形成原因
大尺寸箱形空間彎扭鋼結構構件的加工製做,截至2005年,中國國內外
鋼結構製做廠尚無成熟的經驗可借鑑,製做難度大。而隨著建築鋼結構施工技術的發展,越來越多的工程採用新穎獨特造型,構件截面形式也日趨向異型截面發展。因此,探索總結箱形空間彎扭構件的製做技術對於推動箱形空間彎扭構件在中國國內外建築鋼結構領域的套用具有積極的創新和推廣意義,同時從節約資源的角度上也符合中國的可持續發展國策。
《箱型空間彎扭鋼結構構件加工製作工法》是北京城建集團有限責任公司和浙江精工鋼結構有限公司結合
國家體育場鋼結構工程箱形空間彎扭構件製做綜合技術等研究成果,自行研製的箱形空間彎扭鋼構件的加工製做工法。
工法特點
與傳統鋼構件加工製做相比,《箱型空間彎扭鋼結構構件加工製作工法》的特點為:
首次將多點無模成形理論引入建築鋼結構加工製做領域,用數控模具取代傳統的整體模具;通過最佳化無模壓製成形的變形路徑、實時控制變形曲面,實現可隨意調整板材的變形路徑和受力狀態,從而擴大加工範圍;通過採用分段成形新技術,實現小設備成形大工件功能;解決傳統製做工藝難以解決的彎扭構件製做關鍵技術難題,並最大限度地降低生產成本、提高生產效率。
操作原理
適用範圍
《箱型空間彎扭鋼結構構件加工製作工法》主要適用於板厚在10~60毫米範圍內,材質為
Q345、Q345GJ鋼,截面尺寸不大於1350毫米×1350毫米箱形空間彎扭構件的工廠製做,對於其他截面形狀和強度等級的彎扭構件製做可以參照該工法執行。
工藝原理
《箱型空間彎扭鋼結構構件加工製作工法》的工藝原理敘述如下:
根據箱形空間彎扭構件由四塊空間彎扭的板件組裝焊接形成的原理,先將箱形空間彎扭構件離散成四塊空間彎扭的板件,採用多點無模成形技術將平板壓製成符合要求的四塊空間彎扭板件,然後將這四塊空間彎扭板件在胎架上組裝焊接形成箱形空間彎扭構件。
其中,彎扭板件多點無模成形原理則是將傳統的整體模具離散成一系列規則排列、高度可調的基本體(即沖頭),通過對各基本體運動的實時控制,自由地構造出成形面,實現板材的三維曲面成型。其成形過程如圖1。
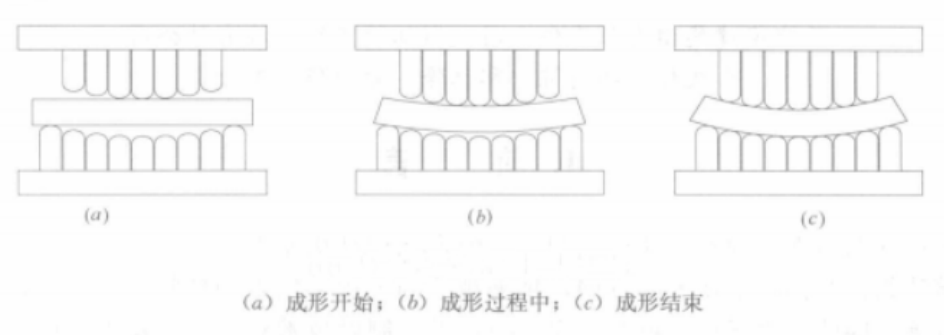
圖1 無模成形過程示意圖
施工工藝
《箱型空間彎扭鋼結構構件加工製作工法》的工藝流程如下:
箱形空間彎扭構件製做工藝流程如圖2所示,空間彎扭板件多點無模成形工藝流程如圖3所示。
《箱型空間彎扭鋼結構構件加工製作工法》的工藝操作關鍵點主要包括:彎扭板件的多點無模壓製成形和彎扭構件的組裝焊接,具體操作要點如下:
一、彎扭板件多點無模壓製成形
採用多點無模成形工藝進行空間彎扭板件的壓製成形時,主要涉及基本體(即沖頭)調平、工件加工、大型工件分段成形等內容,其操作要點如下:
