所謂冷壓型焦法,是以粘結劑(也有不用粘結劑的)和惰性組分煤(或半焦粒)為原料,通過冷壓工藝來製取冶金型焦的方法。
基本介紹
- 中文名:冷壓型焦
- 外文名:formcoke from cold briquetting
- 含義:以粘結劑和惰性組分煤制冶金型焦
- 套用:冶金型焦的製備
產品簡介
產品原理
工藝流程
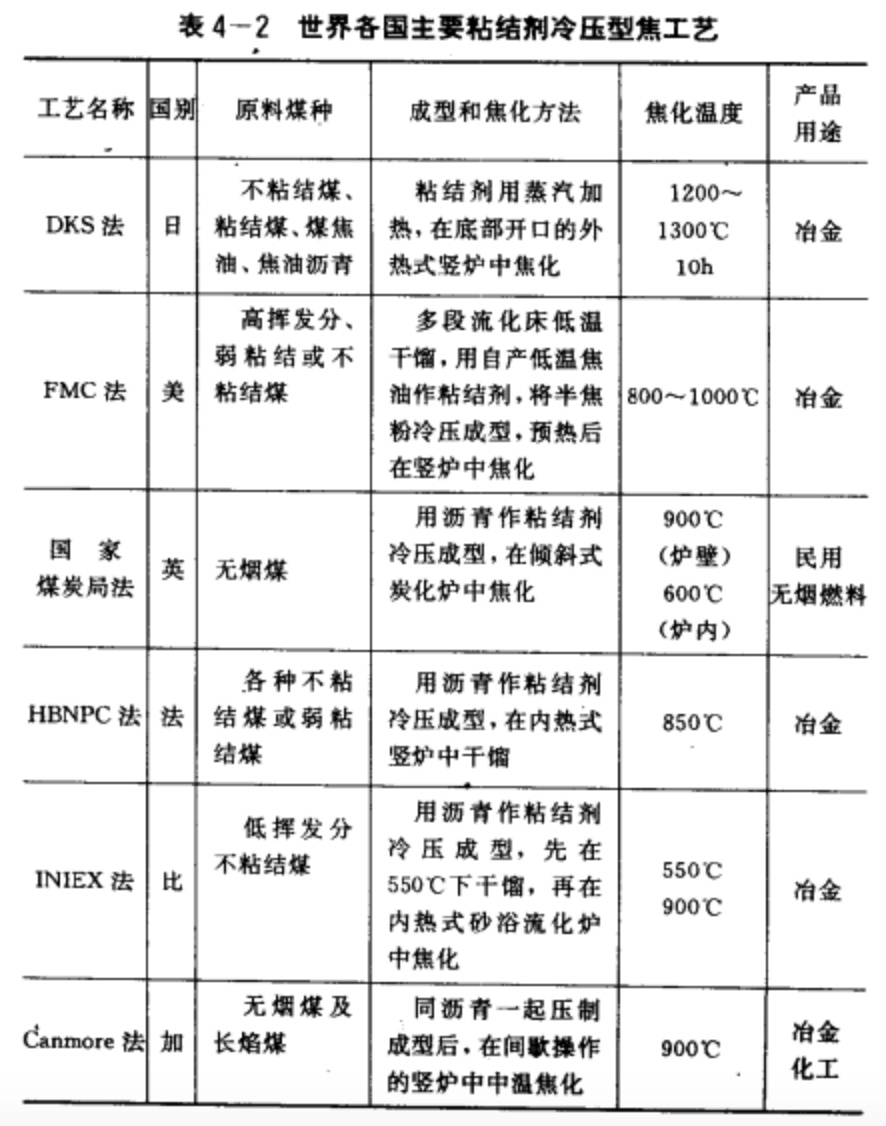

所謂冷壓型焦法,是以粘結劑(也有不用粘結劑的)和惰性組分煤(或半焦粒)為原料,通過冷壓工藝來製取冶金型焦的方法。
所謂冷壓型焦法,是以粘結劑(也有不用粘結劑的)和惰性組分煤(或半焦粒)為原料,通過冷壓工藝來製取冶金型焦的方法。產品簡介冷壓型焦又有無粘結劑的冷壓型焦和有粘結劑的冷壓型焦之分。無粘結劑的冷壓型焦主要以泥煤、褐煤等低變質程...
