《蛋氨酸結晶分離系統及結晶分離蛋氨酸的工藝》是重慶紫光化工股份有限公司於2014年3月14日申請的發明專利,該專利的申請號為2014100965090,公布號為CN103804252A,授權公布日為2014年5月21日,發明人是韋異勇、覃玉芳、耿明剛、徐洪、鄭皓,該發明屬於含氮有機化合物製備領域。
《蛋氨酸結晶分離系統及結晶分離蛋氨酸的工藝》公開了一種蛋氨酸結晶分離系統,包括進料口、換熱器、結晶器、分離系統和促使溶體流動的循環泵,在循環泵的作用下,原料由進料口進入換熱器,經換熱器換熱後進入結晶器結晶,結晶所得溶液一部分返回換熱器繼續循環,另一部分進入分離系統進行分離;分離所得固態產物排出系統,退出循環,液態產物返回換熱器繼續循環;該實施例還公開了利用上述系統結晶分離蛋氨酸的工藝。該發明的蛋氨酸結晶分離系統在整個處理過程均在封閉環境進行,可以連續穩定生產,該發明結晶分離系統無需外加熱源,可節約大量能源並避免污染環境,該發明結晶分離蛋氨酸的工藝,獲得蛋氨酸的堆密度大,純度高。
2016年12月7日,《蛋氨酸結晶分離系統及結晶分離蛋氨酸的工藝》獲得第十八屆中國專利優秀獎。
(概述圖為《蛋氨酸結晶分離系統及結晶分離蛋氨酸的工藝》摘要附圖)
基本介紹
- 中文名:蛋氨酸結晶分離系統及結晶分離蛋氨酸的工藝
- 公布號:CN103804252A
- 公布日:2014年5月21日
- 申請號:2014100965090
- 申請日:2014年3月14日
- 申請人:重慶紫光化工股份有限公司
- 地址:重慶市永川區化工路426號
- 發明人:韋異勇、覃玉芳、耿明剛、徐洪、鄭皓
- Int.Cl.:C07C323/58(2006.01)I、C07C319/28(2006.01)I
- 代理機構:北京同恆源智慧財產權代理有限公司
- 代理人:趙榮之
- 類別:發明專利
專利背景,發明內容,專利目的,技術方案,有益效果,附圖說明,權利要求,實施方式,榮譽表彰,
專利背景
蛋氨酸是一種非極性α胺基酸,廣泛套用與飼料及醫藥行業。2014年3月前普遍採用海因法製備蛋氨酸,即首先製備含蛋氨酸的溶液,然後對蛋氨酸溶液進行結晶得到蛋氨酸固體。2014年3月前業內普遍採用分段蒸發的方法從蛋氨酸溶液中提取蛋氨酸,其工藝路線如圖1所示:含有蛋氨酸的溶液首先進入第一蒸發段在高溫區(約130-150℃)進行蒸發,蒸發過程中溶液中的水分和其他雜質隨氣體排放到空氣中,蒸發所得高濃度蛋氨酸溶液通過管道進入下一蒸發段並在較低溫度繼續蒸發,如此循環直至濃縮得到蛋氨酸成品。
這種分段蒸髮結晶蛋氨酸的方法原理簡單,操作方便;但也存在以下缺點:首先,這種方法蒸發過程中產生大量的水蒸氣及雜質氣體,消耗大量的能量並帶來空氣污染;其次,這種方法離心後固態產物水含量高,乾燥後堆密度小(通常小於0.3)需造粒,產品中硫酸鈉含量高,顆粒過於細小,並且蛋氨酸純度不高,通常帶有一定氣味。
發明內容
專利目的
