“潤滑經濟”是指通過套用先進潤滑技術,顯著提高機械設備的極壓抗磨性能,減少摩擦磨損,減少動力損失,延長潤滑介質壽命,降低惡性機械事故發生機率,延長設備壽命,減少能耗,提高能效,減少排放,實現巨大經濟效益,其投入所產生的綜合效益遠高於1:100。套用先進潤滑技術帶來的不僅僅是直接節能,而且可以實現每道工序、工業環節及各產業鏈重複循環節能增效,改變機械設計、製造和套用及管理理念,改變石油煉製、冶金、機械製造、運輸等基礎產業結構,改變經濟成長方式,甚至改變人們的生產生活方式。
“潤滑經濟”,對我們的啟示,實現“潤滑經濟”的重要保證,“潤滑經濟”效應和國家利益分析,簡介,節約,增效,安全,巨觀效益,戰略意義,先進潤滑技術節能是低碳發展第一戰略,潤滑經濟的企業效益,提高資源利用率,摩擦付長壽命,變廢為寶,用油高性能化,安全保障,變被動維修為主動維護,潤滑技術發展帶來了新曙光,納米材料,金屬磨損再生技術,氟特加氟碳表面改性塗層材料,傳統理念束縛,必須突破部分企業領導、管理人員對潤滑偏見,必須突破目前企業管理者只認購廉價油,突破目前企業一出現故障只從備件上找原因,必須突破“三無”現象,
“潤滑經濟”
“潤滑經濟”背後的國家利益
1何謂“潤滑經濟”,能源消耗到哪裡去了?
從古埃及“金字塔”的建造到現代工業大發展,幾乎所有運動的設備裝備都需要潤滑。“潤滑經濟”是指通過推廣套用先進潤滑技術實現節能、降耗、減排和增效,拉動相關設備設計、製造和套用等基礎產業發展,實現巨大的經濟價值和社會效益。
能源消耗究竟到哪裡去了?國際權威機構測算,世界能源的30%-50%消耗於摩擦磨損,潤滑不良造成的材料磨損占60%以上,而且50%以上的機械裝備惡性事故大都源於潤滑失效造成的過度磨損。採用先進潤滑技術,可減少摩擦磨損,降低機械裝備惡性事故的發生,從而實現直接節能,並為產業鏈的各個環節創造價值,提高經濟效益。
中國工程院《摩擦學科學及工程套用現狀與發展戰略研究》(2009年3月第一版)報告指出: 2006年我國工業領域因摩擦磨損造成的損失約9500億元人民幣,僅汽車行業,按2006年乘用車數量計算,套用先進潤滑技術可節約汽油500萬噸,約占乘用車汽油消耗總量的10%;載貨車可節約柴油近900萬噸,約占載貨車柴油消耗總量的8-10%左右。報告還稱,歐美已開發國家因摩擦磨損造成的損失約占其國民生產總值的2-7%。目前,我國的經濟發展模式尚比較粗放,資源浪費嚴重,套用先進潤滑技術節約的潛力應遠遠大於歐美已開發國家。
因此,如果在我國全面推廣套用先進潤滑技術,我國的國民生產總值不僅可大幅度增加,而且可以降低各工業環節的單位能耗,產生巨大的“潤滑經濟”效應。所以說,“潤滑經濟”下的先進潤滑技術產業化發展,是促進國家經濟長期穩定增長的重要戰略和技術手段,必將對我國社會經濟的發展起到巨大推動作用。
對我們的啟示
潤滑是一個古老而又不斷發展的課題,《詩經·邶風·泉水》中有“載脂載宣,還車言邁”的詩句,表明中國在春秋時期已套用動物脂肪來潤滑車軸。西晉張華所著《博物志》提到酒泉的延壽和高奴有石油,並且用於“膏車及水碓甚佳”,這是套用礦物油作潤滑劑的最早記載。從人類開始大規模使用石油產品作為潤滑劑即礦物油潤滑,到添加多種添加劑以改善抗氧化、耐低溫、抗磨損性能的第二代潤滑技術,再到第三代的低粘性、高性能和長壽命潤滑技術,人類經歷了一百多年的時間。
20世紀60年代中期,英國工業飛速發展,雖然政府投入很大,但能耗卻很高,於是英國女王專門委派大臣組織調查,結果發現英國的企業由於對潤滑、摩擦和磨損知識的了解和套用不夠而損失重大。據測算,改進這方面的教育、研究和套用,英國每年可節約5億英鎊以上,這還僅僅限於直接效益方面。另外,調查組與牛津大學出版社英文字典部磋商後,還創造了“TRIBOLOGY”這個新詞來表達潤滑、摩擦和磨損這門綜合學科的內涵,其中文譯名為“摩擦學”,我國台灣省譯成“摩潤學”。此後,摩擦與潤滑學作為一門獨立的學科受到世界各國工業界和教育研究部門的普遍重視,摩擦與潤滑學研究進入了一個新的發展時期,並且共同認為先進潤滑技術才是節能降耗的根本所在。但是解決摩擦磨損的先進潤滑技術並沒有引起我國政府的足夠重視。
