滴注成型是一種新型的模具生產工藝,相比於傳統的注塑成型具有成型效果好、成型時間短、能耗低、模具的尺寸大幅度降低的優點。
基本介紹
- 中文名:滴注成型
- 外文名:Drip molding
注塑成型,工藝,優點,
注塑成型
注射成型過程大致可分為以下6個階段 :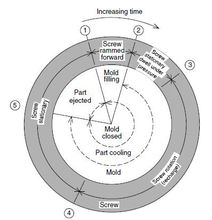
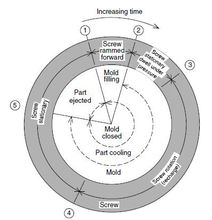
注射成型過程分為6個階段
上述工藝反覆進行,就可批量周期性生產出製品。
成型周期:成型周期直接影響勞動生產率和設備利用率。因此,在生產過程中,應在保證質量的前提下,儘量縮短成型周期中各個有關時間。在整個成型周期中,以注射時間和冷卻時間最重要,它們對製品的質量均有決定性的影響。注射時間中的充模時間直接反比於充模速率,生產中充模時間一般約為3-5秒。注射時間中的保壓時間就是對型腔內塑膠的壓力時間,在整個注射時間內所占的比例較大,一般約為20-120秒(特厚製件可高達5~10分鐘)。在澆口處熔料封凍之前,保壓時間的多少,對製品尺寸準確性有影響,若在以後,則無影響。保壓時間也有最惠值,已知它依賴於料溫,模溫以及主流道和澆口的大小。如果主流道和澆口的尺寸以及工藝條件都是正常的,通常即以得出製品收縮率波動範圍最小的壓力值為準。冷卻時間主要決定於製品的厚度,塑膠的熱性能和結晶性能,以及模具溫等。冷卻時間的終點,應以保證製品脫模時不引起變動為原則,冷卻時間性一般約在30~120秒鐘之間,冷卻時間過長沒有必要,不僅降低生產效率,對複雜製件還將造成脫模困難,強行脫模時甚至會產生脫模應力。成型周期中的其它時間則與生產過程是否連續化和自動化以及連續化和自動化的程度等有關。