冷壓型焦工藝(cold briquetting process)是指型焦用料加壓成型煤,再經炭化或其他後處理製成型焦的一種型焦製備工藝。其成型溫度遠低於熱壓型焦工藝。冷壓型焦工藝分為有粘結劑冷壓型焦工藝和無粘結劑冷壓型焦工藝兩種。冷壓型焦工藝...
以焦粉為主要原料,添加一定比例的複合粘結劑,充分攪拌潤濕,並採用冷壓工藝製成的型焦。3.2 冷壓強度 型焦於環境溫度下在壓力試驗機上,以規定的均勻位移速度單向施力至開裂時的抗裂強度。3.3 熱強度 型焦在受熱後的抗壓強度稱為...
冷壓[型]焦工藝是1996年公布的煤炭科學技術名詞。定義 型焦用料在常溫下加壓成型煤,再經焦化或其他後處理製成型焦產品的製備工藝。分“有黏結劑冷壓[型]焦工藝(cold briquetting process with binder)”和“無黏結劑冷壓[型]焦工藝(...
冷壓型焦是將低揮發分的弱粘結煤或不粘結煤。也可將高揮發分煤或不粘結煤的半焦,配以適量的粘結劑,在粘結劑的軟化溫度(一般為70~100℃)下成型後炭化(個別也有不加熱成型的)。型焦工藝在配用非粘結性煤和弱粘結性煤的比例上...
型焦可作為工業或民用的塊狀燃料和氣化原料, 有的型焦可代替部分常規焦炭用於高爐煉鐵或沖天爐熔煉。型焦品種很多, 按製備工藝分為熱壓型焦和冷壓型焦兩類;按原料或用途可分為褐煤型焦和無煙煤型焦或高爐型焦和鑄造型焦等。型焦...
工業型焦 工業型焦是以粉煤為原料,經配煤I 或單種煤J 加工壓製成型,再經碳化工藝而形成的型焦和型焦煤製品。碳化溫度在600攝氏度左右出來的產品為型焦煤I 半焦型煤J ,碳化溫度在攝氏1000度以上出來的產品為型焦。
HBNPC工藝(HBNPC process)法是指法國巴森煤礦和加來巴斯煤礦聯合開發的冷壓型焦工藝。又稱HBN工藝。HENPC工藝於1968年開始研究,最初的目的是用低揮發分煤生產民用無煙燃料,後來在此基礎上研究型焦藝。1969年,建成第一個生產能力為10t...
IChPW工藝(IChPW process)是指波蘭煤化學加工研究所(lnstytut Chomicznej Przerobki Wegla,縮寫為IChPW)開發的,利用高揮發分弱粘結性或不粘結性煤的冷壓型焦工藝。該工藝於1955年開始研究。1960年,建成100t/d的型焦裝置。1961年...
焦末壓球機技術先進,質量可靠,一機多用,壓力強大,適合大、中、小型企業建立具有一定生產規模的生產線。適用於工業造氣、鍋爐型煤、冷壓型焦、點火型煤、民用型煤、民用冶金、耐材、醫藥等材料的各種成型。用途 壓球機是一種將粉狀物料...
型焦 型焦是由煤粉等原料加壓成型煤,再經炭化等後處理製成的一種新型焦炭。型焦品種較多,按製備工藝可分為冷壓型焦和熱壓型焦兩類;按用途可分為高爐型焦和鑄造型焦等;按所用原料可分為褐煤型焦和無煙煤型焦等。焦炭質量指標...
立式混捏機(vertical kneader)是指用於冷壓型焦用料加熱和混捏的型焦製備設備。把配合料加熱到稍高於粘結劑軟化點的溫度,並通過混捏使其中粘結劑充分潤濕煤粒表面,使配合料具有可塑性,以製備型煤。 結構和主要參數 立式混捏機的...
