《在直形連鑄機上生產直徑≥φ800mm圓坯的連鑄方法》是江陰興澄特種鋼鐵有限公司於2008年12月1日申請的發明專利,該專利的申請號為2008102431302,公布號為CN101428335,公布日為2009年5月13日,發明人是張文基、周月林、李國忠、李峰、童憶、朱國榮、徐國慶。
《在直形連鑄機上生產直徑≥φ800mm圓坯的連鑄方法》包括以下工藝過程:從煉鋼爐出來的鋼水注入鋼包內,通過鋼包迴轉台轉到中間包的上方,鋼水流入結晶器內,結晶器表面保護渣的主要成分重量百分比為:SiO226~32%、Al2O314~18%、CaO24~28%、C16~20%和Li2O2~4%,結晶器下端出口處坯殼有一定厚度時,同時啟動拉矯機和結晶器振動裝置,使帶有液心的圓坯緩慢往下拉出,由火焰切割機切成4~8米的定尺圓坯,將切斷的圓坯放平拉出,將表面溫度600℃以上的定尺圓坯吊到緩冷坑進行24小時以上的緩冷,緩冷結束後的圓坯吊到拋丸機進行表面拋丸檢查。
2014年11月6日,《在直形連鑄機上生產直徑≥φ800mm圓坯的連鑄方法》獲得第十六屆中國專利優秀獎。
(概述圖為《在直形連鑄機上生產直徑≥φ800mm圓坯的連鑄方法》摘要附圖)
基本介紹
- 中文名:在直形連鑄機上生產直徑≥φ800mm圓坯的連鑄方法
- 公布號:CN101428335
- 公布日:2009年5月13日
- 申請號:2008102431302
- 申請日:2008年12月1日
- 申請人:江陰興澄特種鋼鐵有限公司
- 地址:江蘇省江陰市濱江東路297號
- 發明人:張文基、周月林、李國忠、李峰、童憶、朱國榮、徐國慶
- 分類號:B22D11/00(2006.01)I、B22D11/10(2006.01)I、B22D11/112(2006.01)I、B22D11/115(2006.01)I等
- 代理機構:江陰市同盛專利事務所
- 類別:發明專利
- 代理人:唐紉蘭
專利背景,發明內容,專利目的,技術方案,改善效果,附圖說明,權利要求,實施方式,榮譽表彰,
專利背景