1.基本體群調平
彎扭板件壓制前首先需要進行基本體調平,確定所有基本體的初始零點,並保證其在同一參考平面內。調平時,套用控制軟體的手動調形功能,將所有基本體的高度調整至較低數值,保證調平裝置的順利放入;然後選擇調平選項,逐行將上下基本體群中所有的基本體調整至同一高度,以此高度值作為參考面,確定其基準零點。
2.板件壓製成形工藝
板件壓製成形時,其主要的操作要點如下:
1)根據加工圖紙確定成形工件的尺寸,輸入工件上數條表征其空間三維形狀的曲線坐標值,軟體將自動生成其CAD模型。
2)根據板材厚度及材料參數確定回彈係數,人機互動確定工件的定位關係。
3)進行工藝計算,得到上下基本體群的型面數據,並進行成形工藝校驗。如果出現錯誤情況,返回第二步重新確定工藝參數,無誤後轉化為數控代碼。
4)進行系統自檢,通過匯流排將控制命令傳遞給各數控子系統,調整基本體群到設計的形狀。
5)在接送裝置的支撐下,將需要成形的板材定位,控制壓力機成形,得到需要的空間形狀。如果是分段成形,則需要多次調形、定位和成形,直到整張板材成形完畢。
3.大尺寸板件分段壓製成形工藝
對於大尺寸(板長方向)板件彎扭成形時採用分段壓製成形技術進行壓制。壓制時將彎扭板件的基本體成形面劃分為成形區域和過渡區域兩部分:對於成形區域板件按該文中板件壓製成形工藝將板件一次壓製成形;對於過渡區域板件採用NURBS曲面造型技術直接生成過渡區的形狀,先按照該文中板件壓製成形工藝將板件壓制過渡形狀然後移動板件,調整基本體成形面,將過渡區壓制到最終形狀。
採用分段壓製成形工藝可以實現大尺寸(板長方向)板件的連續壓製成形。
二、彎扭構件製做要點
組成箱形彎扭構件的四塊空間彎扭板件壓製成形後,即可在胎架上進行箱形空間彎扭構件的組裝、焊接工作,其操作要點如下:
1.胎架設定
裝配胎架採用可調式專用胎架,剛性平台要求平面度±2毫米;在平台上劃出各控制點的二維坐標,先在鋼平台上用洋沖標出彎扭構件的胎架定位點(如圖4所示),作出標記點後再設定胎架。
根據深化圖給定的坐標設定胎架,胎架間距不大於2000毫米,為便於操作最低的支架離地高度為800毫米,同時應考慮牛腿的安裝空間。如圖5所示。
2.U形組裝
1)放置下翼緣板
將噴有定位線的彎扭構件的下翼板置於胎架上(如圖6所示),調整板件與胎架的貼合度使其控制在2毫米內。

圖6 下翼緣板安裝放置示意圖
2)安裝隔板
下翼緣調整到位後定位內隔板。內隔板定位主要是通過下翼板上的噴粉線及內隔板上部的一端點來進行定位(隔板上部的一端點的投影點事先在鋼平台上已標出),在裝配時通過吊線垂及測標高來確定空間位置。如圖7所示。
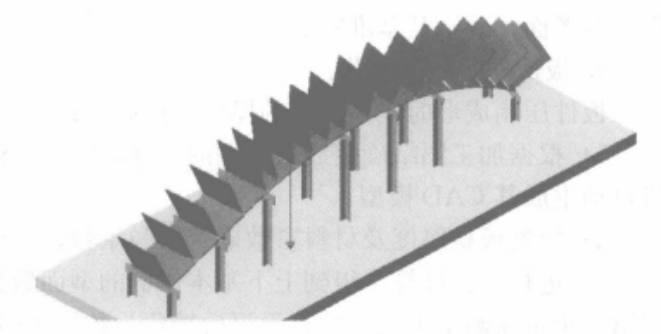
圖7 隔板安裝示意圖
3)安裝兩側腹板
