零件結構,材料特性,設計模式,設計步驟,澆注系統,抽芯機構,冷卻系統,工作原理,
零件結構
如汽車鎖扣蓋的示意圖及實物圖(圖1尺寸示意圖,圖2為實物圖)所示。汽車鎖扣蓋,下部為4mm底板,上部有兩個突出三角形板,其上分別有兩個φ6mm和一個φ4mm圓柱側向伸出,兩個φ6mm圓柱上有兩凹槽。
示意圖及實物
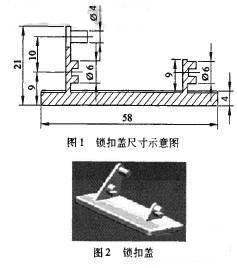
材料特性
汽車鎖扣蓋的成型材料為ABS,它具有強度高、熱穩定性和化學穩定性好、注塑時流動性好、易於成型的特點,其成型收縮率小,理論計算收縮率為0.6%,溢料值為0.04mm;比熱容較低,在模具中凝固速度快,模塑周期短;塑膠件尺寸穩定,表面質量高。
設計模式
汽車鎖扣蓋為小型製品,尺寸精度不高,比較適合於大批量模塑生產。為了提高生產效率,降低模具生產成本,設計採用一模4腔的設計模式(詳見模具結構圖)。汽車鎖扣蓋注塑模具的設計要點在於兩凹槽的斜頂側向抽芯機構和斜導柱滑塊抽芯機構的設計。
設計步驟
“汽車鎖扣蓋注塑模具”的設計步驟主要分三部分:澆注系統設計——抽芯機構設計——冷卻系統設計。
澆注系統
“澆注系統”,是為將熔融態的塑膠液引入模具型腔而在模具內開設的通道。主要由主流道和分流道構成。
主流道
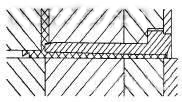
主流道是自注塑機噴嘴與模具主流道襯套接觸的部位起至分流為止的一段總流道,它是熔融塑膠進入模具時最先經過的部位。在臥式機上,主流道垂直於分型面,由於它與高溫塑膠及噴嘴反覆接觸,故設計成可拆卸的主流道襯套,主流道襯套應帶凸緣,使之固定在定模上。為便於流道凝料的脫出,將主流道設計成圓錐形,其錐角為5°,內壁表面粗糙度為0.8μm。主流道上部小端的直徑比注塑機噴嘴直徑大1mm,球面半徑比注塑機噴嘴的球面半徑大2mm,其作用是補償噴嘴與主流道的對中誤差,避免注塑機注塑時在噴嘴與主流道之間造成漏料或積存冷料使主流道無法脫模。
在“汽車鎖扣蓋注塑模具”中,分流道的布置採用對稱平衡式。這種布置使各分流道的長度、截面形狀和尺寸都對應相等,可實現均衡進料和同時充滿各型腔的目的。分流道直徑5-砌,分流道長度選取L1=65mm、L2=11.5mm。
流道和側澆口

澆口設定在底板處,如流道和側澆口圖(a-流道分布;b-側澆口 )所示,開模後,由推料板將澆口製品和凝料一起推出,在澆口部分剪斷。
抽芯機構
“抽芯機構”,是一種將整個塑膠件從模具中脫離出來的機構。一般分為斜導柱滑塊抽芯機構和斜頂桿抽芯機構,兩者基本原理相似,最大的不同在於兩者的動作驅動力不同。斜頂桿抽芯機構,是為解決平行於分型面的凹槽而發展的一種側抽芯機構,基本原理是將模具開閉的垂直運動轉化成水平運動。其動作驅動力,來自於推動板的動作。
“汽車鎖扣蓋注塑模具”中型腔的分布為一模4腔,且塑膠件同時存在兩個平行的凹槽,因此在模具的中間存在雙內抽芯。採用單一的斜導柱滑塊機構不能完全實現側抽芯動作,所以在設計中採用斜頂和斜導柱滑塊相結合的側抽芯機構,對模具內側的塑膠件凹槽採用斜頂側抽芯,靠近模具外側的凹槽採用斜導柱滑塊機構來實現抽芯。這樣既解決了單獨使用斜導柱滑塊機構難以完成內側抽芯的問題,又避免了使用雙斜頂機構所產生的裝配空間不夠的難題。
斜導柱滑塊抽芯機構和斜頂桿抽芯機構

