納米科技是本世紀科技發展的重要技術領域,納米科技將創造另一波技術創新及產業革命。其套用領域非常廣,遍及電子產業﹑光電產業﹑醫藥生化產業﹑化纖產業﹑建材產業﹑金屬產業﹑基礎產業﹑噴繪油墨、晶片拋光液、電子陶瓷、細胞破碎、化妝品、藥品、紡織品、噴墨墨水、生物製藥、金屬納米材料等領域…等。不論其套用領域為何,所需要用的材料均為次微米或納米級尺度之材料。如何得到納米級粉體及如何將納米級材料分散到其最終產品已成為產﹑經及學術界共同之研究課題。本文將針對如何得到納米粉體研磨及如何將納米材料分散到其最終產品技術加以詳加探討。
基本介紹
- 中文名:納米研磨派勒集團
- 套用領域:電子產業﹑光電產業等
- 成就:得到納米級粉體
- 作者:雷立猛
基本介紹,引言,現況發展,原理,構造,設備來源,套用實例,結論建議,
基本介紹
作者: 雷立猛
(德國Puhler Group)
引言
筆者從事德國公司研磨機銷售業務數年,且已曾受邀在國內大專院校﹑工研院﹑中科院及國內外企業針對”新一代高效率納米研磨的現況及發展”主題演講,並已規划過數百多個案子,在國內已銷售數百廠實績。其主要套用領域可以1998年為區分點。1998 年以前,企業界所面臨的問題為如何提高分散研磨效率以降低勞力成本,如染料﹑塗料﹑油墨﹑…等產業。而1998 年以後,產業技術瓶頸則為如何得到微細化(納米化)材料及如何將納米化材料分散到最終產品里,如光電業TFTLCD﹑Jet ink﹑電子﹑磁性材料﹑醫藥﹑生物製藥和細胞破碎﹑氧化物﹑食品﹑…等行業。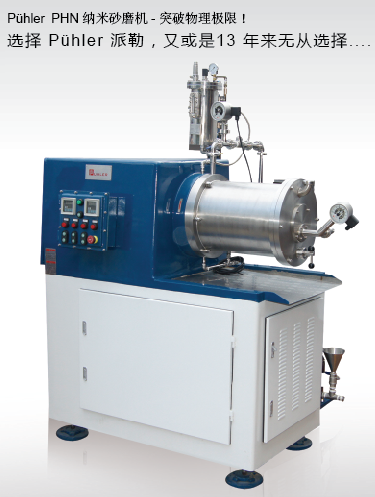
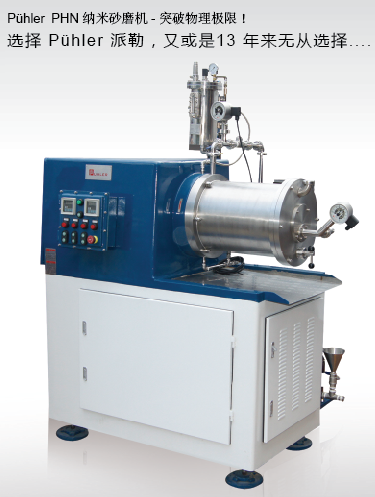
不論是傳統產業提升研磨效率求快或是高科技產業納米化材料求細需求,污染控制都同樣重要。所以細﹑快﹑更少污染已成為新一代分散研磨技術最重要之課題。
本文將針對納米級研磨的現況及發展﹑納米級分散研磨技術的原理﹑納米級研磨機的構造﹑現有設備的來源﹑套用實例及注意事項﹑結論及建議等六大主題加以探討。
現況發展
1) Bottom up ; Top down
隨著 3C 產品之輕、薄、短小化及納米材料套用之白熱化,如何將超微細研磨技術套用於納米材料之製作及分散研磨已成為當下重要課題。一般想得到納米粉體有2 個方法。一個為化學方法由下而上之製造方法(bottom up),如化學沈澱法,溶膠凝膠法(sol-gel),…。另一種方法則為物理方法,將粉體粒子由大變小(top down),如機械球磨法、化學法、物理法…等。
到目前為止,化學法或Bottom up 之納米粉體製造方法大部分在學術界被研究且已有豐碩的成果,可以得到數納米粉體。唯其製造成本有時相當高,且不易放大(scale up), 同時所得到粒徑分布亦較大。所以到目前為止,企業界仍以物理機械研磨(top down)方法以得到納米級粉體為主。Top down 方法較易得到粒徑分布較小納米粉體,同時生產成本相對較低,參數容易控制,將研發實驗機台所得到參數放大(scale up)到量產機台。唯Top down 方法只能研磨到30 nm,但已能滿足業界需求。
2) 乾法研磨(Dry grinding);濕法研磨(Wet grinding).