經過科學家和工程師的多年努力,20世紀90年代出現的納米潤滑材料摩擦學標誌著摩擦、磨損和潤滑的研究進入了一個嶄新的階段。從以傳統潤滑油以粘度為重點的流體潤滑理論和極性分子與金屬表面形成吸附膜的邊界潤滑狀態,以及隨後的化學變化的極壓潤滑狀態,改變為從分子、原子尺度上揭示摩擦磨損和潤滑機理, 建立材料微觀結構與巨觀特性之間的構性關係和定量準則,並確認厚度從微米量級擴展到具有高耐磨特性和優異潤滑性能的納米量級薄膜潤滑。由此開始了“薄膜潤滑” “納米潤滑”理論研究。同時專家特別指出,“極壓抗磨”性能的突破才真正是潤滑技術的核心突破,才是潤滑技術的根本革命,才能使潤滑產品生產工藝、性能、套用和管理髮生徹底改變,才能引發工業環節的節能、減排、和增效。因此,潤滑技術將在我們的生活中扮演更為重要的角色。
3核心技術突破是
實現“潤滑經濟”的重要保證
潤滑油技術的發展主要來自兩個方面,一是改進基礎油的品質,二是提高潤滑添加劑的性能,並且後者發展空間巨大,也就是說,添加劑是改善潤滑油性能的核心和關鍵所在。潤滑產品的每一次升級換代都是在添加劑技術獲得突破基礎上實現的。現代先進潤滑技術的突破,應該在提高潤滑油極壓承載能力的前提下,進一步提高摩擦副的抗磨和減摩性能,達到延壽和節約能源的目的。
以前,為防止設備軸承和齒輪等摩擦副表面的點蝕、擦傷,大多採用大體積的笨重設備以增大接觸面積,減小接觸應力,同時採用高粘度的潤滑油以期形成厚油膜的技術,以滿足衝擊性重負荷、高承載能力條件下抗磨減摩性能的要求。如此以來,過高的潤滑油粘度會帶來一系列的動力損失、摩擦溫升高和散熱困難等問題,使潤滑油變質速度加快,過早喪失潤滑和承載能力,造成機械事故和油品損失,造成低功效、高能耗和高排放。
為了滿足現代設備大功率、低能耗、重負荷、高速、高承載、高可靠性、長壽命運行不維修對流體潤滑油的技術要求,解決邊界潤滑造成的摩擦損失和潤滑油粘度過高帶來的流體動力損失浪費等問題,就必須提高潤滑油的極壓“抗磨減摩” 性能,降低潤滑油的粘度。而潤滑油的油膜強度即極壓“抗磨減摩” 性能取決於潤滑油添加劑的配方和生產工藝技術水平,這是潤滑油品在摩擦化學條件下成膜強度的關鍵,是提高潤滑油極壓“抗磨減摩” 性能的最有效的核心技術,是節能的關鍵技術手段。
長期以來,由於我國缺乏高性能潤滑油脂,工業領域設備的重要潤滑部位只能依靠進口油脂,而這些進口油脂也只是一般理化性能優於國內同類產品,依然不能改變摩擦副之間較大的摩擦磨損狀況,且價格昂貴,但是,企業仍大量進口,浪費了大量國內經濟資源,因此,迫切需要開發具有我國自主智慧財產權的創新技術和提高企業用油工程師的技術水平。已經獲得國家發明專利,保護期長達20年的具有完全自主智慧財產權完全自主創新的“高效節能納米抗磨劑的製備和套用”技術表明,運用納米材料所具有特殊表面和界面效應,將納米級顆粒潤滑油添加劑加入到潤滑油中可極大提高潤滑油的承載能力和抗磨減摩性能。經權威機構檢測表明,該技術支持下的納米抗磨劑粒徑為5-20nm,相應的潤滑油品單位承載壓力高達44000kg/cm2,綜合抗磨性達到國內外品牌潤滑油的210多倍,並可使金屬摩擦副間的摩擦係數從0.12的平均水平最低降低到0.039,按此數據,摩擦功將降低80%以上,即節能可達80%以上。其他專業摩擦磨損試驗表明,與國外知名品牌同類產品相比,摩擦係數至少可減小33.3%,400N壓力下運行60分鐘後摩擦溫升低37%。這些數據表明,採用先進潤滑技術可大大提高節能效果,保守估計可達20%左右。如果在全國推廣先進潤滑材料,不但可以維護我國工業生產線、大型裝備和高速載運工具的運行安全,也可助推我國順利實現節能減排目標。
“潤滑經濟”效應和國家利益分析
簡介
經權威測試和首鋼礦業公司等企業實踐證明,在高耗能的冶金行業、運輸、機械裝備製造以及機械領域先套用進潤滑材料,設備潤滑狀況明顯改善,承載負荷大幅度提高,設備壽命延長,動力損失減少,配件損失減少,管理損失減少,事故減少。採用先進節能潤滑技術可使首鋼礦業公司直接節約電能10%,而直接節能的效益僅占套用該技術應產生總效益的5.46%;延長一倍的潤滑油壽命,節約潤滑油創造的效益占總效益的1.7%;節省的人工費用可占總效益的6.17%;節省的維修費和材料費占總效益的67%;提高效率產生的效益占總效益的19.67%。按可比價格計算,各環節可實現的總效益遠遠超過投入的1:100以上。
