變壓吸附法
變壓吸附技術是19 世紀60 年代出現的,當時沸石對氮和氧的分離係數較低(在2~3之間),故當時沒能在制氧方面實現套用。隨著合成沸石分子篩技術的不斷發展,變壓吸附技術逐步開始套用於制氧領域。其工作原理是利用分子篩對氮氣和氧氣的選擇性吸附性能,增壓時分子篩對氮氣進行吸附,得到富氧氣體,而降壓時氮氣解吸,分子篩獲得再生。最初由於技術工藝不成熟,變壓吸附制氧多套用於平原地區,近十年來由於分子篩性能的不斷提高和高效的氣體分離系統,為變壓吸附制氧技術在高原地區套用提供了可能。
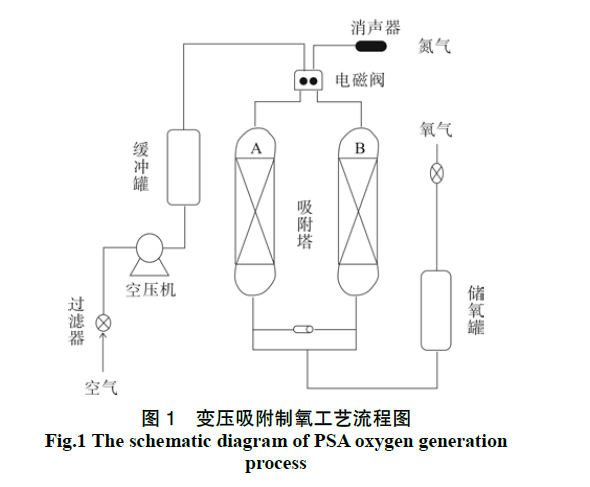
圖1 變壓吸附制氧工藝流程圖
變壓吸附技術制氧具有能耗低、設備投資少、使用方便,而且可以連續產氧等優點,因此近年來不少學者對此開展了大量研究,不論是在工藝技術還是設備研製等方面都有許多新成果。我國軍事醫學科學院衛生裝備研究所為了解決高原邊防部隊用氧難題,自上世紀70年代開始對高原變壓吸附制氧技術進行了系統深入的研究,是國內開展高原變壓吸附制氧工藝研究最早的單位。該研究所朱學軍等對高原環境對小型
醫用制氧機性能的影響進行了研究,發現隨著海拔高度增加,制氧機的進氣量不斷減小,相同刻度流量下氧氣濃度逐漸降低,但是吸氧效應實驗證明氧濃度降低的程度不會影響在高原搶救缺氧病人。田濤等針對小型制氧機在高原使用時出現氧濃度和回收率下降的問題進行了研究,通過最佳化制氧流程可有效提高氧濃度和回收率。目前兩塔或四塔變壓吸附工藝的氧回收率較低,僅為30%~40%,回收率低會增加設備能耗,這對高原地區制氧尤為不利。
為此,石梅生等研究了六吸附塔制氧工藝及其控制方法,用多通旋轉分配閥來實現氣體的分配,提高了回收率,解決了高原部隊用氧問題。王濟虎等為高原行駛車輛研製了車用
變壓吸附制氧機,經現場檢驗該制氧機達到了技術指標要求,效率高,操作與維護方便適於高原地區使用。
在高原條件下的供氧方式研究中,肖華軍等在拉薩地區對分子篩制氧機室內彌散式供氧效果進行了分析,實驗顯示制氧機在開機2h後,房間內的供氧水平可以達到2200m以下高度的氧濃度,供氧房間人員睡眠
血氧飽和度高於未供氧房間人員,所以通過向房間內彌散式供氧可有效避免高原反應。對於高原彌散式供氧的特性,劉應書等基於實驗和模擬研究發現在高原環境中供氧軸向最大速度和氧氣摩爾濃度都隨軸向距離的增加而衰減,並且在軸向0~1.5m範圍內有很大的速度梯度和濃度梯度,而且位於不同海拔高度上的彌散供氧所形成的富氧區域具有相似的形狀,該研究結果為高原富氧室的供氧設備布置、安裝提供了參考和借鑑。
目前,
變壓吸附制氧設備在高原地區已得到了廣泛套用。2002年在風火山上建立了世界上第一座變壓吸附高原制氧站,從而使人員高原發病率下降了44.1%。而後中鐵二十局建立兩座變壓吸附高原制氧站,安裝在隧道進山口兩端,從兩頭向施工隧道內進行彌散式供氧,使隧道內氧含量達到了14%左右,相當于海拔高度下降了1000 m。目前青藏鐵路沿線已經建立17 座變壓吸附制氧站,同時配置了25個高壓氧艙供人員吸氧使用。2012 年軍事醫學科學院衛生裝備研究所為我國南極崑崙科考站專門研製出適應海拔4087m、可在環境溫度-90 ℃儲存的變壓吸附制氧設備,保障了科考站人員的工作、生活用氧需求。
全氧燃燒技術
日用玻璃是人民生活必需品,也是科學研究工作不可或缺的產品,我們日常生活的方方面面都離不開日用玻璃。日用玻璃涉及
瓶罐玻璃、器皿玻璃、
藝術玻璃、儀器玻璃、藥用玻璃、保溫瓶玻璃、電光源和照明玻璃。
全氧燃燒由美國能源署在20世紀80年代提出,並委託美國的幾個較大的氣體公司、科研機構立項研究,其最初的宗旨是節約能源、降低排放。該技術在20世紀90年代獲得了實際套用,並取得了理想的效果。我國玻璃領域的全氧燃燒技術的引進是在2000年,首先套用在