對納米粉體製造廠而言,當然希望以乾法研磨方法來得到最終納米粉體。但若以機械研磨方式研磨粉體時,在研磨過程中,粉體溫度將因大量能量導入而急速上升,且當顆粒微細化後,如何避免防爆問題產生等均是研磨機難以掌控的。所以一般而言,乾法研磨的粒徑只能研磨到8μm。如果要得到8μm以下粒徑,就必須使用濕式研磨。
所謂濕法研磨即先將納米粉體與適當溶劑混和,調製成適當材料。為了避免研磨過程中發生粉體凝聚現象,所以需加入適量助劑當助磨劑。若讀者希望最後納米級成品為粉體而非漿料,則需考量到如何先將漿料中之大顆粒粒子過濾及如何將過濾後之漿料乾燥以得到納米級之粉體。所以,當讀者以濕法研磨方式得到納米級粉體時,如何選擇適當的溶劑﹑助劑﹑過濾方法及乾燥方法將影響到是否能成功地得到納米級粉體關鍵技術。
3) 研磨(Grinding)?分散(Dispersing)?
顧名思義,研磨定義即是利用剪下力(shear force)﹑摩擦力或衝力(impactforce)將粉體由大顆粒研磨成小顆粒。分散定義為使納米粉體被其所添加溶劑﹑助劑﹑分散劑、樹脂﹑…等包覆住,以便達到顆粒完全被分離(separating)﹑潤濕(wetting)﹑分布(distributing)均勻及穩定(stabilization)目的。在做納米粉體分散或研磨時,因為粉體尺度由大變小的過程中,凡得瓦爾力及布朗運動現象逐漸明顯且重要。所以,如何選擇適當助劑以避免粉體再次凝聚及如何選擇適當的研磨機來控制研磨漿料溫度以降低或避免布朗運動影響,將成為濕法研磨分散方法能否成功地得到納米級粉體研磨及分散關鍵技術。
原理
承接上文,以機械方法的濕法研磨方式是得到納米級粉體最有效率且最合乎經濟效益方法。本文將針對濕式研磨及分散方法之原理及製程做一深入探討。為了方便說明,
本文將以圖(一)Puhler研磨機為例做一說明。
圖(一)納米級高速攪拌珠磨機範例

圖(一)研磨機為一密閉系統,在研磨機研磨室內放了適當材質大小的磨球(研磨介質;grinding media)。
磨球大小 | 最後um | 起始um | 黏度cps | 固成份 %(wt) | 濾網 間隙 mm |
0.3-0.4 mm | < 0.1 | < 20 | < 100 | < 35 | 0.15 |
0.4-0.6 mm | < 1 | < 40 | < 1000 | < 60 | 0.22 |
0.7-0.9 mm | < 2 | < 80 | < 2000 | < 70 | 0.3 |
0.9-1.1 mm | < 10 | < 150 | < 5000 | < 75 | 0.5 |
1.75-2.5 mm | < 20 | < 150 | < 100000 | < 83 | 0.6 |
圖(二)納米級高速攪拌珠磨機的原理示意圖, 其原理如圖(二)所示。
馬達利用皮帶傳動攪拌轉子將動力由磨球運動產生剪下力(shear force),漿料因Pump 推力至研磨室移動過程中與磨球因相對運動所產生剪下力而產生分散研磨效果。其粒徑小於研磨室內分離磨球與漿料之動態大流量分離器濾網間隙大小時,漿料將被離心力擠出至出料桶槽以便得到分散研磨效果。上述過程為研磨1 個pass,若尚未達到粒徑要求,則可以重複上述動作,通常大家稱之為進行循環研磨,…直到粒徑達到要求為止。