套用該技術各項節約占總效益百分率如圖1所示。
圖1 各項節約占總效益百分率圖 如果一般工業企業採用先進潤滑材料實現直接節能1%,就可實現相當於企業利潤10%的綜合效益,如果直接節能10%,就可實現企業利潤翻番。以上計算不包括設備維修固定資產的投入,人員機構的配置、福利、薪酬及其它費用,並且不包括對設備設計、製造、運輸、管理,以及能源等相關產業的拉動作用,還不包括潤滑產品的生產工藝、性能、套用、管理髮生徹底改變帶來的綜合效益。所以說採用先進潤滑技術、產品和加強管理的重大意義是可實現每個工序環節、工業環節及各產業鏈的重複節能增效,經過長期實踐,若按上述潤滑經濟效益計算方法,在目前我國能源和資源消耗水平條件下,如果在全國全面推廣先進潤滑技術及產品,我國的國民生產總值再增加5萬億不是夢想,具體表現在以下幾個方面:
各項節約占總效益百分率圖
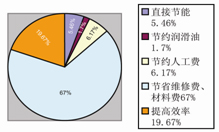
節約
a節電、節省燃油、節省潤滑油、減少易耗件,減少日常值守和保養人員配置;
b減少主機設備等固定資產的投入、減少配件損耗及庫存資金的占用、減少利息支出,減少維修配件,減少維修時間和其它費用;
c減少設備維修固定資產投入和管理人員配備,減少工資福利類費用支出;
d減少機械故障對設備等固定資產及人員造成的傷害以及因此而發生的重新購置、修復、建設、製造、醫療、賠償、誤工損失等善後費用,減少排污治理費。
增效
a提高設備輸出功率,減少失效和事故停機損失,增加因此而創造的效益;
b減少保養性停機時間,提高設備運轉效率、人員效率、管理效率;
c延長設備壽命,減少因設備壽命減少而產生的相關費用;
d提高資金利用率及其產生的相關效益,減少再製造產生的一切費用。
安全
a減少機械故障性停機事故,減少其對設備等固定資產、對人員造成的傷害;
b減少社會的危害和環境的污染;
c減少周轉資金對經營安全的威脅。
巨觀效益
a能源、主機設備、配件、潤滑油、人員的節約;
b潤滑油品單一化,大大簡化現有的生產和管理體制的效益;
b設備的小型化可以推動上下游產業鏈中每個製造過程的節約增效;
c減少報廢材料回收、再製造對資源的浪費和排污再治理費,機構、人員配置及管理費用。
戰略意義
A降低對國外能源和資源依賴程度,減弱國外勢力給我國經濟社會造成的威脅;
b軍事上可延長設備壽命,延長續航里程,提高子彈射程,增強航空母艦用彈射器效率,減少維修類非戰鬥機構、設備和人員配置,降低保障難度,提高戰鬥力。
綜上所述,採用先進潤滑技術,必將帶來巨大的“潤滑經濟”效應,增加國民生產總值,實現國家利益最大化。
先進潤滑技術節能是低碳發展第一戰略
開源和節流是解決我國經濟發展所需動力問題的兩大方面,新能源戰略和節能技術戰略應齊抓共舉,需要提醒的一點是,開發新能源過程中有相當一部分資金將消耗在摩擦磨損上,因此,先進潤滑技術顯得尤為重要。
2009年9月21日和22日,溫家寶總理連續召開了三次新興戰略性產業發展座談會,聽取經濟、科技專家的意見和建議。他強調,重大發現和發明將改變人類社會生產方式和生活方式,新興產業將成為推動世界經濟發展的主導力量。選擇關鍵核心技術,確定新興戰略性產業直接關係我國經濟社會發展全局和國家安全。2010年4月22日,國務院總理、國家能源委員會主任溫家寶主持召開國家能源委員會第一次全體會議,會議明確提出了新時期能源戰略的十六字方針,“節約優先、立足國內、多元發展、保護環境”。可見,節約應成為發展第一要務,如何節約才是解決問題的關鍵。
工業和信息化部李毅中部長曾指出:“我國節能減排要靠結構調整、技術進步和加強管理三種途徑來實現。就節能而言,結構節能是一項長期任務,管理節能要靠日積月累,從某種意義上講,技術節能更具有實效性。在產業結構和能源消費結構一時沒有重大變化的情況下,技術進步、技術創新顯得尤為重要,只有在技術、工藝、設備和材料的創新與套用上取得重大突破,才能在較短的時間內推進節能降耗減排工作再上新台階”。筆者認為,立足近期形勢,著眼長遠未來,技術節能,特別是採用先進潤滑技術節能,才是節能的關鍵,才是節能的根本保證,先進潤滑技術節能應成為低碳經濟發展的第一戰略。
