Corex簡介
COREX是由奧鋼聯開發的一種使用塊礦或球團礦作原料、使用非焦煤作還原劑和燃料的熔融還原煉鐵工藝。COREX這個名字的前兩個字母CO代表Coal,是
煤的意思;中間兩個字母RE 代表Reduction,是還原的意思(煉鐵就是
還原過程);最後兩個字母EX 是Extreme,是終極目標的意思。所以COREX完整的意思是直接用煤來煉鐵作為它的終極目標。 應當說,這是煉鐵工作者夢寐以求的目標。 高爐煉鐵是用粉礦和粉煤, 但粉礦必須通過燒結廠燒結成燒結礦,粉煤必須通過煉焦廠將其結焦成焦炭,然後供高爐煉鐵。因此流程長、工序多、污染較重,而且焦煤資源稀缺。 COREX工藝是直接使用天然的塊礦和塊煤。 取消了燒結廠和煉焦廠。因而流程短、工序少、污染輕、可以不用資源稀缺的煉焦煤。COREX工藝是1977年才開始研究,1989 年才開始套用的熔融還原技術,是一項非常年輕的煉鐵技術。
在目前比較有代表性的三種(COREX、Finex和HIsmelt)
熔融還原煉鐵工藝中,COREX是最先實現工業化生產的,也是工藝最成熟的,目前,世界範圍內正在運行的COREX 爐只有7座,其中南非撒丹那的一套COREX -C2000、
印度4座和
中國寶鋼的兩座COREX-C3000,
韓國浦項另有2座改型FINEX爐,FINEX也是一種煉鐵工藝。
COREX發展歷程
COREX於20世紀70年代開發,1989年第一座年產能40萬t的COREX -C1000工廠在南非伊思
科爾廠(Lscor)實現工業化運行(目前已停產)。1995-1999年,又先後建成了4座年產能為60-80萬t的COREX-C2000工廠:一座建在韓國的
浦項制鐵(目前,該座COREX-C2000已被改造成世界第一座Finex裝置,並於2007年4月30日點火投產),一座建在南非的撒丹那(Saldanha)(65萬t/a,1998年12月建成),另外兩座建在印度的
金達爾(Jindal)(年產80萬t,分別於1999年和2001年投產)。2007年11月,寶鋼又建成投產了年產能為150萬t的COREX-C3000,標誌著COREX工藝又向前推進了一步。
COREX煉鐵工藝
COREX工藝需使用天然礦、球團礦和燒結礦等塊狀鐵料;燃料為非焦煤,為了避免爐料粘結並保持一定的透氣性,還需要加一定數量的焦炭;熔劑主要為石灰石和白雲石。原燃料經備料系統處理後,分別裝入礦倉、煤倉和輔助原料倉,等待上料。
如圖,上面是還原豎爐,塊礦、球團礦、熔劑從它的頂部加入。還原煤氣在它的中部進入。還原後的直接還原鐵從下部經螺旋輸送器排出。下面是熔融氣化爐。塊煤和直接還原鐵從頂部加入。在中下部鼓入
氧氣,下部有鐵口排出渣鐵。它產生的高溫煤氣也由頂部排出經過一系列的處理,大部分通入上部的還原豎爐。少部分與豎爐頂部的排出煤氣匯合在一起形成輸出
煤氣,作為二次能源供鋼鐵廠使用。
COREX工藝流程示意圖COREX工藝的渣鐵處理與高爐相似。
COREX各代技術
COREX-C1000
早在1989年12月, 在
南非ISCOR公司的Pretoria廠建成投產了世界上第一台年產生鐵30萬噸的Corex設備, 即C -1000。 將礦石、一定比例的焦炭和部分熔劑裝入預還原豎爐,在爐料下降過程中完成預熱和還原。降至豎爐底部的礦石已被還原成金屬化率大於90%的海綿鐵。海綿鐵(700-800℃)、非焦煤、一定比例的焦炭和熔劑通過海綿鐵螺旋加料機加入到下部的熔融氣化爐中。熔鍊氣化爐有兩個作用,即將海綿鐵熔煉成鐵水及產生還原豎爐需要的還原氣。熔融氣化爐內的燃料為非
焦煤,通過煤料斗加入到爐內,助燃劑使用工業
純氧,煤與氧燃燒放出熔煉和造氣所需的熱量。熔煉過程形成的渣鐵積存於爐缸底部。燃燒和氣化過程生成的煤氣再由爐頂連續排出,進入煤氣處理系統。處理後的煤氣一部分返回還原豎爐作為熱源和還原劑,一部分回收它用。
COREX-C2000