特大規格圓坯主要供給無縫鋼管廠製作無縫鋼管和鍛件廠製作各種設備毛坯。以往特大規格圓坯的生產工藝是用模注工藝生產。由於模注工藝生產率低下,能耗高,成材率比連鑄工藝低10%以上,導致生產成本很高,並且質量也不穩定,難以滿足市場的需求。連鑄圓坯由於克服了模注圓坯的缺點,正大量取代模注圓坯。但對於直徑≥φ800毫米的圓坯,2008年12月前世界尚未有用連鑄成功生產的先例。生產大規格圓坯由於缺乏有效的控制手段,特大規格圓坯在澆注凝固時產生的大收縮量將無法補足,勢必引起坯料中心產生嚴重的偏析和疏鬆,同時由於冷卻過程中產生應力,坯料中心還會產生嚴重的裂紋;另外,由於常規結晶器保護渣的保溫效果滿足不了大規格圓坯生產的要求(大規格圓坯散熱面積大),澆注過程中會不同程度的出現結晶器表面鋼水出現結殼凝固的問題,給正常生產帶來了很多困難,如果生產≥φ800毫米大規格的圓坯,必須開發專用保護渣。
發明內容
專利目的
《在直形連鑄機上生產直徑≥φ800mm圓坯的連鑄方法》的目的在於克服上述不足,提供一種能補足在澆注凝固時產生的大收縮量、解決冷卻過程中產生應力問題、結晶器保護渣的保溫效果能滿足大規格圓坯生產要求的能在直形連鑄機上生產直徑≥φ800毫米特大規格圓坯的連鑄方法。
技術方案
《在直形連鑄機上生產直徑≥φ800mm圓坯的連鑄方法》其特徵在於所述方法包括以下工藝步驟:從煉鋼爐出來的鋼水注入鋼包內,經過鋼包爐精煉和真空脫氣爐真空脫氣處理後用行車吊到連鑄機的鋼包迴轉台上,通過鋼包迴轉台轉到中間包的上方,鋼水通過鋼包底部的水口再注入到中間包的衝擊區內,中間包的衝擊區和澆注區用流鋼通道相連,該流鋼通道長1.2~1.6米,外徑φ500毫米±50毫米,內徑φ200毫米±20毫米,主要成分重量百分比:MgO80~90%、C10~20%。中間包壁使用了納米保溫材料,中間包內設定有感應加熱裝置和連續測溫裝置,通過對中間包內的鋼水實施實施納米保溫材料保溫、感應加熱和使用連續測溫裝置測溫,可以有效控制中間包內鋼水過熱度穩定在10~25℃。(這段還是再添加上去比較好)中間包澆注區水口的位置被預先調好以對準下面的結晶器,打開中間包塞棒後,鋼水通過水口流入下口由引錠桿頭封堵的結晶器內,在結晶器內,鋼水沿結晶器周邊逐漸冷凝成鋼殼,結晶器採用水冷結晶器,結晶器冷卻水量控制在350~450立方米/時,在結晶器外,使用電磁攪拌裝置對結晶器內的鋼水進行攪拌,攪拌電流50~150A,攪拌頻率0.5~1.0赫茲。為了防止結晶器表面因圓坯斷面大和拉速慢而結冷鋼,重新設計了保護渣的成份。結晶器表面保護渣的主要成分重量百分比為:SiO226~32%、Al2O314~18%、CaO24~28%、C16~20%、Li2O2~4%。