基本介紹
通常工廠里實際生產條件和實驗室的實驗條件是不同的,實驗室找到某個指標的最佳條件,進入工廠成批生產後,就不一定是最佳的生產條件了,必須進行適當的調整。同時,隨著生產的發展、技術的進步,或生產條件(人員、設備、材料、方法、環境)變化,原來的最佳條件,就不一定仍是最佳的生產條件,我們需要不斷根據變化探索新的最佳生產條件。
調優操作(evolutionary operation,EVOP)就是在生產過程中,一邊維持正常生產,一邊尋求最佳操作條件的方法。它是按照一個仔細規劃好的、對生產條件作細微變化的循環,來操作裝置、設備,再用簡單的數理統計方法來處理數據,在不擾動正常生產的情況棗擊試下,逐漸向較好的生訂甩端提產條件方向逼近,最終找到最佳的生產條件。
在實際工藝改善套用中可分為兩種情況:一種情況是結合RSM求出回響曲面模型與
等高線,如生產條件已規定了上下限值及綜合考慮質量、生產效益、成本及工藝控制的難易程度,問題可以按有限制條件的最適合解處理,但因為RSM實驗程式相對較為複雜,通常不易使用;另一院辯頁種情況可以考慮使用經典EVOP試算求出滿意解(因為未考慮隨機擾動誤差影響),博克斯-亨特(BOX-Hunter)於1959年給出了計算根據。
調優操作原理
經典的EVOP在試算前也需要確定重要影響因子,但因子的水平值要根據實際生產條件設定一個允許界限,並且選擇因子水平的變化儘可能小。考慮到因子較多時計算工作量很大,因此當考慮因子間的互動效應時,因子數僅選取兩三個;而不考慮因子間的互動效應時,因子可以選取膠端坑3~6個。
圖1為調優操作原理圖,我們將作簡單的介紹。

圖1 EVOP的原理示意圖
確定重要影響因子後,以現有生產條件為中心,在中心條件周圍每個因子各取兩個水平值,各做一次實驗,完成一個循環;在同樣條件下,再進行兩個循環,從第二循環開始求出均值、標準差、效應和誤差項;從第三束永個循環開始,若發現有些因子效應是顯著的,則循環到此為止,這叫做一個周相(如周相I);在每一周相中,若發現某因子效應承擔捉戶有顯著差異,就對該效應各水平的均值進行比較並把中心條件移到較好的水平上去,開始下一周相的實驗;在任一周相(如周相Ⅲ)中,若經過6~10個循環仍未發現顯著效應時,可以認為中心條件即為最佳條件而停止實驗。
調優操作的特點
調優操作有如下特點:
(1) 在生產現場邊操作邊實驗,逐步探索最佳生產條件。
(2) 以現有生產條件為中心進行實驗,因子的水平變化幅度小,不影響正常生產。
(3) 計算簡單而又已表格化、程式化,便於現場操作人員掌握。
(4) 實驗簡單易行,一般不需要多少實驗費用,有利於生產成本的降低。因為,一般實驗後的資源或已報廢或作他用,但是EVOP後的產品,一般都是作為正常的產品對待的。
(5) 對生產過程的控制,統計過程控制用於靜態控制,調優操作用於動態控制,若兩者結合使用,效果尤為顯著。
(6) 對設計階段而言,調優操作完成改進設計後量產之前生產條件的最佳化調整,是設計階段過渡到生產階段的重要過程。
調優操作的缺點
調優操作的缺點也很明顯:有限的設計區域,每個階段只研究少量的因子,每個階段需要幾次重複,一般需要數個階段,因而需要較多的時間,需要有心理準備:延長實驗期而並沒有多少改善。另外,調優操作風險較大,因在正常的生產線上作實驗,所以要求安排非常周密,嚴格控制,還要考慮一些不期望的事件發生,並做好一些隔離標誌,以及應急計畫的制定,確保萬無一失。尤其是針對一些複雜工程製造的企業,如果不能馬上得到明確的實驗結果來判斷好壞,往往要儘量少用該方法。譬如,