上述流程可以下列圖(三)之流程圖表示並加以探討說明如下:
圖(三)納米級高速攪拌珠磨機之操控流程
1)漿料前處理及預攪拌(Pre-mixing)

本系統能否成功地達到研磨或分散目的,主要靠研磨介質(即磨球)大小及材質之選擇是否得當。以筆者曾規劃及實際試車數百廠經驗,所選擇之磨球需為0.1-0.4 mm或以下。同時,為了讓那么小的磨球能夠在研磨過程中不受漿料於X 軸方向移動之推力影響而向前堵在濾網附近而導致研磨室因壓力太高因而停機,其攪拌轉子線速度需超過10 m/sec 以上。同時,漿料粘度控制調整到100 cps 以下,以便讓磨球運動不受漿料粘度影響。同時,漿料的固體成分(solid content by weight)也需控制在35%以下,以防止研磨過程中因粉體比表面積之增加而導致粘度上升而無法繼續使用小磨球。當然,為了避免0.3-0.4mm磨球從動態分離器流出研磨室或塞在濾網上,所以濾網間隙需調整到0.1 mm。
上述之關係可以整理成下列表(一)所示。
表(一)納米級高速攪拌珠磨機各種不同大小磨球之選擇參考法則
為了達到上述表(一)要求,於前處理或預攪拌時,需依下列法則準備研磨前之漿料,整理如下:
(1) 先決定所欲研磨之最後粒徑需求(target fineness)。
(2) 將漿料粘度(viscosity)﹑固含量﹑研磨前細度(start fineness)、(最終要求細度)Target之粒徑做準備並滿足表(一)需求。
(3) 預攪拌或前處理系統攪拌轉子轉速需為高線速度 (High speed) 設計。建議切線速度為2-13 m/sec 以避免漿料沈澱或不均勻問題產生。
2)研磨機部份
為了快速達到研磨粒徑要求且使研磨機可以正常地運轉,所需控制之法則及參數如下:
(1) 依照所需粒徑要求選擇適當的磨球。例如,若需達到納米級要求且避免磨球損耗,需選擇釔穩氧化鋯磨球,莫氏硬度越大越好,磨球表面需為真圓,沒有孔隙,磨球大小為0.05-0.4 mm。磨球選擇適
當與否將會決定能否成功地研磨到所欲達到粒徑要求。
(2) 依據磨球大小及漿料黏滯性調整適當的攪拌轉子轉速。一般納米級研磨,轉速需達12.5 m/sec 以上。
(3) 控制研磨漿料溫度。一般納米級漿料之研磨溫度需控制在45℃以下。影響到漿料溫度之主要參數為控制轉子轉速﹑磨球充填率﹑研磨桶熱交換面積大小﹑冷卻水條件及流量。
(4) 依據磨球大小選擇適當動態分離系統間隙。一般間隙為磨球直徑之1/2~1/3。
(5) 調整 Pump 轉速。在研磨桶可以接受壓力範圍內,Pump 的轉速越大越好。
如此,可以於同一研磨時間內增加漿料經過研磨機研磨次數以得到較窄粒徑分布。
(6) 記錄研磨機所需消耗之電能kW 值。
(7) 取樣時,記錄每個樣品之比能量(specific energy)值,並於分析該粒徑大小後,
