概念
分級配煤技術的原理是首先將各原料煤按粒度分級,分成
粉煤和
粒煤,然後根據配煤理論,將各粉煤按比例混合配製成粉煤配煤燃料,各粒煤配製成粒煤配煤燃料。粉煤配煤燃料供給粉煤鍋爐或
循環流化床鍋爐;粒煤配煤燃料供給
層燃鍋爐或層燃窯爐。這樣,一方面可減少粉煤鍋爐或
循環流化床鍋爐的燃料製備費用,更重要的是層燃爐燃用
粒煤可大大改善燃燒狀況,提高效率,減少污染。
動力煤分級配煤技術
動力配煤的質量指標主要是熱值、揮發份、硫份、灰熔融性、水份和
焦渣特徵,對燃料煤的粒度組成控制不嚴,有的只要求燃料煤粒度上限≤ 25mm(或≤40mm或≤ 50mm),對燃料煤粒度下限基本上沒有控制,有的也只是規定0~30mm含量≤30%,而在實際生產中沒有有效控制。實際上,燃料煤粒度組成對燃料燃燒狀況有很大影響。粉燃爐和
循環流化床鍋爐由於配備了專用燃料加工設備,對燃料煤原始粒度組成要求不高,但層燃爐一般不配備專用燃料煤加工設備,因而對燃料煤的粒度組成要求較高,一般要求最大粒徑小於30~40mm,0~6mm顆粒含量不超過50%~60%,實際上這一小粒級粉煤含量越小越好,特別是小於1mm~2mm
粉煤最好是沒有。因為這些粉煤將使漏煤炭損失和飛灰碳損失增加,使火床布風均勻性變差,導致灰渣含碳量以及煙氣中CO含量增加,同時還會使煙塵排放量增加。鍋爐型煤的產生和發展正是為了減少燃料煤的
粉煤含量,以適應層燃爐對燃料粒度的要求。但從研究開發到小範圍的工業套用,近20年來鍋爐型煤始終未能得到大面積的推廣套用,原因主要有2個方
面:一是原煤全部粉碎至3mm以下,加上粘結劑成型,加工成本高,缺乏市場競爭力;二是型煤粒度單一、表面光潔,著火性和燃盡性都較散煤差。
動力煤分級配煤工藝流程
動力煤分級配煤工藝流程與現有動力配煤工藝流程的區別在於:增加了對各原料煤的分級並採取
粉煤與
粒煤分別配煤,雖然流程複雜了一些,但獲得了粒煤配煤成品和粉煤配煤成品2種產品。與單純配煤或單純型煤或配煤+型煤方案相比,動力煤分級配煤方案在投資、生產成本、節煤、節電及環保等綜合效益上有很大優越性。
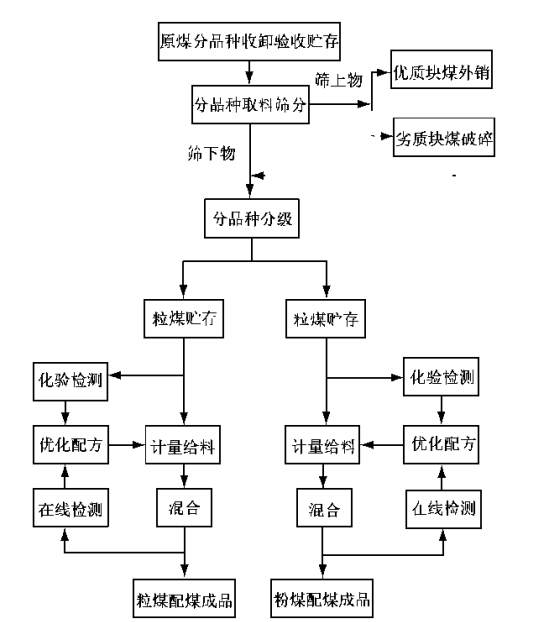
圖 1 動力煤分級配煤工藝流程
在實際生產中,根據配煤場地特點、配煤生產線的規模大小、機械化程度的高低、資金投入的多少等情況,生產工藝流程可以有所不同。粉煤配煤生產線與粒煤配煤生產線可以是同一條生產線,粉煤與粒煤交替配煤,也可以設2條生產線,粉煤配煤與粒煤配煤並行作業。
在分級配煤流程中,各原料煤的分級粒度是一個重要參數。從改善層燃爐的燃燒角度看,
粒煤的粒度下限可以是2mm、3mm、4mm、5mm或6mm等,對層狀燃燒效果不會有很大差別,因為引起層狀燃燒種種問題的主要是燃料煤中小於2mm的粉煤,換句話說,只要除去燃料煤中小於2mm的
