擠壓變形程度、凹模半錐角、潤滑狀態及摩擦因子等是影響塑性失穩成形極限的主要因素。將不同應力狀態下測得的兩個主應變的許用值,分別標在以板面內較小的那個主應變為橫坐標、較大的那個主應變為縱坐標的坐標系裡,定下一些點,由這些點連成的曲線就稱為板料的成形極限圖FLD。
基本介紹
- 中文名:成形極限
- 外文名:forming limit
- 主要因素:擠壓變形程度、凹模半錐角等
- 解決辦法:應力分析法,應變分析法
板料成形極限
成形極限圖
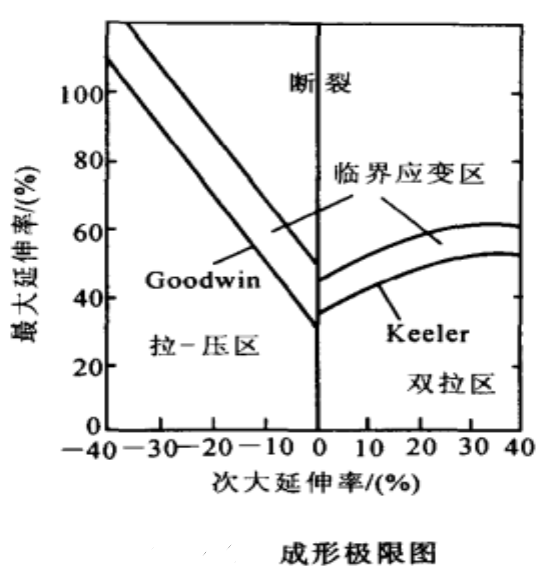
意義
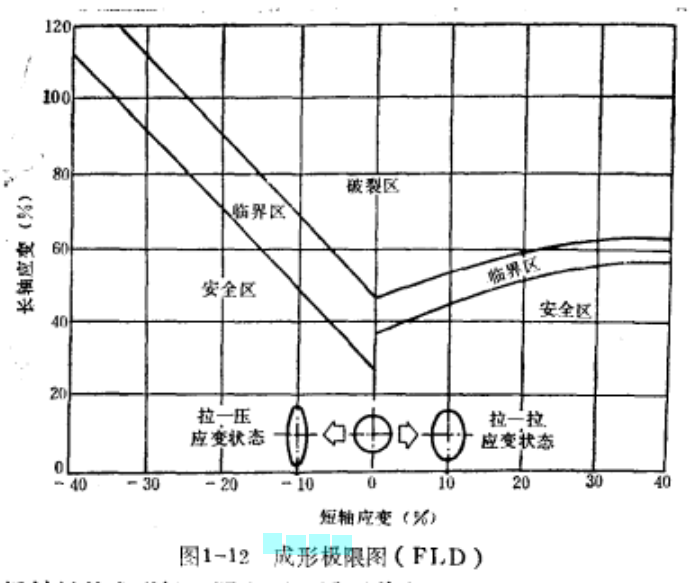
確定方法
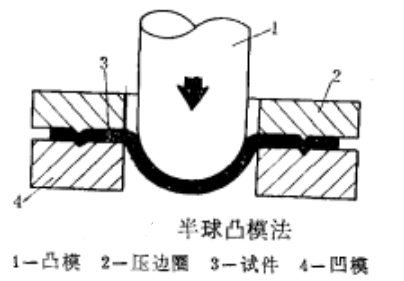
理論成形極限圖
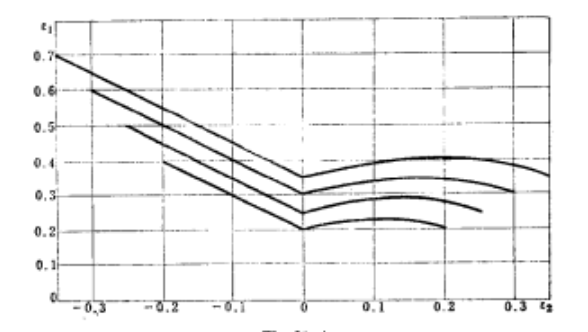
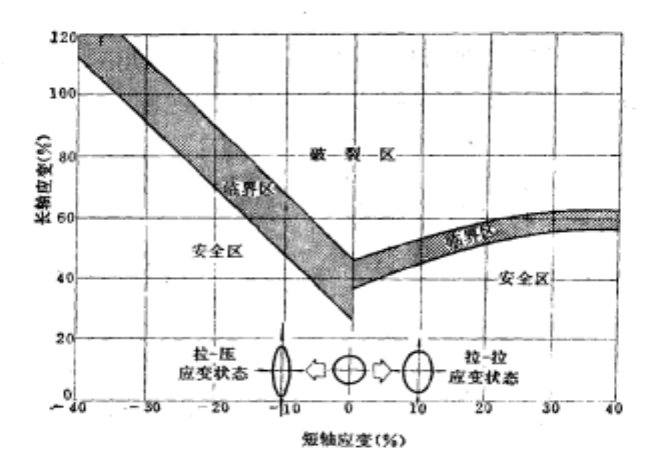
擠壓變形程度、凹模半錐角、潤滑狀態及摩擦因子等是影響塑性失穩成形極限的主要因素。將不同應力狀態下測得的兩個主應變的許用值,分別標在以板面內較小的那個主應變為橫坐標、較大的那個主應變為縱坐標的坐標系裡,定下一些點,由這些點連成的曲線就稱為板料的成形極限圖FLD。
擠壓變形程度、凹模半錐角、潤滑狀態及摩擦因子等是影響塑性失穩成形極限的主要因素。將不同應力狀態下測得的兩個主應變的許用值,分別標在以板面內較小的那個主...