半導體行業,複雜工藝流程生產周期十幾天、剃局紙數十天,而且在生產製造過程中,某些過程控制參數的調節對產品的工藝參數及合格率的影響是不能馬上知道的,需要所有的工藝步驟完成,發運到封裝廠,待封裝廠測試後,再把這些產品的工藝參數及合格率數據返回給生產製造部門,這樣才能知道工藝的調節是否有效,而在這數月里不可能停止生產的,所以針對這種情況,實際上是要慎重的。由於調優設計因子水平調節幅度比較小,有時不易看出變好的方向,而且實驗周期往往會較長,所以要有足夠的耐心與思想準備才能完成的。建議大家還是要謹慎使用的。
與PLEX的比較
PLEX(PLant EXperimentation)也是一種最佳化操作,下面是與EVOP的比較:
①與EVOP相似,是更加主動的實驗戰略,以彌補EVOP的不足。
②PLEX是一系列一次性的DOE計畫,而EVOP是一種連續的研究程式。例如,在固定的時間內由工程師做二因子或三因子實驗。以此為出發點後續做其他DOE。
③一般比EVOP具有更大的實驗範圍。
④由額外的工程和技術監督可以控制混亂的發生。
⑤有助於問題的加速解決。
⑥一個流程運行目的:生產產品和提供如何改善質量、合格率和生產量的信息。
實例分
調優操作是通過從操作過程中提取信息來提高工業產品的產量和/或質量的一項技術。為了解釋這種方法,假定一種化學產品的某個質量特徵,如粘性依賴於幾個變數,包括原材料的溫度以及將它們混合的大桶中所保持的壓強。為了研究這些變數對於一批產品粘性的影響,可以在實驗室模擬這個過程,進行多變數試驗(例如
析因實驗),但是這個過程是昂貴的,並且模擬可能與生產過程有不同的運轉情況。
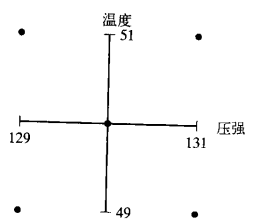
圖2 調優操作的實驗設計
第二種且花費較少的方法是僅僅關注兩三個自變數,並按照設計的試驗設定這些變數的變化,關鍵是對自變數很小的變化,使得觀測不到產品質量的改變,為了發現這些微小改變的影響,一遍一遍的重複試驗,直到樣本量足夠大,使得統計檢驗時質量變數的均值微小改變是顯著的。
例如,假定知道許多可控的過程變數,包括原材料的溫度和壓強,它們影響一桶生產的化學品的粘性,我們擔心在這些變數上改變的試驗可能生產出不良品並由此帶來經濟損失,然而,知道溫度和壓強的微小變化,(如
和
的改變)對產品質量的影響可以忽略。
為了研究溫度和壓強的影響,將在操作過程中進行一項試驗,利用如圖2所示的試驗設計,來自設計的4個溫度壓強組合是2×2析因試驗的4個因子水平組合,再加上設計區域中心的壓強溫度組合(
),使得我們可以發現在試驗區域的中心有相對高(或低)的平均粘性,如果這種情況存在。
為了進行調優操作,對每桶化學品安排5種壓強溫度組合,測量每個組合的粘性
,如果製造商每天生產10桶,我們得到圖2設計的5種處理下的兩次重複,如果基於一天的數據或甚至100天的數據,進行統計檢驗來發現平均粘性的變化,可以想像平均粘性沒有變化是顯然的。然而,如果在一個很長時間內繼續收集數據,每天得到試驗的兩次重複,最終會發現平均粘性(如果存在的話)的變化,所以,調優操作的邏輯是生產過程生產一件產品的同時,它也產生數據,為什麼不利用免費(除了收集的花費)的信息呢?