兩腹板安裝以內隔板及下翼板作為定位基準,待各板件之間相互裝配貼合後進行定位焊,組裝時截面尺寸加4毫米的餘量(如圖8所示)。組裝定位焊從下翼板的中部開始向兩側進行,局部間隙採用花籃螺絲(板厚≤20毫米)或15000~30000千克的拉桿式液壓千斤調整或採用專用的裝配工具進行裝配(如圖9所示)。在下胎架前測量構件兩端頭洋沖點之間的相對距離,作為後道焊接工序中的焊接變形的跟蹤測量。
3.U形焊接
U形焊接主要是指隔板與下翼板焊接和隔板與兩側腹板焊接。焊接時分兩步進行,先是在胎架焊接完成1/3坡口焊縫,然後吊至焊接平台上焊接完成剩餘2/3坡口焊縫。
1)隔板與兩腹板焊接
隔板與兩腹板焊接時,整體焊接順序為由無餘量端向有餘量端進行,每塊隔板的焊接方法相同;隔板焊接時,焊縫2和焊縫4同時進行,自下而上跳焊焊接,跳焊間距為200毫米,焊縫焊接至坡口1/3,如圖10所示。
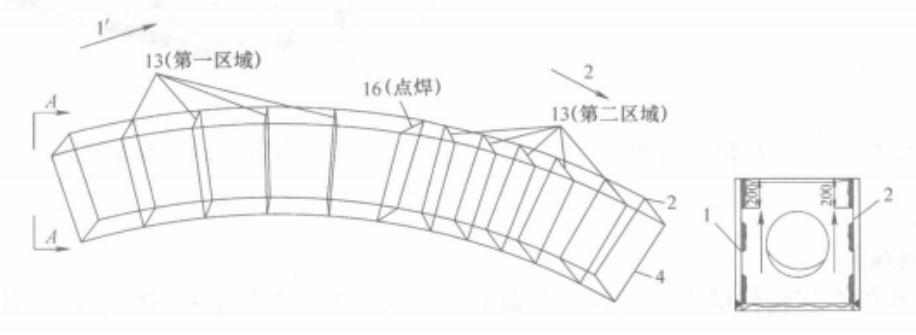
圖10 隔板與兩腹板焊接順序示意圖
2)隔板與下翼緣板焊接
隔板與下翼緣板焊接時,整體焊接順序為由構件中間向兩端進行,焊縫焊接至坡口1/3,如圖11所示。
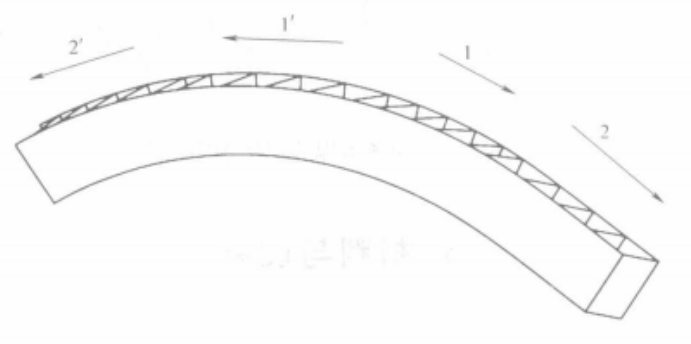
圖11 隔板與下翼板焊接順序示意圖
3)焊接平台上U形彎扭構件的焊接
隔板與兩腹板、下翼緣板焊縫焊接至坡口深度1/3後,將U形彎扭構件吊至焊接平台上繼續焊接。焊接前按圖12所示對U形彎扭構件進行剛性固定。焊接時,翻轉構件採用平角焊,隔板與兩側腹板按圖10的焊接順序焊接,隔板與翼板按圖11的焊接順序焊接。焊接過程中要對構件凹面的AC,BD(彎曲),AD,BC(扭曲)等尺寸進行測量;當AC或BD(彎曲)超過8毫米,應及時對構件翻身,焊接另一側的焊縫;當AD或BC(扭曲)超過15毫米,立即停止焊接進行火焰校正,並調整加強體的連線位置。

圖12 焊接過程剛性固定及焊接控制點示意圖
4.上翼緣板組裝焊接
1)U形組立彎扭構件焊接完成後,拆除其剛性固定裝置,對其成形質量進行檢查。AC或BD小於6毫米,且AD或BC小於10毫米時,可以進行上翼板的裝配,否則應通過火焰校正等措施使其滿足上述要求。
2)在裝配上翼板前應對U形彎扭構件在胎架上進行校正,要求彎扭構件兩頭與胎架的貼合度控制在2毫米內,其他部位貼合度控制在4毫米內。
3)在U形彎扭構件焊接完成並檢驗合格後裝配上翼板(如圖13所示),剛性固定後即可進行隔板與上翼板焊接,整體焊接順序為由構件中間向兩端進行,如圖11所示。
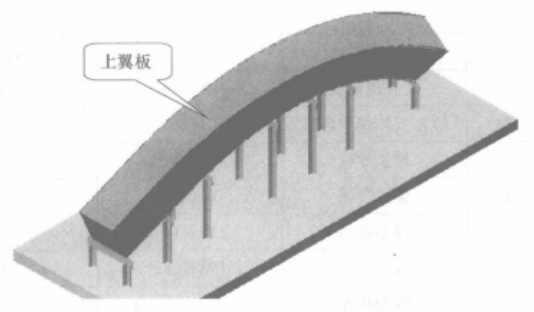
圖13 上翼緣板安裝示意圖
5.四條主焊縫焊接