陰極射線管玻璃(CRT)的玻錐和玻屏熔化。全氧燃燒(又稱為純氧燃燒)是使用氧氣取代傳統空氣作為助燃劑,與燃料進行燃燒,減少氮氣產生,既有利於節能,又有利於減少
氮氧化物排放。隨著制氧技術的迅猛發展及電力成本的降低,全氧燃燒逐步得到推廣和套用。
套用
1、全氧燃燒技術套用領域
全氧燃燒首先在
電子玻璃方面得到套用,幾乎全部技術從國外引進。在我國日用玻璃領域的推廣起源於電磁爐
微晶玻璃面板(鋰鋁矽玻璃系統),現在套用領域包括高硼矽器皿玻璃、高鋁矽玻璃、藥用低硼矽玻璃、藥用中硼矽玻璃、
光學玻璃、光伏玻璃、低熔點玻璃、無鉛玻璃(照明)、玻璃棉、高鉛玻璃、
玻璃微珠、玻纖、陶瓷釉料、精白料(高白料)白酒瓶、化妝品瓶、啤酒瓶等領域。
2、日用玻璃全氧燃燒熔窯
與傳統的空氣助燃熔窯(馬蹄焰、橫火焰)相比,日用玻璃全氧燃燒熔窯有以下幾個特點:
(1)熔化部使用1支或多支純氧燃燒噴槍,不間斷噴出氧氣和燃料,在熔窯的特定位置設立調節煙道用以排出煙氣、調節窯壓;
(2)噴槍的布置有橫向布置、縱向布置、頂燒等多種方式,可根據玻璃的特點及要求由設計人員靈活選擇。
與傳統的熔窯不同之處在於:
(1)通常情況下使用全氧燃燒技術後熔化率有所提高,提高的幅度與熔化的難易程度、玻璃品質要求、碎玻璃使用量等因素有關;
(2)全氧燃燒熔窯由於其獨特的燃燒方式,熔窯的尺寸及形狀會有別於現有熔窯。相比常見的馬蹄焰熔窯會有更大的長寬比;
(3)耐火材料的選擇會發生較大的變化,火焰空間由於超高的水蒸汽濃度導致矽質材料被完全棄用,並且,由於材料的變化引起鋼結構必須採用適合耐火材料;
(4)採用了完全不同的噴槍和與之匹配的安全性、可靠性、控制精度更高的
燃燒系統;
(5)更為完善的測量系統,獲得更多的熔窯運行參數,為操作者的調整提供更為可靠的依據。
3、全氧燃燒燃料
目前,除了塊煤、煤制氣(
發生爐煤氣)不能用於全氧燃燒熔窯之外,其它燃料均可使用。其中,焦爐煤氣、石油焦在日用玻璃和
建築玻璃行業全氧燃燒熔窯中運用,大大拓寬了全氧燃燒技術的套用領域。
環保問題
日用玻璃由於其特殊性造成環保問題解決起來有相當大的困難。日用玻璃的特殊性集中表現在以下幾個方面:
(1)產品的多樣性;
(2)窯型的多樣性;
(3)企業規模偏小;
(4)熔窯面積不大。
上述特點,導致企業在選擇煙氣處理方案、設備及運行方式時很難下手。不少企業花錢購置了環保設備,卻由於自身產品的特殊性難以達到當地的環保排放標準,即使達到也會因運行費用高而難以推廣。
全氧燃燒技術在日用玻璃行業使用時,對環保的影響有以下幾個方面:
(1)由於燃燒時沒有引入助燃空氣里的
氮氣,所以可有效降低直排時的NO,濃度;即使生產的料方中引入有硝酸鹽,煙氣處理也會較為簡單,達標相對費用低,更加可靠。
(2)全氧燃燒由於沒有傳統的馬蹄焰窯的換向操作,所以可部分降低粉塵的排放。
(3)全氧燃燒技術運用於日用玻璃領域後,對氟化物、硫化物、HCl、其他重金屬(砷、鉛、鉻等)的排放沒有明顯的幫助。如果玻璃成分中含有上述物質,還是應該採取相應的煙氣處理措施。但是由於全氧燃燒煙氣的特殊性,其環保設施的選擇和使用上會有一定的不同,這一點是應該注意的。
經濟性分析
1、運行成本
運行成本涉及燃料品種、當地的燃料價格、電價(直接決定氧氣成本)、氧氣的來源、玻璃的熔化難度(越是難以熔制的玻璃節能效果越明顯,改為全氧燃燒後的運行費用也會越低)、設計節能率。
(1)燃料種類及價格。能耗數據與熔窯形制、管理水平、玻璃種類、碎玻璃用量、是否有電助熔等因素相關;燃料價格與地區、統計時間有關。