2010年我國能源發展的主要預期目標是:一次能源生產總量約28.5億噸標準煤,到2020年我國單位國內生產總值二氧化碳排放比2005年下降40%-45%,非化石能源占一次能源消費的比重要達到15%左右。根據我國現有的能源需求增長趨勢,如果沒有重大核心技術突破,實現上述目標,難度是非常大的。要實現這一目標,到 2020年我國高清潔能源投資:水電裝機要達到3億千瓦以上,核電投運裝機達到7000萬千瓦以上,風電、太陽能及其他可再生能源利用量達到1.5億噸標準煤以上。如果能源消費總量增長過快,水電、核電、風電及太陽能的發展力度還要更大,否則不可能實觀這一目標。中投顧問發布的《2010-2015年中國核電行業投資分析及前景預測報告》介紹,中國正在加大能源結構調整力度,積極發展核電、風電、水電等清潔優質能源。預計到2020年,國家要投入4萬億資金髮展核電,而核電裝機的比重僅占電力總容量9億千瓦時的4%。除了這些清潔能源,在傳統能源領域,我國到2020年要投入2000億元,開發近海石油,增加產能5000萬噸,相當於增加新能源7143萬噸的標準煤,占能源消耗總量的2.5%,投入產出比略高於1:1。新能源的建設需要大量投入,建設和運行過程還要消耗大量資源、能源,甚至造成新的環境污染。如果將中海油投入的0.1%-1%的資金投入到先進潤滑技術產業,加快先進潤滑技術的全面推廣套用,發展 “潤滑經濟”產業,我國每年直接節約的能源可占能源消耗總量的5-10%,其產生的綜合效益是GDP總值的15%以上,相當於目前我國經濟發展水平條件下GDP可再增加5萬億元。
因此,先進潤滑技術節能顯得尤為重要,就目前我國的發展水平來講,如果採用先進潤滑技術,就能在較短的時間內實現節能降耗工作的突破,降低工業生產鏈上的能源消耗,降低運行中裝備的能源消耗,降低汽車行駛過程中的油耗,同時降低材料的摩擦磨損,緩解鐵礦石供應緊張局面;如果採用完全自主創新的具有完全自主智慧財產權的先進潤滑技術,將特別有助於實現我國高速鐵路機車運行的高安全性,消除對某島國潤滑油品的依賴性;將特別有助於實現我國風電核心部件的長壽命,保證其安全穩定運行;將特別有助於實現我國特殊野外載運裝備的高可靠性,提高機動性能,提高打擊能力,擴大作戰半徑。這些都具有非常重大的現實和戰略意義,對我國經濟社會發展意義重大,影響深遠。採用先進潤滑技術,普及先進潤滑技術知識,加強管理和培訓,不僅可以節約大量能源和資源,而且可以改變管理理念,改變企業甚至社會的經濟成長方式,實現低碳經濟發展。綜上所述,可以肯定先進潤滑技術的推廣套用,必將催生節能環保型新興戰略產業,必將助推早日實現節能減排目標。先進潤滑技術產業化發展也必將引起全社會的廣泛關注,產生巨大“潤滑經濟”效應,實現國家最高利益。
潤滑經濟的企業效益
提高資源利用率
就國內資源而言,我國石油、天然氣、煤炭,可采儲量為例,僅為世界 4% 、 5% 和 57% 。能源短缺是我國經濟社會軟肋。更為嚴重的是我們資源利用率僅為 30% 。有人形容這好比是:“吃一碗、倒二碗”。我國固定資產原值達 10 多億元,這么多設備只要一運轉就有摩擦,有摩擦就有磨損,有磨損就有潤滑,可謂面大,涉及到國民經濟各個部門、行業。但所用潤滑材料確有本質上不同。日本通過節能潤滑設計和操作,以及採用節能型潤滑油脂措施,使機械磨損大大降低,節能動力 10%--20% [3] 。再比如交通運輸用油占石油總耗 45% ,汽車機械耗能 68% 消耗在摩擦付上,如合理潤滑正確開展摩擦學設計、節約效果,將十分明顯。據報導,汽車發動機磨損 60% 發生在起動初期,如使用多級油後,即可減少油料消耗 5---10% ,就是冷凍起動,也能得到良好潤滑。美國 90% 以上汽油機, 60% 柴油機。日本 100% 汽油機, 52% 柴油機,均使用多級油。我國前幾年報導,汽油機 13% ,柴油機 16% 。可見潛在節能效益。節能也表現在間接上,一出設備從原料生產、冶煉、軋制、鑄造、機加、裝配整個過程都要效耗大量能源,如果我們通過摩擦學設計以及運行中對油品維護,就可以大幅延長設備壽命,使得一台設備等幾十台用。這些間接節能僅以用數字計算嗎?