四條主焊縫焊接時,要求兩條主焊縫同時焊接,即由兩名焊工先1、2後3、4對稱進行焊接;焊接過程中要對AC,BD(彎曲),AD,BC(扭曲)等尺寸進行測量,如圖14所示另外,四條主焊縫距兩連線埠各留100毫米左右不焊接,待預拼裝合格後焊接。

圖14 四條主焊縫焊接順序示意圖
材料設備
一、主要材料
《箱型空間彎扭鋼結構構件加工製作工法》涉及的材料主要是焊接材料及氧氣、乙炔等輔助材料;焊接材料的規格、型號由焊接工藝評定結果確定;氧氣、乙炔等輔助材料的選用則根據烤槍、割槍等設備的型號確定,不再贅述。
二、主要設備
《箱型空間彎扭鋼結構構件加工製作工法》需要的主要機具如表1。
| | | | | |
| | | | | 1.該工法所列設備機具數量系按"一個作業面、三班倒"原則配備;2.主要機具型號、數量,使用時應結合施工單位設備情況及工程量靈活採用;3.在使用電加熱器對鋼構件進行整體或局部熱處理時,需要配有專門的溫度控制箱來實現熱處理工藝中的升溫、降溫、恆溫等溫度和時間的控制。 |
| | | | |
| | | | |
| | | | |
| | | | |
| | | | |
| | | | |
| | | | |
| | | | |
| | | | |
| | | | |
| | | | |
| | | | |
| | | | |
| | | | |
| | | | |
| | | | |
| | | | |
| | | | |
| | | | |
| | | | |
| | | | |
| | | | |
| | | | |
質量控制
一、應執行的標準規範
《箱型空間彎扭鋼結構構件加工製作工法》應執行的主要標準規範有《國家體育場鋼結構施工質量驗收標準》JQB-046-2005、《鋼結構施工質量驗收標準》GB 50205-2001、《建築鋼結構焊接技術規程》JGJ 81-2002、《低合金高強度結構鋼》GB/T1591-1994和《建築結構用鋼板》GB/T 19879-2005等。
二、質量要求
《箱型空間彎扭鋼結構構件加工製作工法》施工時,當設計檔案無明確要求時箱形空間彎扭構件的成形質量按照表2的要求進行質量控制。彎扭構件的焊縫質量要求按照國家標準的有關要求執行。
| | | |
| | | |
| | |
| |
| | |
| |
| |
| |
| | |
|
|
|
| △≤0.05t 且△≤1.0(平滑過渡) (t為最薄的面板厚度) | | |
|
|
|
| | | |
| | | |
安全措施
採用《箱型空間彎扭鋼結構構件加工製作工法》施工時,除應執行國家、地方的各項安全施工的規定外,尚應遵守注意下列事項:
一、管理制度
1.加強安全教育,使焊接操作人員牢固樹立“安全第一、預防為主”的思想,認識到安全生產、文明施工的重要性,嚴格執行安全生產三級教育。
