專利背景
異丙醇胺包括一異丙醇胺〔1-氨基-2-丙醇,簡稱〔MIPA〕、二異丙醇胺〔1、1′亞氨基-2-丙醇,簡稱DIPA〕及三異丙醇胺〔1,1,1″氮基-2-丙醇,簡稱TIPA〕三種同系物產品。異丙醇胺屬烷醇胺類物質,稍有胺的氣味,常溫下MIPA為無色液體,DIPA和TIPA為白色或淡黃色蠟狀結晶固體,易溶於水、
乙醇、
乙二醇及
丙酮,微溶於烴類及乙醚。由於它的分子中既含有氨基,又含有羥基,因此具有胺和醇的綜合性能,是製造表面活性劑、酸性氣體吸收劑及氧氮雜環類化合物的原料,具有廣泛的工業用途。
異丙醇胺有多種合成方法。由於純液氨與環氧丙烷即使在高溫高壓下,反應速度極慢,需有酸、鹼、醇、離子交換樹脂或水等活性基團對反應起催化作用,才能加速反應,水即是首選的廉價催化劑,它與原料氨配製成氨水投入反應。一般而言,採用的氨水濃度越低,即催化劑水的量越多時,合成反應條件溫和。
中國國內多用25%氨水與環氧丙烷間歇反應製取,其中水為催化劑,其反應式如下:

以上反應生成的一異丙醇胺(下簡稱一異)繼續與環氧丙烷反應得二異丙醇胺〔下簡稱二異〕:
以上反應生成的二異繼續與環氧丙烷反應得三異丙醇胺〔下簡稱三異〕:

如果環氧丙烷過量,則〔3〕產物能繼續與環氧丙烷反應生成三異丙醇胺丙氧基醚:
同時氨水中的水也能與環氧丙烷反應生成丙二醇和丙二醇丙氧基醚:
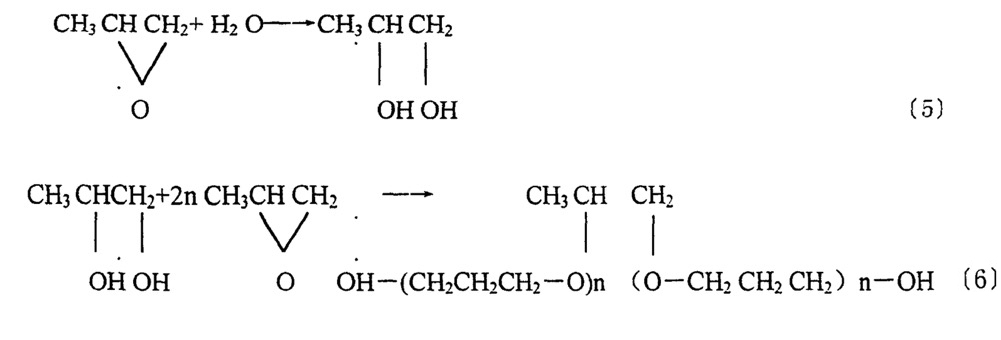
從〔1〕~〔3〕式可知,欲以一、二異丙醇胺為目標產品,必須維持氨與環氧丙烷較高的摩爾比,一般工廠採用10~40:1。當氨水濃度為25%〔W〕時,每噸產品的脫水量達8~40的3倍量。而脫水需消耗大量熱能,同時,大量水的存在會促進〔5〕、〔6〕兩個副反應的發生,造成異丙醇胺的純度下降,不僅使精餾分離工藝複雜化,而且能耗增大。可見傳統的工藝雖然反應條件溫和,但產品純度低,單位能耗高。
中國國外大多採用60-90%〔W〕的高濃度氨水溶液原料,反應壓力控制在6-8兆帕,氨和環氧丙烷比例在10~40:1之間。由於減少了水量,脫水能耗可較大幅度下降,高壓又為閃蒸脫氨供了條件,氨回收能耗也隨之降低。但〔4〕、〔5〕兩式的副反應依然存在,產品純度仍受一定影響。另外,高壓設備投資較高,操作難度增大。
發明內容
專利目的
根據氨與環氧丙烷合成異丙醇胺生產中存在的以上問題,《異丙醇胺生產方法》提供一種異丙醇胺生產方法,目的是提供氨與環氧丙烷的反應最佳工藝條件,使原料氨與環氧丙烷以更低的投料比例,更高的氨水濃度,提高一異丙醇胺的一次合成率,抑制副反應產生,從而提高異丙醇胺的產品純度,節省脫水脫氨過程的總能耗,降低異丙醇胺的生產成本。
技術方案
《異丙醇胺生產方法》以氨與環氧丙烷為原料,在催化劑存在下按如下步驟:將氨、催化劑與環氧丙烷混合後通入管式反應器合成反應,反應後物料經脫氨脫水後得異丙醇胺混合物,然後經負壓蒸餾分離得一異丙醇胺、二異丙醇胺及三異丙醇胺;該發明的特徵在於:所說的催化劑在反應起始階段為水,水與原料氨配製成95~97%〔W〕的氨水投入反應,系統正常運轉後以脫水塔脫出的水與一異丙醇胺混合物為催化劑,投入量為原料氨重量的3~5%;氨與環氧丙烷總投料摩爾比為6~10:1,反應器工作壓力為11~20兆帕,反應溫度為130~180℃,使氨處於超臨界流狀態;原料環氧丙烷為多點分段投入,並通過特製的對撞混合器與原料氨以相對高速噴射的方式均勻混合後入管式反應器反應。
