可逆變化過程的不斷積累,造成了結構、應力狀態的不均勻,微凸體成為應力集中源。在應力和應變反覆作用下產生微裂紋,這些裂紋匯合擴展,最後材料以微粒形態脫落形成磨屑。
總之,接觸疲勞破壞的特徵:接觸疲勞失效的特徵與應力狀態、潤滑條件、零件幾何形狀、表面形貌材料的組織結構和性能以及環境和介質的化學作用等因素有關,隨著服役條件和材料性質的改變其失效特徵也隨之而變。根據裂紋起始部位和擴展方式可分為亞表面麻點剝落、表面麻點剝落和深層剝落三種形式。
腐蝕損傷失效
腐蝕損傷是指零件與周圍介質的化學的或電化學的作用而導致的破壞。
金屬零件由於所處的環境以及其材料內部、成分和組織結構的不同,腐蝕破壞形式也不同,如圖4所示。
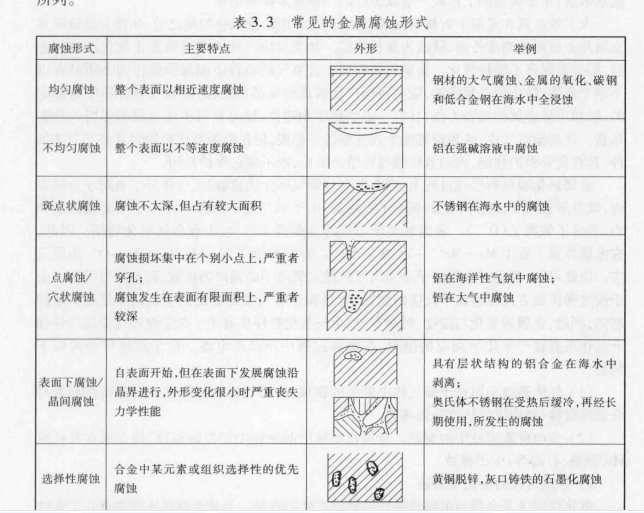
圖4
金屬腐蝕的形式雖然多種多樣,但按金屬與介質作用機理可以分為化學腐蝕與
電化學腐蝕。
腐蝕過程雖然是緩慢的,但危害卻相當大,破壞裝備的正常工作,降低使用壽命,是普遍性的嚴重問題。因此,減輕腐蝕的主要措施有:
(1)正確選材。根據環境介質和使用條件,選擇合適的耐蝕材料,如含有鎳矽、鈦等元素的合金鋼。
(2)合理設計。在裝備製造時,套用較優良的材料,在結構的設計上從金屬防護角度加以全面考慮,努力使整個部位的所有條件儘可能地均勻一致,做到結構合理、外形簡化
表面粗糙度合適。
(3)覆蓋保護層。在金屬表面上覆蓋一層不同的材料,改變表面結構,使金屬與介質隔離開來,用以防止腐蝕。主要方法包括覆蓋金屬保護層、非金屬保護層、化學保護層以及
表面合金化。