“線圈骨架”即用於纏繞線纜的骨架,一般用於電子元器件上呈“工”字形的塑膠件。在工業生產中,線圈骨架是依靠“線圈骨架注射模具”來進行生產批量的。“線圈骨架注射模設計”,運用的是pro/e軟體對線圈骨架注射模具進行設計的。
基本介紹
- 中文名:線圈骨架注射模設計
- 外文名:線圈骨架注射模設計
- 運用:是pro/e軟體
- 採用:PET-530(本色)
塑件分析
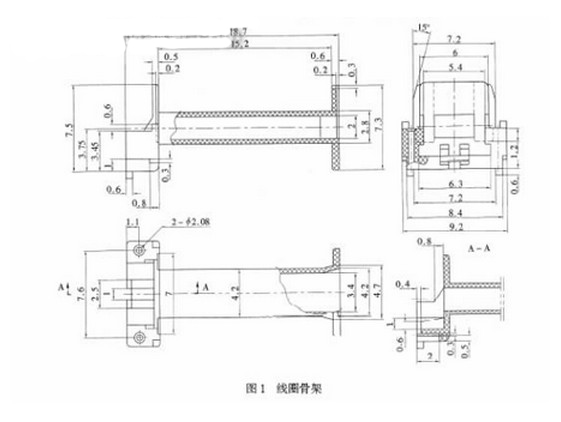
設計方案
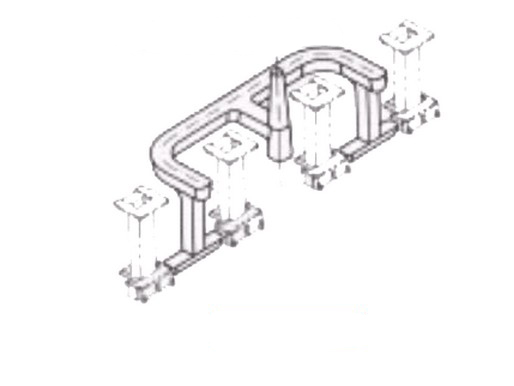
設計步驟
分型設計
澆口設計
流道設計
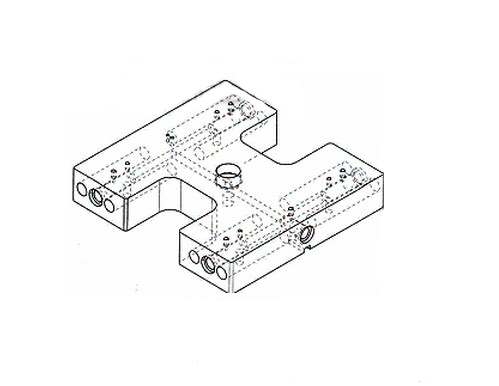
工作過程
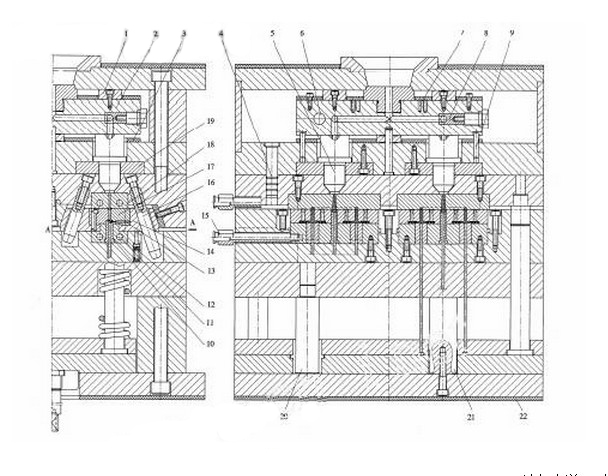
“線圈骨架”即用於纏繞線纜的骨架,一般用於電子元器件上呈“工”字形的塑膠件。在工業生產中,線圈骨架是依靠“線圈骨架注射模具”來進行生產批量的。“線圈骨架注射模設計”,運用的是pro/e軟體對線圈骨架注射模具進行設計的。
“線圈骨架”即用於纏繞線纜的骨架,一般用於電子元器件上呈“工”字形的塑膠件。在工業生產中,線圈骨架是依靠“線圈骨架注射模具”來進行生產批量的。“線圈骨架注射...
《注射成型模具設計108例》一書的出版社是中國輕工業出版社,作者是(德)林納 /...3.18 成型聚醯胺(尼龍)6.6軟管接頭的注射模具 3.19 成型中間繼電器線圈骨架的...
介紹的模具有熱流道模具、冷流道模具、疊層模具、大型模具、特殊設計的模具以及...3.19 成型中間繼電器線圈骨架的雙型腔注射模具3.20 成型聚丙烯殼體的雙型腔注射...
二、電流線圈骨架注射模設計230 第六節模具設計及套用實例239 一、基於UG的汽車覆蓋件模具設計239 二、支架衝壓工藝與模具設計242 三、緊固圈的工藝及模具設計246 ...
本書第l章介紹了設計新型注塑模時必須注意的問題和設計要點;第2章至第4章介紹...7.2.3 線圈骨架模具7.2.4 帶內外側抽芯機構的熱流道疊層模...
《塑膠注射模抽芯機構圖冊》吳祥生 著,該書是一本為廣大從事塑膠注射模設計和...2.10 雙聲道磁頭微型線圈骨架 注射模 ……… 2282.11 線軸注射...
本書可作為大、中專院校塑膠模具課程的輔助教材和課程設計、畢業設計的參考教材,...39.皮帶輪注塑模 40.固定圈注塑模 41.骨架多層注塑模 42.小線圈骨架注塑模 ...
《實用注塑模具結構圖集》避開塑膠製品設計及模具結構分析等繁瑣篇幅,從國民經濟各...實例14 棘輪輪片注塑模實例15 線圈骨架注塑模實例16 繞線軸注塑模...
二、電流線圈骨架注射模設計思考題和習題單元八 壓縮模與壓注模結構第一節 壓縮成型與壓注成型設備及壓機參數校核一、壓縮成型與壓注成型設備...
體現該軟體在產品造型和注射模具設計中的強大功能,展現它的靈活性和工程設計嚴謹...8.3啤酒桶模具設計第9章線圈骨架產品造型與模具設計9.1設計任務及方案...
印刷電路板上.環型變壓器具有高度的靈活性,可根據機箱與整體裝配的要求,設計...由於製作環形變壓器不需要衝模,也不需要線圈骨架注塑模具,所以生產周期短,適用於...