上述合成反應生成物採用二級除氨方案,先入閃蒸塔除去90~95%氨,閃蒸塔壓力0.8-1.6兆帕;余氨通過脫氨塔加熱至100~150℃,壓力降至0.1~0.3兆帕,從塔頂排出,塔內上升的水汽通過塔頂冷凝器冷凝回流。
上述脫氨塔排出的氣氨進入冷阱,以-5℃冷凍液冷卻並用氨壓縮機增壓,以保持脫氨塔壓力在0.1-0.15兆帕。
上述增壓後的氨與閃蒸塔脫出的氨一同冷凝後返回氨罐用作原料。
脫氨後物料通入脫水塔,在-0.06~-0.08兆帕真空下蒸餾分離出水和部分一異丙醇胺,其中一異丙醇胺達30~50%,排出的水和一異丙醇胺混合物返回至氨原料罐作為催化劑使用。
脫氨脫水後物料負壓精餾的三個塔的工作壓力為;一異塔-0.09~-0.098兆帕;二異塔壓力≤-0.098兆帕。三異塔壓力≤-0.0986兆帕。
一異塔塔頂分離獲得的高純度一異丙醇胺可作為商品出售,也可根據需要將它全部或部分通入轉化反應器,按一異丙醇胺與環氧丙烷的摩爾比為3~6的比例加入環氧丙烷,在溫度∠170℃,壓力0.5~1.0兆帕下轉化為二異和少量三異,反應後的轉化液返回一異塔重新蒸餾分離。
該發明環氧丙烷分段投入的段數以四~六段為宜。
管式反應器採用向夾套內通入高溫熱水,在夾套上方的汽包內通過對飽和蒸汽壓的調控來控制反應器工作溫度。
脫氨塔的塔釜熱源大部分來自管式反應器夾套的廢熱蒸汽。
改善效果
《異丙醇胺生產方法》中,合成反應採用的溫度和壓力高於氨的臨界溫度及臨界壓力,使氨處於超臨界流狀態,確保物料在高溫下快速反應。該發明方法將脫水塔脫出的混有一異的水全部返回氨原料罐作為催化劑使用,通過利用異丙醇胺分子的-OH活性基團代替水作為催化劑,從而可進一步提高原料氨水濃度,消除〔4〕、〔5〕兩個反應的產生,使一異、二異產品純度得以提高到99.5%;此方案還可避免脫水塔的污水排放,實現清潔生產;同時還使脫水塔降低塔的高度,節省了能耗。環氧丙烷多點投入,是為了維持每一段的高氨環比,以總氨環比為8:1為例,環氧丙烷分四點投入,則實際氨環比第一段為32:1;第二段為31:1;第三段為30:1;第四段為29:1;可見環氧丙烷多點投料可使實際反應的氨環比提高,從而有效地限制了反應物中三異丙醇的生成量,維持較高的一異生成率。試驗證明最終反應物中三異丙醇的生成量在3%左右,而反應式〔4〕的產物測不出。此外,該發明中,原料氨和環氧丙烷在特製的對撞混合器中快速對撞混合,使環氧丙烷在極短的時間內均勻地分散到液氨中,避免環氧丙烷產生較大液滴而造成局部高濃度,有利於生成〔1〕式反應而抑制〔2〕、〔3〕、〔4〕式反應的發生,因此在較小氨環比下也可提高合成產物中一異丙醇胺的比例。該發明採用二級脫氨的氨回收流程,第一級閃蒸脫氨通過將高壓氨流的壓力驟降,主要利用氨自身攜帶的反應熱氣化,未反應氨的90~95%由此脫除,並可用常溫循環冷卻水使氣氨冷凝為液體,利用位差回收至原料氮罐,無需消耗能源。其餘5~10%的氨利用來自管式反應器夾套的廢熱蒸汽加熱蒸發,並用氨壓縮機將低壓氨蒸汽壓力提升至1.0-1.6兆帕後冷凝回收,-5℃冷凍僅滿足氨壓縮機工作條件,未發生相變,且這部分氨的量小,故氨的總回收能耗仍有大幅度降低。
綜上所述,該發明方法使高氨濃度和低氨環比投料方案的切實可行,從而避免產生副反應,提高了異丙醇胺產品的純度,節省了脫氨脫水能耗,大大降低了異丙醇胺的生產成本。