《蛋氨酸結晶分離系統及結晶分離蛋氨酸的工藝》的目的在於提供一種蛋氨酸結晶分離系統和基於該系統的結晶分離蛋氨酸的工藝。
技術方案
蛋氨酸結晶分離系統,包括進料口、換熱器、結晶器、分離系統和促使溶體流動的循環裝置,在循環裝置的作用下,原料由進料口進入換熱器,經換熱器換熱後進入結晶器結晶,結晶所得混合液一部分返回換熱器繼續循環,另一部分進入分離系統進行分離;分離所得固態產物排出系統,退出循環,液態產物返回換熱器繼續循環。
作為《蛋氨酸結晶分離系統及結晶分離蛋氨酸的工藝》蛋氨酸結晶分離系統的改進,所述分離系統包括稀相濃相分離裝置、離心機和蒸發濃縮裝置;結晶後進入分離系統的混合液首先經稀相濃相分離裝置初步分離為清液和高蛋氨酸固含量混合液,所述高蛋氨酸固含量混合液進入離心機進一步分離為蛋氨酸和清液;所述蛋氨酸排出系統、退出循環,所述稀相濃相分離裝置和離心機分離所得清液一部分返回換熱器繼續循環,另一部分進入蒸發濃縮裝置進一步分離為硫酸鈉和清液;所述硫酸鈉排出系統、退出循環,所述清液返回換熱器繼續循環。
作為《蛋氨酸結晶分離系統及結晶分離蛋氨酸的工藝》蛋氨酸結晶分離系統的改進,所述分離系統還包括清液槽,所述稀相濃相分離裝置和離心機分離得到的清液進入清液槽混合暫存後一部分返回換熱器繼續循環,另一部分進入蒸發濃縮裝置進一步分離。
作為《蛋氨酸結晶分離系統及結晶分離蛋氨酸的工藝》蛋氨酸結晶分離系統的進一步改進,所述結晶器為立式攪拌結晶器。
一種分離蛋氨酸的工藝,包括以下步驟:
(1)向結晶分離系統注入初始量的蛋氨酸和硫酸鈉混合溶液,所述混合溶液經換熱器換熱後進入結晶器結晶;結晶所得混合液一部分返回換熱器繼續循環,另一部分進入分離系統進行分離;分離後得到蛋氨酸、硫酸鈉以及蛋氨酸和硫酸鈉混合清液,蛋氨酸和硫酸鈉經出料口排出,蛋氨酸和硫酸鈉混合清液返回換熱器繼續循環;
(2)根據蛋氨酸和硫酸鈉的生成量向換熱器加入平衡量的蛋氨酸鈉和硫酸。
作為《蛋氨酸結晶分離系統及結晶分離蛋氨酸的工藝》分離蛋氨酸工藝的改進,步驟(1)注入的蛋氨酸和硫酸鈉混合溶液中蛋氨酸的質量濃度為5%-10%wt,硫酸鈉的質量濃度為5%-10%wt。
作為《蛋氨酸結晶分離系統及結晶分離蛋氨酸的工藝》分離蛋氨酸工藝的改進,步驟(1)蛋氨酸結晶時的溫度為8-45℃。
作為《蛋氨酸結晶分離系統及結晶分離蛋氨酸的工藝》分離蛋氨酸工藝的改進,步驟(1)結晶所得溶液中蛋氨酸的固含量為3-10%wt。
作為《蛋氨酸結晶分離系統及結晶分離蛋氨酸的工藝》分離蛋氨酸工藝的改進,步驟(1)結晶後進入分離系統的混合液首先經稀相濃相分離裝置分離為清液和蛋氨酸的固含量為10-30%wt的混合液,所述蛋氨酸的固含量為10-30%wt的混合液進入離心機進一步分離為蛋氨酸和清液;所述蛋氨酸排出系統、退出循環,所述稀相濃相分離裝置和離心機分離所得清液一部分返回換熱器繼續循環,另一部分進入蒸發濃縮裝置進一步分離為硫酸鈉和清液;所述硫酸鈉排出系統、退出循環,所述清液返回換熱器繼續循環。