型焦是由煤粉等原料加壓成型煤,再經炭化等後處理製成的一種新型焦碳。型焦品種較多,按所用原料可分為褐煤型焦和無煙煤型焦等;按製備工藝可分為冷壓型焦和熱壓型焦兩類;按用途可分為高爐型焦和鑄造型焦等。質量評價 焦炭中的...
間歇裝料齡底開式(或斜底式)焦爐,可向高熱值煤氣和副產品。其不足之處是單位爐容的生產能力較小;加熱制度不能按冷壓型煤炭化的要求來調整。所得型焦易融著結塊或部分碎裂。此外,紅熱型焦的顯熱未回收利用。
領導設計了我國的58型標準焦爐,主持了大容積焦爐(高5.5米)試驗並獲得成功,設計了冷壓型焦連續生產的H75型直立爐。1950年5月由上海來鞍鋼化工總廠,曾任化工總廠煉焦車間總值班技術員。1952年被調到鞍鋼公司設計室,後調冶金部...
在製備大塊鑄造型焦時,為保證型焦塊度的完整性,根據主體煤的性質,在型焦用料中適當配入收縮小的情性物質,並根據大塊型煤加熱時的收縮特性選用有效的炭化工藝參數,以減少裂紋的生成。用瀝青作粘結劑的冷壓型焦,也有採用不同速度...
原煤炭部科技計畫項目“植物質配煤乾法冷壓型焦技術”,主持,2000;煤炭高校青年基金項目“最佳化煤熱解產物的加熱技術研究”,主持,2000;煤炭自然科學基金項目“鹼性條件下煤的電化學脫硫”,主持,2001;山東省自然科學基金項目“強粘煤...
17什麼是冷壓型焦?59 18什麼是熱壓型焦?60 19什麼是型焦煤?61 第5章水煤漿技術及套用62 1什麼是水煤漿和水煤漿技術?62 2水煤漿技術產生和發展的背景是什麼?63 3我國水煤漿技術工業化套用現狀如何?64 4...
型焦是由煤粉等原料加壓成型煤,再經炭化等後處理製成的一種新型焦炭。型焦品種較多,按所用原料可分為褐煤型焦和無煙煤型焦等;按製備工藝可分為冷壓型焦和熱壓型焦兩類;按用途可分為高爐型焦和鑄造型焦等 ...
江蘇百萬噸造氣型煤項目於2006年引進,2010年該公司進行了技改,計畫建成兩條生產線生產冷壓型焦,年可實現產值2億元,安排就業130餘人。上藝艾威汽車用品加工項目於2010年引進,主要從事汽車坐墊編織,採取“公司+農戶”的形式,可安排就業...
5.5 炭化升溫速度對鑄造焦質量影響研究 5.6 炭化終溫及恆溫時間對鑄造焦質量影響研究 5.7 顯氣孔率超標的鑄造焦缺陷修補方法探討 5.8 本章小結 6 鑄造型焦的製備研究 6.1 鑄造型焦製備的煉焦工藝參數確定 6.2 冷壓鑄造型焦...
四、冷壓型焦 五、商品煤氣及副產品 第二節 煤化工 第三節 三鋼動力能源 一、熱力車間 二、供電車間 三、供水車間 四、煤氣公司 五、電訊經營部 第四節 耐火材料 一、普通耐火磚 二、特殊耐火磚及不定型耐火材料 三、白雲石襯磚...
長期從事焦化工業科研。參與熱壓型焦、冷壓型焦、焦化工業的化工環保、焦化產品回收及精製的科研。熱壓型焦研究獲國家科學大會獎。寶鋼焦化污水處理模擬試驗及鎂碳磚固體粘合劑。獲冶金部科技進步四等獎或鞍山市科技進步三等獎。
熱壓[型]焦工藝是1996年公布的煤炭科學技術名詞。定義 將型焦用料快速加熱到其中黏結性煤的塑性溫度區間,加壓成型煤,再經焦化或後處理製成型焦產品的製備工藝。分“固體載熱體熱壓[型]焦工藝(hot briquetting process with solid ...