該發明生產異丙醇胺的方法專用的對撞混合器結構如下:混合器本體的中心設有上、下相對的兩個噴咀,本體內以上下兩噴咀軸線為中心,依次徑向設定振盪區、折流區和混合區,各區在混合器內依次環形分布並相通,其中環形混合區是截面為圓形的環形空間;環形折流區是截面為直角波形曲折的環形空間,圓形振盪區上下均為平面,上下噴咀分別以垂直於該兩平面的方向與振盪區相通,混區合區通過出液通道與器外相通。
該混合器的工作原理如下:氨和環氧丙烷分別從兩噴咀相對噴入振盪區,在兩股液流經噴咀提高流速後相向撞擊,進入振盪區後,沿水平徑向擴散並振盪混合,隨著擴散面積的擴大,流速減慢;進入折流區,液流繼續徑向擴散時與曲折的彎道壁不斷碰撞,從而進一步均勻混合;液流進入混合區沿徑向撞擊器壁後返混,混合區同時把液流匯集至出液通道流出,進入下一段反應器。
採用該混合器,原料氨和環氧丙烷實現激烈對撞,快速混合,使環氧丙烷在極短的時間內均勻地分散到液氨中,避免環氧丙烷產生較大液滴而造成局部高濃度。
附圖說明
圖1是《異丙醇胺生產方法》異丙醇胺生產流程框圖。
圖2表示管式反應器段間組合流程示意圖。
圖3、圖4是對撞混合器的結構示意圖,圖3是圖4的A-A剖視圖。
異丙醇胺生產流程如圖1所示,按原料氨重量的3~5%配入脫水塔的塔頂采出物,與原料環氧丙烷混合,入管式反應器進行高壓合成反應,反應後物料經閃蒸脫除大部分氨,經低壓蒸餾脫出余氨,脫出的氨入氨壓縮機增壓後與閃蒸脫出的氨一同經蒸發冷凝器冷凝後返回作原料氨。除氨後物料經脫水塔,脫出的水和部分一異丙醇胺全部返回配料系統作催化劑使用。脫水後物料入一異塔,蒸出一異後入二異塔,蒸出二異產品後入三異塔,塔頂蒸出三異產品,塔底排出殘渣。一異塔塔頂分離出的一異可作為產品,市場需求二異和三異,可將全部或部分一異物料通入液相轉化反應器,加入環氧丙烷繼續反應轉化成二異和少量三異,液相轉化後物料回一異塔再分離。
圖2通過管式反應器段間組合流程說明原料的投料過程。如圖2所示,若干個管式反應器3依次串聯相通,該例中環氧丙烷分為四段進料,每段的投料口設有對撞混合器1和靜態混合器2,氨的總投料量在第一段中一次投入,環氧丙烷則按總投料量的均分,每段投入總量的1/4環氧丙烷,與上一段的反應流出物從對撞混合器的軸向方向相對噴入混合器內,達到充分混合,然後通過靜態混合器2輸入本段反應器內進行合成反應,末段反應器流出的物料去閃蒸塔。
圖3、圖4表示對撞混合器的結構。該對撞混合器的本體1是由上下兩塊金屬體密封連線而成,本體內含有依次相通的振盪區5、波形折流區6、容積擴大的混合區7、出口管8,噴咀2和噴咀4。上噴咀2和下噴咀4從垂直方向相對通入振盪區5。圖中3是密封墊。
權利要求
1.《異丙醇胺生產方法》以氨與環氧丙烷為原料,在催化劑存在下按如下步驟:將氨、催化劑與環氧丙烷混合後通入管式反應器合成反應,反應後物料經脫氨脫水後得異丙醇胺混合物,然後經負壓蒸餾分離得一異丙醇胺、二異丙醇胺及三異丙醇胺,其特徵是在反應起始階段以水為催化劑,原料氨與催化劑水配製成95~97%〔W〕的氨水投入反應,系統正常運轉後以脫水塔脫出的水與一異丙醇胺混合物為催化劑,投入量為原料氨重量的3~5%;氨與環氧丙烷總投料摩爾比為6~10:1,反應器工作壓力為11~20兆帕,反應溫度為130~180℃,使氨處於超臨界流狀態;原料環氧丙烷為多點分段投入,並通過特製的對撞混合器與原料氨以相對高速噴射的方式均勻混合後入反應器。
2.根據權利要求1的異丙醇胺生產方法,其特徵是合成反應生成物採用二級除氨方案,先入閃蒸塔除去90~95%氨,閃蒸塔壓力0.8-1.6兆帕;余氨通過脫氨塔加熱至100~150℃,壓力降至0.1~0.3兆帕,從塔頂排出,塔內上升的水汽通過塔頂冷凝器冷凝回流。