作為《蛋氨酸結晶分離系統及結晶分離蛋氨酸的工藝》分離蛋氨酸工藝的進一步改進,蛋氨酸和硫酸鈉混合溶液進入結晶器的速度為15-40立方米/小時,結晶器內有效容積為30-60立方米,結晶器內攪拌速度為15-100轉/分鐘。
有益效果
首先,《蛋氨酸結晶分離系統及結晶分離蛋氨酸的工藝》的蛋氨酸結晶分離系統整個處理過程(硫酸鈉析出過程除外)均是在封閉環境中進行,並且不需要外加熱源,可以節約大量能源並避免污染環境;其次,該發明在結晶器前設定了換熱器,使得物料進入結晶器之前溫度均勻適宜,可以顯著提高最終產品性能;再次,該發明可以根據蛋氨酸和硫酸鈉的產量準確及時的向換熱器中加入平衡量的蛋氨酸和硫酸鈉溶液,可以維持整個循環系統中的物料平衡,使得整個生產過程可以連續進行,並有助於提高產品質量的穩定性;另外,該發明結晶分離蛋氨酸的工藝將結晶溫度控制在8-45℃,可以有效的減少蛋氨酸分解從而減少副產物雜質;將原料液中蛋氨酸和硫酸鈉的質量濃度控制在5%-10%wt,有利於晶核的形成和晶型的成長,產品的質量和收率高;最後,該發明方法所製得的蛋氨酸堆密度普遍大於0.6,避免了常規方法還需要對製得的蛋氨酸進行造粒的缺陷。
附圖說明
圖1為2014年3月前已有技術中濃縮蒸發製備蛋氨酸的工藝流程圖;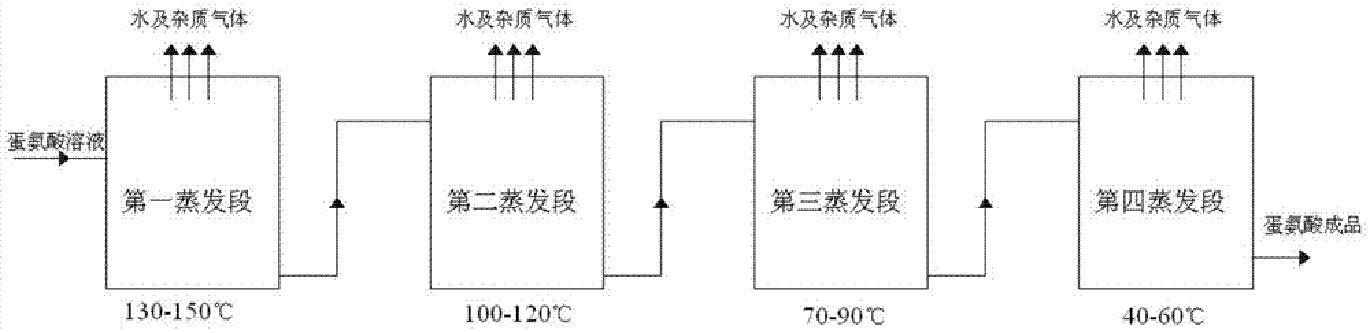
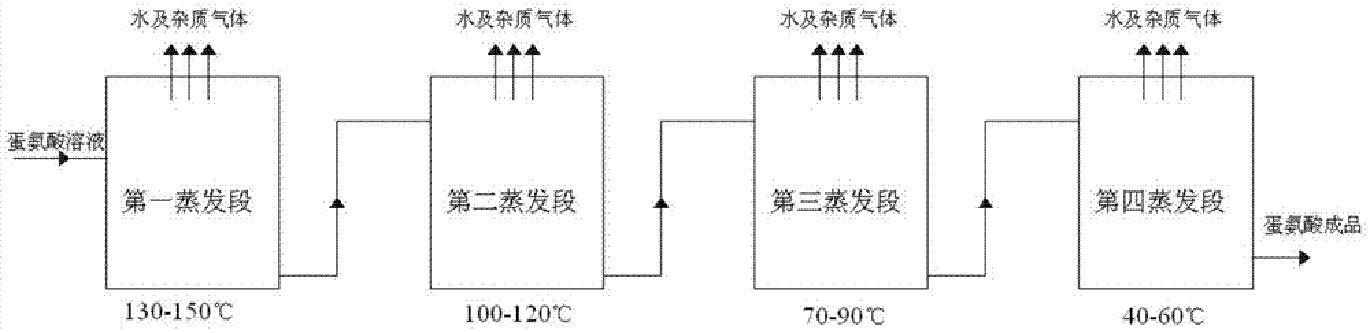
圖1
圖2為《蛋氨酸結晶分離系統及結晶分離蛋氨酸的工藝》蛋氨酸結晶分離系統的示意圖,圖中箭頭方向表示物料走向,虛線框內為分離系統。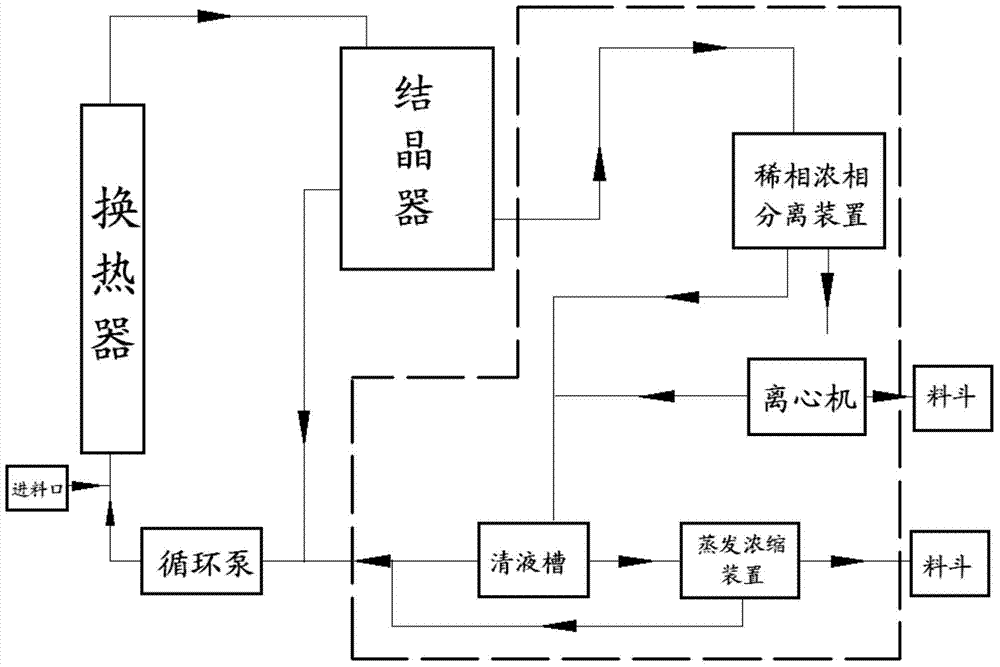
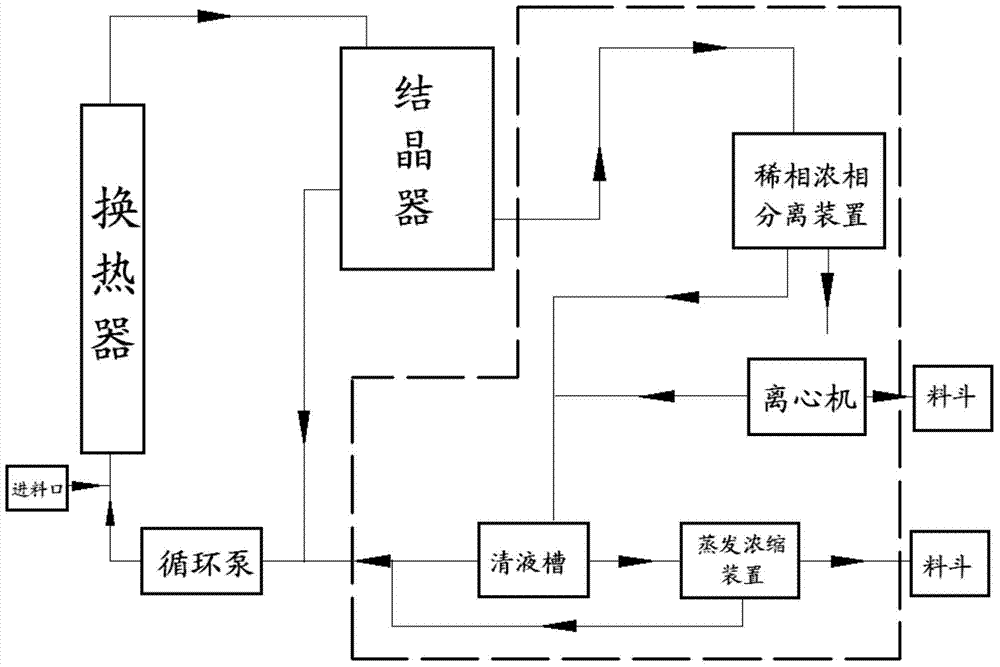
圖2
權利要求
1.蛋氨酸結晶分離系統,包括進料口、換熱器、結晶器、分離系統和促使溶體流動的循環裝置,其特徵在於:在循環裝置的作用下,原料由進料口進入換熱器,經換熱器換熱後進入結晶器結晶,結晶所得混合液一部分返回換熱器繼續循環,另一部分進入分離系統進行分離;分離所得固態產物排出系統,退出循環,液態產物返回換熱器繼續循環。
2.根據權利要求1所述蛋氨酸結晶分離系統,其特徵在於:所述分離系統包括稀相濃相分離裝置、離心機和蒸發濃縮裝置;結晶後進入分離系統的混合液首先經稀相濃相分離裝置初步分離為清液和高蛋氨酸固含量混合液,所述高蛋氨酸固含量混合液進入離心機進一步分離為蛋氨酸和清液;所述蛋氨酸排出系統、退出循環,所述稀相濃相分離裝置和離心機分離所得清液一部分返回換熱器繼續循環,另一部分進入蒸發濃縮裝置進一步分離為硫酸鈉和清液;所述硫酸鈉排出系統、退出循環,所述清液返回換熱器繼續循環。
3.根據權利要求2所述蛋氨酸結晶分離系統,其特徵在於:所述分離系統還包括清液槽,所述稀相濃相分離裝置和離心機分離得到的清液進入清液槽混合暫存後一部分返回換熱器繼續循環,另一部分進入蒸發濃縮裝置進一步分離。
