形成原因
截至2005年來,隨著經濟的發展、產鋼量的提高,
鋼結構工程由於其優越的力學和環保節能等性能得到了迅速的發展。2010年世博會、亞運會在中國舉行,大型體育場館、公共建築、構築物以及大跨徑的廠房及市政共用工程等建設,給中國的鋼結構設計施工帶來了挑戰。隨著各類特大型複雜鋼結構工程的湧現,高強超厚板(如60~100毫米厚的Q390D、Q420D、Q460E等材質鋼板)的現場
焊接就越來越多,焊接難度也越來越大,特別是多桿件匯交形成的複雜節點。為滿足節點構造要求和現場吊裝要求,一些超長、超厚
焊縫在施工現場進行焊接也就在所難免,而高強鋼材的可焊性程度、
焊接參數、焊接應力和變形控制等受現場條件、焊接位置及環境的影響,存在較多的不確定性因素,尚無成熟的規範及焊接工藝參數作參照。研究、探索高強超厚板現場焊接工藝具有重要的理論意義和實際意義,也是需要解決的問題;同時對施工單位也提出很高的要求,需要根據工程本身特點與實際工況,進行施工工藝革新。
中建三局股份鋼結構公司在鋼結構厚板焊接方面不斷總結經驗。通過在中央電視台新台址工程CCTV主樓鋼結構安裝中,以10根超大型複雜蝶形節點的多箱型分體鋼柱為代表的超長、超厚焊縫的成功焊接,總結了一整套關於高強鋼超長、超厚板的現場焊接思路和方法,形成《高強異型節點厚鋼板現場超長斜立焊施工工法》。
工法特點
《高強異型節點厚鋼板現場超長斜立焊施工工法》的工法特點是:
一、使用半自動實芯焊絲CO2氣體保護焊(FCAW-G)和半自動藥芯焊絲CO2氣體保護焊(GMAW)相結合的焊接方法,模擬工況進行焊接工藝試驗,獲取焊接參數。
二、用電腦控制的電加熱設備進行焊前預熱、焊中層間溫度控制以及焊後熱消氫處理,確保母材受熱均勻,有效控制了冷裂紋的產生,提高了焊接工效、保障了連續施焊,避免了火焰烘烤工的集中作業,節約了焊接時間和焊接成本。
三、採取分段退焊順序,並在焊前、焊中與焊後用全站儀進行實時監測,及時調整加熱能量,減少焊接變形。
四、焊後48小時焊接探傷和15天后延遲裂紋探傷檢驗,進一步保障了焊接質量。
操作原理
適用範圍
《高強異型節點厚鋼板現場超長斜立焊施工工法》適用於
厚板、長焊縫的焊接,最適用於鋼結構安裝工程中高強材質Q390D、Q420D、Q460E的長焊縫的二氧化碳氣體半自動保護焊、立焊位置的焊接;對於其他板厚在100毫米以上的現場焊縫焊接同樣具有很大的參考價值。
工藝原理
《高強異型節點厚鋼板現場超長斜立焊施工工法》的工藝原理是:
一、施工前,根據焊接形式有針對性地進行焊接工藝評定。
二、鋼分體安裝,先安裝本體鋼柱、並部分焊接,然後安裝分離下來的一部分鋼柱。
三、焊接前先對焊接坡口兩側的母材進行超音波無損探傷檢測,檢查母材內部有無缺陷,同時用焊縫量規對焊縫坡口大小、角度以及安裝組對情況進行仔細的檢查。
四、使用電加熱技術進行焊接預熱、後熱加熱保溫,保證鋼柱整體溫度同步均勻加熱和降溫。
五、焊接過程中採用分層、分道、對稱、同速分段退焊的方法進行施焊。
六、在整個焊接過程中,採用高精度全站儀對鋼柱的關鍵部位進行跟蹤測量,如鋼柱的軸線有偏移,則及時通過調整焊接順序和電加熱的熱輸入量技術對鋼柱進行校正。
