液滴分離器是用於分離氣流中夾帶的液滴的平行設定的分離器。主要用於治理冶金行業中鋼板鋁板冷軋過和產生的油霧,套用先進的機械分離技術及靜電沉積技術。常見為旋風分離器。
基本介紹
- 中文名:液滴分離器
- 實質:平行設定的分離器
- 常見:旋風分離器
- 用於:冶金工業
旋風分離器簡介,工藝流程,相關數據,旋風分離器結構改進的研究現狀,
旋風分離器簡介
工藝流程
有關此旋風分離器的工藝系統流程圖如圖1。
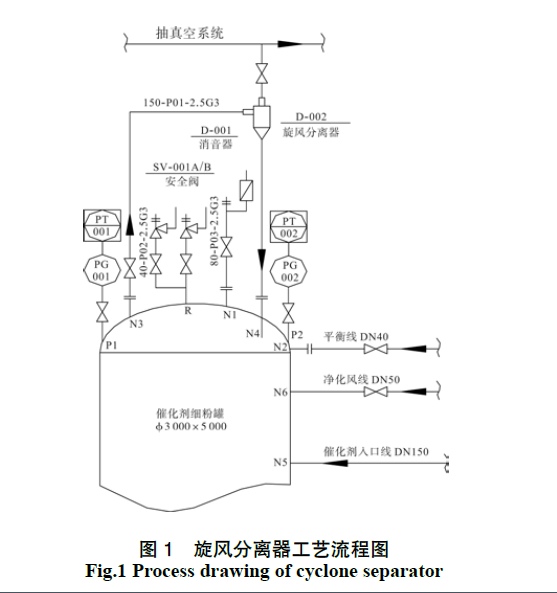
在流程圖中,D-002 即為新增的旋風分離器。
相關數據
細粉罐操作壓力:0.07MPa(負壓);
細粉罐操作溫度:常溫~475℃;
旋風分離器入口空氣(含催化劑)流量:594m3/h。
旋風分離器結構改進的研究現狀
旋風分離器套用於工業生產以來,已有百餘年的歷史,對於捕集、分離5~10μm以上的顆粒效率較高。由於能耗相對比較小,結構簡單可靠,廣泛地套用於冶金、化工、石油、建築、機械、電力、輕紡、食品等工業部門。旋風分離器中顆粒分離的機理是:顆粒由於離心力的作用克服氣流的阻力向壁面運動,到達壁面附近後,由於邊界層內較小的湍流,顆粒會沿著壁面進入灰斗中,從而得到分離。對於微細顆粒(粒徑小於5μm),由於其所受到的離心力小於氣流對其的阻力,因此,一般來說,這一類顆粒很難得到分離。隨著工業裝置生產規模的提高以及操作條件變得更為苛刻,對旋風分離器性能的要求也不斷提高。一方面要求旋風分離器有更強的捕集細粉的能力;另一方面要求旋風分離器的壓降進一步減少,以降低能耗。所以,迫切需要研究出高效能且低能耗的新型旋風分離器。而通常是採用有針對性地開發新結構或最佳化各部分尺寸的匹配關係的方法來減少不利因素的影響,以達到高效的目的。
1、旋風分離器進口結構的研究現狀
普通旋風分離器單體大多採用了單切向進口或蝸向的進口結構形式,氣固兩相流進入旋風分離器後,隨著遠離旋風分離器排氣芯管入口截面,平衡塵粒逐漸減小,即空間點上顆粒分離能力逐漸增強。因此,最佳化改進位於旋風分離器上部的進口結構形式是旋風分離器技術改進的可行措施。但是採用切向或蝸向單進口結構形式易造成旋風分離器內部氣流場的軸不對稱(渦核偏向270°一側),不但增大了旋風分離器的阻力,而且增加了排氣芯管短路流。所以趙兵濤等提出最佳化改進旋風分離器進口結構,首先增設了進口迴轉通道,通過試驗得出所有增設迴轉通道的旋風分離器分離效率均大於無迴轉通道的效率。因為阻力係數的變化可影響進口速度的變化,進口速度的大小反映出旋風分離器分離能力的強弱。當阻力係數較小時,進口速度較大,表明旋風分離器分離能力強,由於迴轉通道的增設,使顆粒在進入旋風分離器腔體前進行預分離,從而使分離效率增大,但隨著迴轉角度的繼續增大,二次返混影響增大,這就使得分離效率在90°甚至270°以後有所減小,但總體仍高於0°的分離效率。所以改變其迴轉角度,就改變了兩相流含塵濃度分布,使含塵濃度外濃內淡,從而減少短路流的攜塵量。
同時若採用雙進口迴轉通道形式,則有利於降阻增效,由於進氣口面積增大為原來的2倍,使進口氣流速度減半,從而降低了阻力;由於採用漸縮的迴轉結構,減小了顆粒到達捕集壁面的距離,從而提高了分離效率;進一步的流場測定結果表明,雙進口結構由於採用在旋風分離器內多點對稱進氣,增強了旋風分離器內部流場的軸對稱性,使短路流攜塵量減少,同時實現了降阻增效,又增強了氣流場軸對稱性,以降低旋風分離器阻力。具體試驗結果表明,將旋風分離器常規進口結構最佳化改進為採用單進口等寬通道進口結構時,旋風分離器迴轉角度為90°時性能較優,比0°(無迴轉通道)時的阻力降低14.73%,效率提高2.48%。採用雙進口漸縮通道進口結構時,旋風分離器性能優於所有單進口,比0°(無迴轉通道)時的阻力降低33.06%,效率提高3.95%。
2、旋風分離器出口結構的研究現狀