4.根據權利要求1-3任意一項所述蛋氨酸結晶分離系統,其特徵在於:所述結晶器為立式攪拌結晶器。
5.一種基於如權利要求4所述蛋氨酸結晶分離系統結晶分離蛋氨酸的工藝,其特徵在於:包括以下步驟:
(1)向結晶分離系統注入初始量的蛋氨酸和硫酸鈉混合溶液,所述混合溶液經換熱器換熱後進入結晶器結晶;結晶所得混合液一部分返回換熱器繼續循環,另一部分進入分離系統進行分離;分離後得到蛋氨酸、硫酸鈉以及蛋氨酸和硫酸鈉混合清液,蛋氨酸和硫酸鈉經出料口排出,蛋氨酸和硫酸鈉混合清液返回換熱器繼續循環;
(2)根據蛋氨酸和硫酸鈉的生成量向換熱器加入平衡量的蛋氨酸鈉和硫酸。
6.根據權利要求5所述結晶分離蛋氨酸的工藝,其特徵在於:步驟(1)注入的蛋氨酸和硫酸鈉混合溶液中蛋氨酸的質量濃度為5%-10%wt,硫酸鈉的質量濃度為5%-10%wt。
7.根據權利要求5所述結晶分離蛋氨酸的工藝,其特徵在於:步驟(1)蛋氨酸結晶時的溫度為8-45℃。
8.根據權利要求5所述結晶分離蛋氨酸的工藝,其特徵在於:步驟(1)結晶所得溶液中蛋氨酸的固含量為3-10%wt。
9.根據權利要求5所述結晶分離蛋氨酸的工藝,其特徵在於:步驟(1)結晶後進入分離系統的混合液首先經稀相濃相分離裝置分離為清液和蛋氨酸的固含量量為10-30%wt的混合液,所述蛋氨酸的固含量量為10-30%wt的混合液進入離心機進一步分離為蛋氨酸和清液;所述蛋氨酸排出系統、退出循環,所述稀相濃相分離裝置和離心機分離所得清液一部分返回換熱器繼續循環,另一部分進入蒸發濃縮裝置進一步分離為硫酸鈉和清液;所述硫酸鈉排出系統、退出循環,所述清液返回換熱器繼續循環。
10.根據權利要求5-9任意一項所述結晶分離蛋氨酸的工藝,其特徵在於:蛋氨酸和硫酸鈉混合溶液進入結晶器的速度為15-40立方米/小時,結晶器內有效容積為30-60立方米。
實施方式
實施例1:
如圖2所示,該實施例蛋氨酸結晶分離系統,包括進料口,換熱器、結晶器,強制循環泵和分離系統,所述進料口通過管道與換熱器入口相通,所述換熱器出口與結晶器入口相通,所述結晶器設有兩個出口,其中一個出口與強制循環泵入口相連,另一個出口與分離系統入口相連;所述分離系統設有蛋氨酸出口、硫酸鈉出口和清液出口,其中蛋氨酸出口和硫酸鈉出口分別與外界料斗相通,清液出口則與強制循環泵入口相連,所述循環泵的出口與通過管道與換熱器入口相通。在強制循環泵的作用下,原料經進料口進入換熱器,經換熱器換熱後進入結晶器結晶,結晶後混合液的一部分經強制循環泵回流換熱器,另一部分則進入分離器,經分離器分離為蛋氨酸、硫酸鈉和蛋氨酸與硫酸鈉混合清液,清液經強制循環泵回流換熱器繼續循環,蛋氨酸和硫酸鈉則分別經相應出口排出,退出循環。
