高爐供料系統的特點是運輸數量大、工作節律性強。它的任務是將經過預處理的鐵礦石、焦炭和輔助原料分別從原料場、燒結廠、煉焦廠用火車或皮帶運輸機送到高爐貯焦槽和貯礦槽。
基本介紹
- 中文名:高爐供料系統
- 特點:運輸數量大
- 皮頻寬:1.6~2.5米
- 斜傾角:12~13左右
系統發展,無鐘爐頂,安全技術措施,
系統發展
貯焦槽容積約為高爐容積的 0.7倍,貯焦6~8小時;貯礦槽容積約為高爐容積的1.6倍,貯礦9~14小時;輔助原料貯存20小時左右。原料、燃料由篩分器篩分後,經稱量車卸入料罐或料車;20世紀上半葉大多使用斜橋供料;70年代大型高爐使用帶式輸送機上料,皮頻寬1.6~2.5米,斜傾角12~13左右,速度2米/秒左右。
爐頂裝料設備
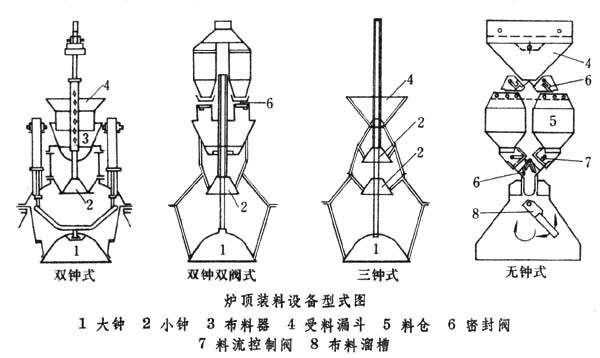
早期小高爐爐頂為敞口式,由人工裝料。後來發展為封閉式。1850年出現單鐘爐頂;1907年出現雙鐘爐頂;60年代以後出現三鐘爐頂、帶封閉閥的雙鐘爐頂和最新的無鐘爐頂。爐頂大鐘的斜度50~60,一般53,採用二段斜傾角,外加護板,一般壽命約為5~7年。高爐大型化以後,大鐘太大,運輸不便,而且造成爐頂的布料徑向不勻。60年代聯邦德國設定可調爐喉導料板,改進布料,煤氣利用率增高,焦比降低約30公斤/噸生鐵,並能保護爐身磚襯。日本有帶導料板和密封閥雙鐘爐頂的高爐。
無鐘爐頂
這種爐頂是1970年由盧森堡保羅‧伍爾斯公司(s.a.paul wurth co.簡稱p.w.)發展的,1972年在聯邦德國試驗成功。中國首鋼1979年在2號高爐,1982年在4號高爐採用這種爐頂,取得很好效果。無鐘爐頂有帶密封閥的爐頂料倉和旋轉溜槽。它有以下優點:可選擇多種布料方式,如圓環布料、扇形布料、螺旋布料、定點布料等,實現最佳布料,充分利用煤氣能量,並能防止爐內布料偏斜現象和堵塞局部氣流通道。原料、燃料混層較少,對高爐使用球團和型焦有利。設備重量較一般爐頂約減輕一半,爐頂吊車可由 120噸改為30噸,爐頂框架可降低,節省投資。維修方便,更換溜槽時間僅為4~8小時(各式有鐘爐頂換大鐘需2~7日),提高高爐作業率,延長高爐壽命。無鐘爐頂用的爐料必須粒度整齊,否則粒度偏析大。
安全技術措施
(1)運人、儲存與放料系統。大中型高爐的原料和燃料大多數採用膠帶機運輸,比火車運輸易於自動化和治理粉塵。儲礦槽未鋪設隔柵或隔柵不全,周圍沒有欄桿,人行走時有掉入槽的危險;料槽形狀不當,存有死角,需要人工清理;內襯磨損,進行維修時的勞動條件差;料閘門失靈常用人工捅料,如料突然崩落往往造成傷害。放料時的粉塵濃度很大,尤其是採用膠帶機加振動篩篩分料時,作業環境更差。因此,儲礦槽的結構應是永久性的、十分堅固的。各個槽的形狀應該做到自動順利下料,槽的傾角不應該小於50°,以消除人工捅料的現象。金屬礦槽應安裝振動器。鋼筋混凝土結構,內壁應鋪設耐磨襯板;存放熱燒結礦的內襯板應是耐熱的。礦槽上必須設定隔柵,周圍設欄桿,並保持完好。料槽應設料位指示器,卸料口應選用開關靈活的閥門,最好採用液壓閘門。對於放料系統應採用完全封閉的除塵設施。
(2)原料輸送系統。大多數高爐採用料車斜橋上料法,料車必須設有兩個相對方向的出入口,並設有防水防塵措施。一側應設有符合要求的通往爐頂的人行梯。卸料口卸料方向必須與膠帶機的運轉方向一致,機上應設有防跑偏、打滑裝置。膠帶機在運轉時容易傷人,所以必須在停機後,方可進行檢修、加油和清掃工作。
(3)頂爐裝料系統。通常採用鐘式向高爐裝料。鐘式裝料以大鐘為中心,有大鐘、料斗、大小鐘開閉驅動設備、探尺、旋轉布料等裝置組成。採用高壓操作必須設定均壓排壓裝置。做好各裝置之間的密封,特別是高壓操作時,密封不良不僅使裝置的部件受到煤氣沖刷,縮短使用壽命,甚至會出現大鐘掉到爐內的事故。料鐘的開閉必須遵守安全程式。為此,有關設備之間必須連鎖,以防止人為的失誤。