形成原因
《CRTSⅠ型無砟軌道軌道板單元台座製造工法》的形成原因是:
中鐵八局根據中國國內外的先進經驗和
軌道板產品的特點進行了軌道板模型的設計、製造及生產線工藝布置方式的初步嘗試,並取得了試製和批量生產的成功經驗。
混凝土軌道板外形尺寸簡單,主要尺寸為4930毫米×2400毫米×190毫米,但製造要求精度高,長寬控制±3毫米,高度要求0~3毫米,產品平整度要求高,其他
預埋件位置要求準確,產品外觀質量要求高。必須進行工廠化批量生產,才能保證產品質量。
因軌道板要求精度高,模型設計為底部振搗結構,模型重量大,為保證軌道板的表面平整度達到要求,需設計專用台座進行生產。該方法設備投入少,勞動力用量少,一人可完成多項工作,各台座生產不相互影響,投產快,見效快,產品質量穩定。
工法特點
《CRTSⅠ型無砟軌道軌道板單元台座製造工法》的工法特點是:
一、用單元台座法生產軌道板,模型設計為一套模型一次生產一塊軌道板形式,模型分為底模、側模、端模、內模(框架型),通過幾個模型的組合、拆分實現軌道板生產的合模、脫模。模型設計和製作精度要求較高,能充分保證軌道板的各項外形尺寸要求,生產中主要需控制軌道板模型基礎不發生較大變形,
脫模、合模時不損傷軌道板。軌道板鋼筋要求進行絕緣測試,電阻大於2兆歐,軌道板鋪設線上路上,兩標準軌距鋼軌間電感和電阻偏差在規定範圍內,對信號傳輸不產生影響。
二、單元台座法生產軌道板具有較多優點:
1.能保證軌道板精確的外形尺寸,長度±3毫米,寬度±3毫米,高度0~3毫米,板面平整度1毫米,翹曲量3毫米。
2.針對模型設計工作基坑,基坑強度容易保證,變形後容易調整。每套模型單獨設計蒸汽養護系統,模型之間不相互干擾。
3.模型結構簡單,組裝容易,模型不受張拉力,且經過時效處理,不易變形。增加模型使用壽命。
4.生產速度不受限制,可增加操作工人加快生產節奏。
5.設備少,主要大型設備有門吊、攪拌站、鍋爐。
6.基建投入少,建設速度快,技術難度降低。
7.整個場地布置簡單,機具少,蒸汽管道布置在基坑內,不影響工人施工,保證施工安全。投產快、見效快、產品質量穩定(圖1)。
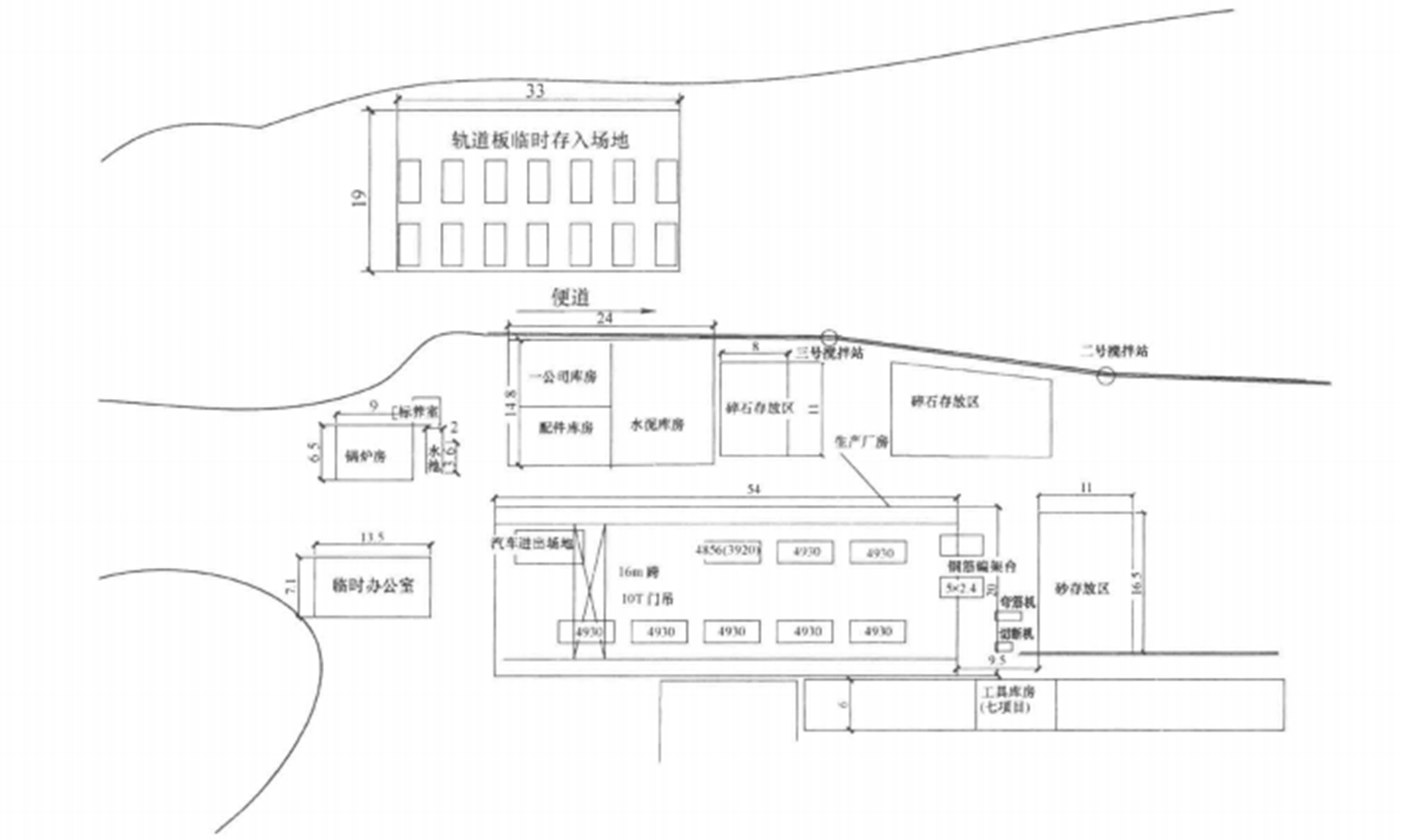
圖1 遂渝線軌道板生產線平面布置示意圖
操作原理
適用範圍
《CRTSⅠ型無砟軌道軌道板單元台座製造工法》的適用範圍是:
各種類型無砟軌道用混凝土軌道板,隧道、路基、橋樑上軌道板,過渡段用軌道板的生產;減振型軌道板、雙向預應力軌道板、框架型軌道板、預應力框架板、橫向預應力軌道板的生產。
工藝原理
《CRTSⅠ型無砟軌道軌道板單元台座製造工法》的工藝原理敘述如下:
一、該工藝設計的目的是為保證產品能達到《遂渝線無砟軌道用混凝土軌道板技術條件》中對產品質量的要求。軌道板產品對塑膠套管位置,鋼絞線位置,表面平整度,軌道板絕緣性能等要求較高,鋼模的製作和生產線的設計全部有針對性地考慮了這些問題,使生產出的產品能完全滿足標準要求。