作為該實施例蛋氨酸結晶分離系統的改進,所述分離系統包括稀相濃相分離裝置、離心機和蒸發濃縮裝置;所述混合液由結晶器進入稀相濃相分離裝置後分離為蛋氨酸和硫酸鈉混合清液和高蛋氨酸固含量混合液,所述高蛋氨酸固含量混合液進入離心機後進一步分離為蛋氨酸、蛋氨酸和硫酸鈉的混合清液;所述蛋氨酸經出料口排出,所述稀相濃相分離裝置和離心機分離得到的蛋氨酸和硫酸鈉混合清液一部分返回換熱器繼續循環,另一部分進入蒸發濃縮裝置濃縮得到硫酸鈉和濃縮後的蛋氨酸和硫酸鈉的飽和溶液,硫酸鈉經出料口排出,濃縮後的蛋氨酸和硫酸鈉的飽和溶液返回換熱器繼續循環。
作為該實施例蛋氨酸結晶分離系統的進一步改進,所述分離系統還包括清液槽,所述稀相濃相分離裝置分離得到的蛋氨酸和硫酸鈉混合清液和離心機離心得到的離心清母液進入清液槽混合後一部分返回換熱器繼續循環,另一部分進入蒸發濃縮裝置蒸發濃縮。
作為該實施例蛋氨酸結晶分離系統的進一步改進,所述結晶器為全混式攪拌結晶器。
該實施例結晶分離蛋氨酸的工藝,包括以下步驟:
(1)向結晶分離系統注入初始量的蛋氨酸和硫酸鈉混合溶液,所述混合溶液經換熱器換熱後進入結晶器結晶;結晶所得混合液一部分返回換熱器繼續循環,另一部分進入分離系統進行分離;分離後得到蛋氨酸、硫酸鈉以及蛋氨酸和硫酸鈉混合清液,蛋氨酸和硫酸鈉經出料口排出,蛋氨酸和硫酸鈉混合清液返回換熱器繼續循環;
(2)根據蛋氨酸和硫酸鈉的生成量向換熱器加入等量的蛋氨酸鈉和硫酸。
作為該實施例結晶分離蛋氨酸的工藝的改進,步驟(1)注入的蛋氨酸和硫酸鈉混合溶液中蛋氨酸的質量濃度為5%wt,硫酸鈉的質量濃度為5%wt。
作為該實施例結晶分離蛋氨酸的工藝的改進,步驟(1)蛋氨酸結晶時的溫度為8℃。
作為該實施例結晶分離蛋氨酸的工藝的改進,步驟(1)結晶所得溶液中蛋氨酸的固含量為3%wt。
作為該實施例結晶分離蛋氨酸的工藝的進一步改進,步驟(1)結晶後進入分離系統的混合液首先經稀相濃相分離裝置分離為清液和蛋氨酸的固含量為12%wt的混合液,所述蛋氨酸的固含量為12%wt的混合液進入離心機進一步分離為蛋氨酸和清液;所述蛋氨酸排出系統、退出循環,所述稀相濃相分離裝置和離心機分離所得清液一部分返回換熱器繼續循環,另一部分進入蒸發濃縮裝置進一步分離為硫酸鈉和清液;所述硫酸鈉排出系統、退出循環,所述清液返回換熱器繼續循環。
作為該實施例結晶分離蛋氨酸的工藝的進一步改進,蛋氨酸和硫酸鈉混合溶液進入結晶器的速度為15立方米/小時,結晶器內有效容積為60立方米,結晶器內攪拌速度為100轉/分鐘。
經檢測,該實施例所得蛋氨酸鈉的堆密度為0.62。
實施例2:
該實施例蛋氨酸結晶分離系統與實施例1的區別在於,該實施例中循環泵的數目為2個,除實施例1所述強制循環泵外,另一循環泵設定在分離系統和結晶器的連線迴路上,且該實施例經分離系統分離得到的蛋氨酸和硫酸鈉的清液直接與換熱器入口相連。
該實施例結晶分離蛋氨酸的工藝,包括以下步驟:
(1)向結晶分離系統注入初始量的蛋氨酸和硫酸鈉混合溶液,所述混合溶液經換熱器換熱後進入結晶器結晶;結晶所得混合液一部分返回換熱器繼續循環,另一部分進入分離系統進行分離;分離後得到蛋氨酸、硫酸鈉以及蛋氨酸和硫酸鈉混合清液,蛋氨酸和硫酸鈉經出料口排出,蛋氨酸和硫酸鈉混合清液返回換熱器繼續循環;
(2)根據蛋氨酸和硫酸鈉的生成量向換熱器加入蛋氨酸鈉和硫酸,控制蛋氨酸鈉和硫酸的加入量使得混合液中蛋氨酸和硫酸鈉的質量濃度波動小於1.5%。
作為該實施例結晶分離蛋氨酸的工藝的改進,步驟(1)注入的蛋氨酸和硫酸鈉混合溶液中蛋氨酸的質量濃度為10%wt,硫酸鈉的質量濃度為10%wt。
作為該實施例結晶分離蛋氨酸的工藝的改進,步驟(1)蛋氨酸結晶時的溫度為45℃。
作為該實施例結晶分離蛋氨酸的工藝的改進,步驟(1)結晶所得溶液中蛋氨酸的固含量為10%wt。
作為該實施例結晶分離蛋氨酸的工藝的進一步改進,步驟(1)結晶後進入分離系統的混合液首先經稀相濃相分離裝置分離為清液和蛋氨酸的固含量為30%wt的混合液,所述蛋氨酸的固含量為30%wt的混合液進入離心機進一步分離為蛋氨酸和清液;所述蛋氨酸排出系統、退出循環,所述稀相濃相分離裝置和離心機分離所得清液一部分返回換熱器繼續循環,另一部分進入蒸發濃縮裝置進一步分離為硫酸鈉和清液;所述硫酸鈉排出系統、退出循環,所述清液返回換熱器繼續循環。
作為該實施例結晶分離蛋氨酸的工藝的進一步改進,蛋氨酸和硫酸鈉混合溶液進入結晶器的速度為40立方米/小時,結晶器內有效容積為30立方米,結晶器內攪拌速度為15轉/分鐘。
經檢測,該實施例製得的蛋氨酸的堆密度為0.67。
實施例3:
該實施例蛋氨酸結晶分離系統與實施例1相同。
該實施例結晶分離蛋氨酸的工藝,包括以下步驟:
(1)向結晶分離系統注入初始量的蛋氨酸和硫酸鈉混合溶液,所述混合溶液經換熱器換熱後進入結晶器結晶;結晶所得混合液一部分返回換熱器繼續循環,另一部分進入分離系統進行分離;分離後得到蛋氨酸、硫酸鈉以及蛋氨酸和硫酸鈉混合清液,蛋氨酸和硫酸鈉經出料口排出,蛋氨酸和硫酸鈉混合清液返回換熱器繼續循環;
(2)根據蛋氨酸和硫酸鈉的生成量向換熱器加入蛋氨酸鈉和硫酸,控制蛋氨酸鈉和硫酸的加入量使得混合液中蛋氨酸和硫酸鈉的質量濃度波動小於3%。
作為該實施例結晶分離蛋氨酸的工藝的改進,步驟(1)注入的蛋氨酸和硫酸鈉混合溶液中蛋氨酸的質量濃度為8%wt,硫酸鈉的質量濃度為8%wt。
作為該實施例結晶分離蛋氨酸的工藝的改進,步驟(1)蛋氨酸結晶時的溫度為20℃。
作為該實施例結晶分離蛋氨酸的工藝的改進,步驟(1)結晶所得溶液中蛋氨酸的固含量為6%wt。
作為該實施例結晶分離蛋氨酸的工藝的進一步改進,步驟(1)結晶後進入分離系統的混合液首先經稀相濃相分離裝置分離為清液和蛋氨酸的固含量為18%wt的混合液,所述蛋氨酸的固含量為18%wt的混合液進入離心機進一步分離為蛋氨酸和清液;所述蛋氨酸排出系統、退出循環,所述稀相濃相分離裝置和離心機分離所得清液一部分返回換熱器繼續循環,另一部分進入蒸發濃縮裝置進一步分離為硫酸鈉和清液;所述硫酸鈉排出系統、退出循環,所述清液返回換熱器繼續循環。