3.根據權利要求1的異丙醇胺生產方法,其特徵是脫氨塔脫出的氣氨進入冷阱,以-5℃冷凍液冷卻並用氨壓縮機增壓,以保持脫氨塔壓力在0.1-0.15兆帕。
4.根據權利要求3的異丙醇胺生產方法,其特徵是增壓後的氨與閃蒸塔脫出的氨一同冷凝後返回氨罐用作原料。
5.根據權利要求2的異丙醇胺生產方法,其特徵是脫氨後物料通入脫水塔,在-0.06~-0.08兆帕真空下蒸餾分離出水和部分一異丙醇胺,其中一異丙醇胺達30~50%,排出的水和一異丙醇胺混合物返回至氨原料罐作為催化劑使用。
6.根據權利要求1的異丙醇胺生產方法,其特徵是一異塔塔頂分離獲得的一異丙醇胺全部或部分通入轉化反應器,按一異丙醇胺與環氧丙烷的摩爾比為3~6的比例加入環氧丙烷,在溫度≤170℃,壓力0.5~1.0兆帕下轉化為二異和少量三異,反應後的轉化液返回一異塔重新蒸餾分離。
7.根據權利要求1的異丙醇胺生產方法,其特徵是環氧丙烷分段投入的段數為四~六段。
8.根據權利要求1或2或3或4或5或6或7的異丙醇胺生產方法,其特徵是管式反應器採用向夾套內通入高溫熱水,通過對汽包內飽和蒸汽壓的調控來控制反應器工作溫度。
9.根據權利要求8的異丙醇胺生產方法,其特徵是脫氨塔的塔釜熱源大部分來自管式反應器夾套的廢熱蒸汽。
實施方式
實施例
含水3%的原料氨水232千克/時和19.2千克/時的環丙分別用泵輸送,在11.0-20.0兆帕下進入對撞混合器,混合後的原料進入預熱器,預熱到100-130℃進入第一段高壓管式反應器,反應溫度140-170℃,反應在等溫下進行,等溫反應器夾套內通有熱水,熱水攜帶的反應熱在汽包中產生部分低壓蒸汽,反應溫度由汽包壓力控制。一段反應器出口物料與二段進料的環氧丙烷在二段對撞器混合器迅速混合後進入二段反應器。同樣方法進行三段、四段的投料。四段反應器物料出口由一個調節閥總調反應壓力,四段反應器出口壓力為15-16兆帕。
四段出口物料經節流進入閃蒸塔,閃蒸壓力為1.0-1.4兆帕,加上蒸餾塔底再沸器蒸發,未反應氨的90-95%由此汽化蒸出,經蒸發冷凝器冷凝成液氨後返回原料罐重複使用。閃蒸塔釜液進入脫氨塔,在0.1-0.3兆帕下操作,蒸出殘餘的未反應氨,此氨用氨壓縮機升至1.0-1.4兆帕後與閃蒸塔氨蒸汽一同冷凝並返回使用。脫氨塔釜液的組成為一異60-62%(質量不同),二異30-32%,三異占3%左右,水3%,其餘為含氨基的高沸物。
脫水塔釜液經-0.06~-0.08兆帕真空下蒸餾脫水,脫出的水中含有部分一異,將脫出的一異和水返回作催化劑使用。脫水塔釜液送入一異塔,在-0.098兆帕真空下將一異從塔頂分離出來,此一異可以作為產品出售,也可通過液相管式反應器再與環丙反應生成二異和三異,轉化過程中,二、三異的比例可通過一異、環丙的投料比在一定範圍內調節。例如,一異與環丙的摩爾比在4-5時,可以獲得和高壓反應液中二、三異的相近比例。該液相轉化反應液返回一異分離塔,一異塔釜液進入二異分離塔,二異塔頂得到高純度二異產品。二異塔釜液進入三異分離塔,從三異塔的精餾段得高純度的三異產品,塔頂液返回一異塔釜液罐,塔底少量殘液排除系統。一異塔、二異塔、三異塔要求的真空度是遞增序列。
如果一異全作產品出售,上述規模的裝置每小時可得一異60公斤,二異30公斤左右,如果一異全部轉化為二異和少量三異,則每小時可得二異130公斤,三異8-10公斤左右。
榮譽表彰
2007年,《異丙醇胺生產方法》獲得第五屆江蘇省專利項目獎優秀獎。