專利背景
中國以
輪胎為主的
橡膠消費持續高增長,使中國成為世界最大的廢橡膠產生國,廢舊橡膠的綜合利用是橡膠工業循環經濟的核心,對於降低中國橡膠資源對外依存度,節約石化資源,保護環境具有重要意義。利用物理,化學或者生物等方法,打開廢橡膠三維交聯網路,製備再生膠是2012年前中國廢橡膠循環再利用的最主要方式,理想的再生是只斷開交聯鍵,而橡膠分子主鏈(C-C分子鏈)保持完好。據不完全統計,中國2010年再生膠產量達到300萬噸左右,再生膠產品套用於橡膠製品各行業,其中管帶、
膠鞋和輪胎的
再生膠使用量居多。
再生膠行業經過多年的發展與技術創新,形成了以“高溫高壓動態脫硫”為主的
脫硫再生工藝。其脫硫反應是在脫硫罐中完成,將再生劑和水一起加入脫硫罐中,工作壓力2.2兆帕左右,工作溫度220℃左右,脫硫時間3小時左右後,泄壓取料得脫硫膠粉,然後經3~4台高速精煉機壓片得到再生膠,得到的再生膠呈現出較優異的加工性能和力學性能,套用廣泛。從脫硫反應機理來看,高溫高壓動態脫硫屬於化學再生,即在外界熱的作用下,活化劑在軟化劑的輔助下,滲透並進入廢橡膠內部與之發生反應,破壞交聯網路,使之成為準線性化的、可再加工的過程。但是利用此方法再生劑向廢橡膠的滲透是在高溫高壓較長時間內完成,不僅能耗高、存在嚴重的安全隱患,而且長時間的高溫反應增加了主鏈斷裂的機率,不利於再生膠的利用性能。因此,通過縮短高溫反應時間並保證脫硫膠粉的隔氧冷卻,以進一步提高再生膠的力學性能;實現生產過程的安全簡單連續、節能和環保,是廢舊橡膠再生行業可持續發展的關鍵所在。
螺桿擠出機因其可連續化生產、生產效率高、適用範圍廣等優勢,逐漸被中國國內外學者套用於廢橡膠脫硫再生領域。日本的Matsushita等採用雙螺桿擠出機再生廢橡膠,通過雙螺桿擠出機對廢橡膠施加高溫高壓高剪下的作用,實現廢橡膠的脫硫再生,其脫硫溫度在100℃~520℃。並通過在螺桿內引入某種除氣載體帶走分解產物,達到連續生產、淨化排氣的作用。
陶國良等(CN101418082B廢橡膠綠色脫硫工藝方法)將廢橡膠顆粒經加料區加入雙螺桿橡膠脫硫反應裝置中,經壓縮剪下區的高溫、高壓和剪下能共同作用,使橡膠的交聯鍵發生斷裂,然後排氣淨化,再經過雙螺桿橡膠脫硫反應裝置混煉區的混煉,生成再生膠。其加料區溫度為250℃~350℃,因加料過程不可避免得會帶入氧氣,過高的進料口溫度會導致氧化,不僅不利於再生膠的力學性能,而且會導致進料口處冒煙,污染環境;壓縮剪下區的壓力位20兆帕~80兆帕,如此高的壓力不僅對設備材質、設計要求嚴格,增加成本,而且增加了安全隱患。
馬如琦等(CN1908042A.2007.一種橡膠脫硫的方法及裝置)將已硫化橡膠經過粉碎、篩選、磁選後再經過微波爐進行微波脫硫,脫硫後由微波爐出料口直接進入擠出機餵料口,通過擠出機進行塑化、降溫、過濾,最後完成整個生產過程。可以看出此方法工藝複雜,效率不高,而且微波再生廢橡膠溫度不易控制,所得再生膠質量不穩定,僅在實驗室取得成功,尚未見工業化報導。
