概述
在煉鋼過程中,用經過壓縮的氬、氮等氣體把冶金反應劑(鈣一矽、氧化鈣、鎂、炭等粉料)噴吹到鋼液里以提高鋼的質量的新技術,叫做噴射冶金。簡稱噴粉。它是強化鋼水精煉過程的最有效的方法。所噴射的粉料具有每克約500~2000平方厘米那樣大的表面積。當載流氣體噴入鋼液中時,會分離成許多小氣泡,使鋼液運動得到加速,並形成射流,射流區附近的鋼液不斷被吸人力作用區,使鋼液呈微滴狀態懸浮在氣相和固相中,這就大大增加了鋼液與粉粒的接觸面積。另外,射流的機械能傳遞給鋼液,會產生激烈的攪拌運動,使擴散界面層厚度降到極小,並強化液態體積元素中粒子到界面的輸運,增加顆粒湍流碰撞,促進體積元素中粒子長大。在反應區, 粉料具有很高的局部濃度梯度。 所有這些,創造了最佳的傳質條件,使鋼水脫磷、脫硫、脫氧等精煉反應迅速而充分地進行,夾雜物浮升排除速度大大加快,鋼液的質量得以有效地改善,冶煉時間也可以縮短,從而提高生產率,降低能耗。
攪拌帶來的極高的傳質速度,可使合金粉料高速溶解於鋼液之中,這就使合金消耗大幅度降低,使合金收得率幾乎接近於100%。特別是高蒸氣壓,低密度的活性粉料,直接噴入鋼液深處後,不但可以經濟地生產出高純度鋼種,而且還能有效地改善鋼液中夾雜物的類型、形狀、大小和分布,同時為鋼精確的微合金化開闢新的途徑。
封閉式的噴吹系統可使工作環境清潔,而且熔池本身就是一個集塵器。其噪音很小,因此噴射冶金不會對環境污染。
噴粉技術設備簡單,投資和成本低廉。它通常由粉料輸送裝置、貯料罐、輸氣系統、粉料分配器,噴槍和控制系統等組成。噴粉技術適應性強,靈活多變。噴吹的粉料,可以是還原劑、氧化物,也可以是合金、渣料或脫硫劑、脫氧劑等。它在爐外爐內均可採用。不僅適用於電爐,也可用於轉爐。特別是底吹轉爐噴吹氧氣和石灰粉,造成高鹼度、低粘度、高彌散度爐渣,可以達到同時脫磷和脫硫的目的,給氧氣轉爐煉鋼帶來革命性變化。
最早(1969年)應有鋼包噴射冶金技術的是聯邦德國蒂森公司(Thyssen Niederrhein AG),所以有人稱鋼包噴射冶金技術為TN處理法。隨後
瑞典、
法國等也開展了這一工藝的研究工作,在理論研究、設備和工藝方面也有所發展。80年代初,中國鋼鐵工業陸續裝備了噴射冶金設備,開展了電爐工藝改革、爐外精煉及鐵水中有價元素富集等方面的工作。
噴射冶金技術的發展,至今雖然只有十幾年的時間,但由於它使傳統的火法冶金術取得了突破性的進展,顯示出強大的生命力,因而在世界上受到普遍重視和廣泛套用。噴射冶金技術近幾年在我國也取得了可喜的發展,已從工業性試驗階段逐步過渡到了生產套用階段。但是,人們對這項新技術的認識還很不夠,目前,只知道噴粉可以起到什麼作用,還不知道為什麼能起到這種作用。因此,要繼續大力開展這項技術的研究工作, 使之更好地為冶金工業現代化建設服務。
動力特性