摩擦付長壽命
近年來陸續有報導,由於油品污染造成的損失數目驚人。如某礦山新油運到礦井地面,其污染度已達到 NASIO 級。某礦務局從國外引進綜采機組由於油液污染嚴重,短短的幾個月時間內,就有數十台液壓泵和液壓馬達損壞,造成直接經濟損失幾十美元。某築路單位從國外購買卡特公司各種工程機械達幾百萬元,由於使用時不懂維護,短短的幾年造成液壓閥組卡咬,動作失效,換成國產閥組至今處於出工不出力狀態。國內外資料表明,液壓元件失效 70---85% ,歸因於油品污染,變質。這其中除了管理上問題外,還由於近年來液壓潤滑元件精密程度越來越高,運動間隙變小,對超細微粒越來越敏感所致,加之一些用油單位不認識,又沒有檢測手段造成事故頻繁。通過國內外大量實際研究證實了油品本身質量外,常與管理維護不當使油污染有關,要在油品高清潔度上下功夫,必須有一個與使用設備相適應的高效潤滑過濾系統,把污染物及時分離出來。
SKF 軸承製造商是世界最負有盛名的公司,它們通過大量試驗,深入研究了負荷、油液粘度、顆粒污染物等各種因素對軸承壽命的影響並得出結論:即清除潤滑油中 2---5 微米固體顆粒,滾動軸承疲勞壽命可延長到原來的 10---50 倍。根據發動機綜合研究理論,使用改良後的清潔型機器潤滑油將發動機壽命延長 8 倍。 1997 年 BHP (澳大利亞墨爾本大學維護技術研究院)鋼鐵維修委員會在日本 BHP 鋼鐵公司兩大軋鋼廠中,通過運行中潤滑問題的研究,在 1975 年 ----1985 年間 NSC 鋼廠設備故障率由每年 342 起減少至 85 起。設備故障率減少 87% 。又在此期間通過在全廠範圍內實行潤滑污染預防控制工藝,取得了顯著效益。全廠範圍內軸承購買率減少 5% ,液壓泵更新率減少 80% ,潤滑油消耗減少 83% ,潤滑故障頻率減少 90% [4] 。我國天津港務局是外貿主要港口之一,現有 66 個泊位,各類機械 2272 台(套),船舶 44 艘,設備固定資產總值達 17 億元,該局從 20 世紀 90 年代開始抓油液淨化工作,使得各種發動機,鏟車、吊車、裝載車故障明顯下降。停機維修損失大為減少,每年節約油料和維修成本高達 500 萬元。當前,已有單位,甚至將新進油品(當然不是高清潔度油)先過濾達到污染度等級再用,針對這一全球技術課題,美國一公司提出了“全面清潔度控制”( TCC )的理念,旨在從單個零件的生產系統開始運行及今後的工作壽命的整個生產過程中,降低污染物發生率及其影響與全面質量管理( TQC )相似, TCC 也需要“全過程、全系統、全體人員”參加,特別是液壓系統,其失效除了系統本身質量不合格外,往往與系統管理工作不落實有效規章制度,規範,未能實施有關。因此,要想真正落實 TCC ,必須做到“三全”管理才行。目前我國高清潔度油生產不多,就是生產多,在運行過程中,也必須線上過濾才算最好。因為將油中顆粒物分離出去,會使軸承疲勞壽命提高 10----50 倍。這種易於得到巨大效益,何人不要呢!一台濾油機過濾裝置有幾萬元就可買到,顯然投資是很少的。關鍵是認識問題。
變廢為寶
所謂廢油是指各種潤滑油在不同機械設備使用過程中,因受到污染,氧化等因素,改變了原來的各項性能指標,不能繼續用而換下來的油,這些廢油如內燃機油,在工作時,活塞頂部溫度可達 300℃ 以上,部分烴類反應成了 3.4 —苯並芘等多環芳烴化合物,它們一部分隨廢油排入大氣,一部分留在油中,隨廢油排出。因此礦油不降解,倒入土壤中,導致植物死亡,進入水源,則污染飲用水。而且 3.4 —苯並芘在水中溶解度很小,但可溶解許多有機溶劑中,它通過人體和動物的表皮滲透到血液中,並在體內積累,導致各種細胞喪失功能,是當今由各種渠道排放到環境中多環芳烴成為對人類威脅的最大致癌物。