南非撒丹那的COREX-C2000於1998年12月建成投產,設計年產量65萬t,原料中60%~80%為塊礦,20%~40%為球團礦,每年還使用30多萬t熔劑等副原料。對煤粒度的要求是8~10mm,大於6.3mm的部分應達85%以上,小於3.5mm的要低於5%;乾燥後的煤含水量要在20%以下,固定碳含量要達到60%以上,揮發分25%~28%,P含量越低越好。熔融氣爐化拱頂溫度高達1050℃。該套COREX-C2000的設計焦比為5%,但由於使用80%的塊礦,煤的質量不佳,焦比過低時爐況不順,因此目前該設備的焦比為13%左右,其中11%從豎爐加入,2%直接加入到熔融氣化爐。燃料比1050kg/t左右,扣除5%的水分,乾基燃料比1000kg/t。正常生產狀態下,鐵水
矽含量0.5%以下,
硫0.05%左右。年產水渣量27萬t左右,渣中含SiO2 30%左右,含CaO35%左右,含MgO11.5%左右,Al2O3 15.7%左右。COREX-C2000的布料可分別從氣化爐和豎爐處加入,
煤和少量副原料從氣化爐加入。COREX熔融氣化爐爐頂的加煤孔安裝了萬向布料器,像高爐的無料鐘一樣,可以實現任意角度的布料。COREX爐中煤氣溫度高於850℃時會發生礦石粘結,低於700℃時又容易發生析炭反應。公司每年都需定期(半年一次)對爐內進行清空處理,對結塊爐料進行清除。目前COREX-C2000設備的作業率為80%-90%。由於焦炭使用量少,因此死料柱較軟,鐵口泥包不易形成,鐵口深度維持在1.5-1.9m。2002年5月,公司對COREX-C2000進行了中修,將熔融氣化爐第5、6段
鑄鐵冷卻壁換成了
銅冷卻壁,並進行了
噴塗。由於爐缸爐襯侵蝕嚴重,因此公司2008年對熔融氣化爐進行大修。該COREX-C2000設備第一代壽命為9~10年。
COREX-C3000
2007年11月,世界第一套COREX-C3000在寶鋼羅涇投產。COREX-C3000的設計充分吸取了C1000和C2000的經驗,克服了其不足,在爐體、耐材、冷卻系統以及布料裝置等方面做了大量改進,設計年產能達到了150萬t。
寶鋼COREX-C3000的預還原豎爐(總高29m、還原段12m、內徑8m)下部水平沿圓周方向布置了8台螺旋排料機,連續地在熱狀態下向熔融氣化爐供料。熔融氣化爐(高33m、爐缸內徑9m)設28個氧氣風口,氧氣風口由風口小套、風口大套及氧槍組成。在半焦固定床上方的拱頂空間設有6個氧氣燒嘴,以改善和調整熔融氣化爐拱頂的熱狀態。
寶鋼的COREX-C3000
與COREX-C2000相比,
寶鋼COREX-C3000在熔融氣化爐、還原豎爐、爐體冷卻系統、布料系統以及耐材系統等方面進行了相應改進。
(1)熔融氣化爐
將爐腹角加大到22°,以避免冷卻壁燒蝕;風口以上採用2段銅冷卻壁,增大半焦炭床的體積;增加出鐵口的長度和死鐵層的深度,以減輕鐵水對爐缸的沖刷侵蝕;風口以上的半焦床高度由7m增加到10m。
(2)還原豎爐
加大了爐身角,以利於爐料的順行;增大了煤氣圍管的直徑及圍管以下部分的高度;提高豎爐下部的壓差,防止或減少氣化爐煤氣通過海綿鐵下料管直接竄入還原豎爐,導致局部爐料溫度過高,產生粘結。
(3)爐體冷卻系統
增加了冷卻壁段數,由9段增加到10段;風口以上爐腹採用2段銅冷卻壁,以改善爐體的冷卻效果。
寶鋼COREX-C3000設計一代壽命為10-15年。
2008年4月,寶鋼試製成功了COREX-C3000噴煤技術,並計畫於年底投入工業套用。項目實施後,將逐步利用塊煤篩下粉煤和除塵煤粉,使COREX-C3000爐直接利用
粉煤,對降低
煉鐵成本、改善
經濟技術指標、提高工藝競爭力具有重要意義。
COREX質能特點
能量消耗
Corex工藝重要特點是如何有效利用過程產生的