在鈦渣熔煉中,直流一空心電極電爐的套用可以說是這一領域發展進程中的一次質的飛躍。當人們的視角從填充床反應器移向全流反應器時就會看到,直流一空心電極電爐熔煉鈦渣工藝的高效率和優異的冶金效果,主要是由電漿一氣粉射流通過對熔體做功產生的攪拌作用和由此造就的氣泡、液滴、顆粒構築成的彌散系統及其對冶金反應的強化作用,而這一切正是現代理念上的噴射冶金。
理想反應器
從冶金反應工程學角度,可以把多渣熔煉的礦熱電爐視為一個工業反應器來研究。反應器的巨觀動力學因素是流體的流動,因為傳熱和傳質總是伴隨流動而進行的,物質濃度、溫度和停留時間的分布都與流動特性有關,從而反應的速度和轉化率也與流動有關。反應器中流動和混合屬於理想流動即活塞流和混合流的,稱為理想反應器,它有如右圖所示的三種:間歇式反應器、活塞流反應器和完全混合反應器。活塞流也稱平推流,其含義是所有物料在反應器內停留時間相同,不存在返混。由於多渣礦熱電爐的裝料和熔煉產物放出具有連續或半連續的性質,在達到穩定工況以後,反應物(爐料)的轉化率不隨時間而變化,儘管各點濃度不一定相同,但徑向截面速度分布比較均勻,所以具有活塞流的特點。但不斷加入的爐料的熔化和原有物料的迅速混合,又使各處物料的濃度趨於一致,這是一種返混現象,所以又具有返混流即傘混流的特點。
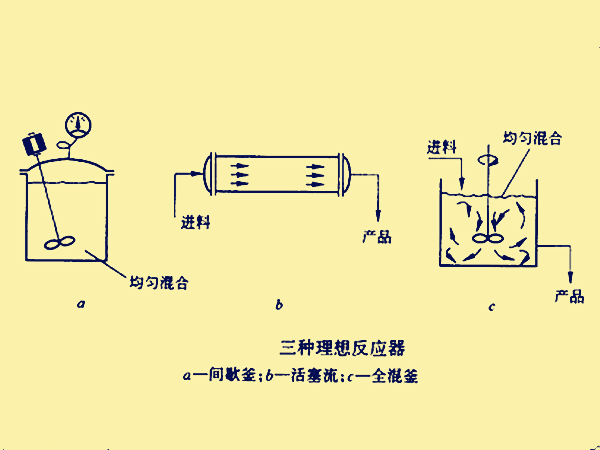
上述的三種理想流動反應器,可以把間斷法工藝熔煉鈦渣電爐定性在間歇式反應器,連續法工藝的電爐定性在流通式(活塞流和全混流)反應器。但它們實際都算不上完全理想流動,因為在交流電爐中以熱壓頭推動的熔體運動和電磁力引起的熔體運動只限於發生在電極插入深度的區域,電極端下面是“死流”區(參見第4章)。當然,死流也不是絕對靜止的,按定義,死流的停留時間為物料平均停留時間的兩倍。因此,這樣的熔池流動的現象應看作是活塞流一全混流一死流的組合;但增加了氣粉射流(電漿射流)作用的空心電極加料直流電弧爐,由於消除或減少死流區並強化了渣、鐵熔體流動,則可認為是全混流區占有很大比例的理想反應器。
射流特性
獲得動能的氣體自噴嘴噴出將形成軸向射流,射流進入靜止的周圍中,在不受周圍空間的限制時,形成自由射流。其結構如右圖所示。在氣一氣噴出體系中,氣體起始速
自直徑為
的噴嘴噴出,在截面
處,其速度可視為均一的。隨著射流沿
軸方向繼續運動,周圍流體被射流卷吸,使射流加粗,但靠中心部分的速度仍保持從噴嘴流出時的起始速度,這一區域成為勢流核心區。由於卷吸的作用,核心區的直徑隨z的增加而逐漸減小,直至為零。由噴嘴出口截面到射流軸線上速度開始減小處的距離即為核心區的長度勢流核心區的外圍是混合區,流動速度逐漸降低,至外邊界處速度為零,混合區的寬度隨的增加而逐漸增加。
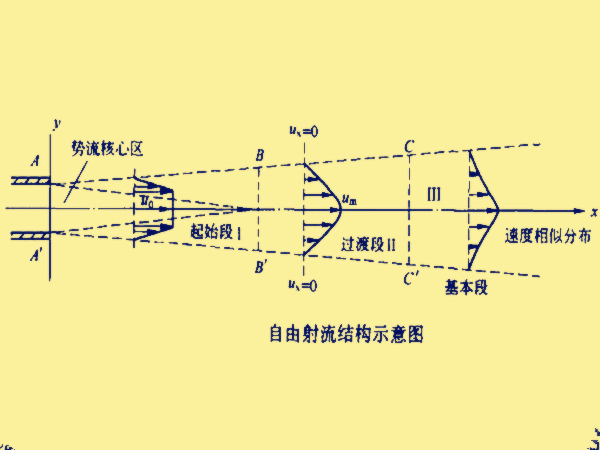
這一段為射流發展區,稱為起始段,其範圍約為(0~6.4)
,在這一區域內流股的擴張速度可以用擴張角表示,其數值可由實驗獲得。對於氣一氣體系,擴張角為
。射流經歷起始段後,軸線上的速度開始降低,進入了流股的第二階段過渡段。