2.嚴格執行現場安全生產有關管理制度,建立獎罰措施,並定期檢查考核。
3.根據工程特點編制焊接操作規程和作業人員崗位職責,確保分工明確、責任到人。
二、技術安全措施
1.加強操作人員的安全教育培訓工作開工前做好安全交底工作,並形成書面交底記錄;每天認真開展好班前安全教育活動,確保每個操作人員對安全防護工作做到心中有數。
2.彎扭板件壓制過程中,操作人員應嚴格按照無模壓製成形的安全操作規程進行板件的計算機調形、傳動機構的傳輸及壓制等工序。
3.彎扭構件的胎架組裝過程中應嚴格按照國家規範或標準的有關安全管理規定執行,不得進行野蠻施工。
4.彎扭構件胎架上焊接施工時,應嚴格執行國家規範或標準關於焊接施工安全的有關規定。
環保措施
《箱型空間彎扭鋼結構構件加工製作工法》的環保措施主要從污染源的控制、傳播途徑治理、個人防護和環保教育等四方面進行。
一、污染源控制
1.焊接方法選擇時,焊接條件允許的前提下優先選用自動化程度高的焊接方法進行焊接;選用低塵低毒性焊接材料,以降低電焊煙塵的濃度和毒性;改善焊工的作業條件,減少電焊煙塵污染。
2.選擇合理的切割、矯正設備,控制加工製做過程的噪聲到合理的範圍。
3.加強對無模成型設備的維護、保養及管理,避免其對壓制鋼板造成二次污染。
二、傳播途徑治理
1.改善作業場所的通風條件,當封閉或半封閉結構施工時必須有機械通風措施。
2.車間焊接時,通過在牆體表面採用吸聲、吸收材料進行裝飾等措施,降低加工場所的噪聲,減少焊接弧光的反射,加強對操作者的保護。
3.焊接時保證工件接地良好,控制做業場的溫、濕度,控制焊接時電磁輻射對操作者的傷害。
三、個人防護
對作業人員配備必須的個人防護用品,若在封閉或半封閉機構內工作時,還需佩戴使用送風面罩。
四、強化職業衛生宣傳教育及現場跟蹤監測工作
對作業人員應進行必要的職業安全衛生知識教育,提高其職業衛生意識,降低職業病發病率。同時,還應對焊接作業場所的塵毒危害進行定期監測,對作業人員定期進行體檢,以便及時發現問題,預防和控制職業病。
效益分析
一、經濟效益分析
由於《箱型空間彎扭鋼結構構件加工製作工法》的關鍵技術為新開發的技術,因此在進行經濟效益分析時主要與傳統技術方案(即傳統模具工藝和傳統火工彎板工藝)進行生產成本費用比較。
傳統模具工藝、傳統火工彎板工藝及該工法各項成本費用支出如表3所示。
以國家體育場鋼結構工程為例,採用該工法加工的箱形彎扭構件約2000根,總用量約6000噸,則該工程由於採用該工法其生產成本費用節約如下,材料攤銷係數取0.4。
相對於傳統模具工藝:[(500+1.5×2000×4)-(500+350)]×(1-0.4)=6990(萬元),