張立群等(CN101508795A.Aug.19,2009.一種採用雙螺桿擠出機脫硫再生硫化橡膠的方法)引入雙階螺桿擠出機脫硫的概念,提出採用物理化學聯動和雙螺桿聯動相結合的方法,將經過預處理的膠粉加入第一台雙螺桿擠出機中加熱加壓,溫度在200~230℃,壓力在2~3兆帕,然後側向對接入第二台擠出機繼續加溫加壓,使溫度達到250~300℃,壓力達3~5兆帕。雖然此方法能夠實現工藝的連續、環保,但是連續的高溫高壓高剪下可能導致主鏈的過分降解,不利於保證力學性能。
以上利用雙螺桿擠出機脫硫方法的技術核心,都是通過雙螺桿擠出機同時施加高溫高壓高剪下的條件甚至是藉助化學助劑的作用,來破壞廢橡膠的交聯網路。通過施加剪下力選擇性打斷交聯鍵的理論基礎是利用C-C鍵、C-S鍵和S-S鍵彈性係數的差別,相對而言,在剪下的作用下,S-S鍵更容易斷鏈。但是,由於在硫化膠交聯網路內S-S鍵的數目遠遠少於C-C鍵,很難保證能夠通過高剪下力的施加,只斷裂S-S鍵而不破壞C-C鍵。特別是在高溫條件下,通過高剪下作用破壞交聯網路時,更容易導致橡膠主鏈歧化反應的發生,導致主鏈降解嚴重。雖然高溫和高剪下的脫硫條件,能夠高效地破壞廢橡膠三維網路結構,但是由於其會導致大量的主鏈降解,使再生膠的力學性能降低。因此,合適的脫硫工藝條件應該是在隔氧、低剪下的條件下,通過高溫化學作用快速脫硫再生。
此外,傳統工業利用高速精煉機對脫硫膠粉進行強行剪下、捏煉,以達到降低再生膠門尼粘度的作用,這是整個再生膠生產過程中能耗最大、污染最嚴重、工作量最大的環節。因此,通過冷卻輸送裝置對脫硫膠粉的隔氧冷卻後,利用密閉剪下設備,低溫下對其施加進一步強剪下以達到降低門尼粘度的目的,不僅實現了生產過程的安全簡單連續、節能和環保,而且有利於進一步提高再生膠的力學性能。
發明內容
專利目的
該發明的目的在於克服2012年10月之前的廢橡膠再生技術的不足,提供一種利用雙階雙螺桿擠出機連續製備再生膠的方法。
技術方案
《一種雙階雙螺桿擠出機連續製備再生膠的方法》其特徵是將廢膠粉與再生劑於攪拌機內60℃~120℃下預處理1分鐘~15分鐘後在50℃~100℃靜置12小時~36小時,加入第一台異向雙螺桿擠出機,通過控制擠出機的加熱段溫度在150℃~220℃,反應段溫度在220℃~320℃,冷卻段溫度在80℃~220℃,反應1~10分鐘後由擠出機擠出,然後經過渡輸送裝置冷卻至40℃~100℃後對接進入第二台同向雙螺桿擠出機,在60℃~100℃下剪下擠出後,即可得到所製備的再生膠;所述的再生劑包括軟化劑和活化劑:軟化劑是煤焦油、松焦油、妥爾油、環烷油、雙戊烯、石蠟油、油酸、松香的一種或幾者的混合物,活化劑是芳烴二硫化物、多烷基苯酚硫化物、苯基硫醇、胺基化合物的一種或幾者的混合物;廢膠粉與軟化劑、活化劑的質量比為100:(5~20):(0.1~3)。