粉煤,就能改善層狀燃燒,獲得節能與環保效果。因此,從燃燒角度出發,各燃料煤的分級粒度最小為2mm,具體可根據配煤場用戶對粉煤需求量與對粒煤需求量的比例來確定,即由市場確定。當粉煤需求量大時,分級粒度可大一些,反之則小一些,而且根據各原料煤各粒級的煤質特性,各原料煤的分級粒度也可有所不同。
煤炭細粒分級技術
在分級配煤流程中,用篩分機對原料煤進行細粒分級是很困難的。因為煤用篩分機的最小分級粒度為6mm,且不能精確篩分,只能機率篩分,在生產中還常常出現篩孔堵塞等問題,而小於6mm分級在生產中尚為空白,主要原因是篩孔越小,篩孔堵塞越嚴重。為了從根本上解決篩孔堵塞問題,研究發明了無篩網煤炭分級技術——潮濕煤炭
振動流化床氣力分級技術。如圖2所示,振動流化床氣力分級機組由振動流化床(VFB)分級器、細粒分離器、
旋風除塵器、循環風機、
布袋除塵器、引風機及管道等組成。其工作原理是:煤炭連續地加入振動流化床分級器,在振動力和氣力作用下,顆粒上下翻騰,碰撞劇烈,使粘結在一起的煤團快速分散,粘於塊煤表面的粉煤快速脫落,粉煤與粒煤充分分離,其中細顆粒隨氣流帶出並由細粒分離器和除塵器收集成為相當於篩分機的篩下產物;粗顆粒從分級器的入料端沿振動的布風板快速地移向出料端排出,成為相當於篩分機的篩上產物。
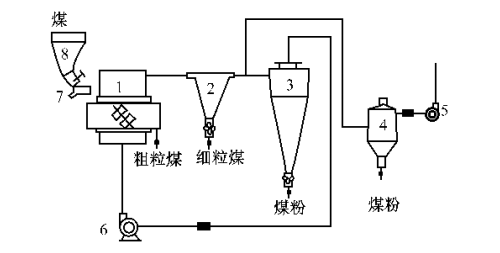
圖 2 振動流化床氣力分級原理
振動流化床氣力分級與機械篩分的最大區別是:粉煤不是透過篩孔從原煤中分離出來,而是通過上升氣流的夾帶分離出來,調節氣流速度即可調節分級粒度,比篩分機通過改變篩孔尺寸調節篩分粒度更簡便靈活。
分級配煤技術經濟效果分析
動力煤分級配煤與常規動力配煤相比,增加了各原料煤的分級,從支出看,約需增加分級電耗噸煤1度;從收益看,獲得
粒煤和
粉煤2個粒級產品。對於粉煤產品用戶,可省去從原煤粉碎至與粉煤產品同粒級時所需的電耗(噸煤約1度),可與分級電耗相抵。而對於粒煤產品用戶,效益更為顯著:①與型煤相比,燃用該粒煤產品不需要改造鍋爐;②不僅與燃用原煤相比有顯著的節能和環保效果,而且與燃用型煤相比也有更好的節煤效果,因為個大面光的型煤著火性和燃盡性都不及自然粒級組成的顆粒煤;③粒煤燃料加工費比型煤小很多,型煤的噸煤加工費用一般都在40元以上,而粒煤的加工費僅為分級過程中增加的電耗(噸煤1度)。可見,與型煤相比,動力煤分級配煤有很強的市場競爭力。