將比能量與平均粒徑關係做出,以利將來Scale up 用。
(8) 達到所需比能量值時即可停機。此時,原則上已達到所需研磨分散平均粒徑要求了。
3)循環桶部分
一般要得到納米級粉體,均需利用研磨機研磨數十次,甚至上百次才可以達到納米級粉體。為了節
省人力及有利於自動化﹑無人化操作,筆者極力推薦使用循環式操作模式(recirculation operation
mode) 做納米級粉體研磨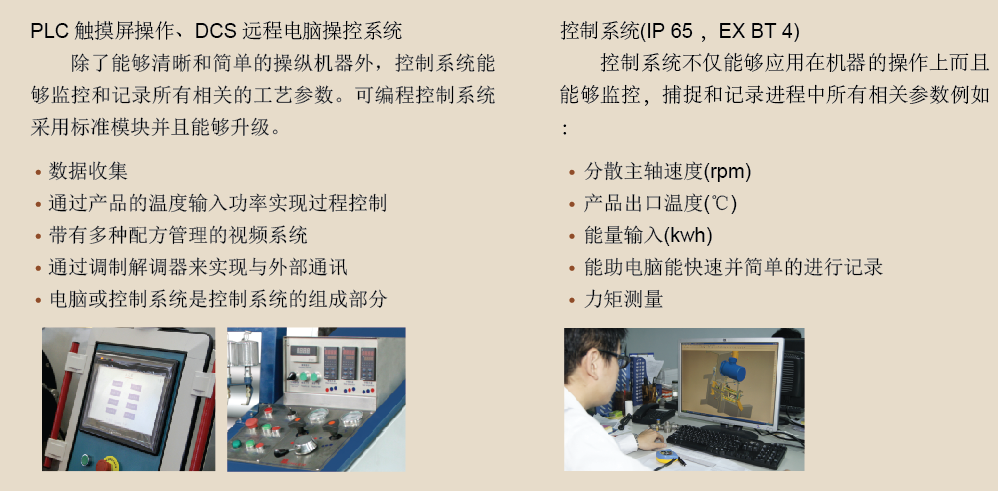
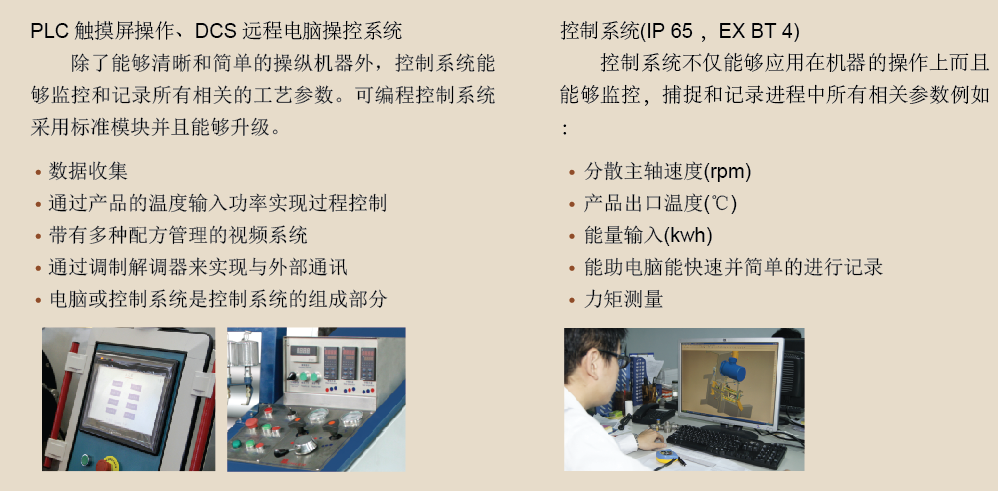
其主要之考慮重點如下:
(1) 循環桶的大小不宜太大。一般若研磨機對大流量為3000 l/hr 時,則移動缸最大容量為500 L。
一般循環桶大小為研磨機最大容許流量之1/5~1/10 為宜,越小越好。如此可以增加循環桶槽內漿料
於同一時間經過研磨機之研磨以得到較好之粒徑分布。
(2) 循環桶需有攪拌葉片設計,攪拌速度不宜過快,以0-3 m/sec 為宜以避免氣泡問題產生。
(3) 循環桶槽需有熱夾套層之設計以增加研磨效率。若欲有效率地得到納米級粉體分散研磨,
上述前處理,研磨機及循環桶各要素均需具備缺一不可。
4)決定平均粒徑(D50)之方法若漿料配方固定,研磨機操作條件亦固定條件下,平均粒徑將決定於
比能量(specific energy)值,比能量E 值定義如下:
E : 比能量,單位為kWh/t
P : 消耗電力,單位為kW
P0 : 無效的消耗電力,尚未加入磨球時,啟動研磨機消耗電力,單位為kW
m' : 流量,單位為ton/hr
Cm : 固成分,單位為%
由上可知,比能量之物理意義為每噸粉體每小時所消耗的電力。
如圖(四)所示,以研磨碳酸鈣為例,筆者改變了6 種不同的研磨機攪拌轉子的速度為(6.4-14.4m/sec),7 種不同流量,以X 軸為比能量,Y 軸為平均粒徑,由此圖可以得知,不論流量或攪拌軸速度在允許範圍內如何改變,只要比能量值固定,其研磨所得平均粒徑都將固定。所以,想讓產品品質重現,只要控制相同的比能量值,即可得到相同的平均粒徑值。
圖(四)研磨機消耗比能量與研磨所得漿料平均粒徑關係
5)磨球大小對研磨結果之影響
如圖(五)所示,不同磨球大小將影響所需之比能量值。由圖(五)可得知,當使用1.0-1.4 mm 磨球研磨碳酸鈣時,需320 kWh/t,才可達到粒徑D80 <2μm。但當比能量E 值達到96 kWh/t 後,改用0.6-0.8 mm 磨球繼續研磨,則只需要比能量180 kWh/t,即可達到相同粒徑D80 < 2μm。若漿料起始粒徑可以先處理的更小,例如20μm以下,則可以改用0.2-0.6 mm磨球研磨,相信達到D80 < 2μm所需之比能量值將再大大地縮小。由上述之研究及說明可以得知,磨球越小,則研磨效果越好,所需比能量值越小。
圖(五)研磨得到相同漿料粒徑要求時,使用不同磨球大小與其消耗比能量與關係
6)決定粒徑分布(Particle size distribution)方法