二、模型設計:模型是保證產品外形外觀質量的基礎。根據軌道板生產工藝的特點,模型不受張拉力作用,因此模型設計以滿足產品成形質量、通用性、延長使用壽命為主,要求模型具有足夠的強度、剛度、穩定性和精確的結構尺寸。
1.底模採用鋼板拼焊而成,底模面板焊接後變形較大,製作時加厚鋼板,時效處理後進行機加工,保證底模表面平整度,平整度不大於0.2毫米/0.5米,且底模筋板避開預埋套管孔位置。
2.側模、端模採用鋼板拼焊而成,面板同底模一樣進行時效和機加工處理,加強筋板位置避開鋼絞線位置和起吊螺母位置,板式軌道板鋼模側模、端模上設計有預應力鋼絞線錨穴孔,保證鋼絞線的位置,同時設計側模、端模拖拉裝置,保證側模、端模順利脫模。
3.底模上設計振動器安裝位置,保證灌注混凝土時順利進行密實。振動器之間設計鋼模安裝支撐台座,每套鋼模設計10個支撐架,保證鋼模的穩定、平整。
4.框架型軌道板設計有內模,採用鋼板拼焊,進行時效和機加工處理,內模分成4塊進行組合,方便脫模。
5.端模、內模與底模間採用螺栓進行定位,保證軌道板的長寬尺寸要求。
三、軌道板鋼模基礎設計
1.根據軌道板鋼模設計特點和所確定的工藝流程,進行鋼模工作基坑設計。鋼模放置在基坑上,鋼模受震動後不產生較大變形;工人可進入基坑內進行操作,在鋼模下部安設振動器、安裝預埋套管固定螺栓等。鋼模設計寬度為2.8米,長度為5.33米,長度和寬度方向均有拖拉絲桿,鋼模下部設有支撐台座,台座之間布置振動器,因此考慮基坑寬度設為2.6米,長度設為6.5米,高度設計1.3米,端部設定階梯,方便工人上下(圖2)。

圖2 軌道板鋼模基礎
2.基坑內設定10個承台,鋼模支撐台座放置在相應承台上,承台上設定預埋鋼板,預埋鋼板上設定定位鋼板,以固定鋼模位置。基坑下方設計1%的縱坡,端部設計一個集水坑,蒸汽冷凝水流入基坑內,用水泵抽出。蒸汽管道安裝在基坑底部兩邊,與鋼模距離稍遠,避免蒸汽對鋼模和混凝土產生過大影響,保證低溫蒸汽養護。
四、鋼絞線位置控制:板式軌道板有縱向和橫向預應力鋼絞線,鋼絞線位置偏差要求為±1毫米。在設計時,對側模、端模上錨穴孔的位置進行控制,生產時,由於為後張法生產,需對鋼絞線進行預緊,將擠壓好的鋼絞線從錨穴固定端穿入,張拉端穿出,在張拉端安裝鋼絞線張緊裝置,用扳手將緊固裝置擰緊,保證鋼絞線在鋼模內平直。
五、封頂塑膠套管的定位控制:塑膠套管位置精度要求為±1毫米,在設計和製作時要求套管位置偏差±0.2毫米,並對套管孔的垂直度進行控制,設計專用套管螺栓從鋼模底部對套管進行固定,能保證套管位置達到標準要求。
六、長度、寬度控制:軌道板長度、寬度要求為±3毫米,為保證軌道板外形尺寸,鋼模設計時在底模上設計一個5毫米高凸台,側模、端模合模後緊靠凸台,側模、端模之間也互相制約固定,保證產品外形尺寸。