為了減小拉矯機的拉坯阻力,在結晶器底部設定結晶器振動裝置,使凝固的坯殼不沾在結晶器壁上,當結晶器下端出口處坯殼有一定厚度時,同時啟動拉矯機和結晶器振動裝置,澆注速度控制在0.2~0.3米/分鐘,使帶有液心的圓坯緩慢往下拉出,在這裡圓坯一邊下行,一邊經受外圍二次冷卻區中許多噴嘴噴出的水的強制冷卻繼續凝固,為了解決圓坯中心容易產生裂紋的問題,採用每隔3~5米用噴嘴進行冷卻、再每隔5~7米不用噴嘴進行冷卻的間隔冷卻方式。當圓坯拉出一定長度時,引錠桿頭與圓坯脫開。待圓坯完全凝固後,由火焰切割機切成4~8米的定尺圓坯,使用傾覆裝置將切斷的圓坯放平拉出,最後由行車使用專用夾具將表面溫度600℃以上的定尺圓坯吊到緩冷坑進行24小時以上的緩冷,緩冷結束後的圓坯用行車吊到拋丸機進行表面拋丸檢查。
澆注快結束時,由於得不到鋼水的及時補給,φ800連鑄大圓坯中間出現明顯的縮孔,影響的圓坯長度在1000毫米以上,成材率影響較大,為解決這一問題,主要採取以下措施:在澆注結束前20~30分鐘,
1)放慢引錠桿頭拉速到0.10~0.15米/分鐘(正常拉速是0.20~0.30米/分鐘)。
2)採用塞棒點動脈衝衝擊鋼流,提高鋼水衝擊深度,達到鋼水補充縮孔的效果。
3)在不捲渣的情況下,加大結晶器電磁攪拌強度,攪拌電流200~300A,攪拌頻率0.5~1.0赫茲。
4)為了延遲圓坯尾部鋼水的凝固時間,保證對圓坯良好的補縮通道和足夠的補縮鋼液,減小圓坯尾部縮孔,往結晶器內加入發熱劑,發熱劑的主要成份重量百分比為:MgO2~5%、Al20~28%、Al2O325~40%、NaNO38~12%、SiO220~30%、鱗片狀石墨2~4%。該發熱劑另外添加2~4%的發熱劑,可以使發熱劑膨脹,起到良好的保溫效果。
5)為了進一步增加保溫效果,在結晶器內的鋼水上面加絕熱蓋板,保證補縮。
改善效果
1、採用了專用結晶器保護渣,可以補足在澆注凝固時產生的大收縮量。解決了φ800毫米以上特大規格圓坯低速澆注時結晶器表面鋼水易凝固的技術難題,使坯料中心偏析和疏鬆產生。保證了鋼水的順利澆注。
2、採用每隔3~5米用噴嘴進行冷卻、再每隔5~7米不用噴嘴進行冷卻的間隔冷卻制度,冷卻過程中無應力產生,坯料中心不會產生裂紋。解決了圓坯中心容易產生裂紋的問題。
3、澆注結束時,為了進一步保溫,在結晶器內的鋼水上面加絕熱蓋板,保證補縮。滿足了大規格圓坯生產的要求,澆注過程中不會出現結晶器表面鋼水出現結殼凝固。