在過渡段內,速度分布趨於均勻,整個區域屬混合區,此區域位於(6.4~8.0)
之間。從截面
開始,射流已充分發展,沿軸方向,軸向的均速度在不同的截面上有類似的形狀。當射流中心速度衰減為零時,射流能量完全消耗在周圍空間中,此時射流終結。
氣流或氣粉流噴人高溫熔體中的,屬於限制射流,或稱浸沒射流,它與自由射流最大的不同,就是速度的衰減特性。根據氣體噴入水中的實驗,射流中心線速度開始衰減的距離大大縮短,如有的情況在(1~2)
處就開始衰減,這遠早於氣相中的氣體射流。但在(0.8~5)
之間,液相中氣體射流中心線速度的衰減規律與 5
有很大區別,遠於5
以後,衰減速度明顯加快,在20
處,液相中氣體射流的軸線速度
已減至其噴口原始速度
的1/10。而氣相中氣體射流軸線速度衰減到原始速度的1/10所需的距離約為60
。
此時,不與液相介質反應的氣體射流,在液相中均將形成氣泡,氣泡浮力是影響射流行為的主要因素。
氣粉射流穿透熔體過程
固體粉粒噴入熔體是以氣體作為載體,以氣粉兩相射流方式進行的。氣固兩相射流噴入液體時,根據氣體攜帶固體粉粒密度的不同而具有不同的行為,其兩種極限情況如右圖所示。右圖a是顆粒少而粒徑大的情況,顆粒之間相互不影響,各個顆粒被氣體單獨輸送,氣體速度
明顯大於顆粒速度
;在右圖b的第二種情況中,顆粒相互靠近,以致顆粒周圍的氣體流動邊界層相互重疊,因此氣體和顆粒的運動結合起來,二者的速度幾乎相同。
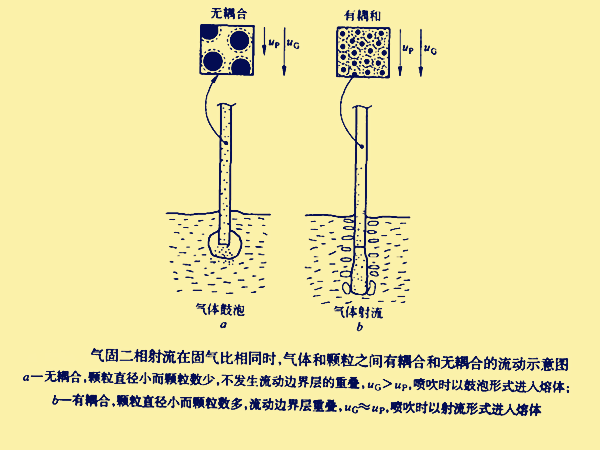
電漿射流的穿透熔體深度
氣粉射流對熔池的穿透深度,既標誌著粉粒的噴吹深度,也決定著熔體流動的速度、範圍等。
與噴嘴射流具有類似特性的直流電弧電漿,是由電磁泵原理產生的陰極射流。電弧本是氣體導電的一種現象,在電離度約1%的冶金常用的電漿中,包含有帶正電的醜離子和帶負電的電子(或負離子),因正、負離子數目相同而呈等離子狀態。在電場力的作只下,電子朝陽極方向運動,正離子朝陰極方向運動,但電子與正離子雖然密度相同而質量卻相差懸殊,以致在二者初速度和受作用力相同的情況下,電子的速度要遠大於正離子的運動速度,因此可以認為電弧電流基本上是由電子流構成的。由於電弧電流產生的磁場和電流自身形成的洛倫茲力的作用,在陰極附近,弧柱將以高達數千乃至上萬米每秒的速度(指多型電爐),形成向熔池陽極方向逐漸減速的和約呈傾斜
擴張的高速射流。而交流電弧,由於極性的交替變化則形成不了高速射流。有實驗測得,碳電弧的陽極發射的氣流速度是100m/s,陰極的則可達到10000m/s,即約相差100倍。
與一般的氣體或氣粉射流的不同點,等離子弧是一個在電場作用下獲得的高速射流,它對熔池的衝擊作用和煉鋼氧氣頂吹轉爐中氧流股的衝擊作用在本質上是相似的。
基本原理
氧氣頂吹熔煉過程是依靠氧氣噴槍的噴射氣流對熔池的強烈攪動作用來實現的,如右圖所示。因而,噴射行為對冶金過程是至關重要的。在金川頂吹熔煉爐中使用的非浸沒式噴槍結構如右圖所示,噴槍由多層同心圓套管組成:中心油管1、氧氣管2、冷水進入套管3和冷卻水排出套管4。冷卻水從套管壁之間通道通過,實現對槍體的冷卻。
