鋅酸鹽鍍鋅就是用ZnO、NaOH配置溶液,加入適當的鍍鋅添加劑,在通電狀態下,在金屬或其他材料表面鍍一層金屬鋅,來增加材料耐蝕性和裝飾性。
基本介紹
- 中文名:鋅酸鹽鍍鋅
- 外文名:Zincate zinc plating
- 主要材料:ZnO、NaOH等
- 優點:鍍液成分簡單、穩定,使用範圍廣
- 工藝:DE與DPE型
- 學科:冶金工程
鋅酸鹽鍍鋅特點,鋅酸鹽鍍鋅工藝規範,鍍液中各種成分的作用,鍍液配製,工藝條件及鍍液維護,鋅酸鹽鍍鋅的研究和添加劑的開發與套用,
鋅酸鹽鍍鋅特點
鹼性鋅酸鹽鍍鋅是以氧化鋅為主鹽,以氫氧化鈉(燒鹼)為絡合劑,它的特點是對電鍍設備沒有腐蝕性,鍍層結晶細緻光亮,成本較低,原材料來源廣,槽液穩定,容易掌握。但必須加適量的添加劑,才能使鍍層達到結晶細緻、光亮的效果。
近年來,鋅酸鹽鍍鋅在國內套用廣泛,主要是這一工藝具有許多優點,如鍍液成分簡單、穩定,使用工藝範圍比較寬,分散能力和覆蓋能力較好,鍍層結晶細緻,只要選擇添加劑適當,就能達到較高光亮鍍層,且容易鈍化處理,操作方便,維護簡單,污染小,無劇毒氰化物。鍍後污水處理方便,有利於環境保護,適用於機械化、自動化生產,如鋼管等幾何形狀複雜的大小五金件鍍鋅實效顯著。
鋅酸鹽鍍鋅工藝規範
國內近年來鹼性鋅酸鹽鍍鋅添加劑品種繁多,但工藝配方實質都大同小異。現將國內套用較廣的DE與DPE型兩種鋅酸鹽鍍鋅的主要配方及工藝條件列於表1。
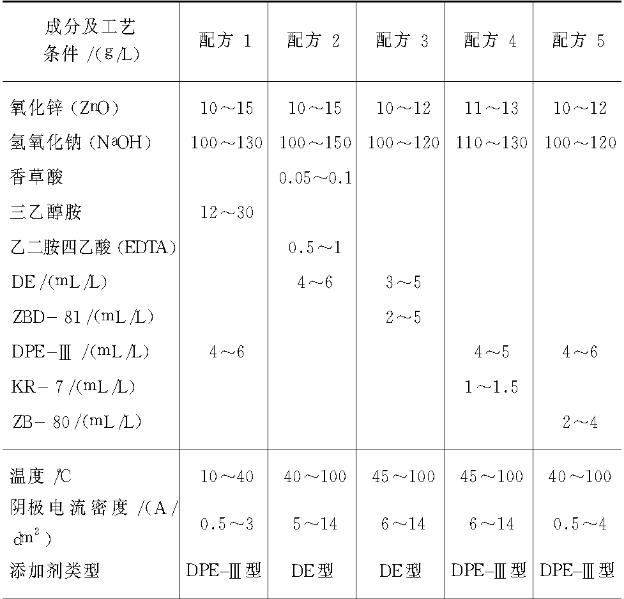
鍍液中各種成分的作用
1. 氧化鋅
鋅的含量對鍍液性能與鍍層質量具有重要的作用。鋅含量若偏高,電流效率雖得到提高,但分散能力和深鍍能力相應降低,複雜件尖棱部位鍍層會粗糙而出現陰陽面;含量偏低,陰極極化增加,分散能力好,但沉積速度慢,通常吊鍍含量為10~12g/L,滾鍍含量為8~10g/L。
2. 氫氧化鈉
主要作用是與鋅離子絡合成穩定的鋅酸鹽,並能使陽極正常溶解而起絡合與導電作用。但一般含量不可太高,太高會使鍍層粗糙,呈青灰色斑跡,鈍化膜不亮;也不可偏低,偏低會使鋅陽極易鈍化。含有適當過量的氫氧化鈉以穩定鍍液是必要條件。在生產中定期分析鋅和氫氧化鈉的含量,並使氫氧化鈉和鋅保持一定的比例。一般掛鍍應控制氫氧化鈉∶鋅(質量比)=10∶1;滾鍍控制氫氧化鈉∶鋅(質量比)=12∶1。
3. 添加劑
過去老工藝採用三乙醇胺(又稱為三羥乙基胺,用TEA表示)作為輔助絡合劑,六次甲基四胺(又叫H促進劑)與三乙醇胺作用相似,可改善鍍液分散能力,提高鍍層光澤,促使結晶細緻;三乙醇胺是非導體的黏稠液體,會增加鍍液電阻,降低沉積速度,含量過低鍍層光亮層變差。光亮劑有甘油、明膠、茴香醛等。甘油在鹼性鍍鋅中與膠體配合,對提高光亮度有一定作用,但與DE、 DPE等相比,這些國內採用過的添加劑在套用中有一定差距。甘油等目前極少使用。
鍍液配製
(1) 先加入水至1/4槽,然後將計算好的NaOH倒入,使其完全溶解。
(2) 將計算量ZnO用少量水調成糊狀,在不斷攪拌下逐漸加入NaOH溶液中,直至完全溶解,稀釋至總體積的80%左右,加入三乙醇胺或EDTA(配方1、2)。
(3) 加入鋅粉1~2g/L,充分攪拌,靜置、過濾。
(4) 短時間電解處理後,加入計算量添加劑,加水至規定容積,略加攪拌即可試驗。
