內裂是鋼材內部缺陷之一,表現為在酸浸低倍試樣上非因縮孔、非金屬夾雜、氣泡造成的不同形態的內部裂縫,是裂縫內較少或完全沒有夾雜物的晶間開裂,多發生在高碳鋼和高合金鋼中,集中在鑄錠中心處的內裂叫軸心晶間裂紋,由於不接觸空氣,內壁未氧化,又無偏析夾雜,熱加工時採用大壓縮比可能焊合。軸心晶間裂紋是由鑄錠凝固時體積收縮引起的中心處受拉而產生的熱裂紋。
基本介紹
- 中文名:內裂
- 外文名:internal crack
- 含義:鋼材未延伸至表面的內部斷裂
- 套用:煉鋼、鑄造
簡介,內裂的產生原因,熱處理應力型,鍛造方法型,熱處理應力型內裂的預防,
簡介
通常人們把未延伸至表面的內部斷裂統稱為“內裂”。內裂大多發生在鋼錠開坯鍛造及鋼材軋制過程中以及澆注鋼錠冷凝時應力產生的過程中。內裂一般都產生在低倍組織不理想的中心部位,因為鋼材中心是碳化物偏析、疏鬆、夾雜等最容易集中的地方,緻密程度差,機械強度低,截面越大越嚴重。所以在鍛造或軋制時容易產生內裂(右圖圖a),有時,大截面的鋼材由於加熱不透,中心塑性很低,在隨後的鍛軋過程中也會造成內裂(右圖圖b)。
有內裂的鋼材,在加熱及鍛造時由於應力集中,會使中心裂紋擴大。圖c為W18Cr4V鋼材因存在內裂(左),經鍛造後中心嚴重開裂(右)。
具有內裂的鋼材,不僅造成鍛造廢品,往往也因檢查不嚴製成產品後使產品報廢。
W18Cr4V鋼製成的多鍵拉刀,熱處理後發現縱向裂紋,斷口檢查,原材料存在內裂,裂紋在熱處理時向表面擴展。下圖1為多鍵拉刀橫斷面,下圖2為多鍵拉刀縱斷面。所以,在生產中對材料要嚴格檢查,發現有內裂的鋼材不能投入生產。
內裂的產生原因
熱處理應力型
大型工件的內裂主要是由熱處理應力引起的,我們稱它為“熱應力型內裂”。由於無損探傷技術的發展和套用,對於內裂等嚴重缺陷的檢測有了一定的手段,但內裂還是時常漏檢,由此造成的突然斷裂也時有發生。因此,研究熱應力型內裂的成因,尋求預防熱應力型內裂產生的措施,是十分必要的。
熱應力型內裂多出現在熱處理過的大型軸類鍛件中,在大型鑄鋼件中,在方形截面的零件以及大型齒圈中也有時出現。在軸類鍛件中有縱向內裂和橫向內裂之分,其裂紋特點是彎彎曲曲,一般不延伸至工件表面。其剖面形態如下圖所示。

工件之所以產生內裂及斷裂,是由於材料所承受的應力超過了材料本身的破斷抗力。因此,我們的分析也必須從熱處理淬火和加熱時的應力及材料的強度和塑性兩方面考慮。
大型工件熱處理淬火過程中的應力,主要由三種應力組成,即熱應力、組織應力以及由於截面上轉變組織的比體積不同引起的應力。下面我們分別加以討論。
熱應力是熱處理過程中,工件表面和中心或薄和厚之間,由於加熱或冷卻速度不一,導致體積膨脹或收縮不均勻而產生的內應力。
一個尺寸一定的圓形工件,從高溫快速冷卻,表面冷卻快,心部冷卻慢,內外之間存在較大的溫差。由於表面先冷卻要收縮,仍然處於較高溫度的心部將阻止它的收縮,所以心部使表面受拉,相反表面使心部受壓,這種應力隨著工件內外溫差的加大而增加。但是鋼在高溫塑性階段屈服點低,塑性變形後應力將得到鬆弛,這時的熱應力不可能很大。當外部先進入彈性階段形成冷硬外殼後,將不允許按照心部需要收縮的要求改變容積和形狀,對心部的收縮將起阻礙作用。這時工件中的熱應力分布將發生改變,表面由原來的受拉轉變為受壓,心部則由受壓轉變為受拉,而且隨著冷卻的繼續進行而不斷增大。這就形成了殘餘熱應力。
組織應力是鋼在淬火冷卻時,由於表面冷卻得快先發生組織轉變(膨脹),中心或冷卻較慢的部分後發生轉變(亦膨脹),從而造成體積轉變的不等時性所產生的內應力。仍以圓形工件為例,當淬火時,它從高溫急冷,表面先發生組織轉變(膨脹),未發生組織轉變的心部將阻礙其膨脹,因而表面受壓,心部受拉。由於這時心部溫度較高而且處於奧氏體狀態,塑性較好,將發生不均勻的塑性變形使應力鬆弛。
繼續冷卻,當心部也開始轉變並體積膨脹時,由於表面已形成彈性的外殼,將阻礙它的膨脹,應力反轉為心部受壓,表面受拉形成殘餘組織應力。
由於組織轉變的比體積不同,以及在隨後冷卻過程中殘留奧氏體的分解,便形成了表面馬氏體層受壓,心部受拉的殘餘應力。
大型工件淬火後的殘餘應力主要是三種應力的疊加。它的淬火應力屬熱應力型的,其最大拉應力峰值位於圓形截面的中心區或壁厚的
處。