七、焊接完成48小時後採用超音波無損探傷和磁粉探傷檢測焊縫的焊接質量,15天后對焊縫再次進行檢查,防止延遲裂紋的產生。
施工工藝
《高強異型節點厚鋼板現場超長斜立焊施工工法》施工工藝流程見圖1。

圖1 施工工藝流程圖
《高強異型節點厚鋼板現場超長斜立焊施工工法》的操作要點如下:
一、焊接材料選擇
根據鋼結構母材和焊接方法,選用匹配的焊接材料,見表1。
二、焊接工藝參數見表2、表3。
材料 | 預熱溫度(°C) | 層間溫度(°C) | 後熱溫度(°C) | 恆溫時間(小時) | 保溫時間(小時) |
---|
| | | | | |
| | | | | |
三、焊接工藝評定
制定焊接工藝評定指導書,嚴格模擬實際工況,按照預定工藝參數進行焊接試件的製作,冷至常溫48小時後,進行UT探傷、力學性能試驗檢測,確定最佳的焊接工藝參數和焊接方法。
四、焊接接頭的準備
焊接前應認真檢查母材坡口的間隙是否超標,如有超標應在坡口表面用小熱輸入、多層、多道堆焊方法減小間隙,使坡口角度和間隙達到標準後方可正常施焊。
檢查邊緣是否光滑,確保無影響焊接的割痕缺口,質量應符合GB50205-2001規範規定的要求,若發現問題套用磨光機認真打磨處理,全格後方可進行焊接。
五、焊接順序和焊接方法
分體鋼柱的立向焊縫縱向通長分布在鋼柱內箱體一側,焊接熔敷金屬量大,由於焊接收縮變形產生的焊接應力對結構質量將造成不利因素,而且母體橫截面大剛性大對子體形成很大約束,因此控制焊接應力、防止厚板在焊接時的冷裂紋及層狀撕裂,將是主要的技術重點,在焊接施工前必須制定出合理的焊接順序及方法,並嚴格按照制定的焊接順序和方法進行焊接作業。
(一)安裝及焊接順序
⒈整體順序
母體(本體)與下節柱焊接-母體與子體立焊縫的焊接-子體和母體部分與下節柱焊接。
⒉母體與子體的焊接順序及方法
①母體與子體的焊接方法為分層退焊,其焊接順序總體為:多人同時、分段、對稱焊接。
②每名操作焊工在焊接所在分段時,應再將所在分段分為兩段或三段,以三段為例焊接順序為:
先從上面的1/3處向上面焊接;焊完一層後再從中間的1/3處由下向上焊接中間的1/3段的第一層;然後再從此分段的底部向上焊接下面1/3段的第一層,這樣完成第一層的焊接;接著再由下向上焊接上面1/3段的第二層,依次類推直到焊接完所在分段部位的全部焊接。母體與子體焊接順序示意圖見圖2、圖3。

圖2 分體鋼柱立焊縫焊接分段示意圖

圖3 分體鋼柱立焊縫焊接分段示意圖
(二)焊接方法
採用薄層多道窄擺幅和分段退焊的焊接方法進行施焊,嚴格控制單道焊縫的厚度和寬度,減少焊接熱輸入,以減小降低焊縫的機械性能因素,單道焊縫厚度應不大於5毫米、擺動寬度不大於20毫米。分段退焊焊接接頭的處理見圖4。

圖4 分體鋼柱立焊縫焊接分段示意圖
在分段退焊上段焊縫時,每一層焊接至上一區域分段處止焊;再退至下段與下一區域分段處起焊,焊接至上一段起焊處止。在某一段焊接前,需將上段焊縫起焊處和下區域止焊處的焊接缺陷需用碳弧氣刨和砂論清除乾淨,並將接頭處處理成緩坡形狀,達到焊接要求,每一層的焊縫接頭必須錯開不小於50毫米,以避免焊接缺陷的集中。
六、焊接工藝要求
(一)預熱