煤氣。根據Corex的實際生產過程統計, 總能量消耗大約在20.9GJ/t(比目前高爐水平15GJ/t高30%左右), 通過氣體回收, 可以回收大約60%的熱量, 即淨能量消耗為8.36GJ/t。總能耗包括燃料消耗、制氧動力消耗等。表1是南非Saldanha、印度JVSL和寶鋼高爐實際生產的燃料消耗。儘管Corex的能耗水平進一步得到改善, 但2003年9月其實際消耗的燃料比寶鋼高爐水平要多近一倍。在Corex開爐初期, 焦炭比例達到20 %~30 %才能保證足夠的生產率, 即使在穩定生產階段, 10%~15%的焦炭比例是不可少的。而為什麼需要一定的焦炭比例, 除了保證爐缸氣流分布以外, 還沒有其它更好的解釋, 即相當於在Corex爐缸記憶體在和高爐一樣的焦炭死料區, 焦炭同樣起到料柱骨架作用。 Corex工藝能耗高的原因是從爐內排出的
廢氣溫度較高, 南非Saldanha生產班報數據表明在1070~1091℃; 同時排出煤氣熱值高, 表2是氣體成分表。和
高爐煤氣熱值3200kJ/m3相比, Corex 產生煤氣熱值高2.5倍。這是Corex工藝必須配套預還原或發電以回收煤氣潛熱和化學熱的原因。而對於預還原過程, 由於氣體中CO2含量比較高, 因此, 對預還原氣體進行處理脫除部分CO2是必須的。Corex煤氣熱值高, 主要是H2和CO含量高, 與使用的燃料主要以煤粉為主, 揮發分在25%~30%有關。印度Corex設有兩排風口, 下風口以空氣和部分富氧鼓風為主, 上風口主要是富氧鼓風, 噴吹部分回收粉塵, 並燃燒部分H2和CO, 以保證足夠的熱量。但Corex爐內的熱交換和高爐是不一樣的, 高爐的逆流傳輸過程時間相對較長, 所以熱量利用比較充分。
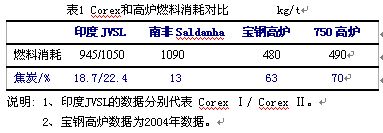

原燃料條件
Corex使用的原料品位達到65%以上, 而高爐原料在60%以下, 所以原料中脈石含量有很大差別。另外, Corex使用的原料中S相對較低。Corex使用的燃料包括煤和10%~20%焦炭, 表4是Corex使用煤的物理化學成分要求。而實際情況下各廠略有差別, 表5是南非和印度使用的實際煤種。Corex工藝對煤的特殊要求不僅表現在化學成分和物理性能上, 對煤的塊度有嚴格要求。因此, 煤種的選擇和合理利用是該工藝的重要技術和限制因素。

同時, Corex為了形成合適的爐渣成分, 保證冶煉的正常進行和鐵水質量, 必須加
石灰石或
白雲石等熔劑。原燃料中的S主要以FeS和FeS2形式存在, 和CaO、MgO在碳作用下形成CaS、MgS。還原氣中S以H2S和COS形式存在, 當含量超過0.087%時,將和Fe反應生成FeS。 如果噴吹煤粉或礦粉,在氧存在的條件下,FeS 和FeS2將和氧反應生成煤氣中的SO2, 熔劑分解後的產物對其有脫除作用。因此, Corex過程產生的廢氣中SO2含量並不高。但為了滿足鐵水對
硫的要求,以及克服H2S和COS對生產過程和設備的影響,必須嚴格控制原燃料的硫含量。
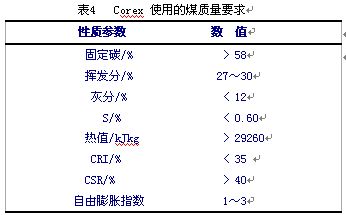
鐵水質量
Corex工藝生產的鐵水
矽含量較高, 而鐵水矽含量影響
煉鋼工序降矽的時間, 影響鐵水或鋼水脫
磷, 不利於工藝過程的整體最佳化, 不利於生產高質量的鋼水。從高爐冶煉矽還原機理的研究可知, 高爐內矽的還原主要是焦炭中的SiO2與碳接觸生成SiO氣體, 再還原生成[ Si ]。由於Corex工藝的反應溫度高於高爐過程, 在氣化爐記憶體在比高爐大得多的大於1400℃的高溫區, 有利於矽的還原。尤其是有利於渣中SiO2的還原。另外, 燃料比高, 而且都是從還原區加入的, 焦炭床存在良好的矽還原條件。所以, Corex 對低矽冶煉是不利的, 解決的辦法包括: 提高焦炭質量, 提高噴吹煤比水平, 提高礦石品位, 降低
脈石含量等。另外, Corex工藝生產的鐵水S、P含量也比高爐高。P主要是由原燃料帶入的, Corex和高爐一樣不具備
脫磷條件。而對於S含量, 原燃料帶入的硫大部分進入熔煉爐(高爐原料中硫大部分在燒結或焦化過程去除), 在熔煉爐內, FeS和CaO、MgO及C反應被去除, 因此和高爐一樣受渣鐵與碳接觸時間、爐渣鹼度、反應溫度和渣中FeO含量等影響。Corex工藝的焦炭床對脫硫有至關重要的影響, 其產品質量受爐渣成分的限制。
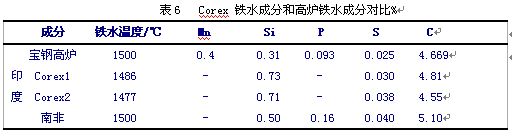