作為該實施例結晶分離蛋氨酸的工藝的進一步改進,蛋氨酸和硫酸鈉混合溶液進入結晶器的速度為25立方米/小時,結晶器內有效容積為45立方米,結晶器內攪拌速度為60轉/分鐘。
經檢測,該實施例製得的蛋氨酸的堆密度為0.7。
實施例4:
該實施例蛋氨酸結晶分離系統與實施例2相同。
該實施例結晶分離蛋氨酸的工藝,包括以下步驟:
(1)向結晶分離系統注入初始量的蛋氨酸和硫酸鈉混合溶液,所述混合溶液經換熱器換熱後進入結晶器結晶;結晶所得混合液一部分返回換熱器繼續循環,另一部分進入分離系統進行分離;分離後得到蛋氨酸、硫酸鈉以及蛋氨酸和硫酸鈉混合清液,蛋氨酸和硫酸鈉經出料口排出,蛋氨酸和硫酸鈉混合清液返回換熱器繼續循環;
(2)根據蛋氨酸和硫酸鈉的生成量向換熱器加入等量的蛋氨酸鈉和硫酸。
作為該實施例結晶分離蛋氨酸的工藝的改進,步驟(1)注入的蛋氨酸和硫酸鈉混合溶液中蛋氨酸的質量濃度為6%wt,硫酸鈉的質量濃度為6%wt。
作為該實施例結晶分離蛋氨酸的工藝的改進,步驟(1)蛋氨酸結晶時的溫度為15℃。
作為該實施例結晶分離蛋氨酸的工藝的改進,步驟(1)結晶所得溶液中蛋氨酸的固含量為5%wt。
作為該實施例結晶分離蛋氨酸的工藝的進一步改進,步驟(1)結晶後進入分離系統的混合液首先經稀相濃相分離裝置分離為清液和蛋氨酸的固含量為15%wt的混合液,所述蛋氨酸的固含量為15%wt的混合液進入離心機進一步分離為蛋氨酸和清液;所述蛋氨酸排出系統、退出循環,所述稀相濃相分離裝置和離心機分離所得清液一部分返回換熱器繼續循環,另一部分進入蒸發濃縮裝置進一步分離為硫酸鈉和清液;所述硫酸鈉排出系統、退出循環,所述清液返回換熱器繼續循環。
作為該實施例結晶分離蛋氨酸的工藝的進一步改進,蛋氨酸和硫酸鈉混合溶液進入結晶器的速度為20立方米/小時,結晶器內有效容積為38立方米,結晶器內攪拌速度為35轉/分鐘。
經檢測,該實施例製得的蛋氨酸的堆密度為0.65。
實施例5:
該實施例蛋氨酸結晶分離系統與實施例2相同。
該實施例結晶分離蛋氨酸的工藝,包括以下步驟:
(1)向結晶分離系統注入初始量的蛋氨酸和硫酸鈉混合溶液,所述混合溶液經換熱器換熱後進入結晶器結晶;結晶所得混合液一部分返回換熱器繼續循環,另一部分進入分離系統進行分離;分離後得到蛋氨酸、硫酸鈉以及蛋氨酸和硫酸鈉混合清液,蛋氨酸和硫酸鈉經出料口排出,蛋氨酸和硫酸鈉混合清液返回換熱器繼續循環;
(2)根據蛋氨酸和硫酸鈉的生成量向換熱器加入等量的蛋氨酸鈉和硫酸。
作為該實施例結晶分離蛋氨酸的工藝的改進,步驟(1)注入的蛋氨酸和硫酸鈉混合溶液中蛋氨酸的質量濃度為8%wt,硫酸鈉的質量濃度為8%wt。
作為該實施例結晶分離蛋氨酸的工藝的改進,步驟(1)蛋氨酸結晶時的溫度為32℃。
作為該實施例結晶分離蛋氨酸的工藝的改進,步驟(1)結晶所得溶液中蛋氨酸的固含量為8%wt。
