振打板是煤氣發生器內件的重要部分。內件振打板由規格為190 mm×170mm、厚度為50 mm、材質為1.7335(13CrMo44)的鍛件及浮焊於其上的規格為100mm×100mm、 厚度為32mm、材質為2.4650的板材組成煤氣發生器的內件是確保設備造氣的關鍵部件。
基本介紹
- 中文名:振打板
- 組成:煤氣發生器內件
- 意義:確保設備造氣的關鍵部件
煤氣發生器內件缺陷,振打板結構,振打板修復原則,振打板修復程式,
煤氣發生器內件缺陷
煤氣發生器的內件是確保設備造氣的關鍵部件。煤氣發生器在工作時,極易出現因爐灰堆積而導致的爐內局部過熱、結疤、結塊等問題,從而影響設備的工作效率。為防止上述問題出現,該設備上設定了振打裝置,工作時定時啟動,作用到內件振打板上,靠振動清除內件受熱面上的煤粉,以保證傳熱面的傳熱效率。因此,壓力容器外殼的振打裝置敲擊器接管口必須與內件受熱面上的振打板方位一致,位置公差在0~20 mm,方能保證敲擊裝置的正常操作。
帶振打板的內件受熱面是由規格為φ38 mm×7.1mm、材質為1.7335 (13CrMo44)的80根傳熱管所組成的中心直徑為φ1272mm的圓筒形膜式壁,傳熱管之間連線有厚度為8mm、材質為1.7335 (13Cr Mo44)的鰭片。內件受熱面的製造及驗收均按國外專利商的內件圖樣及技術規格書的要求進行。內件振打板周向方位產生誤差的原因系圖樣尺寸標註有誤,而除這4個方位有誤的振打板需與外殼管口相對應以外,還有14個外殼管口需與內件相對應,因此無法通過調整方位來解決。由於外殼振打裝置接管的方位符合圖樣要求且已成品,故只能對內件振打板進行修復。
振打板結構
內件振打板由規格為190 mm×170 mm、厚度為50 mm、材質為1.7335 (13CrMo44)的鍛件及浮焊於其上的規格為100 mm×100 mm、厚度為32 mm、材質為2.4650的板材組成,見圖。
由圖可以看出,內件振打板鍛件部分兩端分別與4根傳熱管組焊,之後與整個內件受熱面形成一體。振打板主要靠鍛件部分承受振打力,而不能把振打力直接作用於傳熱管上。
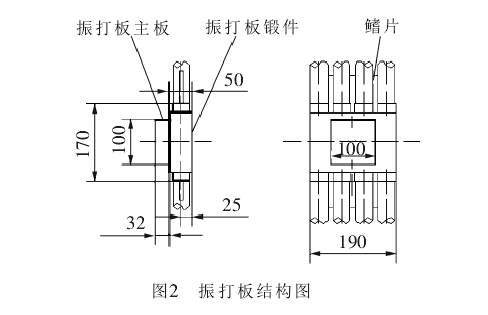
振打板修復原則
圖樣中要求該類內件振打板位置公差在0~20 mm,而內件受熱面上相鄰2根傳熱管的徑向尺寸約為110 mm。振打板在內件受熱面上的周向尺寸誤差為100 mm,即只要把振打板向正確方向移動2根傳熱管的徑向距離,就會使振打板方位滿足圖樣要求。分析認為,割開振打板所在4根傳熱管及其所要調整方向上的相鄰2根傳熱管,將振打板所在受熱面氣割開1個方孔,再將氣割下的帶振打板及相鄰兩段傳熱管的受熱面旋轉180°後重新施焊,是解決問題的最好辦法。
修復過程中需注意以下問題:
①振打板兩端各6道切口須以振打板中心線為軸左右對稱,以使振打板旋轉180°後仍可保證其所在標高。
②氣割後切口間的距離須小於3mm,以保證重新施焊時的焊接質量。
③嚴格控制傳熱管內不得進入任何雜物,以防止設備工作時突然局部溫度升高或造成傳熱管局部腐蝕等因素可能引起的嚴重後果。
④傳熱管的氣割、組對、焊接及熱處理等工藝過程需符合國外內件生產廠家提供的內件製造檢驗技術規格書的要求。
振打板修復程式
①按內件圖樣以實際振打板的位置找出對稱軸,作為氣割及重新組對的基準,同時劃出切割線。
②採用1mm厚切片砂輪,沿切割線將帶振打板及相鄰兩段傳熱管的受熱面切割下來,受熱面上形成350 mm×350 mm方孔。
③將方孔旁傳熱管之間的膜式壁用2mm切片砂輪切開,長度約600mm,使傳熱管端部有活動餘量,以保證振打板旋轉180°後與受熱面重新組對的精度。
④將傳熱管端20mm範圍內外表面的油漆打磨掉,直至露出金屬光澤。
⑤採用旋風銑刀等專用工具加工重新施焊的管端坡口,重新組對好振打板與內件受熱面,採用氬弧焊進行對接管頭的焊接。
⑥對接管之間的焊接接頭進行100%射線檢測及表面磁粉檢測,符合ASME有關標準要求。對修復後的受熱面作局部消除應力熱處理。熱處理後對修復焊縫進行100%MT,符合ASME有關標準要求。