由於超長焊縫需要安排大量的焊工分段同時連續施焊,為保證焊接的質量,減小焊接應力,焊前預熱非常重要。為達到所需要的溫度,焊前預熱的預熱方式主要以電加熱為主,對局部電加熱無法加熱到的地方採用火焰加熱的方式進行,預熱溫度為:不低於120℃。測溫點位於焊縫兩側並離焊縫中心75毫米處,預熱時間4~5小時。加熱範圍見圖5所示。
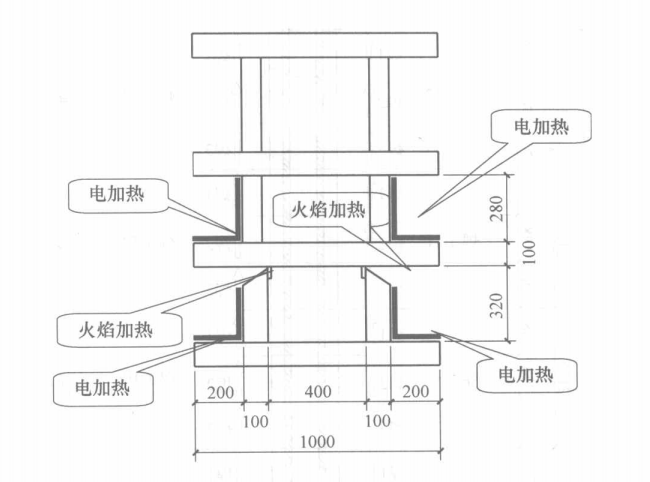
圖5 加熱範圍示意圖
(二)層溫控制
與預熱一樣,超長焊縫層溫控制十分困難,焊接時焊縫分段焊接的長度,應控制在一定長度1米左右,需隨時對焊接焊縫進行測溫監控,層間溫度應控制在不低於預熱時的溫度(即層間溫度應不低於120℃),發現層溫過低時,必須立即進行加熱補償,待達到要求後再進行焊接。
(三)後熱及保溫
分體鋼柱與主體的斜立向焊縫,由於是分段焊接完成,先焊接完成段的焊縫溫度需保持在接近後一段焊接部位焊縫的溫度。因此應及時放置電加熱器進行後熱處理。在放置電加熱設備的過程中,為了防止焊縫溫度降低應先用火焰對焊縫進行補償加熱,保證整個焊縫的溫度不低於焊接過程中的最高層間溫度(即150℃)。當電加熱器的溫度升高到150℃時,停止火焰加熱,從而保證焊縫的均勻收縮,減少焊縫分段焊接的收縮產生的應力。後熱溫度應控制在不低於250℃,加熱到所需溫度後恆溫2小時再進行保溫覆蓋緩冷至常溫。
(四)若遇氣候條件惡劣,不能連續施焊時,應立即採取上述後熱措施,再次開始焊接前應按上述規定重新預熱。
七、焊接時的其他注意事項
(一)在開始施焊前,應對參焊人員進行詳細的交底,並對焊接人員明確其所在的焊接部位;
(二)在焊接過程中,應準備至少兩台備用焊機,以防止某台焊機出現故障後立即有焊機投入使用而不至於某一焊接部位停焊;
(三)在焊接過程中,每一個班組應準備至少一名焊工,以防止某焊工發生不可預見的緊急情況後,立即有人投入焊接而不至於某一焊接部位停焊;
(四)在整個焊接過程中,安排專人全程進行監護,一來對焊接質量進行監督,二來對焊接工人進行防護,以免發生意外。同時,監護人員還要認真、詳細地做好焊接過程中各項參數的記錄。
(五)若在夏季焊接,由於天氣炎熱,焊接時焊工都在封閉的環境中施焊,在焊接過程中應對焊接工人做好防暑降溫的後勤保障。
《高強異型節點厚鋼板現場超長斜立焊施工工法》的勞動力配備如下:
勞動力需要根據所焊接焊縫的用長度、板厚、所需焊接時和允許展開的作業面確定,以焊縫長度為14毫米、板厚為100毫米、兩條焊縫同時對稱焊接時的勞動力需求建議見表4。
說明:以上人員需求是單根鋼柱焊接時的人員安排統計所得,此柱焊接時3班24小時連續作業,每班15人(其中1人為後備補充人員,以防正常施焊的焊工因勞累過度而發生意外),共連續焊接72小時。
材料設備
《高強異型節點厚鋼板現場超長斜立焊施工工法》所需材料設備如下:
CPXS-500型二氧化碳半自動氣體保護焊焊機:16台;XF200型空氣壓縮機:4台;TH-10型碳弧氣刨:10把;氣割設備:10套;超音波探傷儀:1套;焊縫量規:2把;電子測溫儀:16把;DWK-360kW電腦溫控儀:1台;陶瓷磁鐵式電加熱器:若干。
質量控制