七、鋼筋位置控制:根據軌道板技術條件的要求,鋼筋位置偏差控制在10毫米以內,為保證鋼筋位置的準確性,同時提高編架速度,設計專用編架裝置,在長木方上釘上小木方,將每根鋼筋位置固定,保證了下層鋼筋位置。上層鋼筋通過人工編架時,先將兩端與下層對位準確,再進行其他位置編架。採用編架裝置,能正確擺放鋼筋規格、數量,保證編架質量,減少入模後鋼筋的調整量,同時能提高編架速度。根據現場統計,一塊KJ4930框架板鋼筋骨架,6人1.5小時能順利編架完成,保證生產順利進行。
八、絕緣性能控制:軌道板設計為絕緣型軌道板,縱向鋼筋全部採用環氧樹脂塗層鋼筋,橫向為普通鋼筋,為保證縱橫向鋼筋的絕緣效果,鋼筋交點之間墊一層黃臘管,並採用絕緣綁紮線進行綁紮,最後用兆歐表進行電阻測試,達到要求的鋼筋骨架才能進入下道工序。
九、平整度:軌道板要求表面平整度為1毫米,鋼筋設計全部為對稱形式,平整度保證必須通過鋼模來實現,底模面板採用機加工保證平整度,為防止板面翹曲,定期對鋼模基礎進行檢測,發現標高超過範圍時及時對承台進行調整,保證鋼模使用狀態的平整度。軌道板脫模後對放置支點進行調整,使軌道板不在存放中產生變形。
十、密實性控制:軌道板結構為薄壁型,厚度僅為190毫米,鋼模設計採用11台1.5千瓦的高頻振動器進行振動,但鋼模側壁氣泡無法完全排除,因此採用振動棒對側模和端模、內模位置進行輔助振動,軌道板底面平整度要求為5毫米/1米,為達到要求,加強振動效果,採用表面振動器進行面振,將混凝土漿振出,保證表面抹面光滑,平整度達到要求,同時能控制軌道板高度在0~3毫米範圍內。
十一、養護控制
1.由於軌道板要求恆溫溫度為45℃,根據熱工計算,選用1台1噸燃油蒸汽鍋爐,能保證8套模型低溫蒸汽養護要求。
2.軌道板採用台座式生產,每個基坑內均安裝2條蒸汽管道,管道上合理布置Φ5圓孔,能保證蒸汽對產品的養護達到規定要求;同時設計可拆裝式養護支架,便於生產,整塊板養護篷布保持一定的高度,保證蒸汽在篷布內暢通,利於混凝土的養護。養護篷布採用新產品三防塗塑篷布,密封效果好。
3.在軌道板初凝前,須對軌道板進行灑水養護,並覆蓋塑膠薄膜,避免出現表面收縮裂紋;軌道板脫模後進行7天灑水保濕養護,有利於混凝土後期強度增長。由於前期灑水養護、蒸汽養護、脫模後灑水養護,軌道板混凝土強度增長快,不出現表面收縮裂紋,乾縮裂紋等,外觀質量優良。
十二、張拉控制:預應力軌道板設計採用Φ12.7的鋼絞線,採用專用低回縮錨具、錯墊板,使用專用千斤頂進行張拉,千斤頂設計有伸長值讀數,張拉以油表讀數顯示為主,預應力筋伸長值作為校核,可提高張拉力控制精度,張拉後鋼絞線基本無縮量,保證鋼絞線的預應力效果,充分保證產品質量。張拉時兩台千斤頂同時對稱進行張拉,保證軌道板不產生變形。鋼絞線下料時預留張拉鋼絞線的長度,保證千斤頂順利進行張拉。
施工工藝
《CRTSⅠ型無砟軌道軌道板單元台座製造工法》的工藝流程見軌道板生產工藝流程圖(圖3)。

圖3 雙向預應力混凝土軌道板工藝流程圖
《CRTSⅠ型無砟軌道軌道板單元台座製造工法》的操作要點如下:
一、模型定位:模型放置在基坑上,基坑預埋件上焊接定位鋼板對模型進行定位,定期對模型進行檢測,基礎變形後及時加墊鋼板保證鋼模平整度,模型與基礎間墊減振橡膠板,防止振動力的減弱。
二、鋼筋間距及保護層控制:鋼筋保護層要求為+5毫米,-3毫米,鋼筋放入鋼模後,無法進行保護層控制,必須在鋼筋編架時將塑膠墊塊綁紮在底面鋼筋和四周,使合模後鋼筋位置能夠達到要求。鋼筋間距要求為±10毫米,編架時必須在專用編架裝置上進行編架,對鋼筋進行定位,保證間距要求。
三、鋼筋絕緣控制:軌道板鋼筋骨架要求進行絕緣處理,必須在骨架編架完成後進行,用兆歐表對每兩根鋼筋之間的電阻進行測試,電阻達到2兆歐,方可進行下道工序。
四、上預埋件:在鋼筋骨架入模後,開始安裝各種配件,安裝塑膠套管、CA砂漿灌注孔芯棒時必須有一人在上扶住配件,一人在工作坑內擰緊螺栓,並保證每件均擰緊,無鬆動現象。安裝起吊螺母在模型側面進行,用相應的起吊螺栓將其固定,並綁紮螺母外螺旋筋,塑膠套管外螺旋筋,保證各螺旋筋的位置正確。
五、灌注、振動控制:所有配件、鋼筋檢查後,進行混凝土灌注,用天車吊灰斗到模型上方將混凝土灌入模型。灌注必須分層進行下料,先用底部振動器進行底振;灌注第二罐混凝土時用插入式振動棒進行混凝土振動,不能與鋼模垂直接觸;下料完成後用表面振動器進行面振,振動時間約20~30分鐘,以表面泛漿,混凝土不再下沉、無氣泡溢出為度,保證產品內實外美。振動後用抹子抹平混凝土表面,注意填邊填角。混凝土開始凝結後應及時進行表面灑水,然後覆蓋塑膠薄膜保濕。
六、卸預埋件:混凝土養護達到脫模強度後,開始卸各種配件,包括套管固定螺栓、錨墊板固定螺栓,側模、端模定位螺栓,卸套管固定螺栓時應注意方向,防止反向操作,損傷尼龍套管及軌道板。
七、養護控制:每套模型均有獨立的養護系統,蒸汽管道在基坑最下方,蒸汽充滿養護篷布內。養護過程嚴格按照試驗室下發的養護通知執行,靜停時間在3小時以上,升溫速度控制不大於15℃/小時,恆溫溫度控制在45±5℃之間,降溫速度控制不大於15℃/小時,脫模時產品溫度與環境溫度相差不大於15℃,冬季應嚴格控制降溫必須達到要求方可脫模。
八、脫模:在所有預埋件螺栓卸完後,利用側模和端模上的水平絲桿進行脫模,用專用起吊裝置將軌道板緩慢吊離模型。
九、產品堆碼:軌道板堆碼可採用平放,但不得超過4層,支點位置在起吊螺母下方左右100毫米,上下支點位置在同一垂直線上。有條件時應儘量採用立放,防止軌道板產生變形。
十、張拉:軌道板張拉必須保證混凝土強度和彈性模量達到設計要求後方可進行,張拉順序嚴格按照千斤頂使用說明進行,靜停時間為3分鐘,張拉應先橫向,後縱向連續對稱進行。
十一、自製工具:軌道板模型設計有較多螺栓連線,預埋件螺栓較多,需根據具體情況自製脫模、合模用工具,方便操作。
採用《CRTSⅠ型無砟軌道軌道板單元台座製造工法》施工時,軌道板生產主要勞動組織見表1。