槍末端是一個可更換的噴嘴,由噴嘴射出超音速氧氣流衝擊到熔池面上,形成凹坑,產生熔體內的回流運動,造成熔池內氣一液一固三相的攪動混合狀態,加速爐料的熔化和冶金過程。
氧氣流對熔池面的噴射衝擊強度是熔煉過程進行好與壞的關鍵。合適的衝擊強度除了使爐料的熔化速度最快,化學反應迅速,銅鎦或金屬與爐渣的良好分離之外,還應該使熔體對爐襯的沖刷腐蝕最輕、煙塵率最小。投產初期的實踐發現,由於氧槍位高,噴射衝擊強度不夠,造成熔池內的回流微弱,以至產生大面積的“死區”,爐底凍結層達1m之厚。
反之,過強的衝擊造成過於激烈的攪動,導致熔池渣線處爐襯迅速損害。銅精礦的氧氣頂吹熔煉又不同於頂吹煉鋼,後者是氧氣射流衝擊單相液體面,而前者則是液體面上還有不斷加入的精礦爐料,部分固體爐料隨液體環流流動,形成液一固一氣(
)的三相混合流。這種現象比單純的氧氣流衝擊出的凹坑情況負責的多。
技術特點
噴射冶金與傳統的加入塊狀料或通過爐內渣層的精煉過程相比,在冶金反應的熱力學和動力學條件上有顯著改善,其主要特點是:
①載氣強烈攪動熔池,使加入的物料在幾分鐘內達到均勻混合;
②噴入的粉料具有很大的比表面(表面積/容積),而金屬熔體內的組分與粉料的反應速度將隨接觸面積增大而顯著提高;
③粉料與金屬熔體組分間的反應區處於熔體內部,這就大大地減輕了爐襯、爐渣和大氣對反應過程的影響;在粉料顆粒上浮時,它與金屬的接觸為瞬時接觸(transitory contact),在頂面渣能夠吸收反應產物的條件下,這種接觸方式可以使冶金反應在短時間內進行得相當充分,並有可能進行不同程式、不同粉料的噴吹,以控制反應及產物的組成和形態。
實例
噴射冶金的技術特點為某些冶金精煉過程提供了重要條件。以鐵水的脫氧、脫硫為例,金屬鈣是比金屬鋁更強的脫氧劑,也是比石灰更強的脫硫劑。在鋼中加入金屬鈣,還可與大多數脫氧產物作用,形成複合夾雜物,例如鈣鋁酸鹽,這些夾雜物的變性作用顯著改變了夾雜物組成及形態,從而改善了金屬材料的性能。鈣在鋼中的存在還可改善鋼的切削性能。但是,由於金屬鈣的熔點為839±2℃,沸點1484℃,在煉鋼溫度下,鈣蒸氣壓可以達到1.8大氣壓,因此,用通常的辦法以塊狀料加到鋼液面或出鋼流中,都難以保證鈣的使用效果。噴入鈣或鈣基合金粉料,為鐵水和鋼液的精煉提供了有效手段。金屬鎂的套用也需要噴射冶金。用噴粉方法向金屬中加入稀土材料也已經獲得良好效果。
用噴吹法預處理煉鋼用鐵水時,常用的脫硫粉料為
和蘇打粉;載氣為氮氣或氬氣。預處理後的鐵水含硫量可以降到 0.005%。鋼包精煉常用的粉料有
、
、
、
、
和各種合金粉料等,平均粒度為0.1~0.5毫米。每噸鋼耗量:
2~3公斤;
基渣粉為4公斤。一般用氬氣載送粉料,供氣速度0.5~1.5立方米/分,噴射處理時間為10分鐘左右。處理後鋼中最低含硫量達0.001~0.005%或更低,經鈣基材料處理後的鋼中的夾雜物可以球化。