所用異向雙螺桿擠出機最好是全嚙合異向雙螺桿擠出機、部分嚙合異向雙螺桿擠出機或非嚙合異向雙螺桿擠出機的一種。所用同向雙螺桿擠出機最好是全嚙合同向雙螺桿擠出機或部分嚙合同向雙螺桿擠出機的一種。異向雙螺桿擠出機所用的螺桿最好是整體機加工而成或由螺桿元件在芯軸上組合而成中的一種。同向雙螺桿擠出機所用的螺桿最好是由螺桿元件在芯軸上組合而成的。螺桿元件最好包括螺紋元件、嚙合塊和齒形混煉塊中的兩種或三種。所用廢膠粉以輪胎胎面或胎體廢膠粉、邊角余料、廢膠鞋、廢乙丙橡膠、廢丁基膠、廢丁腈橡膠中的一種為宜。
改善效果
《一種雙階雙螺桿擠出機連續製備再生膠的方法》採用兩台串聯的雙螺桿擠出機作為再生膠生產設備,保證了廢橡膠再生過程的安全連續化生產;整個脫硫工藝在密閉條件下完成,煙氣污染減少,改善了工廠的工作環境;無需後續3~4台精煉機,降低了勞動強度和能耗,節約了成本;在預處理過程中實現了再生劑向廢橡膠基體的均勻滲透擴散,進而保證了在螺桿內的高溫條件下短時間內即可完成有效的脫硫反應,提高了脫硫效率。
該發明充分發揮了異向雙螺桿擠出機和同向雙螺桿擠出機各自的優勢,將其套用於廢橡膠再生領域。將異向雙螺桿擠出機作為脫硫設備取代傳統的高溫高壓動態脫硫罐,其螺紋元件異向旋轉,剪下力較小,避免了高溫下高剪下導致的大量主鏈破壞,進而保證了再生膠的性能;異向雙螺桿擠出機正位移輸送能力強,不僅提高了產量,而且降低了能耗,保證了經濟效益。將同向雙螺桿擠出機作為精煉設備取代傳統的精煉機,其螺紋元件同向旋轉,剪下力強,在低溫條件下,對脫硫膠粉能夠施加充分的剪下、分流和置換作用,在不影響再生膠力學性能的前提下,降低其門尼粘度,所得再生膠質量穩定。比如利用輪胎胎面廢膠粉得到的再生膠性能指標均超過了國家特級標準;利用廢乙丙橡膠得到的再生膠不僅基本力學性能達到國家特級標準,而且與與純膠並用作防水卷材,耐老化性能並無太大變化;又如利用廢輪胎內胎脫硫得到的丁基再生膠,氣密性並無太大變化。因此,該發明經濟效益和社會效益明顯,具有廣闊的市場套用前景。
附圖說明
圖1是《一種雙階雙螺桿擠出機連續製備再生膠的方法》工藝路線示意圖。其中,1-計量餵料裝置;2-異向雙螺桿擠出機;3-冷卻輸送裝置;4-同向雙螺桿擠出機;5-機頭。
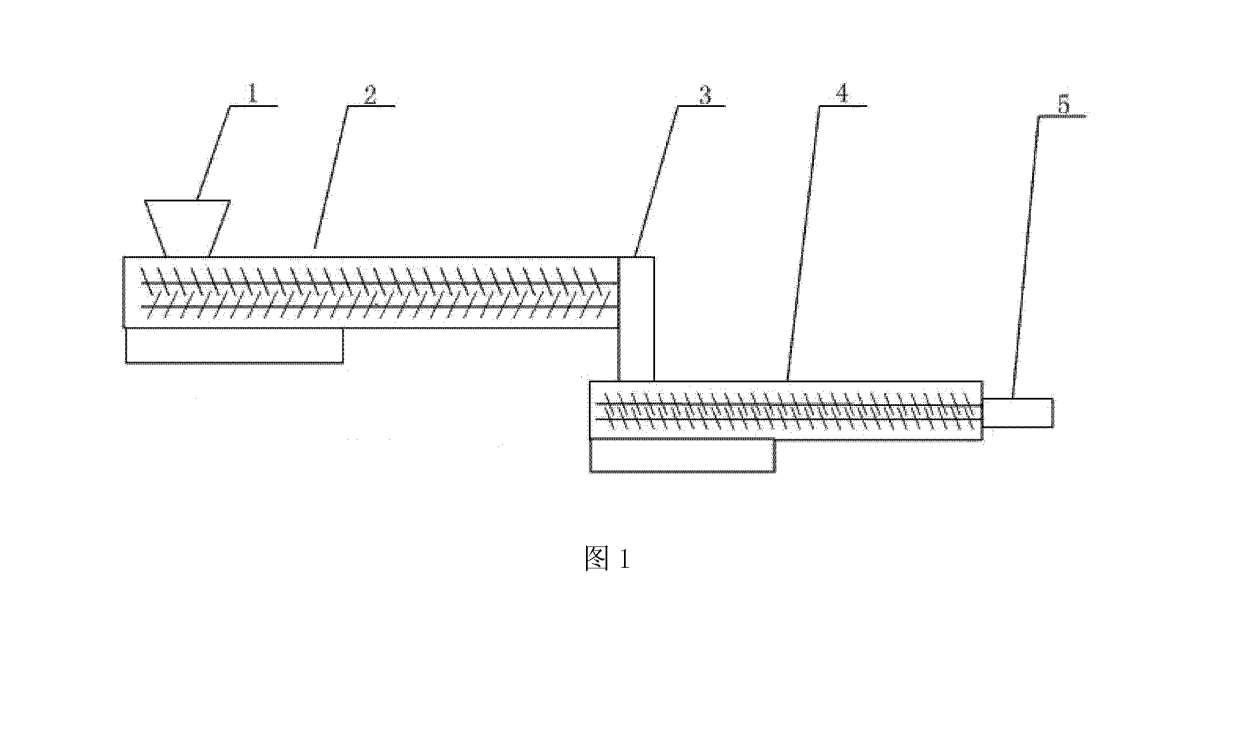
附圖說明
權利要求