工藝
採用開放式模具,迴轉式方式。
大致分為以下步驟
1.噴料(定量定型) 2,成型(冷模) 3,冷卻 4,製品取出
每個步驟又是連續重複的,又是同時進行的。
所以大大提高傳統注塑的效率,注塑一般最少的成型周期需要20秒到10分鐘
滴注成型的的成型時間只需要1.8秒到50秒,主要得益於,小巧的開放式模具,充分冷卻的成型時間。
熱熔塑膠分子承受的力直接來自於上模的壓力,成型效果很好,冷卻更加充分。
由於是定量噴料,整個過程沒有廢料,更加高效節能。
如果是相同模血的情況下 滴注成型的速度是注塑成型的10倍。
優點
1.成型效果好。
採用直接施壓的方法,熱塑體可以被擠入各種細微的空間,不用考慮流道,可以成型非常複雜的產品,而且保證沒有氣孔沒有空腔。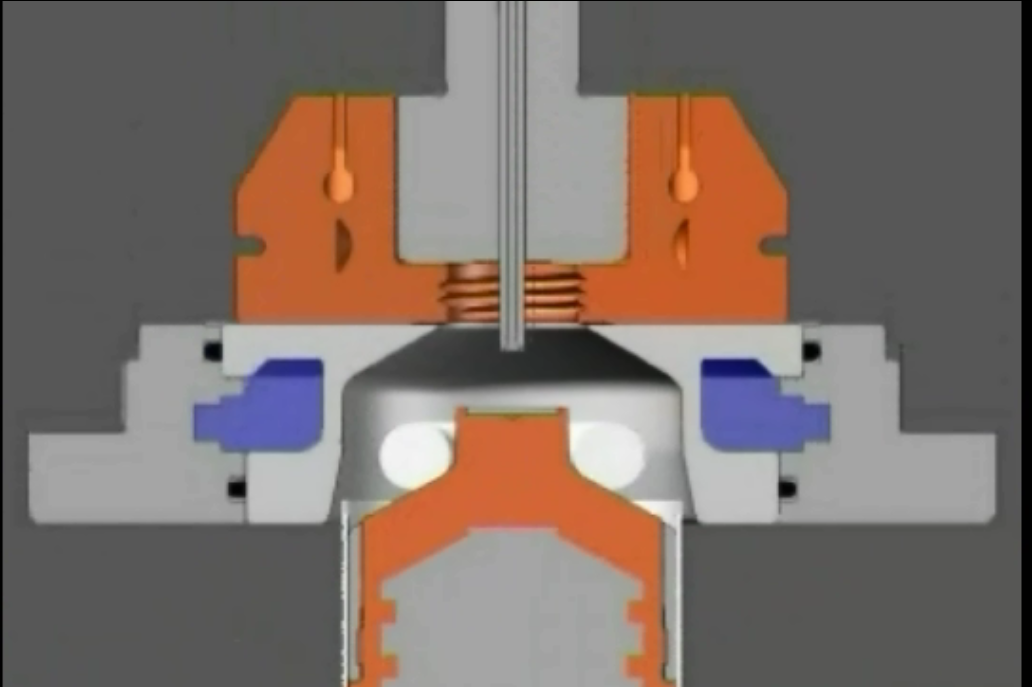
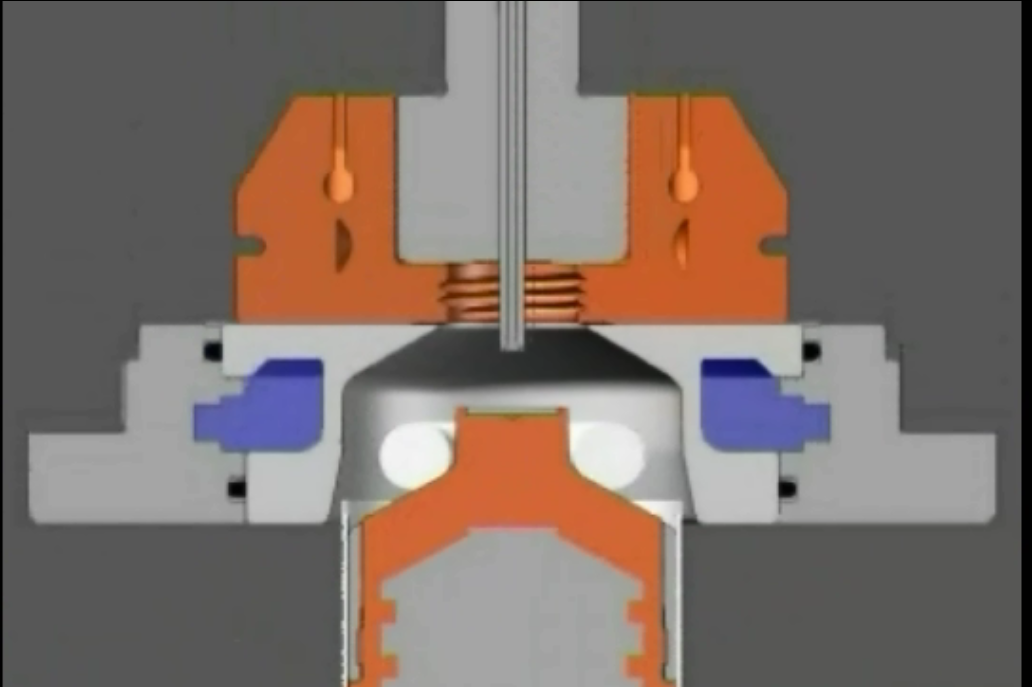
滴注成型製作示意圖
2. 成型時間短
完全改變傳統的,合模、射膠、保壓、冷卻、開模的整個流程。
採用開放式連續迴轉模具,每個動作都是同時獨立進行。生產速度大幅度提高。
3 :傳統 的注塑一般為液壓或者伺服液壓作為動力源。
而滴注成型由於壓力直接作用於塑膠分子,可以採用氣動,氣液複合,伺服作為動力源,能耗大大降低。
舉例 40T的小型注塑機,需要功率7.5kw。
相同效率的滴注成型機,只需要3kw。 能耗大幅度降低。
4: 模具的尺寸大小 大幅度降低
相同的尺寸模具比如50型模具,注塑機的模具重量700kg
滴注成型機的模具重量為50kg,更換模具和開發模具的成本效率提高數倍。