由圖(六)及圖(七)所示,可以得知,粒徑分布決定於Peclet number 大小,
Peclet number 越大,則粒徑分布越大,Peclet 定義如下:
Pe : peclet number
V : 軸向運動速度
l : 研磨室長度
D : 擴散係數
所以當漿料被Pump 打入研磨室後,當軸向的運動速度越快,同時於軸向分力越大,且當研磨室內漿料擴散係數越小時,則Peclet 值將越大,如此可得到較窄之粒徑分布。
實際套用時,若操作者於研磨過程中,可在研磨室壓力允許範圍內,儘量增加流量,如此可以提高Peclet number 值,以便得到較窄粒徑分布,
如圖(八)所示,Peclet number 值越大時,所得到粒徑分布將越窄。
圖(六)研磨漿料在研磨機內運動模式
圖(七)研磨漿料粒徑分布決定法則
圖(八)研磨漿料粒徑分布決定法則與Peclet Number 關係
構造
由前一章節可以得到,若想有效率地完成納米級粉體的分散研磨,大流量﹑小磨球已成為不可或缺之法則。因此,新一代納米級研磨機構造需能滿足”大流量﹑小磨球”設計法則。
以圖(九)示意圖為例,將重點報告如下:
圖(九)納米級超細珠磨機構造示意圖
1) 原則上當研磨室之體積越小,且產能越高時,就稱為較好研磨機。因可以降低漿料殘餘量以方便設備清洗。
2) 分離機構(即專利動態大流量分離器)間隙根據不同磨球大小而任意調整。不需卸下磨球及打開研磨機即可完成。同時,濾網面積越大則研磨機所能使用流量將越大,更能滿足”大流量﹑小磨球”原則。如圖(十)所示,濾網間隙需為磨球大小1/2~1/3。
置於空心攪拌軸內的
超大過流面積專利分離器
圖(十)納米級超細珠磨機分離機構示意圖
3) 研磨桶需有大面積熱夾套層設計,以利於將熱量帶走並控制良好研磨漿料溫度。
4) 研磨桶內,所有與漿料接觸部分材質需適當地選擇以避免污染問題產生。如金屬離子析出等問題,…
設備來源
因為納米級粉體研磨需使用小磨球﹑高轉速﹑高能量密度等,同時亦需避免污染產生,一般歐洲廠牌設備較適合。當然,若讀者已有國產或日制設備,則可以以現有設備做粗磨工藝,然後以歐洲設備做最後一階段超細納米研磨,達到”物盡其用”的最佳套用。
套用實例
上述原理及方法,筆者已有逾百廠實績,主要套用領域如下:
1) Color paste / Color filter / TFT LCD :
R﹑G﹑B﹑Y 及BM 已成功地分散研磨到納米級,透明度需超過90%,粘度控制在 5-15 CPS,
含水率在1%以下。
2) Ink-jet Inks:
顏料型Ink-jet Inks 已成功地分散研磨到納米級,粘度控制在5 CPS 以下。
3) CMP (chemical mechanical polish) slurry:
半導體晶片研磨所需之研磨液粒徑已達納米級且能滿足無金屬離子析出要求。
4) TiOPc (optical contact):
套用於雷射列表機光鼓上所塗布光導體,已研磨分散到納米級。
5) 納米級粉體研磨,如TiO2﹑ZrO2﹑Al2O3﹑ZnO﹑Clay﹑CaCo3﹑…,