全世界每年排放的 3.4 —苯並芘高達 5000 多噸,給環境造成極大影響。為了減少廢油在土壤和水中積累, 1991 年歐盟要求用於公共土木工程機械和液壓設備一率用可降解液壓油。瑞士立法禁止在森林、水源、耕地使用非生物降解潤滑油。如果我們將這些廢油通過符合環保的辦法,如無酸化廢油再生技術,就可使一些廢油變廢為寶。但必須禁止那些仍沿用對環境造成危害的硫酸 / 白土老工藝處理廢油。現在一些單為處理廢油一是倒掉,二是賣給二道販子。很少自己回收。我國是潤滑油生產和消費大國,每年生產和消費得 400 萬噸,只廢油回收每年就達 100 萬噸。如果處理好,是一筆很大財富。 60 年代美國廢油再生處理產量相當新油 18% 。潤滑油在原油提煉過程中,僅很小比例。而且非任何原油均可提煉。廢油回收工藝簡單,投資少,收效快。
用油高性能化
當今機械設備發展的趨勢,正向著重量輕、體積小、負荷大、效益高、長壽命發展。潤滑油必須更新換代,來適應設備向高參數發展,首先油中加了高效添加劑,形成了吸附膜層,稱吸附膜邊界潤滑,對負荷低轉數,低滑動速度,摩擦部件上比流體潤滑膜更為穩定和可靠的潤滑作用。一般情況下,邊界吸附膜厚度約 0.1----1nm 。吸附膜油膜強度優於流體潤滑,但在更高溫度和負荷下也會失效。油中加有硫、磷、氯等極性物質,通過與金屬表面反應形成的化學反應膜進行潤滑,極壓反應膜適用於高溫和重載時等苛刻條件下潤滑。由於潤滑機理髮生變化,傳統靠油的粘度選油,已不在是唯一條件了,油品的高性能化帶了可觀的效益,如將鈣基脂改用相同稠度的鋰基脂,換油期可提高 6 倍, 1ig 可當 6ig 用,將普通 HL 液壓油改用相同粘度抗磨液壓油 HM 。泵的壽命可提高 10 倍, 1 台泵等 10 台泵用。對於這種變化意味著這裡蘊藏巨大經濟效益。實際上也就是換一換油,沒有更大投資,懸殊的投入與產出的比例,是任何從機械和備件上下功夫的人想向不到的。
安全保障
生產必須安全,安全為了生產。潤滑油的改革升級解決不少企業安全隱患。如汽車制動液是制動系統中傳遞壓力制止車輪轉動的液體,其質量好壞,直接關係到行車安全。目前市場上制動液比較混亂。 1998 年國家技術監督局公布顯示,我國汽車制動液合格率當時僅為 41.7% 。最近江西質量監督局又公布了檢查結果,近六成剎車液安全不達標。如運動粘度不達標,流動潤滑性能差,冬季出現制動滯後現象,制動液易汽化產生氣阻,導致制動疲軟。就制動液而言分醇型,礦油型和合成型三類。醇型制動液價格低,高低溫性能差。我國 90 年 5 月已淘汰。但至今市場應有生產和出售。礦油型加了增粘劑,抗氧劑,防鏽劑調和而成,適應性比醇型好,但對天然橡膠有溶脹作用,使用時,應將皮碗軟管換成耐油橡膠製品。合成型通常以乙二醇醚,二乙二醇醚、矽油等加入添加劑組成,適應工作溫度寬,粘溫性好,對橡膠相溶性好,適合高速、大功率、重負荷頻繁制動,是目前使用最多的一種。
再比如,工礦使用鋼絲繩,筆者下現場看到有些用量較大的單位,更換下來鋼絲繩堆積如山,鋼絲繩作為提升、拉拔、牽引的載體,由於在使用時受到拉拔,扭轉、負載突變,時斷時續,風吹日曬,雨淋,工況十分惡劣,特別是室外,出廠時,鋼繩中間有油芯,可儲油進行鋼絲之間潤滑,但實際效果並不理想,出現斷絲、銹絲、乃至突斷,造成惡性安全事故。現在由於研究出可滲透性鋼索油,不但解決了鋼絲之間潤滑,同時使鋼絲表面與導輪間潤滑也得到解決。大連北良港用進口可滲透鋼索油,取得滿意效果。
再比如,我們用量較大往復空壓機油,過去用 13# 、 19# ,由於積炭重,常出安全事故。現在生產的 DAA 、 DAB 、 DAC 空壓機油比 13# 、 19# 積炭減少 4/5 。大大減少因積炭過多,造成爆炸事故。
變被動維修為主動維護