1.《一種雙階雙螺桿擠出機連續製備再生膠的方法》其特徵是將廢膠粉與再生劑於攪拌機內60℃~120℃下預處理1分鐘~15分鐘後在50℃~100℃靜置12小時~36小時,加入第一台異向雙螺桿擠出機,通過控制擠出機的加熱段溫度在150℃~220℃,反應段溫度在220℃~320℃,冷卻段溫度在80℃~220℃,反應1~10分鐘後由擠出機擠出,然後經過渡輸送裝置冷卻至40℃~100℃後對接進入第二台同向雙螺桿擠出機,在60℃~100℃下剪下擠出後,即可得到所製備的再生膠;所述的再生劑包括軟化劑和活化劑:軟化劑是煤焦油、松焦油、妥爾油、環烷油、雙戊烯、石蠟油、油酸、松香的一種或幾者的混合物,活化劑是芳烴二硫化物、多烷基苯酚硫化物、苯基硫醇、胺基化合物的一種或幾者的混合物;廢膠粉與軟化劑、活化劑的質量比為100:(5~20):(0.1~3)。
2.根據權利要求1的方法,其特徵是所用異向雙螺桿擠出機是全嚙合異向雙螺桿擠出機、部分嚙合異向雙螺桿擠出機或非嚙合異向雙螺桿擠出機的一種。
3.根據權利要求1的方法,其特徵是所用同向雙螺桿擠出機是全嚙合同向雙螺桿擠出機或部分嚙合同向雙螺桿擠出機的一種。
4.根據權利要求1或2的方法,其特徵是異向雙螺桿擠出機所用的螺桿是整體機加工而成或由螺桿元件在芯軸上組合而成中的一種。
5.根據權利要求1或3的方法,其特徵是同向雙螺桿擠出機所用的螺桿是由螺桿元件在芯軸上組合而成的。
6.根據權利要求4或5的方法,其特徵是螺桿元件包括螺紋元件、嚙合塊和齒形混煉塊中的兩種或三種。
7.根據權利1所述的方法,其特徵是所用廢膠粉為輪胎胎面或胎體廢膠粉、邊角余料、廢膠鞋、廢乙丙橡膠、廢丁基膠、廢丁腈橡膠中的一種。
實施方式
實施例1
採用22目的廢載重子午線輪胎胎面膠粉100份,加入妥爾油2份、松焦油3份為軟化劑,2,2’-二硫化雙(6-叔丁基對苯酚)1.0份為活化劑,於攪拌機內90℃下將膠粉與上述軟化劑和活化劑混合攪拌15分鐘後置於70℃下靜置24小時,然後通過供料裝置將其加入第一台部分嚙合的異向雙螺桿擠出機(D=30毫米,L/D=24,其中第一區段為加熱段,第二區段為反應段,第三、四段為冷卻段,以下實施例中除有特殊說明均採用此型號的擠出機),使各加熱區段的溫度分別設定為160℃、280℃、180℃、80℃,螺桿轉速為100轉/分鐘,反應3分鐘後物料擠出後,經過渡輸送裝置冷卻至60℃,然後對接進入第二台全嚙合同向雙螺桿擠出機(D=34毫米,L/D=34,以下實施列中除有特殊說明均採用此型號的擠出機),料筒溫度設定為80℃,螺桿轉速為200轉/分鐘在擠出機內剪下的作用下由機頭擠出後,即得所製備的再生膠。所得再生膠性能如下:灰分=6.2%,丙酮抽出物=13.5%,門尼粘度ML100℃(1+4分鐘)=92;按照GB/T13460-2008再生膠再硫化配方硫化,得硫化膠力學性能如下:拉伸強度=15.1兆帕,扯斷伸長率=480%。