4、澆注結束時,為防止鑄坯尾部收縮影響圓坯質量,採用了專用發熱劑來補縮。
5、普通結晶器電磁攪拌的使用頻率在2~10赫茲,但由於大規格圓坯大,常規結晶器攪拌的穿透力不夠,該發明設計的結晶器電磁攪拌可以使用低頻的電流,頻率0.5~1.0赫茲,從而保證了整個圓坯截面上的鋼水都能得到攪拌,改善了大規格圓坯生產時結晶器內鋼水傳熱的過程。
6、在中間包的衝擊區和澆注區之間使用了1.2~1.6米長的流鋼通道,提高了鋼水的純淨度。
7、由於φ800毫米特大規格圓坯的澆鑄速度很低,只有0.1~0.3米/分鐘,常規的直形連鑄機採用鏈條傳動,無法穩定控制,該發明設計採用絲槓傳動系統控制拉矯機,使圓坯拉矯狀態得到穩定控制,保證了特大規格圓坯的順利澆注。
綜上所述,該發明採用的φ800毫米特大規格圓坯連鑄工藝,保證了生產過程的順利實施,並保證了圓坯的內外質量,能生產較長定尺的圓坯,可代替模注鍛坯供無縫鋼管廠製作無縫鋼管和鍛件廠製作各種設備毛坯。
附圖說明
圖1為該發明在直形連鑄機上生產直徑≥φ800毫米特大規格圓坯的連鑄方法的工藝流程圖。
圖中:鋼包1、鋼包迴轉台2、連續測溫裝置3、中間包4、中間包壁納米保溫材料5、保護渣6、冷卻水噴嘴7、液相穴8(圓坯未凝固區域)、圓坯9、流鋼通道10、電磁攪拌裝置11、結晶器12、結晶器振動裝置13、導向輥14、火焰切割機15、傾覆裝置16、平台17、拋丸機18、緩冷坑19。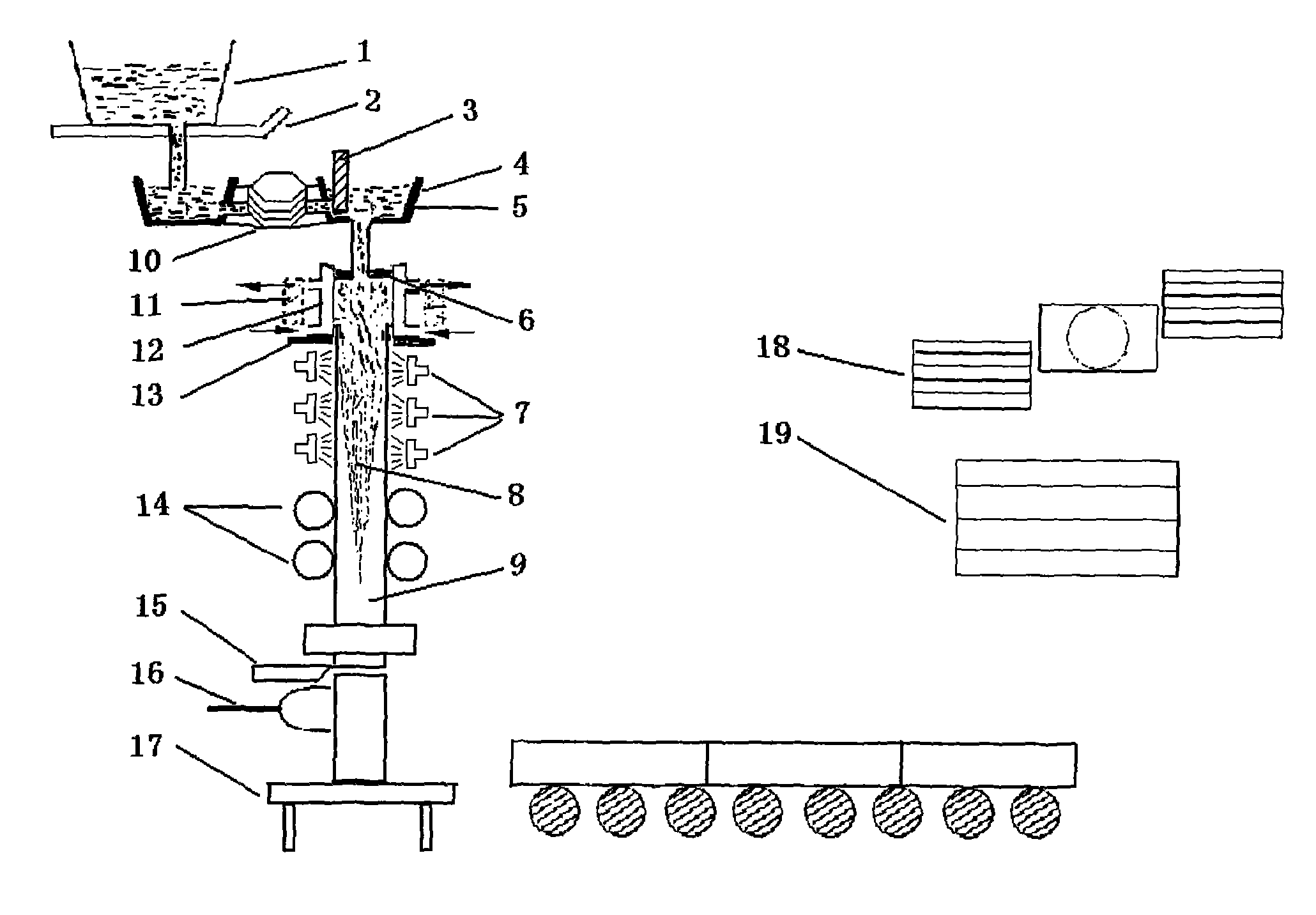
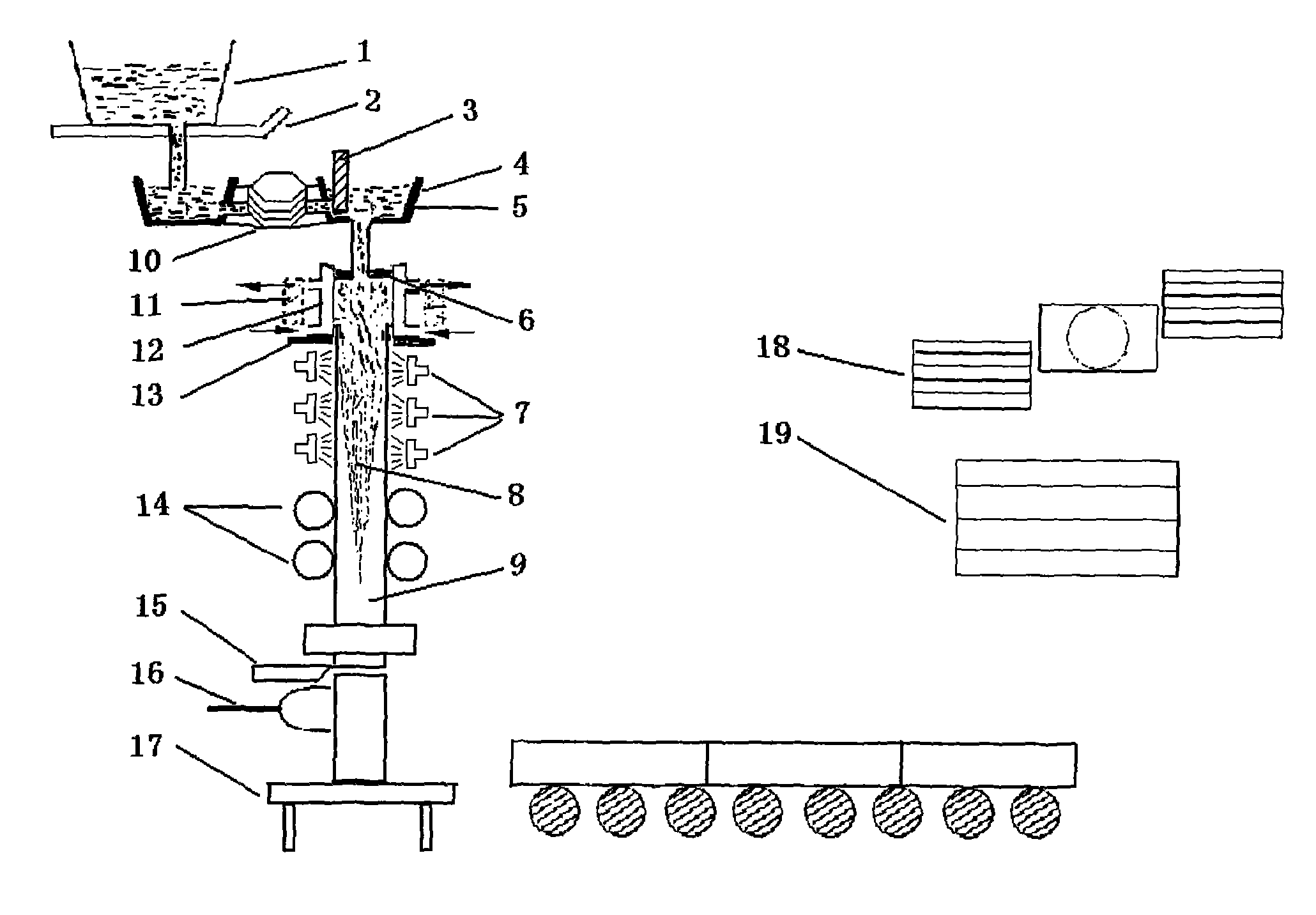
圖1
權利要求
《在直形連鑄機上生產直徑≥φ800mm圓坯的連鑄方法》其特徵在於所述方法包括以下工藝過程:從煉鋼爐出來的鋼水注入鋼包內,經過鋼包爐精煉和真空脫氣爐真空脫氣處理後吊到連鑄機的鋼包迴轉台上,通過鋼包迴轉台轉到中間包的上方,鋼水通過鋼包底部的水口再注入到中間包的衝擊區內,中間包的衝擊區和澆注區用流鋼通道相連,該流鋼通道長1.2~1.6米,外徑φ500毫米±50毫米,內徑φ200毫米±20毫米,主要成分重量百分比:MgO80~90%和C10~20%,中間包壁使用了納米保溫材料,中間包內設定有感應加熱裝置和連續測溫裝置,控制中間包內鋼水過熱度穩定在10~25℃,中間包澆注區水口的位置被預先調好以對準下面的結晶器,打開中間包塞