對於斜導柱滑塊機構的設計,考慮到塑膠件形狀及模具結構特點,採用兩個滑塊機構且分布於模具兩側,其中每個滑塊在開模時由固定在定模上的斜導柱驅動完成位於同一側兩個塑膠件外側凹槽的抽芯動作。該側抽芯機構具有結構緊湊、成本低廉、便於加工裝配的特點。
對於斜頂桿機構的設計,採用了4根斜頂桿分別來實現4個塑膠件內側凹槽的抽芯及塑膠件的脫模。斜頂桿機構的工作過程是推板推動斜頂桿移動,使斜頂桿在動模板上沿著導軌產生縱向移動的同時作橫向移動,從而完成側抽芯動作。由於斜導柱滑塊的驅動力來自於固定在定模或動模的斜導柱,側抽芯時滑塊一般向模具外側運動。當採用斜導柱滑塊機構實現內側抽芯時,必須在模具中間留有滑塊運動空間,這樣就增大了模具的尺寸,同時使模具的結構更加複雜,從而增加了模具的成本。採用斜頂桿側向抽芯簡化了模具結構,降低了模具成本;而且斜頂桿在頂出塑膠件時起到一定的作用,使得塑膠件頂出時的受力更加均衡,可以減小塑膠件的變形。斜頂動作必須由推板的驅動來完成,因此斜頂機構的設計與推板行程有關,這也是斜頂機構設計與斜導柱滑塊設計的最大不同點。斜頂機構在頂出及退回時會在斜頂桿的側面上產生較大的應力,從而使斜滑塊表面較容易損壞,降低塑膠件的精度。因此,斜頂桿在選材和熱處理工藝等方面要考慮其使用性能的要求。
冷卻系統
“冷卻系統”,是一種可以防止塑膠件脫模時變形,降低模具的溫度,縮短成型周期,提高生產效率,增大結晶性塑膠的過冷度,以得到整體性能好表面光滑的塑膠件的系統。冷卻系統的設計應做到冷卻系統內流動介質能充分吸收成型塑膠件所傳導的熱量,使模具成型表面的溫度穩定地保持在所需的溫度範圍內。因此,在不與頂出系統和其它連線件發生干涉的情況下,儘量在型腔附近設定冷卻系統。根據塑膠件的結構複雜程度,冷卻水道可以採用直通式或迴轉式。直通式水道結構簡單,加工方便,但冷卻效果一般;迴轉式水道的路徑更加貼近於型腔輪廓,冷卻效果較好,但加工成本高,有時還必須採用分體式結構。由於鎖扣蓋體積小,形狀簡單,因此為降低加工成本,“汽車鎖扣蓋注塑模具”,採用直通式冷卻水道。模具的熱量是由輻射傳熱、對流散熱、向模板的傳熱及其與注射噴嘴接觸的傳熱等多因素綜合作用所形成的。當考慮冷卻介質在管內強制對流的散熱時,根據計算校核後,冷卻水道直徑為10mm,水道中心偏離型腔15mm。通過調節冷卻水的流量可以控制冷卻系統散發的熱量,從而調節模具型腔的溫度。模具採用直通單循環式結構的冷卻系統。
模具冷卻水道結構
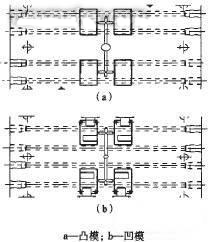
工作原理
根據模具結構圖所示,模具閉合時,熔融的塑膠經過噴嘴注入模具型腔,注射成型完畢後,注塑機帶動動模板4以下部位向下移動,在動模板4和定模板5之間分型,隨著動模板繼續向下移動,滑塊在斜導柱作用下實現側向抽芯;在拉料桿的作用下,塑膠件留在動模一側,主澆道中余料慢慢拔出。待主澆道中余料完全拔出後,動模和定模繼續分離,一直到兩板之間具有足夠的空間以保證塑膠件可以被完全取出。這時,注塑機和動模停止向下運動,注塑機中的推桿推動推板2向上運動,斜頂桿9在隨推板向上運動的同時還順著動模板中斜孔左右運動,實現了斜頂桿和塑膠件的分離,同時使塑膠件從動模中頂出。塑膠件被取出後,推動推板的推桿復位,在復位桿和復位彈簧的作用下推板回到原位,斜頂桿也隨著回復到原來的位置。模具開始閉合,動模板和定模板之間的距離越來越小,一直到完全閉合,完成了一個循環。