(2)氧氣的來源。目前,常見的氧氣可由很多渠道獲得,不同渠道獲得氧氣價格差異很大,這需要根據客戶的具體情況確定。
2、建造成本
建造成本歸納起來為兩加兩減。兩加是指火焰空間使用價格更高的電熔耐火材料,使用控制精度和可靠性更高的
燃燒控制系統。這兩項相比傳統的熔窯,費用有明顯的上升。由於以上原因,使得企業在新熔窯建設上的投資會有一定幅度的上升。兩減是指沒有了傳統熔窯使用的蓄熱室及換向裝置,熔窯占地面積更小、熔窯基礎更小(特別是蓄熱室部分)。由於以上原因,使得企業在蓄熱室、換向裝置的材料購置、建設以及在熔窯土建方面的投資會有不同程度的下降。
全氧燃燒火焰空間裡的水蒸汽濃度可達50%以上,含鹼玻璃品種的鹼金屬水蒸汽會對偏酸性的
矽質耐火材料造成加速侵蝕,所以全氧燃燒熔窯火焰空間不再使用矽質耐火材料,而改為偏中性的電熔耐火材料,這將導致熔窯建設投資的上升。
全氧燃燒需要對燃料及氧氣精確計量、調節靈敏,對設備的可靠性及系統的安全性都提出了更高的要求,所以目前國內使用的
燃燒控制系統較傳統的空氣助燃的熔窯燃燒控制系統價格會更高。在傳統空氣助燃的熔窯中,蓄熱室的造價一般達到熔窯總造價的25%以上。取消了蓄熱室和換向裝置,在設備購買和建造環節可以為企業節省一筆不小的開支。這一點是可以準確預見的。由於全氧燃燒熔窯沒有了蓄熱室,熔窯所占面積會變小,而且不用再建設蓄熱室基礎。這樣,土建成本會有較大幅度的降低。
綜合分析,使用相同品質耐火材料的情況下,全氧燃燒熔窯的建設成本不會比相同生產能力的傳統空氣助燃熔窯更高,甚至在某些時候還會更低。
適用範圍
通過對比分析可以發現,全氧燃燒在節能、環保、提升產品質量、提升綜合經濟效益方面有得天獨厚的優勢,但是全氧燃燒技術也有它的適用範圍,至少目前來看並不是所有的日用玻璃產品都適合用全氧燃燒。目前,國內下列情況比較適宜使用全氧燃燒技術。
1、難熔的玻璃
簡單的講,越是難於熔化的玻璃使用全氧燃燒技術後在玻璃品質的提升、能耗的降低方面效果越明顯。比如:鋰鋁矽系列、鎂鋁系列、高硼系列、無鹼玻纖、高鋇系列、常見的鈉鈣矽玻璃中的精白料、高白料、工藝品等。而相對附加值較低的產品,由於使用全氧燃燒後投入產出比沒有明顯的優勢,所以普通鈉鈣矽玻璃目前推廣全氧燃燒技術的迫切性並不大。
2、品質要求高的玻璃
全氧燃燒熔窯可以提供更高的熔化溫度、更加科學的窯內溫度梯度,這就使得玻璃可以得到更充分的熔化、更充分的澄清、均化、更加易於實現的熔化氣氛(無論工藝需要的是氧化氣氛還是還原氣氛)。比如,傳統的電子
微晶玻璃(鋰鋁矽系列)在使用傳統的空氣助燃熔窯時,不僅能耗很高,而且玻璃的品質很難保證,特別是鋁含量、矽含量無法達到國外同類產品的指標,這樣導致國內該行業生產的產品理化指標與國外同類產品一直存在明顯的差距。2008年,該行業逐步推廣使用全氧燃燒技術後,不僅能耗大幅降低(50%),而且玻璃的理化指標得到明顯改善,目前已接近國外先進水平。現在的行業狀況是:國內生產此類產品的企業大多已經改為全氧燃燒熔窯。與電子微晶玻璃類似的還有玻纖行業,目前國內大部分企業均已改為全氧燃燒熔窯或全氧燃燒加電助熔窯。
3、 NOx處理困難的玻璃
日用玻璃行業在規模、窯型、燃料、玻璃成分、成型方式等方面千差萬別,這就導致日用玻璃領域在進行環保治理時遇到的情況不盡相同。目前,國內常見的脫硝工藝,無論是SCR還是SNCR,都有不少成功的案例。但是,在日用玻璃行業也有不少失敗的案例,究其原因還是跟日用玻璃行業的多面性、複雜性有直接的關係。簡單的講,在某些企業非常成功的脫硝工藝,到另外一家就不一定可行。全氧燃燒技術從燃燒機理上杜絕了產生NOx的氮的引入,這種燃燒方式使煙氣排放更容易達標。