相對於傳統火工彎板工藝:{[(1+0.15+0.072)×2000×4]-(500+350)}×(1-0.4)=5355.6(萬元)。
二、環保節能效益分析
《箱型空間彎扭鋼結構構件加工製作工法》的環保節能效益是明顯的,各項環保節能指標同表3。
以國家體育場鋼結構工程為例,採用該工法加工的箱形彎扭構件總計2000根,總用量約6000噸,則該工程由於採用該工法導致能源節約如下,其中材料攤銷係數取0.4。
相對於傳統模具工藝:
節約模具:2000×4=8000(套),
成本節約:1.5萬元/套×8000套×(1-0.4)=7200(萬元),
相對於傳統火工彎板工藝:
節約彎支胎架:1萬元/套×(2000×4)套=8000(萬元),
節約能源消耗:0.15萬元/套×8000套=1200(萬元),
總成本節約:(8000萬元+2400萬元)×(1-0.4)=6240(萬元)。
三、社會效益分析
《箱型空間彎扭鋼結構構件加工製作工法》的社會效益是明顯的,主要表現為:建築鋼結構工程大量採用大尺寸箱形空間彎扭構件高效優質成形與製做工藝,保證了國家體育場鋼結構工程的順利進行,並為2005年後國家有關規範標準相關內容的修訂奠定了基礎。
另外,《箱型空間彎扭鋼結構構件加工製作工法》內容從節約資源角度符合中國的可持續發展戰略,有利於推進能源與建築結合配套技術研發、集成和規模化套用。
註:施工費用以2005-2006年施工材料價格計算
套用實例
《箱型空間彎扭鋼結構構件加工製作工法》的套用實例如下:
截至2005年,中國國內外建築鋼結構工程僅有國家體育場鋼結構工程大量採用了大尺寸箱形空間彎扭構件。
國家體育場工程為北京“2008”奧運會主會場,其鋼結構工程為了編織“鳥巢”的特殊建築造型,設計時在鋼屋蓋與立面相交部位(即肩部)全部採用了箱形空間彎扭構件,其截面尺寸基本為1200毫米×1200毫米,鋼板材質涉及Q34C、Q345D、Q345GJD、板厚涉及10~60毫米,總用鋼量12000噸。圖15為國家體育場鋼結構工程全貌,圖16為典型彎扭構件實物圖片。
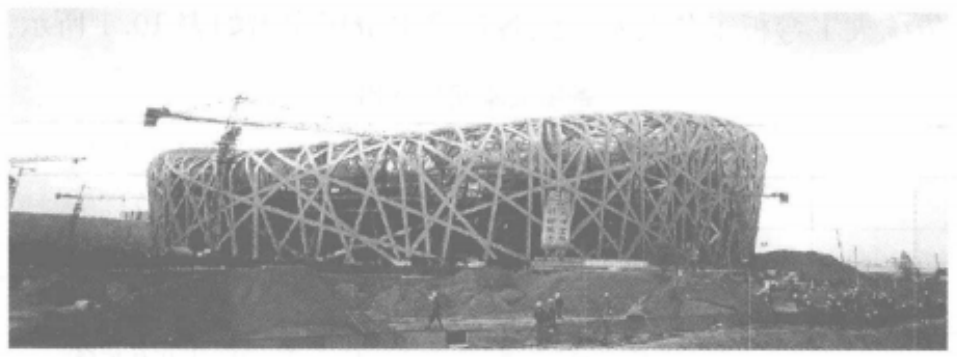
圖15 國家體育場鋼結構工程全貌

圖16 典型彎扭構件實物圖片
在進行彎扭構件製做施工時,按照該工法規定的加工工藝、操作要點及質量標準等進行製做施工,歷時四個月完成全部加工任務,彎扭構件成形及焊縫質量自檢及第三方檢查合格率100%,對保證國家體育場鋼結構工程總體進度和工程質量具有意義。
榮譽表彰
2008年1月31日,中華人民共和國住房和城鄉建設部以“建質[2008]22號”檔案發布《關於公布2005-2006年度國家級工法的通知》,《箱型空間彎扭鋼結構構件加工製作工法》被評定為2005-2006年度國家二級工法。