國家特級A1標準:灰分≤10%,丙酮抽出物≤18%,門尼粘度ML100℃(1+4分鐘)≤95,拉伸強度≥14.0兆帕,扯斷伸長率≥420%。
實施例2
採用22目的廢載重子午線輪胎胎面膠粉100份,加入煤焦油10份、松焦油10份為軟化劑,2,2’-二硫化雙(6-叔丁基對苯酚)0.1份為活化劑,於攪拌機內60℃下將膠粉與上述軟化劑和活化劑混合攪拌8分鐘後置於50℃下靜置12小時,然後通過供料裝置將其加入部分嚙合的異向雙螺桿擠出機,使各加熱區段的溫度分別設定為180℃、230℃、160℃、120℃,螺桿轉速為80轉/分鐘,反應8分鐘後物料擠出後,經過渡輸送裝置冷卻至40℃,然後對接進入第二台部分嚙合同向雙螺桿擠出機,料筒溫度設定為70℃,螺桿轉速為180轉/分鐘,在擠出機內剪下的作用下由機頭擠出後,即得所製備的再生膠。所得再生膠性能如下:灰分=7.5%,丙酮抽出物=16.8%,門尼粘度ML100℃(1+4分鐘)=60;按照GB/T13460-2008再生膠再硫化配方硫化,得硫化膠力學性能如下:拉伸強度=16.3兆帕,扯斷伸長率=535%。
國家特級A1標準:灰分≤10%,丙酮抽出物≤18%,門尼粘度ML100℃(1+4分鐘)≤95,拉伸強度≥14.0兆帕,扯斷伸長率≥420%。
實施例3
採用22目的廢載重子午線輪胎胎面膠粉100份,加入妥爾油8份、松焦油6份、松香4份為軟化劑,二苯基二硫3.0份為活化劑,於攪拌機內100℃下將膠粉與上述軟化劑和活化劑混合攪拌4分鐘後置於80℃下靜置24小時,然後通過供料裝置將其加入非嚙合的異向雙螺桿擠出機,使各加熱區段的溫度分別設定為160℃、260℃、180℃、140℃,螺桿轉速為160轉/分鐘,反應1分鐘後物料擠出後,經過渡輸送裝置冷卻至75℃,然後對接進入第二台部分嚙合同向雙螺桿擠出機,料筒溫度設定為85℃,螺桿轉速為250轉/分鐘,在擠出機內剪下的作用下由機頭擠出後,即得所製備的再生膠。所得再生膠性能如下:灰分=7.0%,丙酮抽出物=14.2%,門尼粘度ML100℃(1+4分鐘)=80;按照GB/T13460-2008再生膠再硫化配方硫化,得硫化膠力學性能如下:拉伸強度=15.0兆帕,扯斷伸長率=485%。
國家特級A1標準:灰分≤10%,丙酮抽出物≤18%,門尼粘度ML100℃(1+4分鐘)≤95,拉伸強度≥14.0兆帕,扯斷伸長率≥420%。
實施例4
採用廢乙丙橡膠粉100份,加入環烷油5份為軟化劑,苯基硫醇0.2份、正丁胺0.2份為活化劑,於攪拌機內120℃下將膠粉與上述軟化劑和活化劑混合攪拌1分鐘後置於100℃下靜置36小時,然後通過供料裝置將其加入全嚙合的異向雙螺桿擠出機,使各加熱區段的溫度分別設定為220℃、320℃、220℃、140℃,螺桿轉速為30轉/分鐘,反應15分鐘後物料擠出後,經過渡輸送裝置冷卻至100℃,然後對接進入第二台全嚙合同向雙螺桿擠出機,料筒溫度設定為100℃,螺桿轉速為300轉/分鐘,在擠出機內剪下的作用下由機頭擠出後,即得所製備的再生膠。將其於20份純乙丙橡膠並用,性能如下:拉伸強度12.5兆帕,斷裂伸長率365%,熱空氣老化(80℃×168小時)拉伸強度變化率-26%,扯斷伸長率變化率-17%。