棒後,鋼水通過水口流入下口由引錠桿頭封堵的結晶器內,在結晶器內,鋼水沿結晶器周邊逐漸冷凝成鋼殼,結晶器採用水冷結晶器,結晶器冷卻水量控制在350~450立方米/時,在結晶器外,使用電磁攪拌裝置對結晶器內的鋼水進行攪拌,攪拌電流50~150A,攪拌頻率0.5~1.0赫茲,結晶器表面保護渣的主要成分重量百分比為:SiO226~32%、Al2O314~18%、CaO24~28%、C16~20%和Li2O2~4%,在結晶器底部設定結晶器振動裝置,結晶器下端出口處坯殼有一定厚度時,同時啟動拉矯機和結晶器振動裝置,澆注速度控制在0.2~0.3米/分鐘,使帶有液心的圓坯緩慢往下拉出,在這裡圓坯一邊下行,一邊經受外圍二次冷卻區中許多噴嘴噴出的水的強制冷卻繼續凝固,採用每隔3~5米用噴嘴進行冷卻、再每隔5~7米不用噴嘴進行冷卻的間隔冷卻方式,當圓坯拉出一定長度時,引錠桿頭與圓坯脫開,待圓坯完全凝固後,由火焰切割機切成4~8米的定尺圓坯,使用傾覆裝置將切斷的圓坯放平拉出,最後由行車使用專用夾具將表面溫度600℃以上的定尺圓坯吊到緩冷坑進行24小時以上的緩冷,緩冷結束後的圓坯用行車吊到拋丸機進行表面拋丸檢查,在澆注結束前20~30分鐘:
1)放慢引錠桿頭拉速到0.10~0.15米/分鐘;
2)採用塞棒點動脈衝衝擊鋼流;
3)結晶器電磁攪拌電流200~300A,電磁攪拌頻率0.5~1.0赫茲;
4)往結晶器內加入發熱劑,發熱劑的主要成份重量百分比為:MgO2~5%、Al20~28%、Al2O325~40%、NaNO38~12%、SiO220~30%和鱗片狀石墨2~4%;
5)在結晶器內的鋼水上面加絕熱蓋板。
實施方式
參見圖1,該發明涉及的在直形連鑄機上生產直徑≥φ800毫米圓坯的連鑄方法的具體工藝步驟如下:實施是在一台單流的直形連鑄機上進行的,具體生產圓坯的規格為φ800毫米,品種為42CrMo、15CrMoG、12CrlMoVG等合金鋼種。
從煉鋼爐出來的100~120t鋼水注入鋼包內,經過鋼包爐精煉和真空脫氣爐真空脫氣處理後用行車吊到連鑄機的鋼包迴轉台上,通過鋼包迴轉台轉到中間包的上方,鋼水通過鋼包底部的水口再注入到中間包的衝擊區內,中間包的衝擊區和澆注區用流鋼通道相連,該流鋼通道長1.4米,外徑φ500毫米,內徑φ200毫米,主要成分重量百分比:MgO80~90%、C10~20%。