基本介紹
- 中文名:硬頭
- 外文名:hardhead
- 含義:煉富渣的一種產物
- 套用:煉錫工業
硬頭的生成機理和成分
鐵在錫中的溶解及硬頭的生成
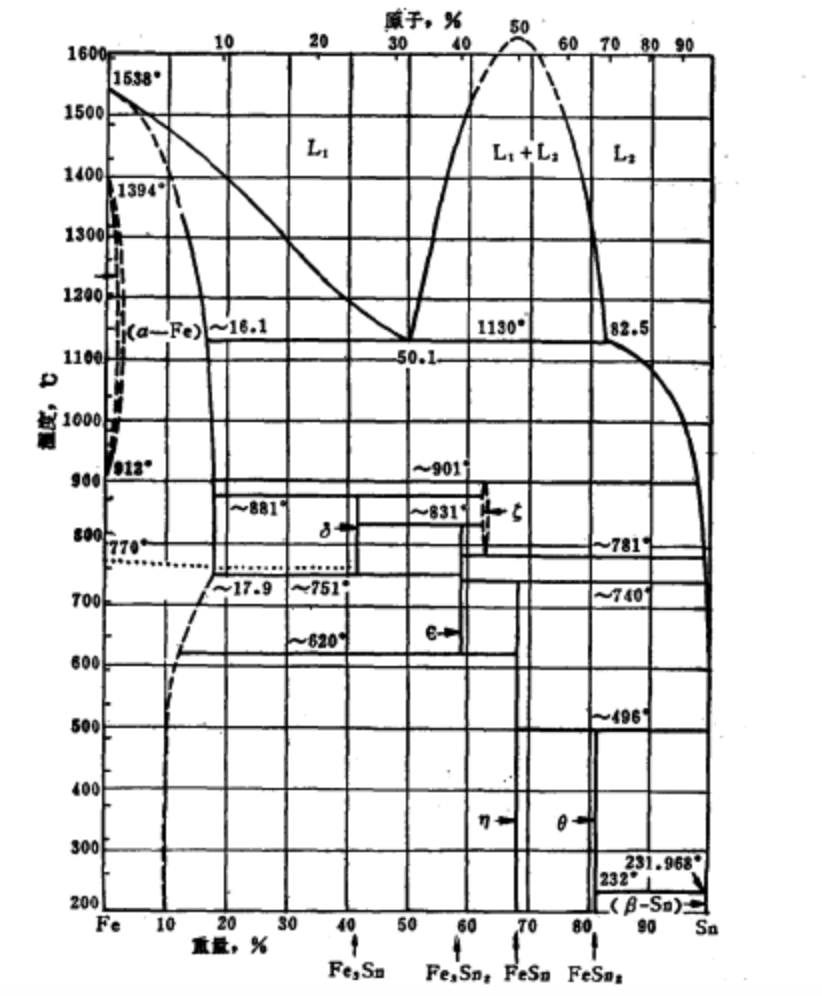

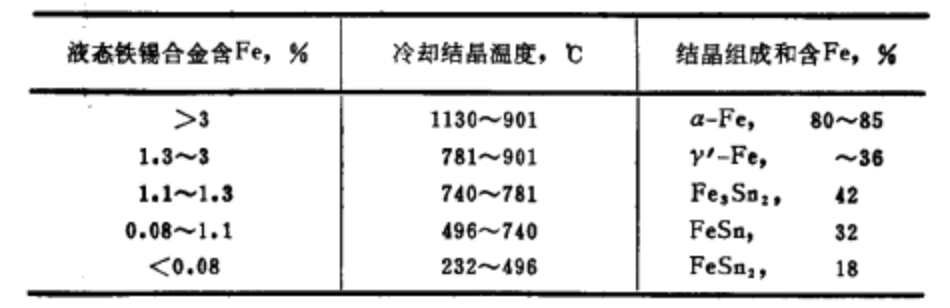
硬頭的處理
煙化法處理硬頭
- 硬頭中的砷絕大部分與錫一道揮發進入煙塵,使煙塵變得不純,這些煙塵重新返回還原熔煉時,砷又溶解進入粗錫,促使硬頭的產生。
- 硬頭的密度大,控制不好易沉入爐底,形成爐底爐結,另由於硬頭中含砷、錫、鐵量均較高,在作業過程中對爐底水箱有一定的腐蝕性。
矽鐵法處理硬頭
加熱熔析法
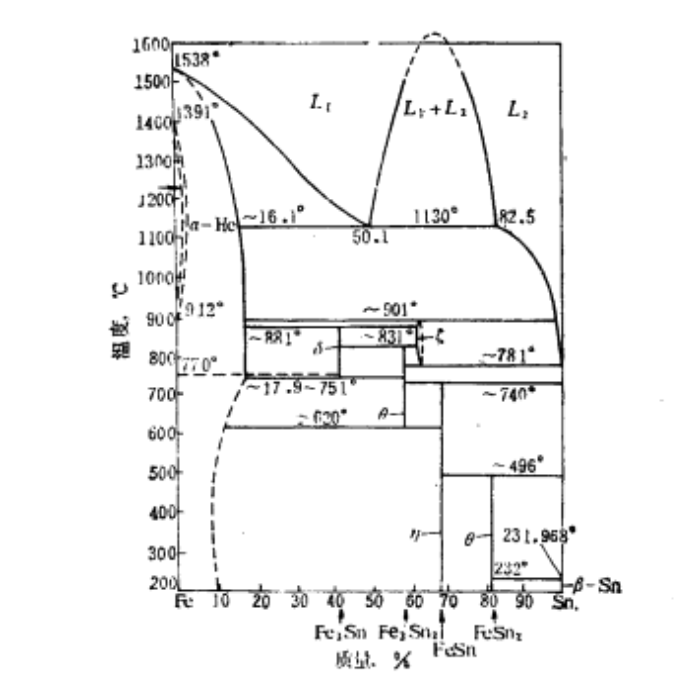
硬頭是煉富渣的產物,其成分主要為錫與鐵,有的含砷較多。對硬頭的處理曾有人作過氯化法和汞齊法的試驗,有的工廠則將硬頭熔化後水淬成粒進行氧化焙燒脫砷,再...