動力煤分級配煤將分級與配煤相結合,不僅能配製出熱值、揮發份、硫份、灰份、灰熔融溫度等煤質指標穩定的、符合鍋爐燃燒要求的燃料煤,而且還能生產出適合於不同類型鍋爐燃燒的粉煤和粒煤燃料。粒煤燃料脫除了對層狀燃燒十分有害的粉煤,特別適合於層燃爐燃燒,與燒原煤相比,可節煤10%以上,煙塵排放量降低60%以上。動力煤分級配煤技術是對單純配煤技術的重要發展,特別符合我國層燃爐量大面廣、耗煤量大、效率低、污染嚴重的國情,有很好的市場前景。
洗煤及配煤技術研究與套用
煤廠工藝流程及處理能力
龍東礦選煤廠投產於1993年10月,因當時資金限制,為節省資金,工藝流程相對比較簡單,設計為原煤30mm分級,-30mm末煤直接銷售,+30mm塊煤入洗,經單段跳汰機排矸降灰,洗後產品經最終分級篩分級,篩上物作為洗混中塊銷售;粗煤泥採用撈坑回收,離心機脫水系統;煤泥水採用濃縮機濃縮,壓濾機回收煤泥的系統。整個系統雖然比較緊湊,但卻制約了洗煤廠的通過能力和處理能力,特別是煤泥水處理系統。全部入洗後,撈坑易跑粗,濃縮機沉澱效果差,洗水濃度高,壓濾機入料中有粗顆粒,影響壓濾工效,底流濃度居高不下,整個系統勢必形成惡性循環,進而影響洗煤效果和產品質量,因此,洗煤廠全部人洗是難以實現的。
選煤廠技術改造
由於井下地質條件的限制,儘管在原煤開採、運輸過程中最大限度避免污染,但原煤灰分仍然居高不下,只有挖掘選煤廠潛力,加大人洗合理配煤降灰,為此對選煤廠的制約因素進行了相應改造。
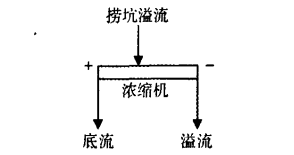
圖3 改造前粗煤泥回收系統圖
(1)更換預先分級重篩,提高篩分效率。預先分級篩的篩分效果好壞,直接影響入洗原煤中末煤含量和篩分粒度。為提高篩分效果,減少篩上物污染,減輕煤泥水處理系統壓力,降低洗耗,對預先分級篩進行了更換,更換後篩分效果明顯提高。
(2)跳汰機風閥改造。由於井下條件變化較大,需經常及時調整跳汰周期和頻率,而原先的臥式風閥在開車狀態下很難調節,為適應井下煤質條件的變化,由數控電磁風閥代替了原臥式風閥,更換後跳汰周期可及時隨煤質變化而得到調整,處理量略有提高,回收率提高近1%,按年人洗65萬t計,可多回收洗混中塊0.65萬t。
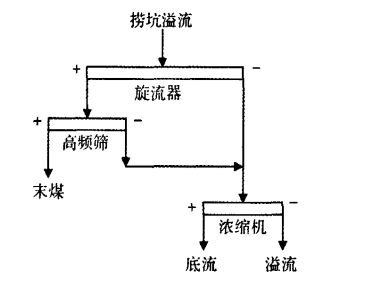
圖4 改造後粗煤泥回收系統圖
(3)設計和增加了粗煤泥回收系統。撈坑為單邊溢流,加大人洗後,撈坑跑粗較為嚴重,直接影響了洗水濃度和壓濾工效,制約了洗煤。通過廣泛調研和論證,設計了一套粗煤泥回收系統。即將撈坑溢流由原來的直接進入濃縮機改為進入旋流器,旋流器底流進入
高頻篩,高頻篩篩下水和旋流器溢流進入濃縮機,改造前、後的工藝流程如圖3、4所示。該系統杜絕了
濃縮機人料中含有粗顆粒的現象。同時回收了部分細顆粒煤泥,減少了
濃縮機和
壓濾機的壓力,年入洗量由原來的45萬t可增加到65萬t。