工藝條件及鍍液維護
本鍍液穩定,平時只需補加適量添加劑,注意每次少加、勤加;定期取樣液化驗及時補加調整,使Zn∶NaOH在1∶12之間。注意調整陽極使可溶性陽極(Zn極)與不溶性陽極面積比為1∶3,陰極與陽極面積比在1∶(1.5~2)之間。陽極與陰極的相對位置及電極的排布關係到鍍層均勻性。極距不可太近,否則凸處易燃燒,凹處發暗,增大陰陽間距離有利於鍍層均勻,鍍複雜件保持在200~250mm,槽兩端留出100~150mm空位,陽極總長要比掛具短100~150mm。
注意控制槽液與電流密度的相互關係。鋅酸鹽鍍鋅有較寬的工作溫度範圍,一般在10~45℃之間,均可獲得合格的鍍層,隨著溫度升高,陰極電流效率增加,套用的電流密度範圍上移,沉積速度增加,生產效率提高。但電解液分解能力下降,鋅陽極自溶解速度加快,槽液便不穩定,故不可在過高的溫度下工作。由此可見,控制溫度比較重要,使溫度控制在工藝範圍之內。鋅酸鹽鍍鋅具有較寬的電流密度範圍,一般在1~5A/dm2之間,當其成分與溫度一定時,宜保持較高的電流密度。它能在一定程度,改善電解液的分散能力,提高陰極極化,有利於得到優良鍍層,但電流密度過高,鍍層結晶粗、無光澤,甚至邊緣出現燒焦。
溫度與電流密度相互關係密切,如溫度低時,電解液的導電性便差,添加劑的吸附強,脫附困難,此時切莫使用高電流,否則便會使邊棱部位燒焦,添加劑夾雜,鍍層脆性大會鼓泡。溫度高時,添加劑吸附弱,極化因而下降,這時須用較高電流密度來提高陰極極化,細化結晶,可防止陰陽面。因此,應根據溫度來選擇適當電流密度。
鋅酸鹽鍍鋅液中雜質有銅時,會使鍍層粗糙無光,用小電流電解或用鋅粉(0.5~1g/L)攪拌靜置、過濾處理。鉛使鍍層發黑不亮,可加入0.1~0.2g/L硫化鈉使之生成硫化鉛沉澱處理,特別是陽極不純(鉛>15mg/L,銅>20mg/L,鐵>50mg/L),均可產生上述烏暗發黑、條紋等毛病,因此,除上述加硫化鈉等化學法外,近年國內多採用CK-778作雜質淨化處理,加0.5~1g/L左右,攪拌30min,停10~20min再攪拌30min,不斷撈去液面髒物,停8h過濾即可淨化。正常生產中不宜多採用低電流電解法處理,主要是日常維護好,注意化工材料及陽極質量,要用鋅板不可將鋅錠作陽極,鋅錠需澆鑄成鋅板,以防止產生雜質。
鋅酸鹽鍍鋅的研究和添加劑的開發與套用
在電鍍工業中鍍鋅占產量的60%,在機電行業中鍍鋅占70%左右,從鍍鋅中淘汰劇毒氰化物,是實現無氰鍍的關鍵。近年來,無氰鍍鋅已用於生產,其中一度銨鹽鍍鋅套用最廣泛,但由於銨鹽鍍鋅電解液對設備和廠房產生嚴重腐蝕,不便於實現自動化生產,工藝控制不好時,鈍化膜在貯存、運輸和使用中嚴重變色,降低了產品的外觀質量,上述缺點仍待進一步克服。因此,近年來許多單位在研究無氰鹼性鍍鋅,其中部分用於生產實際的鹼性三乙醇胺鍍鋅,由於三乙醇胺對鋅絡合能力差,鍍液分散能力不好,生產效率低,還不能滿足生產需要,因此又在鹼性鋅酸鹽鍍鋅的研究方面取得新的進展。
研究無氰鹼性鋅酸鹽鍍鋅的目的,自然最初是希望既可逐步從工藝上入手,又有較高的生產效益,但是道路是艱難的,如用氧化鋅和氫氧化鈉組成的鋅酸鹽溶液,只能鍍出海綿狀的沉積物,因此必須研究某種具有氰化物優良特性的添加劑,以改善電解液的電化學特性,至今尚在努力。