以每天生產8塊P4930軌道板組織勞動力,其他規格軌道板勞動力組織可參照執行。由於單元台座法生產的特點,工人可交叉作業,一人可從事多項工作,減少了勞動力。
序號 | 班組 | 工作內容 | 人數 | 備註 |
---|
| | | | |
| | 上配件、合模、混凝土漲注,平灰、振動,卸配件、脫模、清模 | | |
| | | | |
| | | | |
| | | | |
| | | | |
| | | | |
| | | | |
材料設備
《CRTSⅠ型無砟軌道軌道板單元台座製造工法》所用的材料及設備明細如下:
一、軌道板生產採用的主要材料見表2。
二、軌道板生產主要生產設備和工裝見表3。
質量控制
《CRTSⅠ型無砟軌道軌道板單元台座製造工法》的質量控制要求如下:
一、軌道板生產按照《遂渝線無砟軌道綜合試驗段混凝土軌道板技術條件》執行。
二、軌道板外觀質量控制指標見表4。
三、混凝土軌道板外形尺寸控制指標見表5。
序號 | 檢查項目 | 允許偏差(毫米) | 每批檢驗數量(出廠檢驗) | 檢驗項別 |
---|
| | | | |
| | | | |
| | | | |
| | | | | |
| | | |
| | | |
| | | |
| | | |
| | | | |
| | | | | |
| | | |
| | | | | |
| | | | |
| | | | |
四、鋼模製造和驗收按照軌道板鋼模技術條件執行,鋼模具有足夠的剛度、鋼模底板板面平整,鋼模加工誤差控制為±0.2毫米。
五、鋼模安裝嚴格按照鋼模設計圖進行,控制安裝誤差,充分保證鋼模安裝質量。
六、生產過程中質量控制:採用自檢、專檢、互檢制度,不合格工序不能進入下道工序。每道工序均有工序檢查,保證在鋼筋、預埋件安裝質量,張拉工序有專人進行旁站檢查。項目部從操作工人、工班長、技術人員、檢查工程師到項目負責人,層層把關,嚴格考核,出現問題立即整改,嚴格保證產品質量。
七、嚴格執行混凝土軌道板施工細則和內控標準。
八、制定質量管理體系檔案,在生產過程中嚴格按照ISO 9000質量管理體系檔案程式進行管理。
安全措施
採用《CRTSⅠ型無砟軌道軌道板單元台座製造工法》施工時,除應執行國家、地方的各項安全施工的規定外,尚應遵守注意下列事項:
一、項目部嚴格按照創建“安標工地”管理辦法進行安全管理,嚴格執行國家有關安全生產的規範和規章。建立健全項目部安全組織保證體系,貫徹國家有關安全生產和勞動保護的法律、法規,強化基本知識,基本素質的培訓。
二、施工細則中提出安全注意事項,並進行安全技術交底,在設計生產線時考慮安全生產措施。
三、設專職安全員負責制定施工安全操作規程,檢查安全情況,提出改進措施。
四、堅持崗位安全培訓,杜絕“三違”現象發生。新上崗職工進行安全培訓並進行考核,合格後方可上崗。
五、所有用電設備都安裝漏電保護器。所有設備安排專人進行操作、管理,保證設備的安全性能。