成形極限圖(Forming Limit Diagrams)也稱成形極限曲線(Forming Limit Curves),它是由板料在不同應變路徑下的局部失穩極限工程應變e1和e2或極限真實應變ε1和ε2...
成形極限曲線用於確定指定的薄板在受到拉延、脹形或拉延賬形相結合時能夠達到的變形程度。從安全點到破裂點的界線定義為成形極限曲線。成形極限測定就是獲取這個曲線...
《金屬材料:薄板和薄帶成形極限曲線的測定(第2部分):實驗室成形極限曲線的測定(GB/T 24171.2-2009/ISO 12004-2:2008)》做了下列編輯性修改:a)本國際標準”...
《衝壓成形工藝》是2008年化學工業出版社出版的圖書,作者是李體彬。...... 1.2.1 板枓的衝壓成形性能 1.2.2 板枓的成形性能試驗 1.3 成形極限圖 1.3.1 ...
基本信息板料成形性能及CAE分析 書號: 46422 ISBN: 978-7-111-46422-8 作者: 龔紅英 印次: 1-1 責編: 馮春生 陳建平 開本: 16開 字數: 496千字 定價:...
成形即成為某種形體,形成某種穩固的局面。如正在成形的思想之新奇簡直使他大吃一驚;排列成一定形式或形狀使玻璃成形;醫學上指具有正常的形狀大便成形;醫學上指修復...
極限拱頂高度試驗,一種評估金屬薄板成形性的試驗方法,是杯突試驗的改進。用以確定金屬薄板在各種應變狀態下的極限應變值。簡稱LDH試驗。...
本書是國際精沖成形領域的專家和教授結合多年精沖成形技術研究和生產實踐所形成的大量經驗的總結。書中介紹了冷成形與精沖用材料的基本原理、力學性能、成形工藝、...
《輕量化成形技術》是2010年國防工業出版社出版的圖書,作者是苑世劍。本書以結構特徵為主線介紹了結構輕量化成形技術的基本原理、工藝特點及套用領域,重點介紹了面向...
超塑性成形時,工件的壁厚不均是首要問題。由於超塑性加工伸長率可達1000%,以致在破壞前出現過渡變薄,即成為其加工的成形極限。故在成形中應當儘量不使毛坯局部過渡...
《衝壓成形理論及技術》是西北工業大學出版社2012年9月出版的圖書,作者是吳詩惇,李淼泉。...
精密成形技術包括:精密鑄造(濕膜精密成形鑄造、剛型精密成形鑄造、高精度造芯)、精密鍛壓(冷濕精密成形、精密沖裁)、精密熱塑性成形、精密焊接與切割。這些技術廣泛...
《板料成形性基礎》是2004年西北工業大學出版社出版的圖書。作者是吳建軍、周維賢。本書介紹板料成形性基礎理論與實際套用,涉及板料的塑性異性理論及套用、變形抗...
液壓成形(hydroforming)是指利用液體或模具使工件成形的一種塑形加工技術,也稱液力成形。僅需要凹模或凸模,液體介質相應地作為凸模或凹模,省去一般模具費用和加工...
《衝壓工藝學》對衝壓工藝的基本總量作了系統的論述。全書共八章,介紹了沖裁、彎曲、拉深、脹形和翻邊、板料的衝壓成型性能與成型極限,衝壓工藝設計、沖模結構與...
加工硬化指數英文名即hardening index。該指數由真應力應變關係定義,指金屬薄板成形時真應力S一真應變ε關係式中的冪指數n,關係式如下:S = Kε^n,式中K為強度...