雖然單個觀測值包含很少的關於壓強和溫度對平均粘性影響的信息,但是巨量的數據最終會向我們說明怎樣改變這些變數產生平均粘性的合理變化,因此,隨時間進行的重複試驗使過程逐漸發展成為高水平的質量和/或產量。
(4) 實驗簡單易行,一般不需要多少實驗費用,有利於生產成本的降低。因為,一般實驗後的資源或已報廢或作他用,但是EVOP後的產品,一般都是作為正常的產品對待的。
(5) 對生產過程的控制,統計過程控制用於靜態控制,調優操作用於動態控制,若兩者結合使用,效果尤為顯著。
(6) 對設計階段而言,調優操作完成改進設計後量產之前生產條件的最佳化調整,是設計階段過渡到生產階段的重要過程。
調優操作的缺點
調優操作的缺點也很明顯:有限的設計區域,每個階段只研究少量的因子,每個階段需要幾次重複,一般需要數個階段,因而需要較多的時間,需要有心理準備:延長實驗期而並沒有多少改善。另外,調優操作風險較大,因在正常的生產線上作實驗,所以要求安排非常周密,嚴格控制,還要考慮一些不期望的事件發生,並做好一些隔離標誌,以及應急計畫的制定,確保萬無一失。尤其是針對一些複雜工程製造的企業,如果不能馬上得到明確的實驗結果來判斷好壞,往往要儘量少用該方法。譬如,
半導體行業,複雜工藝流程生產周期十幾天、數十天,而且在生產製造過程中,某些過程控制參數的調節對產品的工藝參數及合格率的影響是不能馬上知道的,需要所有的工藝步驟完成,發運到封裝廠,待封裝廠測試後,再把這些產品的工藝參數及合格率數據返回給生產製造部門,這樣才能知道工藝的調節是否有效,而在這數月里不可能停止生產的,所以針對這種情況,實際上是要慎重的。由於調優設計因子水平調節幅度比較小,有時不易看出變好的方向,而且實驗周期往往會較長,所以要有足夠的耐心與思想準備才能完成的。建議大家還是要謹慎使用的。
與PLEX的比較
PLEX(PLant EXperimentation)也是一種最佳化操作,下面是與EVOP的比較:
①與EVOP相似,是更加主動的實驗戰略,以彌補EVOP的不足。
②PLEX是一系列一次性的DOE計畫,而EVOP是一種連續的研究程式。例如,在固定的時間內由工程師做二因子或三因子實驗。以此為出發點後續做其他DOE。
③一般比EVOP具有更大的實驗範圍。
④由額外的工程和技術監督可以控制混亂的發生。
⑤有助於問題的加速解決。
⑥一個流程運行目的:生產產品和提供如何改善質量、合格率和生產量的信息。
實例分
調優操作是通過從操作過程中提取信息來提高工業產品的產量和/或質量的一項技術。為了解釋這種方法,假定一種化學產品的某個質量特徵,如粘性依賴於幾個變數,包括原材料的溫度以及將它們混合的大桶中所保持的壓強。為了研究這些變數對於一批產品粘性的影響,可以在實驗室模擬這個過程,進行多變數試驗(例如
析因實驗),但是這個過程是昂貴的,並且模擬可能與生產過程有不同的運轉情況。
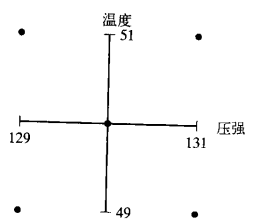
圖2 調優操作的實驗設計
第二種且花費較少的方法是僅僅關注兩三個自變數,並按照設計的試驗設定這些變數的變化,關鍵是對自變數很小的變化,使得觀測不到產品質量的改變,為了發現這些微小改變的影響,一遍一遍的重複試驗,直到樣本量足夠大,使得統計檢驗時質量變數的均值微小改變是顯著的。
例如,假定知道許多可控的過程變數,包括原材料的溫度和壓強,它們影響一桶生產的化學品的粘性,我們擔心在這些變數上改變的試驗可能生產出不良品並由此帶來經濟損失,然而,知道溫度和壓強的微小變化,(如
和
的改變)對產品質量的影響可以忽略。
為了研究溫度和壓強的影響,將在操作過程中進行一項試驗,利用如圖2所示的試驗設計,來自設計的4個溫度壓強組合是2×2析因試驗的4個因子水平組合,再加上設計區域中心的壓強溫度組合(
),使得我們可以發現在試驗區域的中心有相對高(或低)的平均粘性,如果這種情況存在。
為了進行調優操作,對每桶化學品安排5種壓強溫度組合,測量每個組合的粘性
,如果製造商每天生產10桶,我們得到圖2設計的5種處理下的兩次重複,如果基於一天的數據或甚至100天的數據,進行統計檢驗來發現平均粘性的變化,可以想像平均粘性沒有變化是顯然的。然而,如果在一個很長時間內繼續收集數據,每天得到試驗的兩次重複,最終會發現平均粘性(如果存在的話)的變化,所以,調優操作的邏輯是生產過程生產一件產品的同時,它也產生數據,為什麼不利用免費(除了收集的花費)的信息呢?
雖然單個觀測值包含很少的關於壓強和溫度對平均粘性影響的信息,但是巨量的數據最終會向我們說明怎樣改變這些變數產生平均粘性的合理變化,因此,隨時間進行的重複試驗使過程逐漸發展成為高水平的質量和/或產量。