可分散研磨到30 nm。
6) 納米級粉體分散。如將納米粉體分散到高分子,或將納米級粉體添加到塑膠﹑
橡膠等進行分散。
7) 醫藥達到納米級要求,且需能滿足FDA 要求。
8) 食品添加劑達到納米級之要求。如β胡蘿蔔素…,需滿足GMP 要求。
9) 電子化學品達到納米級需求,且需能滿足無金屬離子析出問題。
10) 其他。
結論建議
由上述可以得知”大流量﹑小磨球”為納米級粉體研磨主要依循法則。 若欲滿足細﹑快﹑更少污染﹑”納米級粉體研磨要求,需滿足下列條件:
1) 先認清研磨材料之特性要求。
2) 根據材料特性要求找到適當研磨機。
3) 搭配適當配套設備,如冰水機﹑壓縮空氣機、預攪拌機及移動物料桶﹑…等。
4) 找到合適產品的助劑。
5) 與上﹑下游有完善的溝通,以便調整最佳配方與研磨條件,提高納米粉體相容性。
參考文獻:
[1] Dr. S. Pilotek / Dr. F. Tabellion
Tailoring Nanoparticled for Coating Applications, 2005
[2] Mr. S. Schaer / Dr. F. Tabellion
Converting of Nanoparticles in Industrial Product Formulation :Unfolding the Innovation Potential, Tecchnical Proceedings of the
2005 NSTI Nanotechnology Conference and Trade show, Volume 2,P 743-746
[3] Dr. D. Bertram
Mr. H. Weller
Zerkleinerung und Materialtransport in einer Rührwerkskugelmühle.
1982. Ph. D.-Thesis, TU-Braunschweig
[4] Dr. H. Weit Phys,
Journal. 1 , 2002, Nr 2, P 47-52
[5] Dr. H. Schmidt / Dr. F. Tabellion
Nanoparticle Technology for Ceramics and Composites, 105th Annual
Meeting of The American Ceramic Society, Nashville, Tennessee,USA ( 2003)
[6] Dr. N. Stehr Residence. Time Distribution in a Stirred Ball Mill and their Effect on
Comminution. Chem.Eng.Process.,18 (1984) 73-83
作者簡介:
姓名: 雷立猛(1978年06月),性別:男
民族:漢,籍貫:湖南,學位:工學博士,
職務:銷售總監,
主要研究方向:納米粉體研磨,