六、張拉作業時有專人統一指揮,無關人員不得進入張拉場地。
七、生產線做到布局合理,機械設備安置穩固,材料堆放整齊,生產現場做到工完料清場地淨,保證現場文明衛生,安全生產。
八、項目部對危險源進行辨識,制定應急預案。
九、施工現場設醒目的安全標語、安全警示標誌。
環保措施
《CRTSⅠ型無砟軌道軌道板單元台座製造工法》的環保措施如下:
一、建立以項目經理為首的項目部環保、水保體系,實行“三同時”原則,在軌道板場設計時充分考慮環境保護、水資源保護等。項目經理部設立環保、水保組織機構,切實貫徹環保法規。嚴格執行國家及地方政府頒布的有關環境保護、水土保持的法規、方針、政策和法令,結合設計檔案和工程,及時提報有關環保設計,按批准的檔案組織實施。由專人負責,定期進行檢查。
二、安全環保部為項目部環境保護、水資源保護的常設機構,具體負責環保、水保日常工作。制梁場設專職環保員,作業班組設兼職環保員,負責梁場和班組的環保管理工作。
三、項目部環保、水保方針:環境保護,人人有責,節約用水,利國利民。
四、項目部環保、水保目標:廢水達標排放,廢渣分類堆放,定期清理。控制噪聲在90分貝(A)。
效益分析
《CRTSⅠ型無砟軌道軌道板單元台座製造工法》的效益分析如下:
一、採用台座法生產軌道板,生產線設備投入少,生產占地面積少,節約投資,軌道板存放方式靈活,生產線工藝布置可根據現場具體情況進行設計。適於現場設預製廠生產軌道板。每年可創造產值2880萬元以上,利潤100萬元以上。
二、軌道板模型設計複雜,製作精度要求較高,需專業機械廠進行加工。模型設計可更換側模、端模,同一套底模適用生產預應力板式、框架型、預應力框架型軌道板等多種形式軌道板,節省投資。
三、生產線基建投入少,建設速度快,投產快,見效快。生產線廠房全部採用PVC篷布搭建,建設速度快,易搬遷,可形成標準化生產廠。
四、軌道板生產在中國國內批量生產,項目部通過對軌道板模型設計、生產線工藝設計、基坑設計、各種操作工具的選擇和製作,保證軌道板的產品質量,操作簡單,安全可靠。
註:施工費用以2007-2008年施工材料價格計算
套用實例
《CRTSⅠ型無砟軌道軌道板單元台座製造工法》的套用實例如下:
2007年,石太客運專線Z13標段約20000塊預應力軌道板由中鐵八局集團製造並完工;2008年,武廣客運專線工程試驗段約8000塊框架式軌道板由中鐵八局製造並完工;2008年,廣珠城際軌道交通工程ZH-3標約20000塊框架式軌道板由中鐵八局施工;2009年,哈大客運專線約20000塊預應力軌道板由中鐵八局施工。以上各項工程均採用單元台座法進行施工,能保證軌道板的各項技術指標要求。
榮譽表彰
2009年10月19日,中華人民共和國住房和城鄉建設部以“建質[2009]162號”檔案發布《關於公布2007-2008年度國家級工法的通知》,《CRTSⅠ型無砟軌道軌道板單元台座製造工法》被評定為2007-2008年度國家一級工法。