中間包壁使用了納米保溫材料,中間包內設定有感應加熱裝置和連續測溫裝置,通過對中間包內的鋼水實施實施納米保溫材料保溫、感應加熱和使用連續測溫裝置測溫,可以有效控制中間包內鋼水過熱度穩定在10~25℃。中間包澆注區水口的位置被預先調好以對準下面的結晶器,打開中間包塞棒後,鋼水通過水口流入下口由引錠桿頭封堵的結晶器內,在結晶器內,鋼水沿結晶器周邊逐漸冷凝成鋼殼,結晶器採用水冷結晶器,結晶器冷卻水量控制在350~450立方米/時,在結晶器外,使用電磁攪拌裝置對結晶器內的鋼水進行攪拌,攪拌電流50~150A,攪拌頻率0.5~1.0赫茲。結晶器表面保護渣的主要成分重量百分比為:SiO226~32%、Al2O314~18%、CaO24~28%、C16~20%、Li2O2~4%。在結晶器底部設定結晶器振動裝置,當結晶器下端出口處坯殼有一定厚度時,同時啟動拉矯機和結晶器振動裝置,澆注速度控制在0.2~0.3米/分鐘,使帶有液心的圓坯緩慢往下拉出,在這裡圓坯一邊下行,一邊經受外圍二次冷卻區中許多噴嘴噴出的水的強制冷卻繼續凝固,採用每隔3~5米用噴嘴進行冷卻、再每隔5~7米不用噴嘴進行冷卻的間隔冷卻方式。當圓坯拉出一定長度時,引錠桿頭與圓坯脫開。待圓坯完全凝固後,由火焰切割機切成4~8米的定尺圓坯,使用傾覆裝置將切斷的圓坯放平拉出,最後由行車使用專用夾具將表面溫度600℃以上的定尺圓坯吊到緩冷坑進行24小時以上的緩冷,緩冷結束後的圓坯用行車吊到拋丸機進行表面拋丸檢查。
在澆注結束前20~30分鐘,
1)放慢引錠桿頭拉速到0.10~0.15米/分鐘;
2)採用塞棒點動脈衝衝擊鋼流;
3)在不捲渣的情況下,加大結晶器電磁攪拌強度,攪拌電流200~300A,攪拌頻率0.5~1.0赫茲;
4)往結晶器內加入發熱劑,發熱劑的主要成份重量百分比為:MgO2~5%、Al20~28%、Al2O325~40%、NaNO38~12%、SiO220~30%、鱗片狀石墨2~4%;
5)在結晶器內的鋼水上面加絕熱蓋板。
經檢驗,圓坯的表面質量良好,橫斷面的低倍質量達到了國家(行業)標準的一級,經過用戶試用,完全滿足了用戶要求。由於連鑄圓坯從鋼水到圓坯的成材率可達90%以上,比模注高5%以上,且流程短,成本下降明顯;另外,由於連鑄圓坯質量穩定,滿足了市場的需求。
榮譽表彰
2014年11月6日,《在直形連鑄機上生產直徑≥φ800mm圓坯的連鑄方法》獲得第十六屆中國專利優秀獎。