《高強異型節點厚鋼板現場超長斜立焊施工工法》的質量控制要求如下:
一、防止焊接變形及應力的措施
(一)分層、分道退焊的方法進行施焊。
(二)分區域多機對稱焊接。在焊接過程中首先選用技能優秀的焊工,在對稱位置的兩名焊工,應儘量保持同時、同速施焊,並選擇相同的焊接電流參數及每層的焊接厚度,保證相同的焊接熱輸入,使收縮趨於同步。
(三)使用電加熱設備進行焊接預熱、後熱處理,保證鋼柱整體溫度同步均勻加熱和降溫。
(四)在焊接過程中應嚴格控制層間溫度,同一區域在焊接過程中,焊接操作人員及監護人員應隨時對施焊區域的溫度進行檢測,當層間溫度低於120℃時,應及時用火焰加熱法(使用大號烤槍)進行補熱,當層間溫度高於200℃時,應立即停焊,待溫度自然降至規定層間溫度時,再進行焊接。
二、防止冷裂紋及層狀撕裂措施
(一)針對長焊縫特點採取多人分段分層退焊焊接,即由多名焊接技工,同熱輸入量、勻速焊接,並保持連續施焊,使焊接應力分散,有效地減小峰值應力,減少焊接冷裂紋及層狀撕裂的產生傾向。並且兩條長焊縫採取完全對稱、同時焊接措施。
(二)使用優秀焊工,減少焊縫缺陷及碳弧氣刨的使用。碳弧氣刨使用後應採用角向磨光機磨去刨削部位表面附著的高碳晶粒,避免焊縫裂紋的產生。
(三)控制坡口尺寸和焊縫截面積,防止過量熔敷金屬導致收縮和應力增大。儘量控制焊縫表面的余高,並使之平緩過渡,以減少焊趾部位的應力集中。焊縫余高應控制在0.5~3毫米以內。
(四)焊前預熱和層間溫度的控制。預熱主要採用電加熱器進行加熱,加熱區域為被焊接頭中較厚板的1.5倍板厚範圍,但不得小於100毫米區域,加熱溫度應不低於120℃,由於柱截面特點而不可能在厚板的反面加熱,為了使全板厚預熱溫度達到均衡,在母體側擴大加熱一塊腹板。焊接前應認真檢測焊接區的加熱溫度,確保加熱溫度滿足要求。
(五)焊後熱處理及後熱保溫是防止層狀撕裂的關鍵所在,在焊接完畢後確認外觀檢查合格後,立即進行消氫後熱和長時間保溫處理,有效地消除焊接應力及擴散氫的及時逸出,從根本上解決由於焊接應力集中及擴散氫積累含量過高而發生層狀撕裂的難題。
(六)使用高純度的二氧化碳氣體進行焊接,其純度應保證:CO2含量299.9%,水蒸氣與乙醇總含量(V/V)不得高於0.005%,並不得檢出液態水。藥芯焊絲開盤後應連續用完避免受潮。
(七)採用50級焊絲,使焊縫與母材達到強匹配,避免超強匹配。這是防止母材產生層狀撕裂的重要措施之一。
(八)為減小長焊縫的拘束應力,該柱與下柱的焊接接頭待長焊縫完成和驗收後進行。
三、焊後質量檢測
整條焊縫焊接完畢並經後熱保溫處理、待冷卻48小時後,按設計要求對焊縫進行100%的超音波探傷和磁粉探傷檢測。為保證焊接質量、防止冷裂紋的發生,在焊接15天后對焊縫進行再次超音波探傷檢測。
安全措施
施工單位採用《高強異型節點厚鋼板現場超長斜立焊施工工法》施工時,為了強化管道預製工廠對工程施工安全的監督管理,不斷提高安全管理水平、最大限度減少或控制安全事故的發生、保障員工生命和財產安全,除應執行國家、地方的各項安全施工的規定外,尚應遵守注意下列事項:
由於焊接工作量巨大、焊接時間長,且上下十多名焊工同時進行焊接,所以焊接前需搭設安全、穩固、封閉的安全操作平台,以保證焊接過程中所有焊工能夠安全地操作。