鋅酸鹽鍍鋅添加劑品種有以下幾種可供選擇:
國內無氰電鍍以鋅酸鹽鍍鋅發展得比較快,占無氰鍍鋅中的主要部分,其中關鍵組分添加劑主要有DPE和DE系列。
DPE是套用最廣的品種,與傳統的氰化鍍鋅工藝相比,是較理想的代替氰化鍍鋅的有機添加劑。採用DPE工藝的溶液穩定性好,維護簡單,操作方便,目前生產的品種有DPE-Ⅰ和DPE-Ⅱ(DPE-Ⅱ用得很少)。
DPE-Ⅰ是由二甲氨基丙胺與環氧丙烷縮合而成的水溶性聚合物,適用於15~20μm的鍍層;DPE-Ⅲ是二甲氨基丙胺、乙二胺與環氧丙烷縮合的水溶性聚合物,適用於20~25μm的鍍層。兩者均為實際無毒級。
DE鋅酸鹽鍍鋅添加劑在國內套用比較廣泛。它是由二甲胺和環氧氯丙烷縮合而成的水溶性聚合物,其工藝指標也接近於氰化鍍鋅。
在現場生產中,掌握添加劑的用量和特性至關重要。由於目前尚無有效的分析手段檢查槽液中的實際添加劑含量,合理掌握用量便很重要,少了、多了都不行。添加劑的過多夾雜,易引起鍍層的脆性等故障。添加劑顧名思義也只能添添加加,為此,一般即使是正常情況下,也應該勤加少加。對於以DPE為添加劑的鋅酸鹽鍍鋅工藝,通常可用簡單的赫爾槽試驗來加以判斷,當添加劑過多時,表現出來的是試片低電流密度區不亮,反之,低電流密度區亮而高電流密度區不亮。
光用DPE類添加劑在一般條件下是可以的,但亮度不夠。為了得到滿意的鋅酸鹽鍍鋅鍍層,還需補加光亮劑,與添加劑配合使用。光亮劑有三乙醇胺、芳香醛或氮雜環的化合物,目前國內市售的光亮劑有WA(W906)、WB、ZB-80、ZBD-81等品種,它們性質近似,能有效地改善鍍層外觀質量,細化晶粒,但也在改進中。
對氰化物鍍鋅槽液轉化時應注意,由於氰化物鍍鋅的組成與DPE添加劑的鍍鋅體系最近似,為了採用無氰電鍍,消除氰化物污染,最常用的是自然過濾法,這樣,既可維持正常生產,又能逐步把組分調整到無氰電鍍的規範之內。
採用這個方法過濾,先停止補加氰化物,同時降低主鹽濃度,改用鐵陽極,按比例提高苛性鈉含量,控制NaCN∶Zn=(2~3)∶1。由於NaCN的降低,絡合作用即減弱,則雜質影響便表現出來,當ZnO降到20g/L、NaOH升到100g/L時,可加入Na2S或Zn粉處理槽液,再配合小電流電解處理。當分析NaCN在10g/L以下時,ZnO調到12g/L,NaOH應調到120g/L,此時再處理一次槽液,並開始加入DPE-Ⅲ(4mL/L)添加劑。當NaCN再降低時,可補加光亮劑WB或其分類型光亮劑。
鍍鋅是電鍍中量大面廣的品種,國內外為了提高鍍鋅的質量,除了在鍍液的組成比例,電鍍設備的改造、完善和槽液維護與管理之外,還著重於研究有效的添加劑,並針對以下各方面進行研究工作:
(1) 減少鍍層的脆性。從無氰鋅酸鹽鍍鋅層與氰化鍍鋅層的分析比較,前者鍍層中碳氫的含量高,表明有有機物夾雜,因而造成鍍層的脆性,所以要求一種合適的分子量和結構的有機添加劑是一個重要問題。
(2) 提高鹼性鍍鋅體系的電流效率。由於現代工業的發展,越來越注意經濟效益,提高體系的電流效率,不但可以提高生產力,同時還可減少氫脆。
(3) 防止變色的問題。這個問題不一定由添加劑的性質來決定,與鍍液中雜質的干擾,鍍後處理包括鈍化工藝的改進都密切有關,但添加劑的抗氧能力與在鍍層的夾雜程度也是造成鍍層變色的因素之一,顯然,以上所述問題都是目前有待研究和改進的課題。