模具企業實行信息化現狀,數位化車間技術,精細化管理,技術系統的信息化,管理信息化,模具生產管理軟體,模具生產管理軟體(模具管理軟體),模具生產管理,模具生產現狀,生產管理目的,生產管理策略,模具生產管理系統實施效能與目的,改善日常業務,提升生產效率,目的,
模具企業實行信息化現狀
管理,無疑是21世紀所有企業必須嚴峻面對的問題。管理過硬,企業自然強大。管理漏洞多,企業利潤無法提升,自然無法長期發展。
模具製造業的特點,決定了模具企業管理的特殊性。訂單隨機、產品質量、交貨期無法把控,工程、設計、生產各個環節無法實時把控,各個環節問題層出不窮……一系列問題造成模具企業產品質量、交貨期、成本等問題難以解決。
模具為單件生產,有對特定用戶的依賴性,每件模具產品相對都較為複雜,加工程式量大,單價高,模具是依照產品訂單提供、按照用戶要求進行創新和改型結合的設計,到用戶安裝調試出製品的整個流程中不斷修改與調整,其適時監控更顯得重要,這就要求模具加工設備、測量設備,有其特殊要求。
隨著計算機信息技術的發展,改變了人們做事的方法和經營管理模式。電子商務、虛擬企業、動態聯盟、敏捷供需鏈等新的管理模式不斷出現。模具企業要想在這樣的競爭環境中取勝,實現可持續發展,就必須充分利用信息技術,最佳化企業資源利用,快速回響客戶需求,最大限度縮短生產周期,嚴格控制成本、質量、交貨期,才能提高企業的應變能力、創新能力和經濟效益。當前模具製造的重點發展方向是模具設計、分析及製造的三維化,模具軟體功能集成化、網路化、智慧型化,模具生產的無圖化、單件高精度並行加工、少人化無人化加工。
模具企業如何才能解決這些問題,模具管理軟體無疑是最好的選擇。針對中國模具企業棘手問題,模具管理軟體能提供優秀的解決方案,能無限制的擴大企業的業務信息空間,使業務活動與業務信息得以分離。在訂單的驅動下,原本無法調和的集中於分散的矛盾得以解決。通過技術信息手段,整合企業內部資源,並實現資源的集中、統一和有效配置;通過“協同設計”、“協同製造”、“客戶關係管理”,企業能夠跨越內部資源界限,實現對整個供應鏈的有效組織和管理,從而使模具企業的運作處於良性循環中。
數位化車間技術
數位化車間是模具製造的核心單元,通過不斷提升數位化製造能力和數位化協同水平,建立起全數位化的集成套用環境,利用先進的信息技術,由車間數控設備及工位智慧型化聯網開始,經數位化製造工藝設計和生產經營信息(包括生產計畫編制、製造數據管理、作業調度管理、加工過程控制和質量監控),直到現場生產狀況數據信息採集處理,實現從車間生產經營管理、生產計畫管理、製造資源管理與配送、現場管理和質量保證等職能部門間的管理集成。達到縮短產品製造周期、提高數控綜合套用效率,提高模具結構件製造的快速回響能力,實現高動態性、高生產率、高質量和低成本的模具產品數位化製造。
精細化管理
標準化可以複製,但精細化卻很難複製,它要求模具企業具備卓越的管理和高效的執行力。用條碼技術跟蹤模具從物料投產到成品入庫的整個生產流程,實時採集生產過程中發生的所有事件,讓模具在整個生產過程中變得清晰、透明;能夠很快發現出現質量問題的原因,制定針對措施解決質量瓶頸問題,實現模具質量追溯;通過改變原來手工錄入過程,達到準確、及時、快速的數據反饋,避免人為輸入差錯,更重要的是,使模具現場生產人員精力集中在業務操作上,提高工作效率。在企業未來的規劃上,MES還能夠為汽車模具企業實現一體化的模具設計與製造提供先進技術儲備,支撐企業實施精益生產和精細化管理。
技術系統的信息化
目前模具企業信息化建設主要包括技術系統的信息化和管理系統的信息化。
技術系統的信息化主要是模具CAD/CAE/CAM技術的套用,實現模具設計製造過程的信息化或數位化。
管理信息化
模具企業是典型的面向訂單的單件多品種生產型企業。由於訂單的隨機性、產品的多樣性、設計製造的經驗依賴性、變更的頻繁性、試修模的不確定性等,導致模具的生產情況複雜多變,整個生產過程難以得到有效管理和控制,所以管理信息化也被推到了一個新的高度。現有的一些ERP系統,甚至SAP、Oracle等國際知名大ERP系統供應商也沒有優秀的解決方案,很難滿足模具企業生產管理的上述要求,需針對模具生產特點,提供專門的解決方案。
很多模具企業在技術系統的信息化已經有意識提高自身水平,但在管理信息化上卻還一直不夠重視,很多停留在用手工生產排配、用Excel進行生產進度管理、對生產產能根本無法判斷、對客戶的承諾交期根本得不到實現等初級階段;甚至很多大中型企業也未在此引起足夠重視。
模具生產管理軟體