硬頭黃竹(學名:Bambusa rigida Keng et Keng f.)是禾本科簕竹屬植物,竿高5-12米,直徑2-6厘米,尾梢略彎拱,下部勁直;節間長30-45厘米,無毛,幼時薄被...
硬頭鱒(steelhead, salmon gairdneri)與大麻哈魚、缸鱒魚同屬鮭鱒魚類。原產於美國阿拉斯加的kuskokwin河和加拿大不列顛哥倫比亞省的和平河等水域。由於基因工程的...
硬頭青,剛竹屬植物。稈高4~6m,徑3cm,新稈深綠色,無毛,密布白粉;稈環隆起比籜環顯著。稈籜早落,半革質,灰綠色或灰黃綠色,具明顯紫色條紋,微被白粉,上部...
硬頭錘號稱“單手鈍器之王”,是釘頭錘的一種,是中世紀鼎盛時期最為優秀的冷兵器之一。...
硬頭苦竹,被子植物,竿高3—4米,竿壁較薄,髓豐滿,棉絮狀,新竿綠色,密被不均勻的針點狀紫色和白粉,老竿暗綠色;籜鞘薄革質,宿存,長約為節間的1/2,綠色,...
硬頭青竹是產於湖北西部及四川的一種竹子,竿高3-5米,粗1-2.5厘米,幼竿被白粉並疏生短柔毛;節間一般長20-22厘米,壁厚3-5毫米;節處隆起,竿環高於籜環。...
硬頭海鮎,Arius leiotetocephalus (Bleeker, 1846),海鯰科海鮎屬的一種魚類。背鰭短,具一銳利的硬棘,腹鰭腹位,有6鰭條,臀鰭條14-16。尾鰭深叉形,頭錐形或...
硬頭獅子是一種傳統民俗舞蹈。龍游縣民眾慣稱“硬殼獅子”,目前分布在我縣湖鎮鎮的星光、星火、下葉、上溪頭、竺溪橋、夏家、後陳、下童八個村莊,僅存10對。...
竹海硬頭黃是禾本科、簕竹屬的植物。...... 參考資料 1. 竹海硬頭黃 .國際竹類栽培品種登錄中心(ICRCB)[引用日期2017-06-29] V百科往期回顧 詞條統計 瀏覽...
”撐硬頭船“,諺語,意思是指逆水行船,比喻辦法、態度生硬。...... ”撐硬頭船“,諺語,意思是指逆水行船,比喻辦法、態度生硬。中文名 撐硬頭船 類別 諺語 ...
「猛禽究極硬頭錘」是遊戲王卡片中的一張裝備魔法卡。隸屬於「急襲猛禽」卡組。...... 「猛禽究極硬頭錘」是遊戲王卡片中的一張裝備魔法卡。 隸屬於「急襲猛禽...
護照信息平台資源號:1111C0003301000059 資源編號:301134294080059 種質名稱:黃山庫-硬頭青竹 原產地:不詳 省:湖北 來源地:浙江安吉 歸類編碼:11131500000 資源類型:...
硬頭獅子是一種古老的傳統民俗舞蹈。湖鎮地區民眾慣稱硬殼獅子,用狗樹或樟樹雕成的獅頭,張著血盆大口,五短身材,披一身又厚又長的青蘭色獅毛,威風凜凜,雙開...
硬頭浪簡介 編輯 編號:7562拉丁目名:PERCIFORMES中文目名:鱸形目中文科名:鯻科拉丁科名:Theraponidae中文屬名:鯻屬拉丁屬名:Therapon...
雲錫將含錫30%以下的硬頭,部分地加人煙化爐中和富渣一起硫化揮發處理,硬頭中鐵成為氧化物人渣,錫以SnS的形態揮發。操作時,當煙化爐中爐料全部熔化後開始加硬...
懲戒之神聖·庫斯伯特有著變化多端的外貌。他通常化裝成一個普通的鄉下人,或是一位白髮白須,穿著全身甲的男人。他通常都帶著他著名的硬頭錘。聖·庫斯伯特以...
書寫壓痕是用原子筆、鋼筆、鉛筆等硬頭筆書寫時,由於筆壓作用,在下墊紙頁上形成的無色字跡壓 痕。用壓痕靜電顯現儀或在側光下觀察、拍照可以辨讀其書寫內容;...
頭帽箱是用來存放軟、硬頭帽及髮髻、口條(即髯口)等戲曲道具用具的箱櫃。...... 頭帽箱是用來存放軟、硬頭帽及髮髻、口條(即髯口)等戲曲道具用具的箱櫃。...