焊接安全操作平台使用腳手管搭設,當焊縫過長時,必須搭設多層隔斷封閉式平台,由下到上分成多個區段同時進行焊接,在焊接的過程中,上部區域的焊接作業不得影響下部區域的焊接操作,達到安全穩固的要求。
由於分體連線焊縫超長均需分層分段焊退焊完成、還需由下到上分成多個焊接區域,並在各區域增加相應高度的活動操作平台,可供焊接人員隨時上、下移動位置,按規定的焊接方法和順序進行施焊。焊接安全操作平台的搭設見圖6。

圖6 焊接防護棚搭設示意圖
工程實例
《高強異型節點厚鋼板現場超長斜立焊施工工法》的工程實例如下:
中央電視台新台址工程A標段主塔樓外框鋼柱截面大,鋼板厚(最大板厚達100毫米),由於結構受力要求,部分外框鋼柱分節後的單節重量達120噸,超出現場吊裝設備(最大吊裝設備為M1280D塔吊,最大起重能力為80噸)的起重能力,根據設計要求鋼柱無法減小分節,為減少單節鋼柱重量,滿足吊裝,需要將鋼柱部分箱體或牛腿與主體分離後進行安裝(見圖7所示)。安裝時先將主箱體吊裝、測校、部分焊接,然後再進行分體部分的拼裝,校正後進行焊接。
主樓鋼結構安裝中焊接難度最大的10根外框超重鋼柱,採用了分體安裝、現場半自動實芯+藥芯焊絲CO2氣體保護焊接的工藝。單條焊縫最大長度為14880毫米,鋼板厚度為100毫米,填充金屬量約0.55噸,焊接位置全部為斜立向位置、超長焊縫和超厚板的焊接。施工時用14名焊工同時焊接,52名焊工參與,連續3晝夜,焊接完成一組超長超厚立焊縫。所有焊縫自檢、第三方探傷檢測,全部一次性100%合格,且通過了業主和北京市質量監督檢查站的復檢。

圖7 焊縫示意圖
效益分析
《高強異型節點厚鋼板現場超長斜立焊施工工法》的效益分析如下:
中央電視台新台址工程CCTV由於10根超重分體鋼柱的超長、超厚焊縫現場焊接的成功,使該工程在經濟效益和社會效益都取得了成效,同時也提高了複雜鋼結構施工的技術水平,而且為後期懸臂鋼結構部分的深化設計及安裝方面解決吊裝受限方面提供了可借鑑的方法。
一、設備、措施投入方面:通過將超過原有塔吊起重量的鋼柱分體後安裝、現場焊接的方案,減小了大型吊裝機械的投入及安裝措施的增加,節約了施工投入資金至少100萬元,取得了經濟效益。
二、工期方面:革新傳統焊接工藝,加快了焊接時間,為下部結構的儘快安裝創造了條件。
三、質量方面:通過電腦控制電加熱、實時監控、焊後反覆探傷檢測等多種手段,保障了焊接質量,控制了焊接變形,確保了結構位形滿足設計要求。
四、根據查新資料表明,高強鋼超長、超厚板立焊縫現場焊接的工藝在中國房建領域屬首次套用,施工中無類似的工程可以借鑑。該工程中10根超重鋼柱超長焊縫的順利完成,將填補中國此項焊接施工工藝的空白,為之後類似工程的施工提供理論依據和實際操作方法。
註:施工費用以2005-2006年施工材料價格計算
榮譽表彰
2008年1月31日,中華人民共和國住房和城鄉建設部以“建質[2008]22號”檔案發布《關於公布2005-2006年度國家級工法的通知》,《高強異型節點厚鋼板現場超長斜立焊施工工法》被評定為2005-2006年度國家一級工法。