模具管理系統相當於為模具行業專門定製的模具ERP軟體;富士康科技集團郭台銘說過:企業應該建立自己的四大管制系統,它們是“工管系統、品管系統、生管系統、經管系統”,模具做為生產為主導的行業,各企業統帥也希望了解企業的生產狀況;生產管理也被提升至一個更高的平台,生產管理即是對生產活動有關之計畫與控制所採取的各種手段,確立生產計畫並控制其生產活動依據計畫順利進行,以達成生產之目的。
通過信息化的實施,利用科技手段,引進生產管理系統進行管理,各部門就能夠進行清楚了解模具的交期,適時進行進度跟催,履行對客戶的交期承諾,提升客戶滿意度。並實現部門內各指標的統計調查,提升工作效率。實現成本管控、排程管控、時程管控、經驗累積。達到流程標準化建立,窗體標準化建立,設計標準化建立,料件標準化建立,工程標準化建立,成本標準化建立。
模具生產管理軟體(模具管理軟體)
模具排配生產管理系統是一套模具設計生產的綜合管理系統,涵蓋營業訂單管理、CAD設計管理、機加工生產管理、鉗工管理、試模管理、成本管理以及其它日常人事管理,涵蓋模具廠各職能部門的管理作業。。此系統採用一種智慧型生產排配原則,採用獨特的倒推式計算方法,分析計算各生產單位及加工設備的工作負荷,生成工作負荷表存儲於工作排配管理資料庫,排配模具加工生產工序,並對排配結果進行模擬判斷,生成排配計畫表存儲於工作排配管理資料庫,並將上述排配計畫表傳送給相關單位進行生產加工,並最終輸出管理數據。
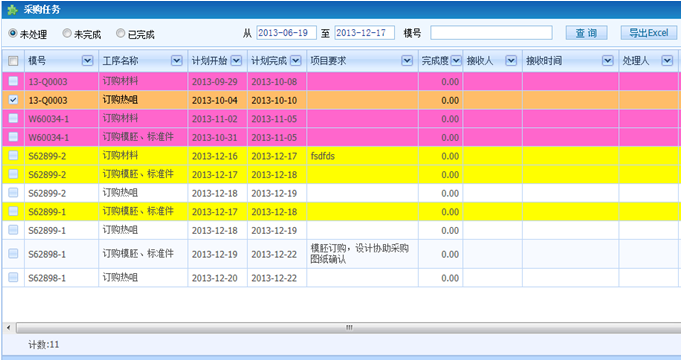
目前國內較大的模具企業如海爾的家電廠、汽車廠等六個廠,富士康的PCEGDTII塑模廠、北京富士康模具廠、煙臺DT6等都採用該模具管理系統進行生產管理。
模具管理軟體套用價值
1.搭建模具企業建立一個高效執行的信息化管理體系與平台,規範基礎管理流程,打造並彰顯領先同行的競爭優勢,提高效率,降低成本,增強模具企業盈利能力和競爭力;
2.為企業管理決策提供及時量化數據支持,使公司決策建立在科學的真實的數據基礎之上,減少聽匯報憑感覺拍胸脯等盲目決策帶來的風險,提高決策正確性60%以上;
3.提高模具企業知識管理,將個人經驗與技能迅速提煉整理轉化為企業知識,建立一個專業化的模具製造團隊,有利於提高與同行模具企業的技術競爭力20%以上;
4.積累模具報價資料庫,實現快速準確報價,贏取銷售訂單,提高報價效率30%以上;
5.幫助公司生產管理人員及時掌控每幅模具設計,採購,加工進度等交期要素的及時信息,增強模具製造過程的透明度,使模具交期達成率提高15%以上;
6.將模具成本控制在製造過程每一個環節,確保模具利潤,增強企業盈利能力5%以上;
7.實現自動調度排程,減少人為窩工,實現資源最佳化組合,使生產能力提高10%以上;
8.加強質量檢驗與控制,提高加工質量,減少試模次數20%以上;
9.加強任務執行管理,及時了解並考核每個人的量化工作業績,提高工作效率30%以上。
模具生產管理
模具生產現狀
目前很多模具生產企業仍然存在生產效率低下,模具生產利潤不高,不知道新的訂單時候是否有生產能力承接,在生產現場的模具是否能夠按時交貨,成本統計困難,設備、人力不足,生產線塞車,產能不平,工序混亂,交貨拖期等眾問題。
生產管理目的
-合乎品質水準
-儘可能降低成本
-在一定的期限內完工
-使資產的周轉數最大
-滿足顧客的要求
生產管理策略
-制定彈性的產銷管理制度
-做好協力廠商管理以避免欠料停工
-合理選擇自製或外包作業
-混合性工廠布置之運用
-實施小批量生產
-培養多能工使工作及人員安排更有彈性
-推展目視管理,重視異常問題之處理
-通過生產負荷管制使產銷配合密切
-使生產管理制度化、電腦化,迅速掌握生產情報
-培養與選用積極主動與協調性佳之生產管理人員
-通過生產周程時間之分析制定,使產銷權責明確
-推行全面綜合性的物料管理制度
-實施存量管制以降低成本
-運用物料需求計畫於採購與庫存管理
-協力廠商管理制度之建立與推動
-減少產品之準備工時
-推行5S工作
-分析品質成本以降低品質異常所造成之負擔
-推行生產績效管理
-設立全面保養制度以提高設備使用率
模具生產管理系統實施效能與目的
改善日常業務
-資料信息化,隨時了解進度
-無需人工排配生產
-系統自動更新日程表
-減少對現場的進度詢問
-全進程管控及成本收集
提升生產效率
-提升報價準確性
-迅速投入模具工程設計
-能判斷委外或自製加工
-提升生產效率及機器使用率
目的
-管控生產大日程
-縮短工期
-減少加班時間
-防止過剩的委外加工
-防止錯過訂單機會
-進行模具成本管理