維修第一。在我國多年每個企業都有一批維修人員和庫有備件。一但出現故障就搶修,似乎成為我國部分企業的維修模式。但先進的主動維護方式的出現,將對傳統模式一大衝擊。主動維護是對導致設備損壞根源性參數進行監測並控制,延遲失效發生,把故障的苗頭消滅在萌芽之中。最大限度減少停機,達到相對成本低的一種維護方式。一些已開發國家,就已開始使設備周期費用達到最經濟。就設備來講,從事後維修、定期維修,到預防維修,發展到維護型,適應性維護,其核心是把設備周期費用降到最低。潤滑技術的發展適應了這一形勢。潤滑劑使用不當,造成摩擦付過度磨損,裝配精度破壞、升溫、振動、噪音接鐘而來。最後導致無形磨損和突發事故。當今機械化自動化程度越來越高,許多設備維修工所能做的就是“換一換油”,像過去那樣大拆大卸已不可能。
國外已有 LCC 周期達到不解體大修。這裡關鍵在維護。正確選油變成十分重要。運行中的油品監測、淨化、過濾變成日常工作。實為液體維護技術,這些都是提前進行的。如我國青島港務局前港公司 CAT 裝載機不解體維修超過 15000 運行台時,佳友 DC---25 輪胎起重機不解體維修達 35000 台時。就是在潤滑劑上先下了功夫。當然主動維護雖然成本低,也需要時間和資金的投入,但忽視所帶來的將是更大的資金和時間的投入。有人估計主動維護所產生的綜合經濟效益所謂投入與產出之比大於 10 ,但從國外一些資料看,遠遠超出比數。未雨綢繆,事半功倍。
潤滑技術發展帶來了新曙光
納米材料
隨著時代的發展、技術的進步,潤滑油性能必須隨之改善和提高。其中包括對傳統潤滑油抗磨進行改進,並開發新的抗磨劑來滿足,降低硫、磷含量又能提高其性能。納米金屬抗磨劑,納米金屬修復劑,出現了無機油運行,據最近報導有一種叫路邦納米抗磨劑有 5000 公里 無機油運行記錄。為什麼有這么神奇效能。綜合各種學說,大致有納米粒子與摩擦表面起到類似滾珠的作用,叫“共晶滾球膜”,將滑動摩擦變為滾動摩擦,大大降低摩擦係數。還有認為納米粒子與摩擦表面生成化學反應膜適應高溫、重載、低速等工況。納米潤滑油抗磨劑比微米級抗磨、減磨效果更好。有人認為,套用納米材料製備的添加劑。可以解決常規載荷添加劑無法解決的問題。
金屬磨損再生技術
目前以“ ART ”和“摩聖”為代表的金屬磨損自修復材料,經過多年廣泛試用,取得比較令人滿意效果。金屬磨損自修復材料不同加在潤滑油中改性添加劑,又是以潤滑油為載體,也不是生成滾球減磨層,據推廣單位介紹是直接在摩擦能轉換成熱能的部位上生化學置換反應,生成金屬陶瓷層,經過這樣處理後的金屬表面有極高顯微硬度和極低表面粗糙度,抗腐、抗磨大幅延長裝備使用壽命,節約能源,還能修復長期運轉中的機械零件磨損表面。這種表面處理方法是目前各種類型油料添加劑無法做到的。
氟特加氟碳表面改性塗層材料
是前蘇聯根據太空飛行器在太空惡劣環境下要求摩擦材料必須達到無固體顆粒,不改變機械公差,化學穩定性和熱穩定性高,減摩抗磨效果好,綜合性能持續時間長,而開發一種新的塗層材料,據說在塗到固體表面時形成一薄層( 4---8 納米)分子膜,但不是化學反應膜。這種膜的消失只在兩種情況下出現:一是工作溫度持續超過 450℃ ,二是隨著基礎材料流失而流失。處理後的表面耐壓及承載力達到 3000 兆牛 / 平方毫米。 P B 值由 94kg 提高到 114kg ,降低摩擦係數 75—90% 。膜層自修復,而成膜速度快,僅需 10 分鐘。高速機械 1000 小時膜持久存在,而且不同於一般在於它對工業橡膠製品經氟特加處理後工作壽命(抗老化和耐磨),經處理過的塑膠製品(如聚四氟乙烯塑膠)可明顯提高耐摩擦、耐油、耐老化特性。因此,此種塗料對改善機器、工具機、工藝裝備,金屬材料、切削工具、發動機、壓縮機、發電機、船舶、車輛均有實效。
傳統理念束縛