下圖是文獻介紹的聲150mm碳鋼在未淬透情況下的殘餘應力曲線。從圖中看出,內應力的分布是熱應力型的,中心拉應力達到最大值,並且軸向拉應力大於切向與徑向拉應力。這就是大型工件在淬火內應力作用下容易產生橫向內裂的原因。
由於大型上件在淬火後的特殊應力分布,加之表面的淬硬層有較高的強度,所以從心部拉應力峰值區開始的斷裂,若延伸至表面比較困難,從而形成內裂。
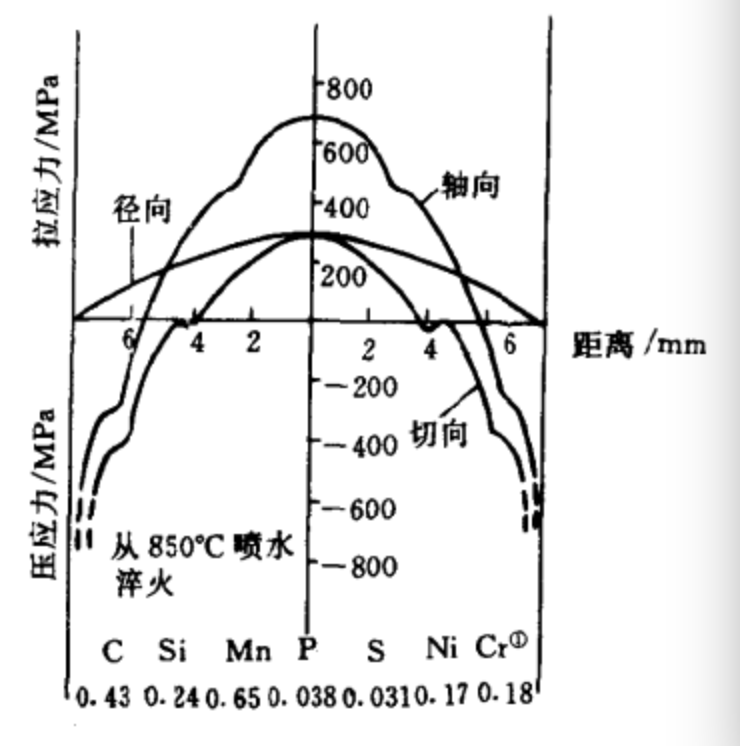
鍛造方法型
內裂這種缺陷容易產生在加工溫度過低,一次變形量過大,以及加工過程中工件截面形狀不當等情況下。下圖表示加工過程中截面形狀不當時,內裂的形成機理。由方料自由鍛造成圓棒時,如果採用(a)那樣的方法鍛造,不會引起內裂,但若用(b)所示的方法鍛造,就會在鋼材內部引起剪下應力而導致內裂。
由於這個原因,內裂大多出現在自由鍛材中,在軋材中幾乎不會產生這種缺陷。

熱處理應力型內裂的預防
熱應力型內裂產生的主要原因是工件淬火時的殘餘應力,材料中的缺陷是引起開裂的輔助原因。為了預防內裂及斷裂的發生,主要應從降低心部拉應力和提高材料破斷抗力兩方面加以考慮。
1.適當降低淬火溫度,可以減少熱應力,對防止內裂有利。因為淬火溫度越高,熱應力越大,同時,加熱溫度過高也會使奧氏體晶粒粗化,使材料強度降低。工件出爐後淬火前適當預冷,也對減小熱應力預防內裂有利。
2.淬火時,注意工件的均勻冷卻。
3.及時回火是預防內裂的有效措施。淬火後不及時回火導致殘餘應力加劇,並且隨著時間的延長,表層的殘留奧氏體繼續分解,進一步加劇了內部的拉應力。因此,大鍛件特別是合金鋼大鍛件,淬火後必須及時回火。
4.控制加熱升溫速度十分重要,快速加熱會導致內外溫差加劇,熱應力增大。特別是含碳與合金元素高的大型鍛件,低溫階段的升溫速度要嚴加控制。一般說來,大鍛件在低溫階段的升溫速度要控制在30~70℃/h。回火加熱時,因工件有很大的殘餘應力,升溫時更要注意。
5.減少材料中的缺陷,提高材料本身的強度對防止淬裂也很重要。為了提高材料本身的強度,對於晶粒粗大的工件,可先進行一次正火,以便細化晶粒,提高強度。
6.帶有內孔的大型工件淬火時,內孔同時冷卻對防止淬裂有利。在調質熱處理聲640mm×1100mm(帶有Φ380mm盲孔)40Cr鋼叉頭時,由於吊裝時盲孔朝下,盲孔內壁得不到充分冷卻,致使4個工件全部在盲孔底部產生裂紋。後來改用盲孔朝上吊裝,孔內冷卻條件改善,本批處理的6件全部合格。