作為該實施例結晶分離蛋氨酸的工藝的進一步改進,步驟(1)結晶後進入分離系統的混合液首先經稀相濃相分離裝置分離為清液和蛋氨酸的固含量為25%wt的混合液,所述蛋氨酸的固含量為25%wt的混合液進入離心機進一步分離為蛋氨酸和清液;所述蛋氨酸排出系統、退出循環,所述稀相濃相分離裝置和離心機分離所得清液一部分返回換熱器繼續循環,另一部分進入蒸發濃縮裝置進一步分離為硫酸鈉和清液;所述硫酸鈉排出系統、退出循環,所述清液返回換熱器繼續循環。
作為該實施例結晶分離蛋氨酸的工藝的進一步改進,蛋氨酸和硫酸鈉混合溶液進入結晶器的速度為35立方米/小時,結晶器內有效容積為50立方米,結晶器內攪拌速度為80轉/分鐘。
經檢測,該實施例製得的蛋氨酸的堆密度為0.73。
對比實施例1:
該實施例蛋氨酸結晶分離裝置如圖1所示,包括四個蒸發段,第一蒸發段的物料出口與第二蒸發段的物料入口相連,第二蒸發段的物料出口與第三蒸發段的物料出口相連,第三蒸發段的物料出口與第四蒸發段物料入口相連;含蛋氨酸的溶液首先進入第一蒸發段進行蒸發,然後依次進入第二、第三、第四蒸發段蒸發,經過第四蒸發段蒸發後分離得到蛋氨酸成品。
該實施例具體操作過程如下:
(1)向第一蒸發段注入蛋氨酸和硫酸鈉混合溶液並在130℃進行蒸發,其中蛋氨酸的質量濃度為10-15%wt,硫酸鈉的質量濃度為12-20%wt;
(2)第一蒸發段蒸發所得物料進入第二蒸發段繼續蒸發,蒸發溫度為110℃;
(3)第一蒸發段蒸發所得物料進入第二蒸發段繼續蒸發,蒸發溫度為80℃;
(4)第一蒸發段蒸發所得物料進入第二蒸發段繼續蒸發,蒸發溫度為50℃;
(5)分離步驟(4)所得物料即得蛋氨酸成品。
經檢測,該實施例製得的蛋氨酸的堆密度為0.27,遠低於實施例1-5的水平。
需要說明的是,以上實施例中稀相濃相分離裝置具體形式可以多種多樣,只要可以起到將結晶後進入分離系統的混合液分離為清液和具有一定蛋氨酸固含量的混合液即可,該發明中稀相濃相分離裝置優選為籌厚器。
《蛋氨酸結晶分離系統及結晶分離蛋氨酸的工藝》的蛋氨酸結晶分離系統整個處理過程均是在封閉環境中進行,並且不需要外加熱源,可以節約大量能源並避免污染環境;該發明在結晶器前設定了換熱器,使得物料進入結晶器之前溫度均勻適宜,可以顯著提高最終產品性能;該發明可以根據蛋氨酸和硫酸鈉的產量準確及時的向換熱器中加入平衡量的蛋氨酸和硫酸鈉溶液,可以維持整個循環系統中的物料平衡,使得整個生產過程可以連續進行,並有助於提高產品質量的穩定性;該發明結晶分離蛋氨酸的工藝將結晶溫度控制在8-45℃,可以有效的減少蛋氨酸分解從而減少副產物雜質;將原料液中蛋氨酸和硫酸鈉的質量濃度控制在為5%-10%wt,對晶核的形成和晶型的成長十分有利,有利於有效提高產品的質量和收率。
榮譽表彰
2016年12月7日,《蛋氨酸結晶分離系統及結晶分離蛋氨酸的工藝》獲得第十八屆中國專利優秀獎。