必須突破部分企業領導、管理人員對潤滑偏見
現在的潤滑已跳出原來的純技術,進入到設備管理、生產管理,直接進入到企業管理行列中。它已涉及到增效、節能、環保和安全諸項企業管理大項。因此企業中高層決策者必須首先接受培訓,轉變觀念,提高認識,特別國家調整產業結構上,節約能源是一種無可選擇的選擇,科學用能,才能完成“十一五”,比“十五”能耗下降 20% 的硬指標。在當前情況下,國人必須重新認識“潤滑”,並給以恰當的定位。當今設備正趨向體積小、功率大、壽命長、自動化程度高,各項指標向高參數發展,潤滑肩負的使命更為突出。如高性能添加劑,納米添加劑,金屬自修復材料以及氟特加塗層,這些加在油里後,使摩擦付形成各種“膜”、“層”、幾倍、十幾倍提高了摩擦付的承載耐磨能力及其他功效。這顯然是原設備設計者,維修工作者及設備管理人員無法想像的。也是從事機械工作的同仁們單純從材料、熱處理、加工上仍沿傳統從機械上再想辦法也難以達到的。這就是當今不斷發展的潤滑。它正在以更小的投資走一條捷徑來滿足設備不斷更新發展的需要。
必須突破目前企業管理者只認購廉價油
一些單位購油只看單價成本,不看企業總成本降低觀念,而不注重購買適合本工況高性能油。
突破目前企業一出現故障只從備件上找原因
不少領導一出故障只從材質、材料、加工精度、和熱處理上找原因,而不從占事故 60% 以上是由選油和維護油不當造成的觀念。隨這企業的發展,操作技術含量逐漸下降,維護的技術含量不斷上升。最終作到設備維護在一個相當長階段保持正常運轉,儘可能避免檢修和維修,追求周期費用最經濟。顯而易見,未來的維修所從事的工作,面對機電液一體化現代化設備只能是換一換油,只要把潤滑劑維護好,就會使摩擦付磨損降到最低。國外已有整個 LCC 不解體大修範例,關鍵在維護。最近茂名石化乙烯報導已安全運行 79 個月的佳績。目前乙烯國際平均運行水平為 54 個月,改變可以往一年一小修,兩年一大修思維管理模式。據統計少一次大修,其效益接近 2 億元,就是強化了對關鍵機組維護保養和狀態監測,從定期檢修變為預知檢修。
必須突破“三無”現象
油品套用,同油品煉製一樣,是一個學科。因為它有廣大的工礦企業市場,必須培養一些即懂油,又懂設備的專業技術人員上崗,把應當建立和配套設施健全起來。
潤滑在我國已明顯落後,在油品套用方面,我們不但落後台灣、東南亞,甚至落後印度和巴基斯坦。不難看出為什麼同樣的設備,國外運行 6000 小時,而我們 1500 小時就要進修配廠。關鍵在選油及油品的維護保養上。有資料顯示,我們如果能達到日本的節能水平,那么我國能源需求量今後 60 年不必增加,日本 70% 能源依靠進口,尤其 99% 以上石油依靠進口。他們重點抓了節能技術和節能潤滑油脂開發, 1980 年增加了低粘度油和稠化多級油,如省能內燃機油省燃料 5—10% 。省能液壓油省電 3—7% 。日本 1973 年 ----1982 年間,取得了每年國民經濟總值增張了 3.8% 。而能源消耗確每年下降 2 。 0----2.9% 。產值能耗單耗每年下降 3.6% , 1982 比 1979 年總能耗取得下降 10% 的巨大節能效果,資源貧乏的日本,其能源儲備遠遠不及我國,為什麼經濟總量始終坐穩第二把交椅, GDP 四倍於中國,它們早在 70 年代就開展了潤滑現代化工作,設立了專門機構,積極推行潤滑現代化,普及到各個行業,甚至家喻戶曉。在科學界形成了一門新興學科“摩潤學” 。我國為加強合理潤滑技術,國家技術監督局 93 年公布了“合理潤滑技術通則”,內容十分豐富,至今翻看仍然新穎。遺憾的是,未能引起人們更多重視。人們的觀念必須更新,潤滑是一座“金山”,它以巨大的效益展現在我們面前。在當前能源十分緊張、材料上漲、成本上升情況下,各個企業都把潤滑經濟開展起來,是一條康莊大道。