在旋風分離器內部的旋轉氣流中,顆粒物受離心力作用作徑向向外(朝向筒錐壁)運動,運動速度可由顆粒物所受的離心力及氣流阻力的運動方程求得。顯然旋風分離器分離的目的就是使顆粒物儘快到達筒錐體邊壁。因此,延長顆粒物在旋風分離器中的運動時間,在氣流作用下提高顆粒物與筒錐體壁相撞的機率,可以提高旋風分離器除塵效率。Y. Zhu提出的旋風分離器,在普通旋風分離器中增加一個筒壁,這一筒壁將旋風分離器內部空間劃分為2個環形區域,同時,排氣芯管被移到了下方,排氣芯管中的上升氣流也變成了下降氣流,顆粒物在內外2個環形區域內都得到了分離,事實上,這種旋風分離器相當於將2個旋風子結合到了一起。從理論上講,這種結構改進提高了顆粒物被收集的機率。Zhu型旋風分離器試驗結果(氣流流量範圍為10~40L/min,粒徑範圍為0.6~ 8.8μm顆粒物)與Stairmand高效旋風分離器進行了比較,改進後的旋風分離器,除塵效率得到提高,並且隨氣流流量的增大而增大;同時,對於相同無因次尺寸的旋風分離器來說,前者的阻力也小於後者。Y. Zhu考慮各方面因素給出相應最佳化綜合指標,得出改進後的旋風分離器性能優於傳統的旋風分離器。但這種改動後的旋風分離器較原有傳統旋風分離器結構稍為複雜。由於旋風分離器對微細顆粒物效率較低,尤其對粉塵粒徑小於10μm的顆粒的除塵效率隨著顆粒直徑減小逐漸降低。也就是說,在旋風分離器的運行過程中,絕大部分微細粉塵穿透了分離區域,導致對微細粉塵效率下降。
3、旋風分離器錐體結構的研究現狀
Xiang Rongbiao等研究了錐體尺寸對用於大氣採樣的小型旋風分離器的影響情況,以顆粒大小和氣流流速為變化參數,對3個具有不同下部直徑錐體的旋風分離器測出了效率。測定結果得知:錐體下部直徑大小對旋風分離採樣器的效率影響顯著,但是並不顯著影響不同粒徑顆粒物效率之間的變化程度。當錐體下部開口部分直徑大於排氣芯管直徑時,該錐體參數的減小,在不明顯增加阻力的前提下,採樣效率會隨之提高;由阻力測試結果還可看出錐體開口部分直徑不宜小於排氣芯管直徑。從理論上講,錐體下部直徑減小能引起切向速度的提高,從而離心力增大;對於具有相同筒體直徑的旋風分離器,若錐體開口小,則最大切向速度靠近錐壁,這使得顆粒能夠更好地分離,同時,如果錐體開口較小,渦流將觸及錐壁,使顆粒又有可能重新進入出氣氣流,但是後者與前者相比對旋風采樣器影響較小。所以,適當減小錐體下部直徑有利於效率的提高。
4、旋風分離器排塵結構的研究現狀
縱觀過去的100多年,旋風分離器的主要研究方向還是集中在進出口狀況,渦流檢測和筒體上,相對於排塵結構部分則很少有人注意。國內外只有極少數學者進行過相關的研究。1982年Mothes發現沿筒壁下降的下旋流與從灰斗上升的氣流在錐體底部位置交換特別頻繁,於是他提出在此加一防混錐的方法。Kirch也就這一方向做了試驗,並發現當灰斗滿載時,防混錐能夠提高效率,但是對於灰斗不滿的旋風分離器,防混錐的效果又不是太明顯。
由於已有試驗表明:錐體底部的下行流量並不為0,表明有一部分氣流進入了灰斗,因為灰斗底部堵死,氣流必將反向重新進入錐體的內旋流中,這將會攪起已被分離出的顆粒並把其中較細的顆粒再次帶入內旋流中,產生所謂的“灰斗返混”問題,這也是影響分離效率的一個重要問題。
Hoffmann等是最早對底部加直管旋風分離器進行專門研究的學者之一。他通過試驗表明,增設直管可以使渦旋尾部停留在直管中,從而增加了旋風分離器的有效分離空間,改善了分離性能。錢付平也針對灰斗返混,對底部加直管的旋風分離器內流場進行了數值模擬,發現在接近直管的底部,氣流切向速度平均3~4m,而該端面的軸向速度分布也表明氣流旋轉至此,軸向速度接近於0,這足以說明,通過增設直管,就將渦流尾端引入到直管內了。
然而,儘管加直管能取得好的分離效果,但是直管並不是越長越好,應有一最優長度。另外,不同筒體直徑的旋風分離器對應的最優直管長度是否存在一定的關係以及不同直管長度時旋風分離器內顆粒運動情況還需進一步研究。由於排塵口處於負壓較大的部位,保證排塵口的嚴密性對提高分離效率有重要作用。試驗數據表明,漏風5%,則分離效率降低50%;漏風10%~15%,則效率降至0。反之,如能從排塵口抽出部分氣流卻能提高分離效率。