多效蒸發是將前效的二次蒸汽作為下一效加熱蒸汽的串聯蒸發裝置稱。在多效蒸發中,各效的操作壓力、相應的加熱蒸汽溫度與溶液沸點依次降低。
基本介紹
- 中文名:多效蒸發
- 外文名:multiple-effect evaporation
- 釋義:蒸發操作的一種
- 特點:節約加熱蒸汽
- 計算內容:各效蒸發水量、加熱蒸汽消耗量等
- 流程:並流、逆流、平流流程
- 缺點:裝置易結垢、腐蝕等問題
原理
流程
並流流程

逆流流程
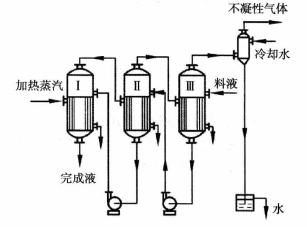
平流流程
計算


多效蒸發是將前效的二次蒸汽作為下一效加熱蒸汽的串聯蒸發裝置稱。在多效蒸發中,各效的操作壓力、相應的加熱蒸汽溫度與溶液沸點依次降低。
多效蒸發是將前效的二次蒸汽作為下一效加熱蒸汽的串聯蒸發裝置稱。在多效蒸發中,各效的操作壓力、相應的加熱蒸汽溫度與溶液沸點依次降低。...
多效降膜式蒸發器的工作原理是:物料溶液從料泵進入到循環泵的吸口處,泵在此時進行升壓,溶液在預熱後進入蒸發器的進料室,接下來進入到加熱管蒸發,蒸發後進入分離...
若蒸發產生的二次蒸汽直接冷凝不再利用,稱為單效蒸發。若將二次蒸汽作為下一效加熱蒸汽,並將多個蒸發器串聯,此蒸發過程即為多效蒸發。 [1] ...
多效膜蒸餾(multiple-effect membrane distillation,簡稱為MEMD)過程: 膜蒸餾過程中水蒸氣的相變熱約為2600kJ/kg,遠大於水的比熱4kJ/ kg.K。因此,若按常規減壓...
加熱介質與溶液直接接觸傳熱,如浸沒燃燒式蒸發器。蒸發裝置在操作過程中,要消耗大量加熱蒸汽,為節省加熱蒸汽,可採用多效蒸發裝置和蒸汽再壓縮蒸發器。蒸發器廣泛用於...
早期的蒸發技術能耗很大,為了節約能源,也是為了最大限度的減小向環境排放帶有物料的二次蒸汽而污染環境,隨著化工技術的發展以及節能技術的要求,人們又開發了多效蒸發...
蒸發器與其他蒸發器比較蒸發方式 反應釜 單效蒸發器 多效蒸發器 噴射泵 MVR蒸發器 能耗 能耗高,蒸發一噸水大約需要1.5噸蒸汽 能耗較高,蒸發一噸水理論上...
單效蒸發是蒸發操作的一種。其特點是所產生的二次蒸汽不用來使物料進一步蒸發,只是單台設備的蒸發。對於單效蒸發,在給定生產任務和確定了操作條件後,通常需要計算...
真空蒸發是在真空下進行的蒸發操作。在真空蒸發流程中,末效的二次蒸汽通常在混合式冷凝器中冷凝。真空蒸發的特點是,在低壓下溶液的沸點降低且用較少的蒸汽蒸發大量...
廢水蒸發器 針對化工有機廢水高鹽分高濃度等特點,基於蒸發濃縮結晶的原理.採用多效減壓蒸發濃縮結晶有機廢水,對濃縮液中的鹽分進行分離後,通過集鹽器進行回收,濃縮...
與減壓蒸發類似,蒸髮結晶器也可在減壓條件下操作。通過減壓可以降低料液的沸點,從而可以通過多效蒸發來充分利用熱量,NaCl 生產曾採用了這種多效蒸發形式的結晶器。 ...
② 正常運行時該系統只用電,蒸發每噸水的能耗為15KW.h至100KW.h,其運行費用為多效蒸發的1/8~1/2。③ 是目前最節能的蒸發器,多為單效蒸發,加熱溫差小,...
可分為單效蒸發、二效蒸發和多效蒸發。如前所述,要保證蒸發的進行,二次蒸汽必須不斷地從蒸發室中移除,若二次蒸汽移除後不再利用時,這樣的蒸發稱為單效蒸發;...
MVR蒸發器不同於普通單效降膜或多效降膜蒸發器,MVR為單體蒸發器,集多效降膜蒸發器於一身,根據所需產品濃度不同採取分段式蒸發,即產品在第一次經過效體後不能...
對於一些不宜在高溫下操作的物料,多效蒸發不適用,而熱壓縮蒸發則可在低沸點下進行。在食品工業,1,。如牛奶和果汁的濃縮;還有海水淡化裝置中,熱壓縮蒸發已得到...
在水平管降膜蒸發中,氣液容易迅速分離,傳熱溫差小,因而比豎管降膜與浸沒管蒸發具有更好的傳熱效果。而且在作為熱法海水淡化主要技術的多效蒸發(multi.effect ...
凡是溶液在蒸發器蒸發時,所產生的二次蒸汽不再利用,則此種蒸發操作稱為單效蒸發。使用單效蒸發方式的蒸發器稱為單效蒸發器。當所需要的生產能力規模小,蒸汽是...
蒸發方式 反應釜 單效蒸發器 多效蒸發器 噴射泵 MVR蒸發器 能耗 能耗高,蒸發一噸水大約需要1.5噸蒸汽 能耗較高,蒸發一噸水理論上需要1噸蒸汽 比較節能,...
瑞普MVR蒸發器是中國瑞普膜技術公司生產的特有多效蒸發濃縮設備。廣泛套用於氯鹼、石油、化工、電力、電子、醫藥、鋼鐵、食品、飲料、紡織印染、中水回用、廢水處理...
多級閃蒸是針對多效蒸發結垢較嚴重的缺點而發展起來的,具有設備簡單可靠、防垢性能好、易於大型化、操作彈性大以及可利用低位熱能和廢熱等優點。因此一經問世就得到...