甲醇蒸汽轉化制氫和二氧化碳技術。
簡介
前言
工藝原理及其特點
工藝技術特點
工藝過程
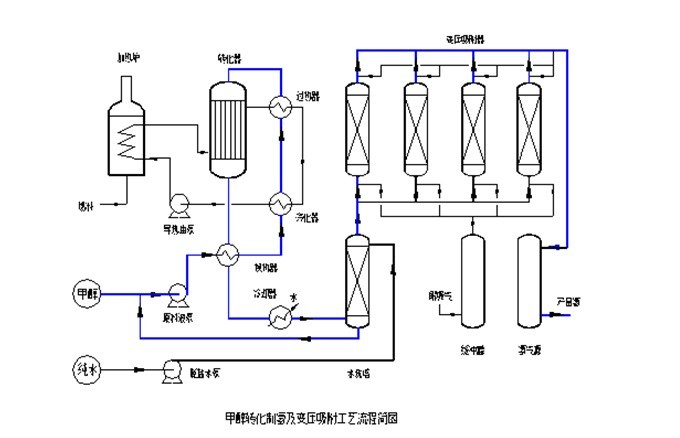
甲醇蒸汽轉化制氫和二氧化碳技術。
甲醇蒸汽轉化制氫和二氧化碳技術。...... 甲醇裂解制氫工藝技術特點 編輯 1.甲醇蒸汽在專用催化劑上裂解和轉化一步完成。2.採用加壓操作,產生的轉化氣不需要進一步加...
甲醇裂解裂解制氫工藝原理 編輯 作用下,甲醇和水發生裂解變換反應。轉化為~75%H2和~24%CO2、極少量的CO、CH4。轉化汽經過換熱、冷凝、淨化,自動程式控制讓將未...
6.1.3甲醇水蒸氣重整反應動力學研究 6.1.4甲醇水蒸氣重整反應催化劑 6.1.5甲醇水蒸氣重整制氫工藝流程 6.2甲醇裂解制氫 6.2.1甲醇裂解制氫反應機理 ...
氫氣是蒽醌法生產過氧化氫的主要原料,其來源廣泛,主要有電解水制氫、合成氨弛放氣或原料氣制氫、氯鹼或氯酸鹽工業副產氫、天然氣水蒸氣轉化制氫和甲醇裂解制氫等。...
2 4甲醇燃料套用1642 4 1甲醇汽油混合或純甲醇燃料1652 4 2甲醇燃料電池1792 4 3甲醇裂解制氫燃料2052 4 4甲醇脫水轉化為二甲醚燃料208...
該法運行成本較甲醇裂解制氫高。NH3 = N2 + 3/2 H2HyCOElectrolyzer (水電解) 用水作原料通過電解製取氫。在用氫量較小(<100 Nm3/h),對氫氣純度要求較高(...
公司有成熟的技術包括:甲醇裂解制氫、天然氣制氫、煤制氫、酒精脫水制無水乙醇、變壓吸附氣體分離提純、國際飲料級食品二氧化碳的製備、氨碳分離、PSA尾氣回收等。 ...
程控閥是一種通過氣動、液動等方式驅動的切斷閥。該閥與DCS集散控制系統或PLC相連,實現電腦程式的遠程控制。廣泛套用於甲醇裂解制氫、酒精幹燥、氯乙烯濃縮回收、...
四川亞聯高科技有限責任公司工業氣體技術轉讓以及成套裝置設備工程。如甲醇裂解制氫、天然氣制氫、酒精脫水等。十多年的發展歷程創建於96年,是一家集工程諮詢、工程...
甲醇制二甲醚生產技術;4.甲醇裂解制氫、氨裂解制氫及甲烷轉化制氫技術;5.甲醇及其下游產品生產技術;5.一氧化碳羰基化制甲酸甲酯技術;6.甲醯胺、二甲基甲醯胺一、...
研究領域:主要研究船舶動力的新能源開發、套用、環保節能等,涉及重油智慧型乳化控制、甲醇裂解制氫、雙燃料等。研究成果:申請實用新型專利1項,獲省級教學成果一等獎2項,...
(LNG)技術;天然氣制氫技術、乾氣制氫技術、甲醇裂解制氫技術;汽柴油加氫精制技術、柴油加氫改質技術、蠟油加氫技術、煤焦油加氫技術;催化汽油選擇性加氫技術、氣體...
(48) Pd催化甲醇裂解制氫的反應機理,排名:1,物理化學學報ISSN 1000-6818,2009-05-01(49) 鎂鋁水滑石及其改性產物的表面性質的研究,排名:3,無機化學學報ISSN ...
碳一所主要研究開發的成果有低壓合成甲醇工藝及其催化劑、甲醇脫水合成二甲醚工藝及催化劑、羰基化法合成碳酸二甲酯(DMC)、甲醇裂解制氫工藝及催化劑等二十餘項,是...
具有自產1000Nm3/h純度99.99%以上的甲醇裂解制氫能力,及總容積為 32550L、單釜容積500L~3000L、最高壓力15MPa、最高溫度250℃的高壓氫化裝置,是國內高中壓液相...
高新技術轉讓主要有:甲醇羰基合成醋酸、甲醇脫水制二甲醚、甲醇裂解制氫、工業排放氣淨化與綜合利用(焦爐氣甲烷化制天然氣、合成氣制乙二醇、電石爐尾氣淨化提純、煤層...
碳一所主要研究開發的成果有低壓合成甲醇工藝及其催化劑、甲醇脫水合成二甲醚工藝及催化劑、羰基化法合成碳酸二甲酯(DMC)、甲醇裂解制氫工藝及催化劑等二十餘項,是...