原始膠料性能:拉伸強度14.5兆帕,斷裂伸長率385%,耐老化性能熱空氣老化(80℃×168小時)拉伸強度變化率-23%,扯斷伸長率變化率-18%。
實施例5
採用廢乙丙橡膠粉100份,加入石蠟油17份為軟化劑,十六烷基胺3.0份為活化劑,於攪拌機內100℃下將膠粉與上述軟化劑和活化劑混合攪拌10分鐘後置於80℃下靜置20小時,然後通過供料裝置將其加入部分嚙合的異向雙螺桿擠出機,使各加熱區段的溫度分別設定為200℃、300℃、200℃、120℃,螺桿轉速為100轉/分鐘,反應5分鐘後物料擠出後,經過渡輸送裝置冷卻至70℃,然後對接進入第二台全嚙合同向雙螺桿擠出機,料筒溫度設定為85℃,螺桿轉速為150轉/分鐘,在擠出機內剪下的作用下由機頭擠出後,即得所製備的再生膠。所得再生膠性能如下:灰分=12.0%,丙酮抽出物=16.5%,門尼粘度ML100℃(1+4分鐘)=45;按照GB/T13460-2008再硫化配方硫化,得硫化膠力學性能如下:拉伸強度=7.6兆帕,扯斷伸長率=340%。
乙丙再生膠國家標準:灰分≤20%,丙酮抽出物≤30%,門尼粘度ML100℃(1+4分鐘)≤65,拉伸強度≥5.5兆帕,扯斷伸長率≥260%。
實施例6
採用廢輪胎內胎丁基膠100份,加入雙戊烯10份為軟化劑,正丁胺2.0份為活化劑,於攪拌機內110℃下將膠粉與上述軟化劑和活化劑混合攪拌6分鐘後置於90℃下靜置18小時,然後通過供料裝置將其加入部分嚙合的異向雙螺桿擠出機,使各加熱區段的溫度分別設定為180℃、300℃、180℃、140℃,螺桿轉速為40轉/分鐘,反應10分鐘後物料擠出後,經過渡輸送裝置冷卻至80℃,然後對接進入第二台全嚙合同向雙螺桿擠出機,料筒溫度設定為90℃,螺桿轉速為320轉/分鐘,在擠出機內剪下的作用下由機頭擠出後,即得所製備的再生膠。所得再生膠性能如下:灰分=6.5%,丙酮抽出物=10.6%,門尼粘度ML100℃(1+4分鐘)=64;按照GB/T13460-2008再生膠再硫化配方硫化,得硫化膠力學性能如下:拉伸強度=8.6兆帕,扯斷伸長率=510%,氣體阻隔係數1.24。
丁基再生膠國家標準:灰分≤10%,丙酮抽出物≤15%,門尼粘度ML100℃(1+4分鐘)≤70,拉伸強度≥6.8兆帕,扯斷伸長率≥460%;原始膠料氣體阻隔係數為1.28。
榮譽表彰
2017年12月11日,《一種雙階雙螺桿擠出機連續製備再生膠的方法》獲得第十九屆中國專利優秀獎。